Топене и леене на медни сплави - Леярство
Обработка на дърво и метал
Медните сплави, които включват калаен и безкалаен бронз и месинг, се топят главно в електродъгови и индукционни пещи и по-рядко в пламъчни пещи, работещи с течно гориво. За малки производствени обеми понякога се използват тигелни пещи.
Тъй като почти всички елементи, които съставляват медни сплави, лесно се окисляват, процесът на топене е принуден, като същевременно се вземат мерки за защита на сплавите от повърхността (защитни или покривни потоци), а отделните лесно окисляеми елементи се използват под формата на лигатури.
1. Материали за зареждане
Зарядните материали за медни сплави могат да бъдат пресни (чисти) метали, вторични сплави, рециклирана сплав, както и различни лигатури, доставяни от индустрията или домашно приготвени.
За дезоксидиране на сплави се използва фосфорна мед под формата на плочки с тегло около 12 kg съгласно GOST 4515-78, които се натрошават на малки парчета преди употреба.
За получаване на сплав са възможни различни комбинации от шихтови материали. Зарядът може да се състои само от пресни метали, от пресни метали или вторични сплави с добавяне на основни сплави, от рециклирана сплав с добавяне на пресни метали и основни сплави, от една рециклирана сплав или от една вторична сплав. Обикновено се използва заряд, състоящ се от 50-60% пресни метали, 25-35% рециклирана сплав и 10-12% закупен скрап, или топенето се извършва върху вторични сплави.
При изчисляване на заряда се вземат предвид отпадъците от различни елементи на сплавта, чиято стойност зависи от естеството на елементите, чистотата на заряда и вида на топилната пещ.
Помислете за пример за изчисляване на таксата за топене на бронз от марката BrOZTs7S5N1.
При производството на сплави за по-малко критични отливки с цел спестяванечисти метали, могат да се използват само вторични сплави - паспортни бронзи на марката BrOZTs8S4N1.
3. Технология за топене на медни сплави
Топене в тигелни пещи. Голямо разнообразие от тигелни пещи се използват за топене на медни сплави. При малки обеми на топене те осигуряват високо качество на сплавта, тъй като няма директен контакт на сплавта с продуктите на горенето и повърхността на металното огледало е много малка. За топене се използват графитни или корундови тигли.
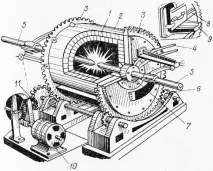
Топене в електрически пещи. Електрическите пещи за топене на медни сплави се разделят на дъгови и индукционни.
Топене в електродъгови пещи. За топене се използват електродъгови пещи с непряко нагряване, т.е. такива, в които електрическа дъга се образува между два хоризонтални графитни електрода.
Пещта DMK (фиг. 1) има формата на барабан с копче за зареждане, отвори за електроди и улей за източване на сплавта.
Корпусът на пещта е облицован с динасови или шамотни тухли. В краищата на корпуса са монтирани зъбни венци, съчетани със зъбни колела, които позволяват разклащане на пещта по време на процеса на топене, което осигурява производството на хомогенна и равномерно нагрята сплав.
Топенето започва с подготвителна работа: цялостно почистване на пещта от остатъците от предишната стопилка, проверка на работоспособността на механизмите и подаване на вода към уплътненията с водно охлаждане. След това облицовката се нагрява до температура от 700–800 ° C, електродите се изваждат от пещта и няколко лопати сух калциниран въглен се изсипват на дъното му, след което се зареждат предварително загряти до 150–200 ° C материали: първо, фини частици, лейки, скрап и отгоре - големи парчета. Сместа трябва да се намира не по-близо от 50 mm от електродите ине трябва да пречи на свободното им движение по пещта. След монтиране на електродите прозорецът за зареждане се затваря и се възбужда електрическа дъга, което се осъществява чрез приближаване на електродите и бързо отстраняване на един от тях за кратко разстояние с помощта на ръчното колело на механизма за придвижването им.
Процесът на топене на заряда е интензивен. След 20-30 минути се включва обратният механизъм на люлеене на пещта, първо с 25-30°, след което люлеенето постепенно се довежда до 90°, а след разтопяване на целия заряд до 160°. Това избягва локалното прегряване на сплавта и насърчава по-доброто смесване. Сплавта се деоксидира, добавят се топими добавки, рафинират се, нагряват се до необходимата температура и се освобождават от пещта.
Топене в индукционни пещи. За топене на медни сплави се използват индукционни пещи със стоманена сърцевина и без сърцевина.
Индукционна пещ със стоманена сърцевина, чийто схематичен разрез е показан на фиг. 2, е трансформатор, чиято първична намотка е медна намотка, монтирана върху сърцевина от електрически стоманени плочи с дебелина 0,35-0,5 mm. Вторичната намотка е пръстен от течна сплав, разположен в канала за топене. Променлив ток с индустриална честота, преминаващ през първичната намотка, създава около нея магнитен поток, който се затваря през магнитната стоманена сърцевина на трансформатора и индуцира ток в сплавта, разположена в пръстеновидните канали. Сплавта, запълваща каналите, комуникира с ваната с течна сплав и й дава топлина поради циркулацията, създадена от температурната разлика на сплавта по височината на пещта.
