Защита на резервоара от корозия
Резервоарите също са защитени от корозия чрез пасивни и активни методи.
Пасивното включва използването на всички видове защитни покрития, които изолират агресивната среда от повърхността на резервоара.
Началото на изграждането на резервоари се предшества от инсталирането на хидрофобизирана основа под тях, за да се предотврати контакт на външната повърхност на дъното с почвената влага. Най-често за тези цели се използват пясъци, смесени в съотношение 9: 1 с едно от следните свързващи вещества: мазут, масло, течен нефтен битум, катран и др. Дебелината на хидрофобизираната основа е 0,1-0,3 m.
Пасивната защита на вътрешната повърхност на резервоарите се осъществява чрез покрития на базата на боя и лак и полимерни материали, цинк и др.
Характеристики на някои бои и лакове и покрития на вътрешната повърхност на резервоарите
Време за съхнене при 15-20 °С, h
Дебелина на системата за покритие, µm
Грунд VL-02, 08,
Боя XC-717 (XC-720)
Буквар V L-08
Буквар V L-08
Нов тип горен слой е емайллак от епоксидна смола EP-AS-6/2-1. Това е състав, съдържащ маслен полимер Aemol, сажди, епоксидна смола и други компоненти. Емайлът се произвежда като пълен комплект под формата на два компонента: полуфабрикат от емайл и втвърдител. Смесват се непосредствено преди употреба в съотношение 50:3 и се нанасят върху повърхността на резервоара ръчно с четка, валяк или пневматичен спрей на два слоя. Пълното втвърдяване на емайла при 18-22 °C настъпва за 7 дни.
Проводимите полиуретанови покрития се използват и за защита на вътрешната повърхност на резервоарите от корозия. Например, беше получено покритие PU1 (TU 2226-011-16802026-97).на базата на полиестер Laprol 5003-2B-10 и е еднокомпонентна система, втвърдена от въздушна влага. Времето за втвърдяване е 12-24 часа при температури от -20 до +50 °C, дебелината на нанесеното покритие е до 300 микрона. Покритие PU-1 върху метална повърхност е прозрачен тънък, лъскав, много еластичен филм с висока адхезия към метала. За да се придадат специални свойства на състава на покритието, могат да се въведат пигменти, метални прахове (например алуминий или цинк), сажди, сажди, графит.
Покритието PU-1 се нанася върху повърхността с четка или валяк или с безвъздушна пръскачка. Преди нанасяне на покритие металните повърхности се почистват, за да се образува повърхност с развита грапавост. Покритието се оформя чрез последователно нанасяне на три слоя материал. Преди нанасяне на всеки следващ слой, предишният се изсушава.
За да се премахне статичното електричество, в покритието PU-1 се въвежда сажди или метален пълнител,
Внесеният аналог на покритието PU-1 е покритието NORCO (Франция). Сравнителните тестове на тези покрития показаха, че PU-1 не е по-нисък от него по качество.
Препоръчителният дизайн на покритието за резервоари е както следва: антикорозионен грунд (1 слой), PU-1 (2 слоя). Последният може да бъде направен с добавяне на сажди за премахване на статичното електричество.
Друго ефективно средство за защита на вътрешната повърхност на резервоарите от корозия са метализиращите покрития, като например цинк. Имат добра устойчивост на нефтопродукти, атмосферен въздух, прясна и морска вода. Те защитават стоманената повърхност, като не само я изолират от контакт с корозивна среда, но и електрохимично, действайки върху протектора.
Оптималнодебелината на метализираното цинково покритие е 120–150 µm. При по-малка дебелина защитните свойства намаляват, а при по-голяма се влошава адхезията на покритието към стоманената повърхност поради големи вътрешни напрежения, появяват се лющене и подуване на покритието.
Процесът на метализация включва две последователни операции: термична абразивна подготовка на повърхността и газотермично нанасяне на метализиращо антикорозионно покритие.
