Вакуумиране на стомана вчерпак
Технологичните процеси на обезгазяване на стоманата допринасят значително за подобряване на качеството на стоманените продукти и поради това те стават все по-широко разпространени. На настоящия етап има два основни метода за дегазация на стомана: циркулационна и камерна дегазация.
Циркулационен вакуум – RH процесът е въведен за първи път в Германия през 1959 г. от Ruhrstahl-Heraeus. Методът на циркулационно вакуумиране използва ефекта на еърлифта за циркулиране на метала в поточна вакуумна камера (Фигура 2.6).
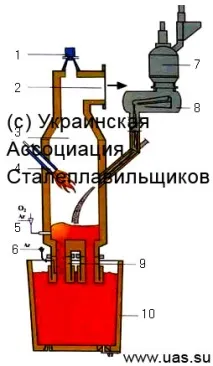
Фигура 2.6- Схема на процеса на циркулационна вакуумна дегазация на стомана: 1 - ТВ камера; 2 - връзка към вакуумната система; 3 – RH-OB камера; 4 – камерно отопление; 5 - кислородни и аргонови дюзи; 6 - разклонителна тръба за подаване на транспортиращ газ; 7 - заключващо устройство за въвеждане на легиране; 8 - дозатор на тава; 9 - потопени тръби; 10 - стоманена черпак
Камерата има формата на удължен цилиндър (височина до 11 m), като в метала на кофата са потопени две дюзи, в едната от които се подава аргон на две до три нива през неръждаеми тръби в количество от 0,5 до 1,5 m 3 /min.
Съвременните инсталации са оборудвани със стационарни камери, а кофата с метал се подава на специална количка с хидравлично повдигане на кофата до височината, необходима за потапяне на дюзите в метала. В същото време се подава аргон и се включват вакуумни помпи. Във всмукателната тръба газът се нагрява, увеличава обема си, издига се, увличайки метала, смес от една част метал и 10 обемни части газ навлиза в камерата със скорост над 5 m/s, избликва на височина до 10 m и създава многократно нарастваща повърхност газ-метал. Дегазираният метал се влива в черпака с дренажна тръба. ТакаПо този начин се осигурява циркулацията на стоманата през камерата. Доставянето на аргон на различни нива с различно налягане увеличава скоростта на циркулация, което интензифицира дегазирането на метала.
Скоростта на циркулация се увеличава с увеличаване на диаметъра на смукателната тръба и консумацията на аргон, достигайки 100 t/min. В края на обработката металът се дезоксидира и легира, като химическият състав се осреднява за още 2 минути.
Методът RH и дизайнът на устройството позволяват въвеждането на прахообразна смес CaO + CaF2 в поток от аргон, осигурявайки висока степен на десулфуризация дори при дебит на сместа от около 3 kg/t, тъй като металът съдържа минимално количество повърхностно активно вещество кислород. За да се компенсират разходите за топлина, в камерата се вдухва кислород, осигурявайки съответния излишък на въглеродно съдържание в метала. Вариант на тази технология се нарича VOF процес (Vacuum-oxygen-flux).
При RH процеса, поради голямата радиационна повърхност на метала, топлинните загуби се увеличават и работните условия на графитните нагреватели се влошават, когато върху тях попаднат метални пръски. Поради това в някои инсталации се предвижда индукционно нагряване на метала в дюзите.
Съвременните инсталации са оборудвани с уреди за вземане на проби, измерване на температура и оксидиране на метали.
Понастоящем основният метод за дегазиране на стомана е методъткамерна дегазация, който има широки технологични възможности за рафиниране на стомана под вакуум, прост дизайн и изисква по-малко капиталови разходи. В допълнение, обемът на работата по поддръжката на камерния дегазатор е минимален, а процесът на обработка е доста надеждно контролиран и контролиран. Оборудването на камерния дегазатор не влиза в контакт с течна стомана (Фигура 2.7), не изисква специални огнеупори за облицовка, няма нужда от товапредварително загряване, производителността на процеса не се влияе от честотата и темпото на работа.
Основните разновидности на процеса на камерно рафиниране са VD - вакуумно дегазиране и VOD & VD - OB - Вакуумна кислородна декарбуризация & Вакуумно обезвъглеродяване - Кислородното продухване позволява дълбоко дегазиране на метала, дезоксидация и обезвъглеродяване (Фигура 2.8).
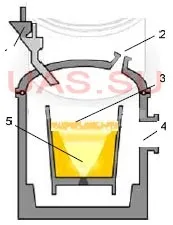
Фигура 2.7- Схема на процеса на камерна дегазация на стомана: 1- бункер за легиращи компоненти; 2 - черпак с метал; 3 - аргон; 4 – капак на вакуумната камера; 5 - вакуумна камера
Съставът на камерната инсталация за вакуумиране на стомана в кофа включва: високопроизводителна пароструйна вакуумна помпа, вакуумна камера с капак и вакуумна линия.
