Технология за лазерно заваряване
Инсталация за автоматично заваряване на надлъжни шевове на черупки - в наличност!Висока производителност, удобство, лекота на работа и надеждност при работа.
Заваръчни екрани и защитни завеси в наличност!Защита от радиация при заваряване и рязане. Голям избор. Доставка в цяла България!
Приложение на лазерно заваряване
Разработена е технологията за лазерно заваряване на малки и средни (5-10 mm) дебелини. Въпреки това широкото използване на лазерно заваряване в редица случаи е възпрепятствано от съображения от икономическо естество. Цената на технологичните лазери все още е доста висока, което изисква задълбочен анализ на възможностите за използване на лазерно заваряване. Перспективата за лазерно заваряване се появява, когато използването на традиционни методи за заваряване е изпълнено с трудности.
Лазерното заваряване трябва да се препоръча, ако е необходимо да се получи прецизна конструкция, чиято форма и размери практически не трябва да се променят в резултат на заваряването; възможността за значително опростяване на технологията за производство на заварени конструкции чрез извършване на заваряване като краен процес без последващо изправяне или механични операции за постигане на необходимата точност; необходимостта от значително увеличаване на производителността, тъй като процесът на лазерно заваряване може да се извършва при скорости от 100–200 m / h или повече, което е няколко пъти по-високо от скоростта на най-разпространения традиционен метод за електродъгово заваряване; производство на едрогабаритни конструкции с ниска твърдост с труднодостъпни шевове. В този случай, за разлика от заваряването с електронен лъч, не са необходими вакуумни камери; свързване на трудни за заваряване материали, включително различни.
Лазерното лъчение се препоръчва за използване в производствотоконструкции, като се вземат предвид технологичните особености на лазерното заваряване на основните конструктивни материали.
Заваряване на стомана
Качеството и надеждността на заварените съединения, направени с лазерен лъч, до голяма степен се определят от точността на сглобяване на елементите за заваряване. Необходимата точност на сглобяване се постига чрез подготовка на заварените ръбове на металорежещи машини (рендосване, фрезоване, струговане).
Повърхността на метала в зоната на заваряване трябва да бъде почистена от мащаб, ръжда, други замърсители, както и влага. Тези примеси и влага създават условия за образуване на порьозност, оксидни включвания и в някои случаи студени пукнатини в заваръчния метал и зоната на топлинно въздействие поради насищане с водород.
Повърхностите, които ще се заваряват, трябва да се почистват с четки от неръждаема стомана в зона от най-малко 10-15 mm както над, така и под ръбовете, които ще се заваряват. Крайните повърхности, съседни на заварените зони, също се почистват. След отстраняване се препоръчва мястото на заваряване да се обезмасли.
Монтажът за заваряване трябва да осигурява възможност за внимателно регулиране на ръбовете по цялата дължина на шева с минимална празнина и изкривяване на ръбовете. При дебелина на заварения материал> 1,0 mm, празнината не трябва да надвишава 5-7% от дебелината (не повече от 0,2-0,3 mm). Отместването на единия ръб спрямо другия по височина не трябва да надвишава 20-25% от дебелината на частите, които ще бъдат заварени (не повече от 0,5 mm).
При сглобяване за заваряване не се препоръчват прихващания. Ако е необходимо, закрепването трябва да се извърши с лазерен лъч.
Предпочитаната връзка е челна. Не се препоръчват препокриващи и блокиращи съединения от въглеродни стомани поради високата им чувствителност към концентратори на напрежение.
Заваръчните повърхности трябва да бъдат защитени от окисление с хелий или смес от хелий и аргон всъотношение 2:1, както и аргон с въглероден диоксид в съотношение 3:1, подавани през специална дюза. Коренът на заваръчния шев от обратната страна се препоръчва да се защити с аргон. В някои случаи при заваряване на нисковъглеродни стомани се допуска липса на защита на шева.
Характерните режими на непрекъснато лазерно заваряване на някои стомани осигуряват комбинация от висококачествено заваряване, висока технологична якост и високи механични свойства на завареното съединение (Таблица 6.1).
Таблица 6.1. Типични режими на непрекъснато лазерно заваряване на стомани
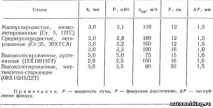
Както следва от табл. 6.1, оптималните режими на заваряване на стомани се осигуряват от относително високи (80-120 m / h) скорости на заваряване. В този случай мощността на лазерното лъчение може да бъде приблизително избрана от условието 1 kW на 1 mm от дебелината на заварената част.
Представени в табл. Режимите 6.1 са дадени за челно заварени съединения, но като първо приближение те могат да се използват и за ъглови, тройни, шлицови и други видове съединения.
