Запояване на високоскоростни ножове
Запояване на високоскоростни ножове
Спояването на пластини от бързорежеща стомана към корпуса на инструмента е трудно, тъй като след запояване те трябва да бъдат термично обработени.
Същността на комбинирането на процеса на запояване с термична обработка е, че обикновената спойка се поставя в специални камери, направени в тялото на инструмента или в плочата. След обработка на тялото и фиксиране на плочите, инструментът се подлага на запояване и термична обработка, като предварително се вари в наситен воден разтвор на боракс. Разтворът на боракс, проникващ в пролуките между плочите и тялото, осигурява въвеждането на поток в зоната на запояване.
Спояващи сплави. За производството на запоени високоскоростни инструменти се използват дифузионни сплави-припои от четири степени. Химичният им състав е даден в табл. 89.
Таблица 89
Химичен състав на спойващи сплави
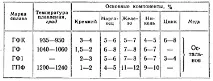
Припоят GFK има много предимства пред другите припои; може да се препоръча като най-универсален за производството на запоени високоскоростни режещи инструменти. Припои GF и GF1 могат да се използват за запояване на инструменти от стомани R9 и R18. Поради високата точка на топене, GPF спойката е с ограничено приложение и се използва само за инструменти за запояване, изработени от стомана P18.
В зависимост от наличното оборудване в завода, припоите GFK, GF и GF1 могат да се произвеждат с помощта на верига за топене на високочестотна единица или в електродъгова пещ.
В табл. 90 показва химичния състав на заряда на спойващи сплави върху чисти метали, като се вземат предвид отпадъците. Технологичният процес за получаване на HFK спойка в индукционна пещ е даден в табл. 91.
Химичен състав на шихтата от спойващи сплави, %
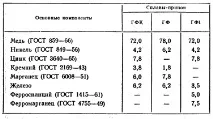
Технологичен процес за производство на HFC сплав в индукционна пещ
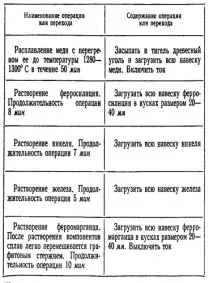
HFK спояващ прах се получава чрез фрезоване на слитък от сплав с нож за резба.
За производството на високоскоростни ножове някои фабрики използват заваръчен прах със следния състав (g):
Компонентите на праха се натрошават и внимателно се смилат.
Подготовка на повърхността за запояване. Грапавостта на повърхностите, които ще се съединяват, трябва да отговаря на степени 5 и 6. Повърхностите на фугите не трябва да са без резки, драскотини, драскотини, неравности, мръсотия и масло. Плоскостта на повърхностите, които ще се съединяват, трябва да бъде в рамките на 0,04–0,07 mm за инструмент с диаметър 50–300 mm. В случаи на конична връзка и припокриване с наклонен разрез, ъглите на конус и наклон на свързващите части трябва да бъдат еднакви. Допуска се отклонение от номиналната стойност на ъглите не повече от ± 1 °. В зависимост от конструкцията на инструмента се използват различни видове връзки от бързорежеща стомана с тялото на инструмента (Таблица 92).
Таблица 92
Видове свързване на бързорежеща стомана към тялото на инструмента
Продължение на таблицата. 92
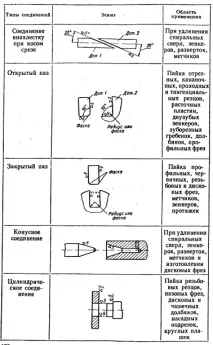
Сглобяване на инструмента преди запояване. Фиксирането на записи към кутията преди запояване е една от основните операции по сглобяване. Извършва се с конични или цилиндрични щифтове и свързващи втулки.
Плочите са прикрепени към корпуса на инструмента с много остриета с два конични щифта, което осигурява надеждно закрепване. В случаите, когато размерите на плочите не позволяват поставянето на два щифта, плочата се закрепва с един щифт, разположен в центъра ѝ. Закрепването с ролков щифт се използва при производството на някои едностранни и многостранни инструменти, които не изискват допълнителномеханична обработка.
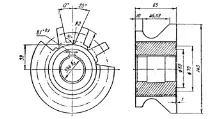
Фиг. 68. Фреза за профили
В този случай закрепването на плочите към тялото с щифтове е необходимо, за да се предотврати движението на плочите спрямо тялото по време на запояване и термична обработка.
Типичните монтажни единици на инструмента, в зависимост от вида на връзката, са дадени в таблица. 93.
Процедурата за сглобяване на инструмент преди запояване може да се види в примера за производство на профилен нож (фиг. 68).