Термоабразивната подготовка на повърхността се извършва с високотемпературна газова струя с въведен в нея абразив (фракции пясък = 1,5 mm). Конструкцията на работния апарат е компактна течна горелка, работеща с авиационно гориво или осветителен керосин. Горивото се пулверизира в горивната камера и се смесва с въздуха, идващ от компресорите. В процеса на изгаряне на газовъздушната смес се образува високотемпературна газова струя, в която се вкарва абразив (технологичен пясък). На изхода от дюзата на апарата скоростта на изтичане на работната струя е повече от 1200 m/s, което превишава производителността на конвенционален струен апарат повече от три пъти. Комбинацията от термични и механични методи за въздействие върху третираната повърхност позволява не само премахване на ръжда, стари покрития, придобити израстъци и отлагания, но и обезмасляване на повърхността и нейното химически активиране. При последващото нанасяне на антикорозионно покритие, това допринася за подобряване на адхезията на покриващия материал към основния материал.
Метализирането на повърхността на резервоара се извършва чрез термично пръскане на разтопен алуминий или цинк не по-късно от 6 часа след почистване на повърхността на резервоара. Термичното пръскане се извършва с помощта на същия апарат като термичния абразивподготовка, но на него допълнително е монтиран механизъм за пневматично подаване на алуминиева или цинкова тел, а в горивната камера е монтирана специална дюза за подаване на телта в зоната на топене.
Разпръснатият метал под формата на фини разтопени частици излита от дюзата на апарата със свръхзвукова скорост, което осигурява значителна сила на удара на частиците с повърхността, която ще бъде покрита. При удар частицата от отложения метал се сплесква и втвърдява с едновременно дифузионно проникване на част от отложения метал в стената на резервоара. Така се постига висока якост на залепване на покритието. Следващите слоеве, поради високата кинетична енергия на частиците, лягат плътно върху предварително отложения метал.
Дебелината на покритието се определя в зависимост от предназначението му и необходимия период на антикорозионна защита. При дебелина на покритието 120-250 микрона експлоатационният му живот е 10-15 години.
Някои технически характеристики на системата за нанасяне на метализиращо покритие са следните: налягането на подавания сгъстен въздух е 0,9 MPa; капацитет за подготовка на повърхността до 25 m 2 /h; производителност за повърхностна метализация до 20 m 2 /h; разходът на гориво на 1 m 2 от третираната повърхност е до 2,3 литра.
Предимствата на процеса на метализиране на резервоари в сравнение с други методи за нанасяне на антикорозионни покрития (бои и лакове, епоксидни и фенолни смоли, полимери и др.) са високата му технологичност, дълъг експлоатационен живот на покритието и възможността за работа дори през зимния сезон.
Пасивните методи също включват защита срещу корозия на вътрешната повърхност на покрива, дъното и корпуса, в контакт с газовото пространство на резервоара и произведената вода, с помощта на инхибитори - веществачието добавяне в малко количество към корозивна среда забавя или значително потиска процеса на корозия. Летливите инхибитори се въвеждат в газовото пространство, а водоразтворимите се въвеждат в произведената вода. Използването на инхибитори не дава голям ефект поради редовното дрениране на произведената вода и постоянното "дишане" на резервоарите.
Активни методи за борба с корозията на резервоарите са тяхната катодна и жертвена защита. Катодната защита се използва предимно за предотвратяване на корозионно увреждане на дъното.
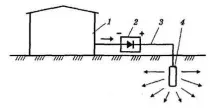
Принципна схема на катодна защита на резервоари от почвена корозия: 1 - резервоар; 2 - станция за катодна защита; 3 - дренажен кабел; 4 - анодно заземяване
Схематичната диаграма на катодната защита на дъното срещу корозия на почвата е подобна на схемата за защита на тръбопровода: „минус* източник на постоянен ток (RMS) 2 е свързан чрез дренажен кабел 3 към резервоар 1, а „плюс“ е свързан към анодна маса 4. Минимален защитен потенциал от -0,87 V се поддържа на резервоара чрез референтен електрод с меден сулфат (MSE). Ако корозията на дъното се увеличи под въздействието на жизнената активност на анаеробни сулфат-редуциращи бактерии, тогава минималният защитен потенциал се увеличава до -0,97 V според ITU. Целесъобразно е да се използват катодни станции за защита на резервоарите от корозия на почвата, ако площта на контакт на гол метал с околната почва надвишава 15 m 2.