По-долу са представени основните технически параметри на пароструйната вакуумна помпа PEVN 500x0.5, която може да се използва за евакуация на камерата:
- работно налягане на входа на главната помпа, 0,5 mm Hg;
- налягане (абс.) на изхода на помпата, 830 mm Hg;
- мощност на помпата за сух въздух с t=20 o C при работно налягане на входа 500 kg/h;
- продължителността на изпомпване на вакуумната камера и вакуумната линия от атмосферно налягане до работното, 6 минути.
Вакуумната камера се състои от две основни части: самата камера и капака. Капакът е монтиран на транспортна количка и може да се премества вертикално с хидравлично задвижване.
Основните елементи на вакуумната камера: тяло на вакуумна камера с уплътнителен канал; стойка с водачи за монтаж на кофа; дупка-мембрана с температурен датчик за аварийно източване на стомана; свързващ разклонител на вакуумна линия с камера; система за подаване на аргон и азот за понижаване на налягането.
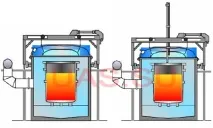
Рисуване2.8– VD диаграма на процеса (вляво) и VOD & VD - OB (вдясно)
В капака с количката за вакуумна камера са разположени следните устройства: защитен топлинен щит с елементи за подаване и отвеждане на охлаждаща вода; система за телевизионно управление на процеса на вакуумна обработка; устройство за вземане на проби и измерване на температура; копие за продухване на стомана с кислород (ако е необходимо); шлюзови устройства за въвеждане на дезоксидиращи, легиращи и шлакообразуващи добавки. За да се избегнат пръски от шлака и метал от кофата по време на обработката, свободната страна на кофата се увеличава с 0,6-1 m.
В зависимост от задачите, които трябва да бъдат решени, технологичните варианти на дегазиране на кофата позволяват ефективно рафиниране на стопилката на всеки етап от обработката извън пещта.
Вакуумирането на недезоксидирана стомана дава възможност да се реализират най-пълно известните предимства на въглерода като дезоксидант. Благодарение на вакуума балансът на реакцията на взаимодействие между въглерод и кислород, разтворен в стоманата, се измества към образуването на газообразни продукти, което прави възможно допълнително деоксидиране на стоманата с въглерод и намаляване на количеството на оксидни включвания, образувани по време на окончателното дълбоко дезоксидиране на метала. В индустриалните вакуумни инсталации обаче не се постига равновесие между въглерод и кислород, разтворени в стоманата. Основните причини за това явление са следните:
- при изключително ниски концентрации на взаимодействащи вещества, скоростта на химичната реакция намалява толкова много, че не позволява дори да се приближи до състояние на термодинамично равновесие по време на обработката;
- Практиката на промишленото вакуумиране показва, че дори малко количество FeO в рафиниращата шлака (до 1%) допринася значително за това, че реакционното равновесие не се достига.
Така че, при налягане от 100-200 Pa, изчисленият продукт на равновесните концентрации на въглерод и кислород е около 2,5-5,9x10 -6, но ходът на реакцията на обезвъглеродяване (дезоксидация с въглерод) спира близо до равновесната крива, съответстваща на Р = 1-10 kPa, т.е. реалната остатъчна концентрация на въглерод и кислород в стоманата след евакуация е няколко порядъка на магни по-висока от равновесието, изчислено в тънък повърхностен слой метал в кофата. Следователно възниква проблемът да се осигури чрез дезоксидиране с въглерод под вакуум максимално възможно намаляване на концентрацията на кислород в стоманата, чиято стойност позволява да се избегне образуването на течни или твърди дезоксидационни продукти в метала след въвеждането на добавки.
В тази връзка, за да се осигури висока степен на реализация на дезоксидиращата способност на въглерода при условия на вакуум, е необходимо:
За да се предотврати прекалено бързото развитие на реакцията на окисление на въглерода под вакуум, се извършва частично дезоксидиране на стоманата чрез увеличаване на съдържанието на силиций и (или) алуминий в нея. Благодарение на смесването на метала и използването на сравнително малко количество дезоксиданти е възможно да се постигне същата висока степен на чистота на стоманата по отношение на оксидни включвания, както при вакуумната обработка на стомана в недезоксидирана форма.
При обработката на частично деоксидирана стомана (0,15% Si и 0,005% Al) реакцията на въглеродно окисление започва при налягане 30-50 kPa. По-нататъшното намаляване на налягането до 100-200 Pa ви позволява постепенно да увеличите интензивността на кипене, която достига най-високата си стойност и се поддържа известно време на определено регулируемо ниво. След това идва постепенното затихване на процеса на кипене.