Заваряване на алуминиеви и магнезиеви сплави
Заваряването на алуминиеви и магнезиеви сплави се характеризира с редица характеристики, свързани с взаимодействието на разтопения метал с газовете от околната среда, изпаряването на легиращите елементи, образуването на оксиден филм върху повърхността на панела, което затруднява провеждането на висококачествен процес на заваряване. Основните трудности при заваряването на алуминий и неговите сплави се елиминират предимно чрез използване на концентрирани енергийни източници, които включват лазерни и електронни лъчи.
За лазерно заваряване повърхностите, които ще се съединяват, се подготвят толкова внимателно, колкото и за електродъгово заваряване, включително машинна обработка, ецване, последвано от избистряне, изплакване с гореща вода и почистване със скрепер непосредствено предизаваряване.
Лазерното заваряване се извършва в среда със защитен газ. Обикновено се препоръчва използването на хелий за защита на горната част на заваръчната вана, докато аргон може да се използва за основата на заваръчния шев. Дебитът на хелия трябва да бъде най-малко 7–8 l/min, а този на аргона 5–6 l/min.
Таблица 6.2. Оптимални режими на заваряване на алуминиеви сплави с CO2 лазерно лъчение
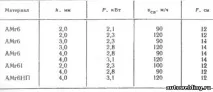
По време на лазерно заваряване на алуминиеви сплави (Таблица 6.2) характерна особеност на топенето на метала се наблюдава само при определено ниво на мощност и плътност на мощността. Например за сплавта AMg6 праговата мощност на излъчване на CO2 е 2–2,2 kW. В този случай веднага се постига дълбочина на проникване от 1,5–2,0 mm, а при по-ниски стойности на мощността проникването напълно липсва. Това обстоятелство се дължи на високата отражателна способност на алуминиевата повърхност и последващото рязко намаляване на отражението след началото на топенето.
Якостта на заварени съединения с дебелина 2,0 и 3,0 mm е най-малко 0,9 от якостта на основния метал при заваряване без тел за пълнене (Таблица 6.3). Фугите се разрушават главно по шева.
Таблица 6.3. Механични свойства на основния метал (числител) и заварени съединения (знаменател) на сплав AMg6
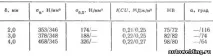
Забележка. Студено обработен материал с дебелина 4,0 mm.
Заварките на магнезиеви сплави, направени с лазерен лъч, са добре оформени, без да се образуват провисвания при заваряване на тежест. Това позволява, за разлика от електродъгово заваряване, да се извършва лазерно заваряване без използване на облицовки, което значително опростява технологията на производство, особено за големи конструкции.
Механичните свойства на заварените съединения, направени чрез лазерно лъчение с оптимални режимни параметри (Таблица 6.4), са на нивосъответстващи свойства на основния метал.
Таблица 6.4. Режими на лазерно заваряване на магнезиеви сплави чрез непрекъснато CO2 лъчение
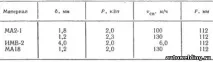
Заваряване на титанови сплави
Основните трудности при заваряването на титанови сплави са високата химическа активност на метала при повишени температури и особено в разтопено състояние, тенденцията към растеж на зърното при нагряване до 330-350 ° C и по-висока, както и повишената склонност към образуване на студени пукнатини с увеличаване на съдържанието на газови примеси в заваръчната и околозаваръчната зона, особено водород. Тези трудности се елиминират чрез заваряване с минимални стойности на входящата топлина, осигурена от такива силно концентрирани източници на енергия като лазерни и електронни лъчи.
Необходима е внимателна подготовка на ръбовете за заваряване, включително механична обработка или пескоструене, пясъкоструене, последвано от химическо ецване, избистряне и измиване.
Качеството на защита на повърхността, корена на заваръчния шев, охлаждащите секции на заваръчния шев и зоната на топлинно въздействие до 400-500 ° C значително влияе върху свойствата на заварените съединения. Хелий с висока чистота се използва за защита на заваръчната повърхност и за потискане на плазмата в зоната на лазерно излагане с приблизителна скорост на потока 10–12 l/min. За защита на охлаждащата повърхност на заваръчния шев и основата може да се използва аргон с висока чистота с приблизителна скорост на потока от 4–5 l/min за основата на заварката и 15–18 l/min за повърхността на заварката.
Режимите на лазерно заваряване се избират от условията за осигуряване на висококачествено образуване, необходимата геометрия на заваръчния шев, предотвратяване на образуването на студени пукнатини и създаване на най-благоприятните структури в зоната на заваръчния шев и около заварката (Таблица 6.5).
Таблица 6.5. Режими на лазерно заваряване на титанови сплави
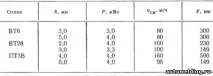
Подобрени механични свойства на заварени съединения,направени чрез лазерно заваряване (Таблица 6.6) са свързани с висока скорост на процеса и съответно с високи скорости на охлаждане на заваръчния метал и зоната на топлинно въздействие, които са 400-600 ° C / s в полиморфната област в сравнение с 20-25 ° C / s при електродъгово заваряване. Това води до увеличаване на дисперсията на заваръчния метал с коефициент три до четири, както и до значително изтъняване на зърното в зоната около заварката.