Направи си сам въглеродни влакна
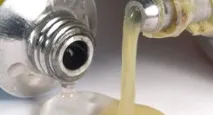
Основните материали за производството на карбон са епоксидни съединения и въглеродна тъкан.
Технологията на производство на карбонови продукти се основава на технологичните особености на полиестерните и епоксидните смоли, които също погрешно се наричат компаундни. Но какво е съединение? По-правилно е смесите да се наричат смес от смола с втвърдител и пълнител, тъй като "компаундирането" е смесване.
Какви са съединенията
Такива смеси - съединения са студено втвърдяване и горещо, което се определя от вида на втвърдителя. Същността на процеса на втвърдяване е превръщането на молекула на смола с реактивни епоксидни групи (= C - C =) в макромолекула чрез реакция с амини, анхидриди на органични киселини, фенолформалдехидни смоли, съдържащи се в втвърдителите. С въвеждането на втвърдители епоксидните смоли преминават от течно-вискозно състояние на олигомери в твърдо, нетопимо и неразтворимо състояние на полиепоксидни полимери. Тоест, молекулите на епоксидната смола се омрежват и придобиват мрежеста структура.
Термоустойчивостта на втвърдените съединения е 150…250 °C.
Студено втвърдяващите се епоксидни съединения са най-широко използвани, тъй като са най-лесни за използване. Но те имат редица недостатъци, които допълнително водят до напукване, разслояване, пожълтяване на автомобилните части, направени от тях.
Това се дължи на тяхната ниска устойчивост на ултравиолетова радиация, високи температури. Това може да се избегне чрез покриване на повърхността с лак, боя и добавяне на пълнител. Продуктът ще бъде по-тежък, но и по-издръжлив. За производството на въглерод се използват методи с използване на всички видове съединения, което се определя от размерите на частта,умения и оборудване.
Предимства на епоксидни смоли и съединения
Епоксидните смоли за въглеродни влакна и съединенията на тяхна основа са популярно и оптимално свързващо вещество за материали за армиране на влакна. И за това те имат широк спектър от потребителски и технологични предимства:
- Отлична адхезия към повечето армиращи материали, пълнители и субстрати;
- Голям избор от марки епоксидни смоли и втвърдители с разнообразни технически параметри, което прави възможно получаването на материали с широк спектър от свойства след втвърдяване;
- Химическата реакция между епоксидни смоли и втвърдители протича без отделяне на вода и летливи вещества - процесът е контролиран и безопасен (необходимо е да се вземе предвид количеството топлина в някои формулировки).
- Свиването при втвърдяване е по-ниско, отколкото при фенолформалдехидни или полиестерни смоли и може лесно да се регулира с помощта на различни пълнители;
- Съвременните модификации на епоксидни смоли позволяват да се избере марка с определена температура, скорост и време на втвърдяване, което е много важно при масовото производство;
- Втвърдените съединения са отлични диелектрици с високо обемно съпротивление.
- Устойчиви са на вода, високи температури, киселини и основи.
Но първоначално епоксидните смоли се използват само като универсални лепила, запълващи намотките на трансформатори и двигатели, уплътняващи съединения на електрически кабели и при производството на модели и форми.
С появата на въглеродната мрежа и с развитието на композитните материали, епоксидните смоли намериха широко приложение в производството на пластмаси, подсилени с въглеродни влакна. Следователно, заедно с използването на епоксидни съединения като лепила, тесе използват в производството на ламинирани пластмаси и композитни материали за намотаване на влакна в електронната, химическата, автомобилната промишленост и в производството на спортно оборудване.
Студени съединения
„Студените“ технологии изискват продължителна подготовка на инструментална екипировка и допълнително оборудване за вакуумни процеси за отстраняване на въздуха от сместа. Този метод е трудоемък и подходящ за дребномащабно производство на части от определена секция. Всички компоненти трябва да бъдат добре смесени и строго дозирани.
Втвърдяването става при стайна температура или при нагряване до 70-80 C. Всичко по-горе се отнася за горещо втвърдяващи се съединения.
Смеси за горещо втвърдяване
Горещо втвърдяващите се епоксиди са по-здрави, но се втвърдяват много бавно при стайна температура. Това свойство се използва при производството на препреги - заготовки за формоване. Те представляват карбонови листове, при които смола с втвърдител в течна форма се нанася върху въглеродните влакна, а реакцията на втвърдяване практически не протича при стайна температура и започва при нагряване.
Такива заготовки могат да се съхраняват от няколко часа до няколко седмици, в зависимост от марката на смолата и предназначението.
