Направи си сам PCB печатащо устройство
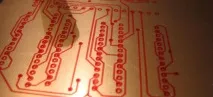
Още веднъж измивайки мивката от червените петна от железен хлорид, след ецване на дъската, реших, че е време да автоматизирам този процес. Така започнах да правя устройство за изработване на платки, което вече може да се използва за създаване на най-проста електроника.
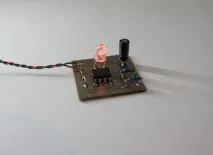
По-долу ще говоря за това как направих това устройство.
Основният процес на производство на печатна платка с помощта на метода на изваждане е, че ненужните участъци от фолиото се отстраняват от материала на фолиото.
Днес повечето инженери по електроника използват технологии като лазерно гладене за домашно производство на печатни платки. Този метод включва премахване на ненужните участъци от фолиото с помощта на химически разтвор, който корозира фолиото на ненужни места. Първите експерименти с LUT преди няколко години ми показаха, че тази технология е пълна с дреболии, понякога напълно възпрепятстващи постигането на приемлив резултат. Тук е и подготовката на повърхността на дъската, и изборът на хартия или друг материал за печат, и температурата във връзка с времето за нагряване, както и характеристиките на измиване на остатъците от лъскавия слой. Трябва да работите и с химия, а това не винаги е удобно и полезно у дома.
Исках да сложа някакво устройство на масата, на което като принтер можете да изпратите източника на платката, да натиснете бутон и след известно време да получите готовата платка.
С малко гугъл можете да разберете, че хората, започвайки от 70-те години на миналия век, започват да разработват настолни устройства за производство на печатни платки. На първо място се появиха фрезови машини за печатни платки, които изрязваха песни върху фолио текстолит със специален нож. Същността на технологията се състои в това, че при високи скорости фрезата, монтирана на твърда и прецизна координатна маса сCNC реже слоя фолио на правилните места.
Желанието за незабавно закупуване на специализирана машина премина след проучване на цените от доставчика. Аз, като повечето любители, не съм готов да дам такива пари за устройство. Затова беше решено да направите машината сами.
Ясно е, че устройството трябва да се състои от координатна маса, която премества режещия инструмент до желаната точка и самото режещо устройство.
В интернет има достатъчно примери как да направите координатна маса за всеки вкус. Например, същият RepRap се справя с тази задача (коригиран за точност).
От един от предишните ми проекти за хоби плотер имам домашно направена XY маса. Следователно основната задача беше да се създаде режещ инструмент.
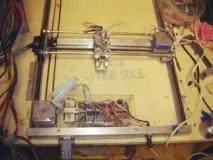
Оборудването на плотера с миниатюрен гравьор като Dremel би било логична стъпка. Но проблемът е, че плотер, който може да се сглоби евтино у дома, е трудно да се направи с необходимата твърдост, успоредност на равнината му спрямо равнината на текстолита (дори самият текстолит може да бъде извит). В резултат на това не би било възможно да се режат дъски с повече или по-малко добро качество върху него. В допълнение, фактът, че фрезата се изтъпява с времето и губи режещите си свойства, говори против използването на фрезоване. Би било чудесно, ако медта може да се отстрани от повърхността на текстолита по безконтактен начин.
Вече има лазерни машини на немския производител LPKF, при които фолиото просто се изпарява от мощен инфрачервен полупроводников лазер. Машинните инструменти се отличават с точност и скорост на обработка, но цената им е дори по-висока от тази на фрезовите машини и все още не е възможно да се сглоби такова нещо от достъпни за всички материали и по някакъв начин да се намали цената му.изглежда проста задача.
От горното формирах някои изисквания към желаното устройство:
- Цена, сравнима с цената на среден домашен 3D принтер
- Безконтактно отстраняване на мед
- Възможност за сглобяване на устройството от наличните компоненти сами у дома
Така започнах да мисля за възможна алтернатива на лазера в областта на безконтактното отстраняване на мед от текстолит. И попаднах на метод на електроискрова обработка, който отдавна се използва в металообработването за производството на прецизни метални части.
