3.1.2. Предимства на формоването на метал
Обработката на метали под налягане е широко разпространен технологичен процес. При определени условия той успешно се конкурира с други методи за получаване на части, включително рязане, което в момента е основното за машиностроенето.
Получаването на продукти с необходимите размери и форми по време на обработка под налягане се постига чрез пластично движение на метални частици. Това е основната разлика и предимство на обработката под налягане в сравнение с рязането, при което формата на продукта се получава чрез отстраняване на част от детайла. В това отношение значително предимство на формоването на метал чрез натиск е значително намаляване на металните отпадъци, както и увеличаване на производителността на труда (намаляване на времето за обработка на продукта), тъй като в резултат на еднократно прилагане на сила формата и размерите на деформируемия детайл могат да бъдат значително променени. Някои методи за формоване на метали позволяват да се получат части, които изобщо не се нуждаят от допълнителна обработка. В допълнение, промяната във физичните и механичните свойства на метала на детайла, която придружава пластичната деформация, както и рационалното подреждане на влакната на неговата структура, позволява да се получат части с най-добри експлоатационни свойства (висока устойчивост на износване, якост, твърдост и др.) с най-малка маса.
По този начин високата производителност на обработката под налягане, ниските отпадъци, ниската цена и високото качество на продуктите определят непрекъснатото увеличаване на ролята му в машиностроенето. Около 90% от цялата разтопена стомана и над 50% от цветните метали се подлагат на обработка под налягане.
Обработката под налягане не винаги постига необходимата структура и необходимите свойства на получения продукт и не винаги се възпроизвежда точно зададената форма,размери, повърхностна обработка на детайла, следователно след обработка под налягане обикновено се прибягва до термична обработка и рязане.
3.1.3. Влияние на обработката под налягане върху структурата и свойствата на металите и сплавите
В резултат на пластичната деформация се променят не само формата и размерите на детайла, но и структурата и свойствата на оригиналния метал.
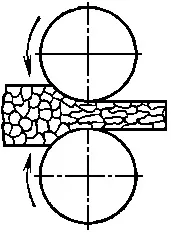
Ориз. 3.4. Схема на промяна на микроструктурата на метала при студена деформация
При обработката на метали чрез налягане се разграничават студена и гореща деформация.
Застудена деформацияе характерна промяна във формата на зърната на структурата. Те се простират по посока на най-интензивния метален поток (фиг. 3.4).Това е придружено от промяна в механичните и физико-химичните свойства на метала. Това явление се нарича втвърдяване (втвърдяване). Промяната в механичните свойства е, че характеристиките на твърдостта и якостта на метала се увеличават, докато характеристиките на пластичност намаляват. Електропроводимостта и магнитната проницаемост на сплавта (физични и химични свойства) също се променят.
Втвърдяването възниква поради изкривявания на кристалната решетка, както и поради въртенето на равнините на приплъзване по време на студена деформация.
Промените, въведени от студената деформация в структурата и свойствата на метала, не са необратими. Те могат да бъдат отстранени чрез термична обработка, като отгряване. В този случай в метала на детайла се извършва вътрешно преструктуриране на структурата, при което поради допълнителна топлинна енергия, която увеличава подвижността на атомите, нови зърна растат от много центрове в твърдия метал без фазови трансформации, замествайки удължени, деформирани зърна. Тъй като в еднакво температурно поле скоростта на растеж на зърното във всички посокие еднакъв, то появилите се нови зърна вместо деформираните имат приблизително еднакъв размер във всички посоки.
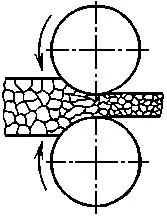
Ориз. 3.5. Схема на промяна на микроструктурата на метала при гореща деформация
Феноменът на зараждане и растеж на нови равноосни зърна вместо деформирани, удължени, протичащи при определени температури, се нарича рекристализация. За чистите метали прекристализацията започва при абсолютна температура, равна на 0,4 от абсолютната точка на топене на метала. Рекристализацията протича с определена скорост и времето, необходимо за рекристализация, е толкова по-малко, колкото по-висока е температурата на нагряване на деформирания детайл.
Гореща деформацияе деформация, характеризираща се с такова съотношение на скоростите на деформация и прекристализация, при което прекристализацията има време да настъпи в целия обем на детайла и микроструктурата след обработка под налягане се оказва равноосна, без следи от втвърдяване (фиг. 3.5).По този начин промяната на формата на детайла при температура над температурата на рекристализация е придружено от едновременно протичане на втвърдяване и рекристализация.
