Грешка в неточността на оборудването
20. Грешка поради неточност на оборудването. Тотална грешка при обработката
Геометричните неточности на машината причиняват отклонения в размера, формата и местоположението на обработваните повърхности. Тези грешки се прехвърлят изцяло или частично върху обработваните детайли под формата на постоянни системни грешки на геометрични неточности на машината Δst. Например, в случай на непаралелизъм "а" на оста на въртене на детайла на траекторията на надлъжното движение на дебеломера с нож (фиг. 2.5, а) в хоризонталната равнина, възниква грешка в диаметъра на обработвания цилиндър
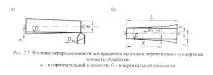
Обработената повърхност получава грешка във формата в надлъжното сечение под формата на конус.
Когато оста на въртене не е успоредна на водачите във вертикалната равнина, обработената повърхност приема формата на хиперболоид на въртене, чийто прираст на радиуса Δr е
Δr=
Предният център "бие", т.е. той е разположен ексцентрично спрямо оста на въртене на шпиндела, оста на задния център съвпада с оста на въртене; оста на стругованата повърхност не съвпада с линията на центровете на детайла.
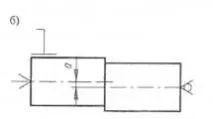
Ориз. 2.6. Влияние на биенето на предния център върху точността на обработка
Ако детайлът се завърта в две настройки (с неговото обръщане и пренареждане на задвижващата яка), тогава частта е двуосна. Тъй като ъгловото положение на скобата не е ограничено по никакъв начин, в общия случай тези оси се пресичат, а в частен случай могат да се пресичат под ъгъл a = 180 - 2β, където ъгълът β се определя от равенството sinβ=a/L.
Тук a е изместването на центъра на главата; L е разстоянието между центровете.
Износването на работните повърхности на металообработващите машини увеличава първоначалнотостойността на Δst поради промяна на взаимното разположение на отделните възли на машините. Една важна причина е износването на направляващите повърхности.
По този начин общата грешка Δst може да се счита за систематично променяща се стойност. Влиянието му може да бъде намалено чрез увеличаване на точността на оборудването, промяна на дизайна на водачите.
Общата грешка на обработката е следствие от действието на първичните елементарни грешки, разгледани по-рано. Определянето на общите грешки на отделните операции на технологичния процес на обработка е необходимо за правилното определяне на технологичните допуски при проектирането на технологичните процеси и анализ на точността на крайните операции.
Общата грешка ΔΣ или полето на разсейване на изпълнения размер може да се изрази в общ вид чрез функционалната зависимост
Ако Δεу, ΔН, ΔST, ΔУ, ΔТ, ΔИ→min и са независими, то грешките могат да бъдат Σ по метода максимум-минимум.
- не отчита реални комбинации и връзки на елементарни грешки,
- дава надценени стойности на грешка.
При метода на вероятностното сумиране първичните грешки се разглеждат като случайни променливи с определени закони на разпределение на вероятностите.
където ki е коефициентът на относително разсейване на първичните грешки.
Общата грешка на машинната обработка ще бъде равна на
Често, когато се изчислява общата грешка, вместо коефициентите ki се използват стойностите на λi - относителните стандартни отклонения на i-тата грешка.
В този случай общата грешка
Δεу, ΔН, ΔУ - разпределението на тези величини е близко до нормалното
ΔST, ΔT, ΔI - разпределението се подчинява на закона за равна вероятност.
21. Регионприложение на CNC машини. Системи за управление на машини. Координатни системи на CNC машини. Изисквания към детайлите, обработвани на машини с ЦПУ. Характеристики на дизайна
Обхват на металорежещи машини, технологични възможности. Машините с ЦПУ са автоматични или полуавтоматични машини, чиито движещи се части извършват работни и спомагателни движения автоматично по предварително инсталирана управляваща програма (КП), записана на програмен носител в цифров вид. Основната област на приложение на машините с ЦПУ е средномащабното производство. Използването на машини с ЦПУ дава най-голям ефект при обработка на детайли със сложна конфигурация с партида за стартиране от повече от 15-20 броя.
Основните предимства на използването на CNC машини:
1. Повишаване на производителността на труда чрез увеличаване на концентрацията на операциите, намаляване на времето, изразходвано за повторно инсталиране, транспортиране на детайлите;
2. осигуряване на висока точност на обработката, тъй като процесът на обработка е автоматизиран и не зависи от квалификацията на оператора на машината;
3. гъвкавост на производството поради бърза смяна на оборудването;
4. намаляване на необходимото количество оборудване;
5. понижаване на квалификацията на операторите на машини;
6. възможност за многомашинна работа.
Негативните явления, които възникват при използване на CNC машини, включват следното:
1. висока цена на оборудването;
2. разходи за изготвяне на контролни програми;
3. увеличение на разходите за експлоатация и ремонт на оборудването;
4. висока цена на режещите инструменти.
Съвременните машини с ЦПУ, в зависимост от вида на обработката, могат да имат различни системи за управление, които реализират движенията на работните органи.
Позиционен с цифрово индексиране (F1)осигуряват движение на работните органи до зададените точки, без да задават траекторията на движение. Движението се извършва в две или три взаимно перпендикулярни посоки последователно. На светлинното табло на такава система непрекъснато се показват числените стойности на координатите на движещите се части на машината. Често системата е оборудвана с дистанционен контролен панел с набор от координати.
Позиционните системи без индикация (Ф2) или контурните правоъгълни системи представляват същото като горните, но нямат цифрови устройства за индексиране и въвеждане на данни.
Контурните системи (FC) с линейни или кръгови интерполатори осигуряват движението на работните органи на машината едновременно по две или три координати по дадена траектория.
