Цилиндрово-бутална група, Камиони и спецтехника
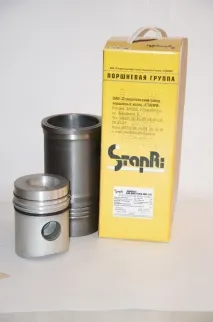
Износоустойчивост на групата цилиндър-бутало
Още в началния етап на производство на дизелови двигатели YaMZ-236 и YaMZ-238 беше постигната сравнително висока устойчивост на износване на части от цилиндрово-буталната група. Увеличаването на ресурса на двигателя изисква допълнително повишаване на устойчивостта на износване на частите от групата цилиндър-бутало, за да се удължи периодът на основен ремонт на автомобила.
При ниска скорост на радиално износване на цилиндрови втулки и бутални пръстени при условия на работа на дизела, изборът на оптимална конструктивна опция за части е ограничен от прекомерната продължителност на експлоатационните тестове, чиято продължителност се увеличава с увеличаване на нивото на устойчивост на износване.
Условията на работа на интерфейсните елементи в периода на основен ремонт на двигателя зависят от техните първоначални размери, смазване, температура на частите, тяхната деформация, износване и други фактори.
Износването на частите се характеризира както с максималното отклонение на размерите (например диаметъра на цилиндровите втулки, радиалната дебелина на буталните пръстени) от първоначалните стойности, така и с формата на диаграмата на износване.
Известни са следните видове разрушаване на буталната група на дизелов двигател: абразивно разрушаване, корозия, настройка, ерозия и мигане.
Интензивността на износване на свързващите части зависи от качеството на маслото, температурата на частите, качеството на метала, както и естеството на тяхната макро- и микрогеометрия и други фактори. Условията на работа на свързващите се части се влошават поради наличието на вибрации, дължащи се на динамичността на работния процес и „преместването“ на буталото.
Опитът на вътрешното автомобилно двигателостроене показва двусмислена зависимост на разрушаването или износването на части от действието на всеки от изброените фактори, т.е. необходимостта да се вземе предвид тяхната връзка. Следователно възможносттаРазпространението на известни концепции за влиянието на определени фактори върху интензивността на износване или разрушаване на части от цилиндрово-буталната група на дизелов двигател с определен дизайн е обект на цялостно проучване, резултатите от което могат да послужат като основа за методология за принудително изпитване. В резултат на това при разработването на методология за принудително тестване на части от тази група бяха идентифицирани следните задачи:
- предоставяне на диаграма на износване на частите, подобна на тази за условията на работа на двигателите;
- увеличаване на скоростта на износване в границите, при които е възможно да се проверят дадените варианти на възела в рамките на ограничен интервал от време, т.е. избор на ниво на принудително износване.
Силата на шефовете на групата цилиндър-бутало
Последният етап от изследването на здравината на шефа е оценката на тяхната здравина по време на работа на двигателя и прогнозирането на експлоатационния живот на буталото. Тестването на производителността за тази цел е много трудно, особено при избора на материал на буталото и метод на топлинна обработка, когато са необходими сравнителни тестове на няколко опции.
За да се ускори тестването на буталните глави, е препоръчително да се увеличат напреженията в тях директно върху работещия двигател. За да се увеличи максималното налягане на горене, се провеждат тестове с увеличен ъгъл на изпреварване на впръскването. В този случай напрежението в шефовете се увеличава с 1,5 пъти. При такова увеличение на напреженията не може да се очаква рязко намаляване на продължителността на тестовете, поради което бяха използвани още два метода за увеличаване на напреженията, които бяха открити при изследване на напреженията в шефовете на специален щанд.
Първият начин е да се въведе фаска на повърхността на главината отвътре. В този случай напреженията в края на главата се увеличават с коефициент 10.
Вторият начин за увеличаваненапрежения - увеличаване на вътрешния диаметър на буталния щифт, т.е. намаляване на модула на сечението. Намаляването на последния с 10% води до 2-кратно увеличение на напрежението в края на шефа.
Според този метод буталата се тестват на двигателя за 250-300 часа, повредите на буталата се отбелязват след 100 часа работа, до 300 часа вероятността за правилна работа на буталата достига 0,6.
Първият пръстеновиден джъмпер е един от най-натоварените елементи на буталото. Максималните напрежения в основата на преградата възникват в момента, в който се достигне максималното налягане в горивната камера. Най-целесъобразно е силата на джъмпера да се оцени експериментално.