Методи за проверка на микрометрични инструменти
Обработка на дърво и метал
Проверката на точността на показанията на микрометрите се извършва чрез крайни мерки за дължина от 5-та категория на всеки 5 mm от скалата и на всеки 0,12 mm, т.е. на всяка четвърт от оборота на микровинта.
Плоскостта на техните измервателни повърхности се контролира с помощта на плоски или плоскопаралелни интерферентни стъклени плочи. Отклонението от плоскост (в зависимост от класа на точност на микрометрите) варира от 0,6 до 0,9 µm или равно на три интерферентни ивици за бяла светлина, без да се отчита разстоянието от 0,5 mm от ръбовете на измервателната повърхност.
Успоредността на измервателните повърхности на микрометрите с горна граница на измерване до 100 mm се проверява с плоскопаралелни стъклени пластини. Комплектът се състои от четири плочи, чиито размери H се различават един от друг по количеството на движение на микровинта, когато се завърти с 'D на оборот. Действителното отклонение от паралелността се определя от броя на интерферентните ивици на контактните повърхности и от тяхното взаимно разположение.
За проверка на микрометри с големи размери вместо отделни плоскопаралелни стъклени пластини се използва комплект от тях, съставен под формата на блокове, всеки от които има две пластини и една крайна мярка.
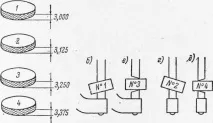
Микрометрите с граници на измерване над 100 mm се контролират с помощта на четири специални щифта, чиито размери също се различават един от друг с количество, съответстващо на XU на оборота на микровинта. Всеки щифт се проверява в четири позиции, като всеки път се завърта около оста на 90 °.
Настройка и ремонт на микрометри. Ако нулевите ходове на скалата на стеблото и скалата на барабана не съвпадат, както и при разхлабен винт, микрометрите трябва да се регулират.
Приизносване на измервателните повърхности на микрометъра и микрометричния винт и при разхлабване на тресчотката инструментът се ремонтира. С малко износване, измервателните повърхности на микрометри и измервателни уреди (от 0 до 100 mm) се регулират едновременно с помощта на измервателни цилиндрични обиколки. Комплектът им се състои от четири обиколки, различаващи се по дебелина с 0,125 мм. Крайните работни равнини на обиколките трябва да са строго успоредни.
Завършването се извършва в следната последователност. Първо, измервателните повърхности се регулират чрез припокриване, докато станат взаимно успоредни. Това обаче не гарантира, че повърхностите са перпендикулярни на оста на шпиндела, най-вероятно те ще бъдат малко наклонени. Освен това, фината настройка се извършва с обиколка, която е с 0,25 mm по-голяма от обиколката, следователно, когато обиколката е затегната, шпинделът ще се завърти на половин оборот, т.е. ще се появи накланяне и изкривяването ще намалее. След това повърхностите на микрометъра се припокриват последователно. След многократно завършване с всички обиколки могат да се постигнат успоредни повърхности и перпендикулярност спрямо оста на шпиндела.
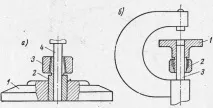
При постъпване за ремонт на микрометри с такова износване на измервателните повърхности, което се установява с помощта на квадрат или крива линийка, шпинделът и петата се доработват отделно. Челната повърхност на шпиндела се регулира в специално устройство. Състои се от плоча, цанга, в която е вкаран шпинделът на микрометъра, и затягащ пръстен, предназначен да закрепи шпиндела в цангата. Долната равнина на плочата се регулира строго перпендикулярно на оста на отвора. Шпинделът на микрометъра се вкарва в цангата, така че краят му да се издига над равнината на плочата с 0,03 ... 0,04 mm и след фиксиране със затягащ пръстен се регулира. Обработеният шпиндел се завинтва в микрометър и се пристъпва към фина настройкаповърхност на петата.
Петата се регулира в сглобен вид с помощта на устройство, което представлява диск, изработен в едно цяло с цангата. Дискът е монтиран плъзгащо се на шпиндела на микрометъра и е закрепен с пръстен. Носещата повърхност на диска е поставена строго перпендикулярно на оста на отвора. След инсталиране и фиксиране на диска върху шпиндела на микрометъра, те започват да усъвършенстват петата; в този случай пастата се нанася само върху едната работна страна на обиколката, а другата се измива добре и се смазва с тънък слой разтвор на стеарин в бензин.
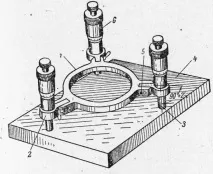
Контролът на обработваните измервателни повърхности се осъществява по интерферентен начин с помощта на комплект плоскопаралелни стъклени пластини. Инструментът се обезмаслява в бензин, старателно се избърсва и върху готовата повърхност се нанася стъклена плоча. При леко притискане на плочата към повърхността се наблюдават светли ивици, по които се оценява качеството на довършителни работи.
За завършване на повърхностите на микрометрични винтове на микрометри с граница на измерване от 150 ... 800 mm, монтажникът S.P. Григориев разработи устройство, показано на фиг. 3. В основата на устройството има три издатини с жлебове, в които са фиксирани стеблата със стебла. Основните равнини на жлебовете са строго перпендикулярни.
Устройството е направено по следния начин. За използвани микрометри с граница на измерване от 0 ... 25 mm, отрежете скобите и оставете стеблата със стъбла. След това стъблата се смилат на мястото на жлеба. След като инсталирате и трите стебла и проверите повърхностите им върху стъклена плоча 4, в ушите на основата се пробиват два отвора и щифтовете се притискат в тях.
При обработка на микровинтове, барабаните се настройват по нониуса до нулева позиция и повърхностите се завършват предварително, след което се завъртат 3-4 пътина ‘D завъртане (с 0,12 mm) и накрая се регулира. След това микровинтовете се отстраняват от устройството, монтират се в ремонтираните микрометри и се извършва контрол.
Ако нулевото деление на микрометърния барабан не съвпада с нулевото деление на скалата, е необходимо да развиете микрометърната глава с 1-2 оборота и, като издърпате барабана към скобата, го извадете от корпуса на шпиндела. След като инсталирате барабана в правилната (нулева) позиция, като завъртите главата на микрометъра, фиксирайте го върху шпиндела с фиксиращ винт.
Плавното движение на микрометърния винт се характеризира с липсата на люфт и задръстване в някои области. Луфтът обикновено се усеща с ръка, а залепването може да се определи чрез завъртане на винта зад главата на тресчотката в целия диапазон на микрометърната скала. Ако в същото време триенето на винта в гайката в някои области е толкова голямо, че тресчотката започва да се върти на празен ход около оста, тогава тя има неравномерно износване и трябва да бъде сменена или коригирана.
Луфтът се елиминира чрез завъртане на конусната гайка, завинтена върху гайката на винта. В случай на неравномерно износване на винта, той се коригира чрез фина настройка със специална разделна резба.