Комбинираните системи (F4) съчетават в себе си качествата на позиционните и контурните системи.
Освен това в обозначенията на моделите машини се въвеждат индекси, които отразяват конструктивните характеристики на машината, свързани със смяна на инструменти: Р - смяна на инструмента чрез завъртане на револвера; M - автоматична смяна на инструмента от магазина.
Според броя на контролираните движения (координати) CNC системите биват дву-, три-, четири-, пет- и многокоординатни. Броят на контролираните координати е важна технологична характеристика на машината. Така че за струговане и шлайфане са достатъчни две; за пробиване и пробиване - три, фрезоване - пет контролирани координати.
За програмиране на преместванията се използват два метода за отчитане на преместванията: абсолютни и относителни (на стъпки).
При метода на абсолютна референтна позиция позицията на началото остава постоянна за цялата траектория на инструмента. Абсолютните стойности на координатите на референтните точки на траекторията се записват на програмния носител. За по-лесно програмиране инастройки, позицията на началото на координатите може да бъде избрана навсякъде в работните ходове на движещите се части („плаваща нула“). При този метод на справка е препоръчително да използвате координатния метод за оразмеряване на детайлите, тогава работните размери ще съвпадат с тези, посочени в чертежа.
При относителния метод за отчитане на координатите позицията на работния орган, която е заемала преди началото на следващото движение към нова референтна точка, се приема всеки път за нула. Координатните стъпки се въвеждат в програмата при преминаване от предишната към следващата референтна точка. Най-добрият вариант за размери и детайли в случая е верижката. В този случай се натрупват грешки при движение.
Точността на обработка до голяма степен се определя от точността, с която се осигурява извеждането на работните органи към зададените координати - точност на позициониране.
Режимите на обработка могат да се променят по време на извършване на преходи или в рамките на отделни преходи, което ви позволява да оптимизирате обработката на сложни повърхности.
Разработване на технологични операции
При проектиране на технологична операция на CNC машина се обръща специално внимание на технологичните преходи. За тях се разработват траектории на относителни работни и спомагателни движения на инструмента и детайла, след което започват програмиране.
Основната координатна система, в която се извършва движението на работните органи на машината, е машинната координатна система (СКС). Местоположението и обозначението на координатните оси, съответстващи на посоките на независими контролирани движения, е прието в съответствие със стандарта ISO - R841. Базира се на ортогонална дясна координатна система с осите X, Y, Z.при което инструментът и детайлът се отдалечават един от друг. В този случай оста Z е подравнена с оста на въртене на инструмента или детайла, а оста X е винаги хоризонтална (фиг. 5.2).
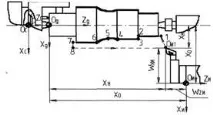
Ориз. 5.2. Връзка на CNC стругови координатни системи
Позицията на нулевата точка на машината ("нула на машината") не е определена от стандартите. Обикновено нулевата точка е подравнена с базовата точка на възела, който носи детайла, фиксиран в такава позиция, че всички движения на машинните инструменти в SCS се описват с положителни координати. Базовите точки са: за шпиндела - точката на пресичане на челната повърхност на шпиндела с оста на въртене; за напречна маса - точката на пресичане на нейните диагонали; за въртяща се маса - точката на пресичане на равнината с оста на въртене на масата и др.
Координатната система на детайла (SKD) се използва за задаване на координатите на референтните точки на траекторията на относителното движение на инструмента. Референтни точки са точките на начало, край, пресичане или докосване на геометрични елементи, от които се образуват линиите на контура на детайла и траекториите на движение на инструментите. SKD избира технолог според следните препоръки:
- началото на ACS - "част нула" трябва да бъде разположено така, че повечето от опорните точки да имат положителни координати;
— координатните равнини трябва да са подравнени или успоредни на технологичните основи на детайла;
— посоката на осите трябва да бъде същата като в SCS;
— координатните оси на SKD трябва да бъдат подравнени с осите на симетрия на детайла или с колкото е възможно повече размерни линии.
Координатната система на инструмента (SCS) е предназначена да зададе позицията на режещия ръб на инструмента спрямо устройството, в което е инсталиран. Осите на SQI са успоредни и насочени в същата посока като осите на SCS. Избира се началото на SKI ("нулев инструмент").като се вземат предвид особеностите на инсталиране и настройка на инструмента на машината: в основната точка на инструменталния блок, шублер, шпиндел.
Върхът на инструмента, точка на оста на инструмента, която е зададена точка, се използва като референтна точка при изчисляване на траекторията на инструмента.
Позицията на началната точка на траекторията се избира, като се вземе предвид удобството за настройка на детайла и смяна на инструмента.
Нулевата позиция на детайла може да бъде преместена във всяка точка („плаваща нула“), включително извън контура на детайла, ако това ще улесни процеса на програмиране или ще увеличи точността на получаване на размерите.
Координатите на върха на инструмента Wz и Wx по време на настройка може да не се поддържат, ако е възможно „нулиране“, т.е. фиксиране на върха на инструмента в SCS с помощта на специални сензори за фиксиране.
При определяне на състава на струговата операция по броя и последователността на преходите контурът на детайла се разделя на зони. Могат да се разграничат два вида зони: селекции от материални масиви и контурни. За да се премахнат припокриванията от областите на масивите, трябва да се използват типични схеми на траектории на обработка и постоянни типични цикли, налични в софтуера на машините с ЦПУ.
На машини с ЦПУ е изгодно да се обработват части със сложна конфигурация, което изисква голям брой технологични преходи и преходи с контуриране. Основните изисквания за технологичност на дизайна на детайла включват:
- стандартизация и унификация на структурните елементи;
- опростяване на геометрични форми;
- максимална инструментална наличност;