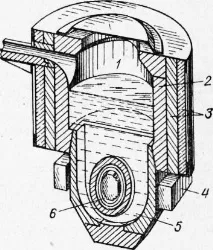
Характеристика на топенето в индукционни пещи е, че течната сплав, запълваща каналите, трябва да остане в пещта дори след освобождаването на стопилката, за да образува затворенелектрическа верига по време на последващо топене. В тази връзка в индукционните пещи преходът към топене на нова сплав е труден. В този случай е необходимо да се източи цялата сплав от каналите и да се направят едно или две промивни топения на некритичната сплав.
След запълване на пръстеновидните канали и „блатото“ (слой от течна сплав с дебелина 30–50 mm, разположен над каналите) с течна сплав и нагряване на пещта, се зарежда предварително загрята шихта: първо мед, а след нейното топене, рециклирани и вторични сплави. Когато целият заряд се разтопи, се извършва дезоксидация, отстраняване на шлаката от повърхността и въвеждане на лесно окисляеми елементи. При източване на готовата сплав е необходимо тя да се остави в каналите и над тях със слой от 30-50 mm.
Топене в индукционни тигелни пещи. През последните години се използват индукционни тигелни пещи от типа ILT за топене на сплави на медна основа - бронз и месинг. Отпадъчният метал в тези пещи не надвишава 0,5-1%.
4. Характеристики на топене и изливане на медни сплави
При топене на медни сплави съставът на шихтата обикновено включва червена електролитна мед, която се разтопява и деоксидира с фосфорна мед преди зареждането на останалите компоненти на шихтата в пещта. Топенето на медта трябва да става много бързо под слой от добре изсушени и калцинирани въглища. Пещта трябва да бъде предварително добре загрята преди зареждане на мед. Качеството на дезоксидацията може да се провери чрез технологичен тест: напълнена и охладена пръчка, когато се огъва, не трябва да се напуква на завоя.
Топене на калаен бронз.
Част от вторичните и рециклираните сплави се зареждат в предварително загрятата пещ и се покриват със слой сух въглен, който след разтопяване на шихтата трябва да покрие цялата повърхност на течната сплав в равномерен слой. Тъй като първоначалната част от заряда се разтопи, те се въвеждат в пещтачасти или изцяло остатъка от сместа, загрята до температура 150-200 ° С. От пресните метали, използвани за подреждане, медта и никелът се зареждат в пещта едновременно с първата част от заряда, а цинкът, оловото и калайът се въвеждат директно във ваната до края на топенето, за да се намалят отпадъците им.
След разтопяване на целия заряд и достигане на необходимата температура, сплавта се деоксидира с фосфорна мед в количество 0,2% от теглото на заряда и се покрива с добре изсушен флюс, състоящ се от 60% калцинирана сода, 33% флуорошпат и 7% боракс. Консумацията на поток е 2-3% от теглото на заряда. След това сплавта се нагрява до температура 1250-1300 ° C и се държи под поток за 20-30 минути, като периодично се разбърква. След това получената шлака се почиства и сплавта се изхвърля в кофа за изливане във форми.
Топене на месинг. Помислете за технологията за топене на силициев месинг марка LKS80-3-3.
При топене на заряд от пресни метали медта първо се разтопява и деоксидира с фосфорна мед, след това се въвежда медно-силиконова сплав, цинк и олово.
Ако зарядът съдържа циркулираща сплав от същата марка, тогава той се зарежда заедно с мед в случай, че масата на пресните метали не надвишава 30-40% от масата на целия заряд. С голямо количество пресни метали циркулиращата сплав се натоварва след топенето на медта и въвеждането на други елементи. Като се има предвид склонността на тази сплав да абсорбира газове, топенето трябва да се принуди, като същевременно се поддържа неутрална или леко окислена атмосфера в пещта. Като флюс може да се използва счупено стъкло и боракс.
За дегазиране сплавта се нагрява до температура 1150-1160 ° C и се държи при тази температура за 10-15 минути. Цинковите пари, отделени по време на експозицията, механично увличат разтворените газове и ги отстраняват от течната сплав. За компенсиране на повишената загуба на цинк по време накато държите сплавта преди да я излеете в пещта, се въвежда допълнително количество цинк.
За получаване на висококачествени медни сплави е необходимо внимателно наблюдение на спазването на правилата за подготовка на изходните материали и провеждането на процеса на топене. Особено внимание трябва да се обърне на контрола на температурата на течната сплав както по време на самия процес на топене, така и по време на освобождаването й от пещта и изливането.
Обикновено за измерване на температурата на сплавта се използват потопяеми термодвойки със защитни капаци, изработени от топлоустойчива стомана. Термодвойките в комбинация с автоматично оборудване могат независимо да регулират температурния режим в пещите или чрез светлинна или звукова сигнализация да привлекат вниманието на работника към нарушения на температурния режим.
Тъй като медните сплави са склонни да абсорбират газове и да се окисляват, при изливане на форми е необходимо да се поддържа ниска височина на струята, да не се прекъсва и да се предотврати пръскането на сплавта. Изливането се извършва чрез черпаци и кранови черпаци, подобни на тези, използвани за изливане на чугун.