За да се осигурят условия за протичане на гореща деформация, с увеличаване на нейната скорост температурата на нагряване на детайла се повишава (за да се увеличи скоростта на рекристализация).
По време на гореща деформация устойчивостта на деформация е около 10 пъти по-малка, отколкото при студена деформация, а липсата на втвърдяване води до факта, че устойчивостта на деформация (граница на провлачване) по време на обработка под налягане се променя леко. Това обстоятелство основно обяснява защо горещата обработка се използва за производството на големи части, тъй като изисква по-малко сили на деформация (по-малко мощно оборудване).
Трябвавземете под внимание, че при работа с натиск на детайли с малки размери (малка дебелина) е трудно да издържат на необходимите температурни условия поради бързото им охлаждане във въздуха и от контакт с по-студен инструмент.
При гореща деформация пластичността на метала е по-висока, отколкото при студена деформация. Поради това е препоръчително да се използва гореща деформация при обработка на трудни за деформиране метали и сплави с ниска пластичност, както и отлети метални заготовки (блокове). В същото време при гореща деформация се получава по-интензивно окисляване на детайла (на повърхността се образува слой от мащаб), което влошава качеството на повърхността и точността на получените размери.
Студеното формоване без нагряване на детайла води до по-голяма точност на размерите и по-добро покритие на повърхността, отколкото формоването при висока температура. Трябва също да се отбележи, че обработката под налягане без предварително нагряване на детайла позволява да се намали продължителността на технологичния цикъл, улеснява използването на средства за механизация и автоматизация, повишава производителността на труда и намалява разходите за обработка.
Първоначалният детайл за много процеси на формоване на метал е слитък. Кристалната структура на слитъка е нееднородна (кристалите имат различни форми и размери). Освен това има порьозност, газови мехурчета и др. Горещата обработка на слитък чрез налягане води до деформация и раздробяване (поради рекристализация) на кристалитите и частично заваряване на пори и черупки. По този начин, по време на гореща обработка чрез натиск на слитъка, плътността на метала се увеличава и неговата структура също се подобрява (металът придобива финозърнеста структура).
В оригиналния слитък примесите и неметалните включвания обикновено се намират по границите на кристалите. В резултат на обработкатаналягане, както вече беше споменато по-рано, неметалните включвания се изтеглят под формата на влакна в посоката на най-интензивния метален поток. Тези влакна се разкриват чрез ецване и се виждат с просто око под формата на така наречената фиброзна макроструктура. Влакнестата макроструктура на метала, получена в резултат на обработка под налягане на лята заготовка, не може да бъде разрушена нито чрез термична обработка, нито чрез последваща деформация. В зависимост от естеството си, обработката под налягане може да промени само посоката и формата на влакната на макроструктурата.
Влакнестата структура на деформирания метал води до анизотропия на неговите свойства (якостта и ударната якост на метала по дължината на влакната му са по-високи, отколкото напречно). Следователно потокът от метал по време на обработката под налягане трябва да бъде насочен така, че влакната да съвпадат с посоката на най-големите напрежения в частта по време на нейната работа. В този случай общите препоръки са следните: необходимо е най-големите напрежения на опън, възникващи в частите по време на работа, да бъдат насочени по протежение на влакната и ако някой елемент от тази част работи при срязване, тогава е желателно

Ориз. 3.6. Макроструктурата на коляновия вал и работните сили, действащи върху вала по време на неговата работа:
a - структура, получена чрез рязане, b - структура, получена чрез щамповане
сили на срязване, действащи напречно на влакната, е необходимо влакната да се доближават до външните повърхности на детайла тангенциално и да не се срязват от външните повърхности на детайла. Тъй като посоката на влакната зависи от естеството на деформацията на детайла, желателно е да се получи такава подредба на влакната в готовата част, при която тя ще има най-добри свойства. 3.6 показва макроструктурата и силите на натоварване по време на работа на коляновия валвал, направен от валцована заготовка само чрез рязане (фиг. 3.6,а)и щамповане, последвано от рязане (фиг. 3.6, б). Якостта на вал, получен чрез щамповане, е с 10 ... 15% по-висока от тази на вал, получен чрез рязане.