Задача номер d-18
За износващи се зъбни колела се използват карбуризирани стомани, както и подобрени стомани след азотиране.
1.Изберете стомана и задайте режими на топлинна и химико-термична обработка за леко натоварено зъбно колело с диаметър 60 mm, максимално сечение 20 mm, ако работната температура на детайла не надвишава 75 ºС. Масова продукция. Начертайте график за топлинна обработка, който включва топлинна и химиотермична обработка в координати температура-време.
2.Опишете процеса CHTO, както и структурните трансформации, които се случват на повърхността и в сърцевината на детайла на всички етапи на топлинна обработка. Посочете крайната твърдост на повърхността и сърцевината на зъбното колело след втвърдяване.
3.Предоставете основна информация за тази стомана: химичен състав съгласно GOST, обхват, изисквания за този тип продукт, механични и технологични свойства, влияние на легиращи елементи и др.
1)Зъбните колела изискват устойчиви на износване профили и зъбни краища.
Високата твърдост на повърхността е необходима, за да се предотврати абразията на контактните повърхности, когато се плъзгат. Най-пълно на това изискване отговарят стоманите с твърд повърхностен слой, както и здрава и достатъчно здрава сърцевина, способна да издържа на ударни натоварвания. Комбинацията от твърда повърхност и жилава сърцевина се постига чрез химическа топлинна обработка на нисковъглеродни стомани или повърхностно закаляване на средновъглеродни стомани.
Някои части работят при условия на повърхностно износване, изпитвайки
и динамични натоварвания. Тези части са направени от
съдържащи нисковъглеродни стомани0,10–0,30% С, след което се подлагат на
За малки продукти, некритични части
използват се стомани 10, 15, 20, за части с по-сложна форма, частите са силно
натоварени, големи, нисколегирани стомани с малък
Продукти с малко напречно сечение и проста форма, работещи при
повишени специфични натоварвания (втулки, ролки, оси, гърбични съединители,
бутални щифтове и др.), са изработени от хромирани стомани 15X, 20X, съдържащи
около 1% Cg. При съдържание на хром до 1,5% се увеличава концентрацията на въглерод в карбуризирания слой, образува се легиран цементит (Fe, Cr) 3C, увеличава се дълбочината на евтектоидния слой, а след термична обработка се увеличава и дълбочината на втвърдения слой. Допълнителното легиране на тези стомани с ванадий (0,1 (0,2%) - стомана 15HF) допринася за производството на по-фини зърна, което подобрява пластичността и якостта.
За малки и средни колела на инструменти, селскостопански машини се използват хромирани стомани 15X, 15XF, 20XP.
Хромните стомани 15X, 20X, както и тези, съдържащи допълнителен ванадий (15HF) или бор (20XP), образуват група от евтини стомани с нормална якост. За да се намали изкривяването, те се охлаждат не във вода, а в масло. В резултат на това те придобиват структурата на троостит или бейнит и са малко по-малко втвърдени. Стоманите от тази група се използват за малки части (с напречно сечение не повече от 25 mm), работещи при средни натоварвания.
Избираме стомана клас 15HF.
Карбуризиране в твърд карбуратор
Технологичният процес на дифузионно насищане с въглерод се нарича циментация. Обикновено след карбуризиране стоманата се подлага на закаляване и ниско темпериране. Повърхностите, които не подлежат на циментиране, са защитени с галванично медно покритие; дебелина на медния слойе 0,02 - 0,05 mm.
Карбуризирането обикновено се извършва върху такива машинни части, които трябва да имат устойчива на износване работна повърхност и вискозна сърцевина: зъбни колела, валове и пръсти, разпределителни валове, гърбици, червяци и др.
Процесът на карбуризиране в твърд карбуризатор преминава през газовата фаза. Най-често срещаният твърд карбуризатор се състои главно от въглен с добавяне на 20-25% BaCO3 за интензифициране на процеса и 3-5% CaCO3 за предотвратяване на синтероването на частиците на карбуризатора. Частите за карбуризиране и карбуратора се опаковат в контейнер (стоманена кутия) и се нагряват в пещ до 910 - 930 °C. При нагряване въглищата взаимодействат с кислорода в остатъчния въздух според реакцията
Освен това в резултат на реакцията се образува въглероден окис
VaCO3 + C → BaO + 2CO
На повърхността на частите протича реакцията на диспропорциониране, водеща до процеса на циментиране
в резултат на което активният въглен се адсорбира от наситената повърхност, която е в аустенитно състояние, а CO2 взаимодейства с въглищата, образувайки нови порции CO.
По този начин, в резултат на обратима реакция на диспропорциониране, въглеродът се прехвърля към насищащата се повърхност.
Типичната структура на карбуризиран слой върху повърхността на мека стомана след бавно охлаждане от температурата на карбуризация се състои от хиперевтектоидни, евтектоидни и хипоевтектоидни зони. Обикновено се сравнява със схеми:
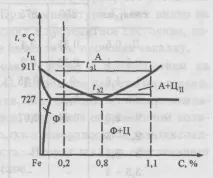
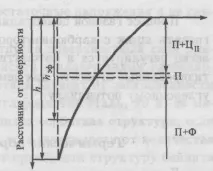
Фиг. 1. График на диаграмасъстояниеFe-Fe3C, както и промяна в съдържанието на въглерод и структура по дебелинатана циментирания слойh(диаграма)tc-температура на карбуризиране;tc1>tc2 -температура на нагряване по време съответно на първото и второто втвърдяване.
Обичайно е да се прави разлика между общата и ефективната дебелина на карбуризирания слой. Ефективната дебелина се приема като сбор от надевтектоидната, евтектоидната и половината от хипоевтектоидната зона на слоя. Ефективната дебелина на циментирания слой обикновено е 0,5 - 1,8 mm и в изключителни случаи достига 6 mm (при големи контактни натоварвания върху циментираната повърхност).
Структурата след карбуризиране се оказва едрозърнеста поради дългото задържане на частите при температура на карбуризиране. Продължителността на изотермично задържане по време на карбуризиране зависи от дадената дебелина на слоя и марката на цементираната стомана.
Топлинна обработка след карбуризиране
За да се получи определен набор от механични свойства след карбуризиране, е необходима допълнителна термична обработка на частите.
В зависимост от условията на работа, както и от стоманата, избрана за производството на детайла, режимът на термична обработка на втвърдяване може да се различава. За леко натоварени триещи се машинни части, които изпитват динамично натоварване при работни условия, в резултат на топлинна обработка, е необходимо да се получи не само висока повърхностна твърдост, но и висока якост (например за зъбни колела - висока якост на огъване), както и висока якост на удар. За да се осигурят тези свойства, е необходимо фино зърно, както на повърхността на детайла, така и в сърцевината. В такива случаи цементираните детайли се подлагат на сложна термична обработка, състояща се от две последователни закалки и ниско темпериране.
При първото закаляване детайлът се нагрява до температура с 30-50°C по-висока от температурата Ас3 на закалената стомана.
По време на второто втвърдяване частта се нагрява до t32 с превишаване на температурата с 30-50 ° CAc1 (виж Фиг. 1).
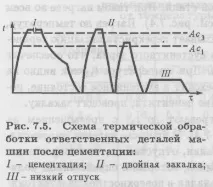
Крайната операция на термична обработка е ниско темпериране при 160–200°C, което намалява остатъчните напрежения и не намалява твърдостта на стоманата.