Нанесете катодна защита и за предотвратяване на увреждане от корозия на вътрешната повърхност на дъното на резервоарите. Това се прави в случаите, когато:
■ високо ниво на произведена вода;
■ специфичното съпротивление на произведената вода е повече от 1 Ohm-m или концентрацията на сол е по-малка от 6 g/l;
■ Произведената вода съдържа сероводород.
Схематичната диаграма на катодната защита в този случай предвижда инсталирането на точкови, радиални или компактни пръстеновидни аноди директно вътре в резервоарите.
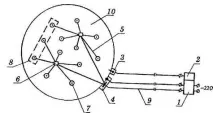
Принципна схема на катодната защита на резервоара срещу вътрешна корозия: 1 - станция за катодна защита (CPS); 2 — предпазен блок; 3 - сензор за предпазен блок; 4 - въвеждаща кутия; 5 - захранваща мрежа; c - разклонителен съединител; 7 - аноден свързващ блок; 8 - анод; 9 - кабелна линия; 10 - резервоар
Трябва да се отбележи, че използването на катодна защита за резервоари с нефтопродукти е опасно от гледна точка на пожар. Искра, генерирана при прекъсване на електрическа верига, може да причини пожар и експлозия.
В случай на използване на жертвена защита, възможността за образуване на искра е изключена, тъй като потенциалната разлика между протектора и защитената конструкция е малка. Защитната защита на резервоарите от корозия на почвата се извършва от единични, групови концентрирани и групови диспергирани протектори (фиг. 9.8). По-сложна защитна схема се използва в почви с високо електрическо съпротивление.
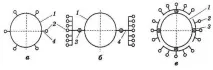
Принципна схема на защита на протектора от почвена корозия: а - единични протектори; b - групови концентрирани протектори; c - групови разпръснати протектори; 1 - резервоар; 2 - протектори; 3 - контролно-измервателни колони; 4 - дренажен проводник
Защитната защита на дъното и първия пояс на резервоарите от вътрешна корозия стана широко разпространена. За тези цели се използват магнезиеви протектори от типа PMR, разработени от VNIIST и Березниковския титаново-магнезиев завод, както и видове AKTsM, AP и ADBM.
Типът на протектора PMR е цилиндър със съотношение на височина към диаметър 0,2-0,4,с вдлъбнатина в горната част под формата на преобърнат пресечен конус. Това се прави, за да се увеличи повърхността на протектора и съответно силата на тока в началния период на неговата работа. Стоманена втулка е притисната в центъра на протектора 16, за да се осигури контакт на протектора с дъното.
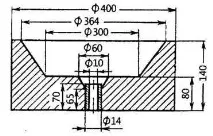
Тип на протектора PMR-20
Серийно произвежданите протектори PMR-5, PMR-10, PMR-20 се различават по геометрични размери и тегло (стойността на последното в килограми е посочена в марката на протектора).
Протекторите от типа PMR се препоръчват да се поставят на дъното по концентрични кръгове, разстоянието между които се приема равно на два пъти радиуса на действие на един протектор. При монтиране на протектори първо се почиства площадка под формата на кръг с диаметър 1,4-1,5 m, след което в центъра й се заварява стоманен прът с диаметър 8 mm и височина 35-60 mm и почистеното място се изолира. След това протекторът се нанизва на посочения прът и се заварява към него (чрез пресована стоманена втулка), след което мястото на закрепване се намазва с епоксидна смола.
Понастоящем по-често се използват протектори под формата на дълги пръти от алуминиева сплав с дължина до 6 м. Протекторите на марката AKCM имат кръгло (диаметър 40 и 60 mm) сечение, докато AP и ACBM имат трапецовидна. През центъра на всяка от тях минава стоманена пръчка с диаметър 5-8 mm. На дъното на резервоара са поставени дълги протектори в концентрични пръстени, свързани последователно един към друг. Те са изолирани от директен контакт с дъното с полиетиленови пръстени или ленти.