Демонтаж на корпуса и отстраняване на старото покритие от него
Демонтаж на заварени елементи на каросерията.
Повечето части в модерното безрамково тяло се съединяват чрез точково заваряване. В машиностроителните заводи точковото заваряване се извършва от роботи, които осигуряват дадена стъпка (разстояние от една точка до друга) на заваряване. Още на етапа на проектиране на каросерията на автомобила се изчислява определена стъпка на заварени точки и е препоръчително да се придържате към този параметър по време на ремонт.
Всяка точка може лесно да се различи по отпечатъка на електрода, който е оставен върху метала. Отпечатъкът е малка вдлъбнатина (дълбочина - десети от милиметъра, диаметър - 4 ... 6 mm).
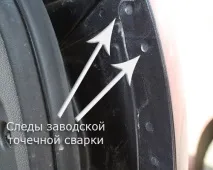
За отваряне на щампа, затворена боя, последната се почиства. Заварените части се разделят по три начина:
1) частично и напълно пробийте точките на заваряване;
2) изрежете точките на заваряване;
3) листът се отрязва възможно най-близо до заваръчната линия, металът се откъсва между заваръчните точки и след това се почиства.
При първия метод, за центриране на свредлото (независимо кой инструмент за пробиване се използва), центровете на заваръчните точки се пробиват. Пробиването се извършва с помощта на специални инструменти, които работят като фрези. Електрическа бормашина, въртяща ножа около неподвижен център, образува кръгло подрязване около обиколката на заваръчната точка. Дълбочината на фрезоване обикновено е равна на дебелината на листа, такава дълбочина осигурява разделянето на заварените елементи. Центърът на заваръчната точка остава върху листа, който не е фрезован. Тази точка може да се отреже с помощта на друг нож, който се вкарва в предварително направено цилиндрично подрязване. След като изрежете цилиндричен жлеб, незабавно се използват две електрически бормашини, за да се премахне центърът на заваръчната точка, това е по-удобно (центърът на точката се отстранява без смяна на инструмента). Същоможе да се изреже цилиндричен жлеб през цялата заваръчна точка, след което заварените елементи се разделят и металът, останал в заварените места, се почиства. В този случай необработената зона на листа остава непроменена.
Можете да използвате спирални свредла за пробиване. Диаметрите на свредлото и мястото на заваряване са равни. Когато всички точки на заваряване са пробити и частите са разделени, върху опорната част остават проходни отвори. Те се затварят с спойка, като се използва твърдо спояване, след което се почистват с шлифовъчен инструмент. За предпочитане е да се използва спояване, а не газово заваряване, спояването осигурява по-ниска температура на нагряване, което помага да се намали деформацията, елиминирана чрез изправяне.
Още един начин. В централната част на точката на заваряване се пробива малък отвор, който не минава през долния лист. Диаметър на отвора 3 мм. Отворът води режещата част на свредлото. Диаметърът на свредлото се взема малко по-голям от диаметъра на точката на заваряване. При свредлото режещата част се заточва почти под ъгъл от 180 градуса, режещата част на долния лист (върху повърхността му) оставя малка издатина. По време на зенкериране се уверете, че свредлото не навлиза твърде дълбоко в метала и не пробива долния лист.
При втория метод се използва специално длето, ръчно или пневматично, за изрязване на точките на заваряване. Поставяйки длето между листовете, прорезът му трябва да покрива заварената точка, която се изрязва.
При третия метод (рязане на листа) повредената част се отстранява не изцяло, а на части. Щамповането на повредената част се извършва възможно най-близо до заваръчната линия с помощта на пневматичен инструмент, оборудван с длето или конвенционален длето. За тази цел не се използва кислородно-ацетиленова горелка, тъй като металът от нея се нагрява силно, причинявайкивлошаване на всички механични свойства. Когато се използва горелка, всякакви вътрешни антикорозионни покрития в близост до огнището светват, развива се корозия. След изрязване върху метала остава лента, върху която приблизително в центъра са разположени точки за заваряване.
Отстраняване на старо покритие.
Старата боя на каросерията се отстранява най-добре с пясъкоструене, но това винаги е възможно. Ето защо по-често се използва механизиран ръчен инструмент (механичен метод) или специални измивания и алкални разтвори (химичен метод) за отстраняване на старото покритие. Когато почистването се извършва заедно с боята, котленият камък и ръждата се отстраняват едновременно.
Металните сачми със зърна от 0,25 mm са най-разпространеният абразивен материал, използван за пясъкоструене на метални повърхности. За да почистите панелите на тялото от старото покритие и да получите необходимата грапавост, ъгълът на наклона на фракционната струя към третираната повърхност трябва да бъде 45 градуса, а налягането на въздуха трябва да бъде от две десети до три десети от MPa. Обработената повърхност не трябва да има грапавост от повече от 20 ... 30 микрона, поради такава грапавост новото защитно покритие ще бъде с високо качество.
Металните повърхности се обработват с фракционна струя на мобилен апарат с ръчен пистолет. Устройството автоматично регенерира абразивната струя и я подава към пистолета за бластиране. Продуктите от корозия се отстраняват механично ръчно с помощта на различни инсталации. Например нож за игла, състоящ се от парчета тел с висока якост и определена плътност на подложката. Отрязва слой метал, котлен камък, ръжда с дебелина от една стотна до един милиметър. Почистете повърхността и отстранете боята с такова ръководствоелектрически инструменти като мелница или мелница. Този метод на почистване не осигурява висока производителност и необходимото качество, така че се използва само за малки количества работа.
Химическият метод за отстраняване на покрития се състои в използването на различни измивки, които се нанасят върху повърхността с четка или спрей. Известно време след нанасяне покритието набъбва и се отстранява механично, след което повърхността се измива. Предприятията за ремонт на автомобили, които извършват големи обеми каросерийни работи, използват алкални разтвори за отстраняване на боя. Почистването се извършва във вани, където кабини, корпуси и други части са напълно потопени. За да се намали времето за ецване, се използват ускорители: етиленгликол, натриев глюконат. Разтвор (етиленгликол - 8%, натриев глюконат - 0,5%, сода каустик - 20%) с температура 95 ... 98 градуса отстранява покритието с дебелина 100 ... 150 микрона за десет до петнадесет минути. При почистване на тялото от корозионни повреди е необходимо да се определи дълбочината на корозията. За да направите това, използвайте гама-дебеломери. При ремонт на каросерия самостоятелно или в малка работилница най-често се използва смесена технология: тялото се покрива с измиване, след което се обработва с абразивен механичен инструмент. Труднодостъпните места се обработват ръчно.