Технически средства за намаляване на загубите на нефтопродукти от изпарение от резервоари
1 Традиционни средства за намаляване на загубите на нефт и нефтопродукти от изпаряване
1.2 Изравнителни системи
1.3 Покрития, плаващи по повърхността на нефтения продукт
1.3.1 Защитни емулсии
1.3.4 Плаващи покриви
2 Използване на системи за събиране на леки остатъци
2.1 ULF адсорбция и абсорбционни системи
2.2 ULF кондензни системи
2.3 Системи за компресия ULF
2.4 Комбинирани ULF системи
3 Избор на технически средства за намаляване на загубите на нефтопродукти от изпаряване
Списък на използваните източници
Едно от основните средства за подобряване на икономическите показатели на производството е максималното използване на наличните резерви (например намаляване на загубите на нефт и нефтопродукти в находищата, в рафинериите, по време на транспортиране, в нефтените депа и в процеса на потребление). Приблизителните изчисления показват, че годишната загуба на нефт по време на изпомпване от кладенеца до инсталирането на петролна рафинерия и нефтопродукти по време на доставка от завода до потребителя, включително, е около 9% от годишното производство на нефт. В същото време, в резултат на изпаряване, основно най-леките компоненти, които са основните и най-ценни суровини за нефтохимическата промишленост, напускат маслото.
Загубата на леки фракции от бензин води до влошаване на търговските качества, намаляване на октановото число, повишаване на точката на кипене и понякога до прехвърляне на петролен продукт към по-ниски класове.
От общите годишни загуби загубите от изпаряване на нефтопродукти в нефтените депа и по време на транспортиране са приблизително 4,5%. Загубите от течове съставляват най-голямата част и могат да бъдатнапълно елиминирани чрез подобряване на общата култура на производство и прилагане на добре известни, задължителни организационни, технически и превантивни мерки.
Загубите на нефт и нефтопродукти, възникващи по време на тяхното транспортиране, съхранение, приемане и освобождаване, могат условно да бъдат разделени на естествени, експлоатационни и аварийни.
Един от основните източници на естествена загуба на нефтопродукти е загубата им от изпарение от резервоари по време на големи и малки "вдишвания". По време на операциите по пълнене на резервоара се появяват "големи вдишвания".
Оперативните загуби, за разлика от естественото изтриване, могат да бъдат напълно елиминирани.
Аварийните загуби възникват поради повреда на резервоари, тръбопроводи и оборудване в резултат на непредвидени ситуации. Тъй като във всички обекти на индустрията се извършва систематична работа за предотвратяване на аварии, приносът на този вид загуби към общата им стойност е сравнително малък.
Независимо от вида на загубата на течни въглеводороди, те в крайна сметка се озовават в атмосферата, което се отразява негативно на околната среда и особено на човешкото здраве.
По този начин намаляването на всички видове загуби на нефтопродукти е спешна задача не само от икономическа, но и не по-малко важна от екологична гледна точка.
Тази статия разглежда прилагането на различни технически средства за намаляване на загубите на нефтопродукти от изпарение от резервоари.
Намаляването на загубите на петролни продукти е една от най-важните области за пестене на ресурси.
1. Традиционни средства за намаляване на загубите на нефт и нефтопродукти от изпаряване
В момента, като средство за намаляване на загубата на нефтопродукти от изпаряване и съответното замърсяване на околната средаприложими среди:
- покрития, плаващи по повърхността на нефтения продукт.
Дефлекторният диск е препятствие с формата на диск, разположено на известно разстояние под монтажните дюзи на дихателния клапан (фиг. 1).
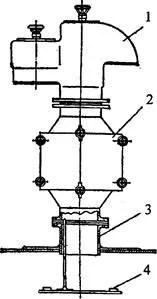
Фигура 1 - Дихателна клапа с диск-рефлектор: 1 - дихателна клапа; 2 - пожарен предпазител; 3—монтажна тръба; 4—диск-рефлектор
Предназначението на рефлекторния диск е да предотврати смесването на съдържанието на газовото пространство на резервоарите при тяхното изпразване.
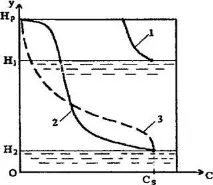
Фигура 2 - Разпределение на концентрацията по височината на НР на резервоара: 1 - преди изпомпване; 2 - след изпомпване при липса на рефлекторен диск; 3—същото, ако е налично
Като правило, разпределението на концентрацията на въглеводороди по височината на газовото пространство (HS) на резервоарите е неравномерно: в близост до повърхността на нефтения продукт тя е равна на концентрацията на наситени пари на Cs, а с разстоянието до покрива постоянно намалява (крива 1 на фиг. 2).