Рафинирането на стопилката по време на вакуумиране на черпака се дължи на факта, чедопълнително (до продухване с аргон) интензивно освобождаване на мехурчета от въглеродни оксиди от дълбоките слоеве на метала, които се образуват в резултат на изместване на равновесието между разтворен въглерод и кислород с намаляващо налягане, създава мощни турбулентни потоци, обхващащи целия обем на метала. При този тип кипене шлаката се пренася дълбоко в кофата и се раздробява, като значително се увеличава повърхността на повърхността, което осигурява допълнително увеличаване на скоростта на потока кислород от шлаката в метала. Това допринася за по-нататъшното развитие на реакцията на въглеродно окисляване и значително увеличаване на количеството отделен въглероден окис. Интензивното кипене на банята създава необходимите кинетични условия за реакция на взаимодействие на въглерод с кислород и освобождаване на разтворен водород и азот.
Намаляването на температурата на метала в кофа с тегло 100 тона по време на вакуумна обработка е от 70 до 80 o C, а действителната вакуумна обработка на частично дезоксидирана стомана (дълбок вакуум) продължава 15-20 минути.
В края на евакуацията помпите се изключват и във вакуумната камера се подава неутрален газ за 1-2 минути или първо неутрален газ, а след това въздух. Газообразните реакционни продукти увеличават обема и повърхността на аргоновите мехурчета и при равни други условия улесняват извличането на водород и азот, разтворени в метала; следователно дегазирането по време на евакуация на недезоксидирана и полудезоксидирана стомана е по-бързо и по-пълно, отколкото в случая на дълбоко дезоксидирана стомана.
В същото време методът за вакуумна обработка на недеоксидирана и полудеоксидирана стомана не гарантира получаване на ниско съдържание на газове в крайния продукт поради редица причини, една от които е, че след края на вакуумната обработка, като правило, се изисква нагряване,смесване, легиране, дезоксидация, карбуризация и десулфуризация.
От друга страна, при обработката на индустриални стопилки, ефективността на отстраняване на азот обикновено не надвишава 15-30%. В същото време анализът на влиянието на състава на метала върху резултатите от обработката предполага, че намаляването на ефективността на дегазирането е пряко свързано с наличието на повърхностноактивни вещества в стопилката.
По този начин, ако основната задача на дегазирането е отстраняването на газовете (водород и азот) от метала, тогава трябва да се стремим да получим минимално съдържание на повърхностноактивни примеси в стопилката. На тези изисквания отговаря дълбоко деоксидираната стомана в крайния етап на обработка на кофата.
За да се получи ниско съдържание на водород и азот, широко се използва технологията за евакуиране на деоксидирана стомана непосредствено преди леене, което може да се комбинира с екстракционно отстраняване на сяра чрез обработка с рафинираща шлака успоредно с евакуация.
За да се осигури достатъчна площ на интерфейса между взаимодействащите фази, вакуумната обработка на деоксидираната стомана се комбинира с прочистването на стопилката с инертен газ. Наблюдава се забележимо увеличение на скоростта на масообменните процеси с увеличаване на специфичната мощност на смесване на метала до ниво от 200-300 W / t.
Трябва да се отбележи, че при атмосферно налягане такава стойност на мощността на смесване е практически недостижима.
Количеството потребление на аргон, необходимо за обезгазяване на стомана, бързо намалява с намаляване на налягането над повърхността на стопилката. В това отношение комбинацията от продухване на стомана с инертен газ и обработка с вакуум е много ефективно средство за обезгазяване на метала. Така че, според теоретичните изчисления, за да се получи остатъчно съдържание в стоманаводород под 1,5 ppm при атмосферно налягане трябва да се въведе в 100-тонна стоманена кофа най-малко 700 m 3 аргон. При продухване с инертен газ под вакуум (0,01 и 0,001 атм.) количеството газ значително намалява и възлиза съответно на 14 и 8 m 3.
В тази връзка, продухването на стомана с аргон в стоманоразливна кофа под вакуум винаги е придружено от значително обезгазяване на метала.
На практика нагряването на метала по време на цикъла на обработка в "пещ черпак" (30-35 минути) гарантирано осигурява дадено прегряване на стопилката. По-нататъшното присъствие на метал в инсталацията често се свързва с необходимостта да се получи необходимото съдържание на сяра в стоманата.
Всъщност, както показва практиката, при паралелни операции по десулфуризация и нагряване в блока за кофа-пещ, степента на използване на трансформатора е около 50%, което води до увеличаване на разходите за обработка и намаляване на производителността.
Следователно, в процеса на обработка на стомана извън пещта се използва технология за непрекъсната десулфуризация, която започва веднага след въвеждането на шлаката в блока на кофата-пещ и завършва след завършване на вакуумирането, включително продухване на метала в кофата с инертен газ в изчаквателна позиция. Това събитие позволява да се намали продължителността на метала в кофата, да се увеличи степента на използване на трансформатора и да се намалят топлинните загуби. Крайният етап на десулфуризация на стоманата, който се извършва в камерен дегазатор, позволява да се постигне изключително ниско съдържание на сяра (до 0,001%) и поради интензивното смесване на метала с шлаката без достъп на въздух предотвратява опасността от абсорбция на азот и окисляване на стопилката по време на обработката, което значително увеличава резултата от рафинирането.