Процесът на сглобяване се състои от следните стъпки:
1) почистване на тялото и плочите и почистване на повърхностите за запояване;
2) маркиране върху плочите и гнездата на тялото на инструмента на сериен номер;
3) маркиране върху плочите на местата на отворите за коничните щифтове;
4) пробиване на отвори върху плочите до дълбочина 1,5-2,0 mm:
5) фиксиране на тялото на инструмента в менгеме, монтиране на високоскоростна режеща плоча в гнездото на тялото, фиксирането й и пробиване на отвори за конични щифтове в плочата и тялото; по този начин се осветяват всички пластини по тялото на инструмента;
6) подрязване на основния край на тялото на инструмента; на струг основата за по-нататъшна обработка са краищата на плочите, които са в една и съща равнина;
7) закрепване на високоскоростни режещи плочи в тялото на ножа, за което е необходимо тялото да се фиксира в менгеме, да се монтира плочата в съответното гнездо на тялото според марката и да се натиснат коничните щифтове с удар с чук;
Типични комплекти инструменти
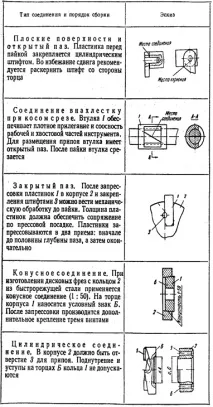
8) отрязване на стърчащите краища на щифтовете;
9) проверка на пролуките между плочите и тялото с щуп; празнините не трябва да надвишават 0,08 mm.
След сглобяване на фрезата с фиксиранплочите влизат в механичната секция за подрязване на основния край на плочите „като чисти“ и поддържане на профила на ножа според шаблона с допустимо шлайфане от 0,6–0,8 mm на диаметър.
Запояване с HFK припой и термична обработка. Запояването може да се извърши на t.v. ч., в газови и електрически пещи с неокислителна среда, както и във вани с бариев хлорид.Процесът на запояване и топлинна обработка се състои от следните стъпки:
1) в края на основата (фиг. 69) свредло се излива в специален жлеб и инструментът се поставя в пещ, където се нагрява до 800-850 ° C;
2) инструментът се изважда от пещта и спойката под формата на малки чипове, смесени с боракс, се излива в специален жлеб, след което инструментът се поставя във втората камера на пещта с температурата, необходима за нагряване за втвърдяване на високоскоростна стомана (за стомана клас P9 температурата на нагряване е 1230 ° C, а за P18 1280 ° C);
3) охлаждане на инструмента във въздуха до температура 1000-1050°C;
4) охлаждане в масло до температура 100-150°C;
5) двойно темпериране в камерна електрическа пещ или селитрова баня при температура 560 ° C с експозиция 1 час;
6) контрол на твърдостта на режещата част на инструмента;
7) закаляване на отвора на инструмента на високочестотна инсталация.
След пясъкоструйна обработка и външна проверка на качеството на запояване, инструментите се прехвърлят в отделението за шлифоване за дообработка и заточване.
1 — тяло на ножа; 2—плоча; 3—флюс и спойка; 4 - щифт
Най-добрият метод за нагряване за запояване и термична обработка на инструменти е нагряването във вана с бариев хлорид. При нагряване на инструмента в солена баня и нагряване за охлаждане във вана с бариев хлорид, потокът не се използва, тъй като инструментът се нагрява в течна среда и ставите не се окисляват.
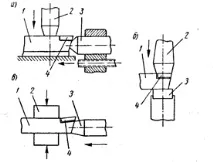
Фиг. 70. Схема за запояване на високоскоростни ножове:
1 - държач; 2, 3 - електроди; 4 - плоча
Непосредствено преди разтопяването на спойката се включва дълъг ток. След като спойката се стопи, токът се изключва. Когато плочата се разтопи с припой по целия шев, тя се притиска към държача с острия край на металния прът, докато спойката се втвърди напълно. След това електродът 3 се отстранява, горният електрод 2 се изтиска, след което инструментът се отстранява с щипки и се поставя в кутия с нагрят пясък за бавно охлаждане.
Схемата за запояване на режещи плочи на челни машини е показана на фиг. 70б. В този случай държачът на ножа се затяга в контактните челюсти, а електрод 2 се захранва от страната на предната повърхност на ножа, който е фиксиран в подвижната част на затягащото устройство на машината. Технологията на запояване на челни машини не се различава от запояване на точкови машини.
Схемата за запояване, показана на фиг. 70, a, b, може да се препоръча за твърди сплави T15K6 и T30K4, които се характеризират с повишена крехкост. В този случай плочата от твърда сплав е защитена от напукване, тъй като няма вредно преходно съпротивление от електродите към плочата. Схема на запояване съгласно фиг. 70, се препоръчва за твърдосплавни пластини клас VK8.
Електроконтактните машини за точково заваряване могат да се използват и за запояване на високоскоростни режещи плочи. В този случай тялото и плочата се нагряват до температура от 950-1000 ° C, след което под плочата се излива прах за заваряване и нагряването продължава, докато се стопи. Високоскоростна стоманена плоча може да бъде заварена към тялото на инструмента без спойка.
На електрически машини за челно заваряване се запоява инструмент с много остриета.