Getting - Lead - Голямата енциклопедия на нефта и газа, статия, страница 2
Получаване - олово
При високи температури (около 1200 C) много сулфиди се редуцират от въглища до метал, което е основата за производството на олово, цинк и мед в промишлеността. [16]
В допълнение към топенето в мините, за преработката на богати концентрати, съдържащи до 78% от основния метал, понякога се използва топене в пещ - най-старият метод за производство на олово. В сместа (смес от сулфиден концентрат с кокс и вар) се вдухва въздух. Оловен сулфид PbS се окислява до оловен оксид PbO. Останалата част от сулфида реагира с оксид и сулфат PbSO4, освобождавайки олово. Реакциите на топене на огнището започват да протичат при температури 700 - 800 С. В допълнение към черното олово при топенето се получават сиви шлаки, съдържащи до 30% олово. Тези богати шлаки обикновено се претопяват в шахтови пещи за допълнително извличане на олово. [17]
Оловен блясък и церусит са основните руди, съдържащи олово. Понастоящем производството на олово от руди се извършва главно чрез редукционно топене в специални шахтови пещи, наречени водни ризи. Процесът на топене се състои от следните последователни операции: печене и синтероване на рудата, топене във водна риза и рафиниране. [18]
Калайът се получава чрез редукция на каситерит с въглища. За получаване на олово галенитът се превръща в PbO, който също се редуцира с въглища. Тенекиеното фолио (станиол) се използва за опаковане на хранителни продукти, в електротехническата индустрия. Оловото се използва за направата на акумулаторни плочи, облицовки на електрически кабели, устойчиви на корозия материали в химическата промишленост и защита срещу радиоактивно излъчване. И двата метала се използват за производство на сплави. [19]
При нагряване на въздух оловният сулфид се окислява до оловен сулфат и оловен оксид. Товаизползвани при печене за получаване на олово. Когато се калцинира в поток от водород, оловният сулфид постепенно се редуцира до метал. Въглеродният окис, напротив, действа върху него, само слабо. Топене със сода, с достъп до въздух, свободен метал се освобождава от сулфид; в този случай сулфидът първо се окислява до сулфат, който след това взаимодейства с други части на сулфида, за да образува SO2 и Pb. [20]
При нагряване на въздух оловният сулфид се окислява до оловен сулфат и оловен оксид. Това се използва при печене за производство на олово. Когато се калцинира в поток от водород, оловният сулфид постепенно се редуцира до метал. Въглеродният оксид, напротив, действа слабо върху него. Топене със сода, с достъп до въздух, свободен метал се освобождава от сулфид; в този случай сулфидът първо се окислява до сулфат, който след това взаимодейства с други части на сулфида, за да образува SO2 и Pb. [21]
В случай на медни руди, среброто се възстановява от анодната утайка по време на електролитното рафиниране на черна мед. От руди, бедни на сребро, които не се използват за производство на олово или мед, среброто сега почти навсякъде се извлича чрез излужване с цианид. При този метод сребърните съединения се обработват с цианиди на алкални метали, в резултат на което се образуват комплексни цианиди и среброто преминава в разтвор. Среброто се изолира от този разтвор чрез добавяне на цинк. Среброто, получено по описаните по-горе методи, винаги съдържа малко злато, както и мед. [22]
Основните трудности при развитието на тази технология в индустриални условия, както и при производството на индий, са свързани с пречистването на електролитите и насищането на електролити и амалгами на биполярни електроди с олово. Промишлена експлоатация на зареден електролизер безпрезареждането, придружено от производството на олово с висока чистота, може да се извърши в рамките на 5 - 8 години. [23]
Основните трудности при развитието на тази технология в индустриални условия, както и при производството на индий, са свързани с пречистването на електролитите и насищането на електролити и амалгами на биполярни електроди с олово. Промишлената експлоатация на натоварена клетка без презареждане, придружена от производството на олово с висока чистота, може да се извърши за 5–8 години. Корекцията на състава на електролитите (намаляване на концентрацията на оловни йони) в секциите на електролизерите поради високия буферен капацитет на електролитите се извършва не повече от веднъж годишно. [24]
Понякога процесът на дестилация произвежда газообразни замърсители, които са в твърдо състояние при нормални температури. Така например арсеновите оксиди попадат във въздуха при изгаряне на въглища или при получаване на олово и цветни метали. При дестилацията също се освобождават олово, антимонов оксид, живак и други химикали. Освен това по време на дестилацията се отделят редица летливи метални хлориди. [25]
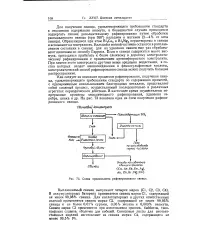
Както следва от описанието на процесите на рафиниране, получаването на олово, което отговаря на изискванията на стандарта за съдържание на примеси, с едновременното използване на благородни метали, е сложен процес, извършван последователно в различни партидни единици. В момента се извършват непрекъснати процеси на окислително рафиниране, отстраняване на сребро, цинк и др. 73 е показана една от схемите за получаване на рафинирано олово. [27]
Калайът се получава чрез редукция на каситерит с въглища. От голямо значение е регенерирането (обратното производство) на калай поради разтварянето на неговите покрития върху желязото (старокутии), в основи и последващо изолиране от разтвора чрез електролиза. За получаване на олово галенитът се превръща в PbO, който също се редуцира с въглища. [28]
Калайът се получава чрез редукция на каситерит с въглища. От голямо значение е регенерирането (обратно производство) на калай поради разтварянето на неговите покрития върху желязо (стари кутии) в основи и последващо отделяне от разтвора чрез електролитни средства. За получаване на олово галенитът се превръща в PbO, който също се редуцира с въглища. [29]
Около 20% от оловото, произведено в света, в момента се рафинира чрез електролиза. Съотношението на електролитното олово се увеличава непрекъснато. Това се стимулира от възможността за получаване на олово с висока чистота на един или два етапа. Ниската интензивност на процеса, сложната схема на обработка на анодната утайка и трудността при избора на електролит за неговото прилагане възпрепятстват широкото използване на този метод. [тридесет]