При този метод металът се отстранява чрез електрически разряди, които се изпаряват и го пръскат от повърхността на детайла. Така се образуват кратери, чийто размер зависи от енергията на разряда, неговата продължителност и, разбира се, от вида на материала на детайла. В най-простата си форма електрическата ерозия започва да се използва през 40-те години на миналия век за пробиване на дупки в метални части. За разлика от традиционната машинна обработка, отворите могат да бъдат направени в почти всякаква форма. В момента този метод се използва активно в металообработването и е довел до появата на цяла серия от видове металорежещи машини.
Задължителна част от такива машини е генератор на токови импулси, система за подаване и движение на електрода - именно електродът (обикновено меден, месингов или графитен) е работният инструмент на такава машина. Най-простият генератор на токови импулси е обикновен кондензатор с желания рейтинг, свързан към източник на постоянно напрежение чрез резистор за ограничаване на тока. В този случай капацитетът и напрежението определят енергията на разряда, което от своя страна определя размера на кратерите, а оттам и чистотата на обработка. Вярно е, че има един важен нюанс - включеното напрежениекондензатор в работен режим се определя от пробивното напрежение. Последният е почти линейно зависим от разстоянието между електрода и детайла.
По време на вечерта беше изработен прототип на ерозионен инструмент, който представлява соленоид, към чиято арматура е прикрепена медна жица. Соленоидът осигурява вибрация на проводника и прекъсване на контакта. LATR се използва като източник на енергия: коригираният ток зарежда кондензатора, а променливият ток захранва соленоида. Този дизайн също беше фиксиран в държача на писалката на плотера. Като цяло резултатът отговаря на очакванията и главата оставя непрекъснати ивици с разкъсани ръбове върху фолиото.
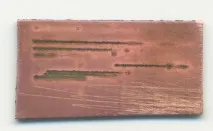
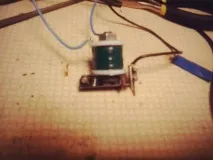
Методът очевидно имаше право на живот, но беше необходимо да се реши един проблем - да се компенсира консумацията на тел, която се консумира по време на работа. Това изискваше създаването на механизъм за подаване и контролен блок за него.
След това започнах да прекарвам цялото си свободно време в едно от хакспейсовете на нашия град, където има металообработващи машини. Започнаха дълги усилия да се направи приемливо режещо устройство. Ерозионната глава се състоеше от двойка прътови втулки, осигуряващи вертикална вибрация, възвратна пружина и издърпващ механизъм. За да се управлява соленоидът, беше необходимо да се направи проста верига, състояща се от генератор на импулси с дадена дължина на NE555, MOSFET транзистор и сензор за индуктивен ток. Първоначално се предполагаше да се използва режимът на самотрептене, тоест да се приложи импулс към ключа веднага след текущия импулс. В този случай честотата на трептенията зависи от размера на междината и задвижването се управлява според измерването на периода на собствените трептения. Въпреки това се оказа възможен стабилен автоколебателен режим в диапазона на амплитудите на трептене на главата, който беше по-малък от половината от максимума. И азреши да използва фиксирана честота на трептения, генерирани от хардуерна ШИМ. В този случай състоянието на празнината между проводника и платката може да се прецени по времето между края на отварящия импулс и първия токов импулс. За по-голяма стабилност по време на работа и подобряване на честотните характеристики, соленоидът беше фиксиран над механизма за издърпване на проводника, а арматурата беше поставена върху скоба от дуралуминий. След тези подобрения беше възможно да се постигне стабилна работа при честоти до 35 Hz.
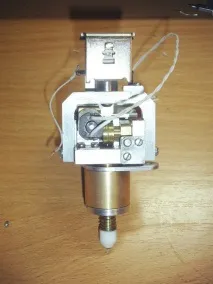
Фундаменталната възможност за изработване на печатни платки чрез електроискрова обработка е потвърдена. В близко бъдеще планираме да подобрим точността, да увеличим скоростта на обработка и чистотата на рязане, както и да направим някои от разработките публично достояние.