Ако обаче на пътя на засмукания въздух е монтирана преграда (това е дискът), тогава при удара енергията на струята изгасва почти наполовина и посоката на струята се променя на хоризонтална. Впоследствие PVA постепенно се заменя с входящия въздух, придружено от тяхното смесване. В същото време в горната част на HP преобладава въздухът, а в долната - парите от нефтопродукти (крива 3).
Лесно е да се види, че при последващото пълнене на резервоара с отразяващ диск в атмосферата, поради изкуствено създаденото неравномерно разпределение на концентрацията по височината на HP, ще бъде изместено по-малко количество въглеводороди, отколкото от резервоар без отразяващ диск. Положителен ефект ще бъде постигнат дори ако преливникът се промени от H2 на H1, тъй като в края на изпомпването в резервоара срефлекторен диск, средната концентрация на въглеводороди в HP е по-ниска. Това се дължи на факта, че след промяна на посоката на въздушните струи, интензивността на тяхното измиване на повърхността на нефтения продукт намалява и следователно скоростта на изпарение намалява.
В „Правилата за техническата експлоатация на резервоарните паркове“ [4] се посочва, че рефлекторните дискове намаляват загубата на бензин от изпарение с 20,30%.
1.2 Изравнителни системи
Газоизравнителната система (GUS) е газопровод, към който е свързан газов колектор. Поради това, ако изпомпването и изпомпването не съвпадат, част от PVA се натрупва в него, което прави HC по-ефективен от GO.
Ролята на газови колектори могат да играят газдържатели с ниско или високо налягане. Еластични контейнери, както и метални контейнери с променлив обем (газови колектори тип „дишащ балон”). Възможните варианти за свързването им към резервоарите са показани на фиг. 3.
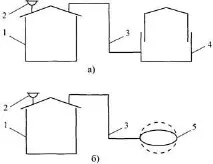
Фигура 3 - HUS с газов колектор с променлив обем: 1 - резервоар с бензин; 2—дихателен клапан; 3—газопровод; 4—газодържач с ниско налягане; 5 - газов колектор тип "дишащ балон" или гумено-тъканен газов колектор
Известни са конструкции на сухи и мокри газови резервоари с ниско (до 4000 Pa) налягане. Предимството на сухите газголдери пред мокрите е в намаляването на потреблението на метал, заеманата площ, капиталовите и експлоатационните разходи и в елиминирането на овлажняването на паровъздушната смес. Резервоарите за сух газ обаче имат и значителни недостатъци. През зимата влагата в газа образува лека коричка върху вътрешната повърхност на резервоара за газ, което затруднява движението на подвижния диск. При изтичане през уплътненията на диска в пространството между подвижния диск и покрива на резервоара може да се образува експлозивна смесгаз с въздух. Освен това при производството на газдържачи се изисква повишена точност.
Газовите резервоари с високо (до 1,8 MPa) налягане са стоманени съдове с цилиндрична или сферична форма. При еднакъв геометричен обем с газови резервоари с ниско налягане акумулиращият им капацитет е десетки и дори стотици пъти по-голям. Газголдерите под високо налягане нямат движещи се части и поради това са по-лесни за производство и работа.
Често срещан недостатък на използването на газдържачи е високата цена на метала.
За да се намали консумацията на метал в системите за улавяне на леки фракции от нефт и нефтопродукти, се предлага колекторите за газ да се изработват от достатъчно еластичен материал (памучен плат, импрегниран с масло- и бензиноустойчив състав) под формата на торби или цилиндри.
Работата на еластичните газови колектори не се различава по принцип от работата на резервоари с "дишащи покриви". Обемът им достига 500 m3 при диаметър 7,6 m.
Поради краткия експлоатационен живот на гъвкавите газови колектори те не са придобили популярност.
Като алтернатива на еластичните газови колектори са предложени "дишащи цилиндри", изработени от стомана. Те са плоски резервоари с голям (12,45 m) диаметър и ниска (1,1,5 m) височина. Покривът и дъното на газовите колектори са изработени от стоманена ламарина с дебелина 2 мм. Когато се напълни с пара, покривът на газовите колектори се издига на височина 2,4,5 м. Газовите колектори от типа „дишащ балон“ (в чужбина те се наричат „цилиндър на Уигинс“) не изискват големи капиталови и експлоатационни разходи.
LPDS "Салават" на Уралския отдел за магистрални нефтопродуктопроводи (сега OJSC "Uraltransnefteprodukt") е едно от малкото места в СССР, където са въведени такива газови колектори. През 1962 г. тук е построен ГУС с два газови колекторатип "дишащ балон" с обем 1000 m3 всеки. Тестовете им показали следното. При пълнене и изпразване на газовите колектори се образуват множество пукнатини с дължина 20,35 mm; техният брой нараства прогресивно с увеличаване на броя на циклите на пълнене и изпразване. Издигането и падането на покрива става при резки удари с образуването на остри ъгли в метала, където се появяват пукнатини. Тъй като работата на газовите колектори тип "дишащ балон" се оказа опасна, те бяха демонтирани и отписани като скрап.