Директно по време на производството на детайла нагрятото съединение става течно и се разпространява, запълвайки целия обем на работната форма и процесът на полимеризация се ускорява.
Всяка марка горещо нанесена смола има свои собствени температурни и времеви режими на втвърдяване. Ето защо, когато избирате, трябва да обърнете внимание на тези параметри и възможностите на вашето оборудване.
Препоръчителна подготовка на смола и съединение
При избора на смола е препоръчително да се съсредоточите върху размерите, условиятаексплоатация на готовия продукт и техния опит.
1. "Бавните" смоли се използват за продукти с големи размери и ако се работи при високи температури, както и с малък опит, за да имате време да изправите всички гънки на тъканта и внимателно да поставите въглеродната тъкан, импрегнирана със смола, преди да започне полимеризацията. Трябва да се помни, че повишаването на температурата ускорява полимеризацията на всяко съединение. Колкото по-висока е стайната температура, толкова по-бавна трябва да бъде смолата. В студено помещение могат да се използват "бързи" смоли.
2. Ако готовият продукт ще се използва на открито, е необходимо да изберете смоли с UV филтри и устойчивост на висока температура. Тоест, не забравяйте да обърнете внимание на спецификациите на производителността. Възможно е използването на лакове със защитни свойства с универсална смола.
3. Качеството на втвърдения състав се определя не само от неговите технически и потребителски характеристики, но и от точността на дозиране и пълното смесване на всички компоненти.
Потребителските характеристики на готовия продукт могат да бъдат променени чрез избор на втвърдители от различни марки.
Опитите за ускоряване или забавяне на времето на полимеризация чрез независима промяна на пропорциите са изпълнени с влошаване на характеристиките на готовото съединение. Повишената доза втвърдител ще ускори втвърдяването, но ще начупи готовия продукт и здравината ще бъде по-ниска. Ако количеството на втвърдителя е по-малко от стандартното, сместа може изобщо да не се втвърди.
Необходимо е да смесите всички компоненти на сместа поне за минута.
4. Тъй като смолата е термореактивна, по време на полимеризацията се отделя екзотермична топлина. Протича химическа реакция. И колкото по-бързо протича реакцията, толкова повече топлина се отделя. Ето защо при работа е необходимо да се спазват следните предпазни мерки:не пипайте с ръце, не вдишвайте горещи смолисти изпарения, не използвайте запалими материали.
Времето, през което сместа остава в течно състояние, се нарича годност. Времевият интервал от течно състояние до твърдо състояние е времето за желиране. Времевият интервал от пълното смесване до пълното втвърдяване е времето на полимеризация.
На етапа на първоначално втвърдяване (материалът е еластичен и при натискане с нокът остава следа) може да се нанесе следващият слой плат и смола, тъй като в този момент новият слой се комбинира с предишния в едно цяло, все още протича химическа реакция. Ако пропуснете този момент, в бъдеще нанасянето на слоеве е възможно само при внимателно шлайфане и полиране на повърхността. Връзката ще премине вече поради капилярния ефект. В противен случай може да възникне разслояване.
Отстраняването на готовия продукт е възможно само след пълно втвърдяване. Но последният набор от сила ще продължи още месец.
Следователно времето за желиране трябва да се знае, за да се изчислят времената за смесване и наслояване. А времето за полимеризация определя времето на задържане и момента на изваждане на продукта от матрицата. Производителите предлагат втвърдители от различни марки, които могат да се използват за регулиране на времето за полимеризация.
За да не направите грешка при избора на всички компоненти на сместа сами, по-добре е да закупите смолата и втвърдителя в комплекти, като обърнете внимание на времето за полимеризация на готовата смес.
Пълнители за смеси
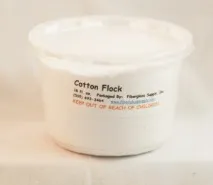
За увеличаване на плътността и сгъстяването на смолата се използват различни пълнители, след старателно смесване на смолата и втвърдителя.
Това могат да бъдат памучни влакна, нарязани фибростъкло и стъклени сфери, нарязани и смлени въглеродни влакна, метален прах, талк. Точендозировката обикновено не се изисква и има поле за вашите експерименти. Гъстите смеси се използват за запълване на празнини и моделиране на форми.
Специални добавки
За придаване на специални свойства, като устойчивост на ултравиолетови лъчи, високи и ниски температури, боядисване, се използват специални добавки.
Излишната смола може лесно да се отстрани с ацетон. Това ще ви бъде от полза. Ако си изцапате ръцете. Но е по-добре да работите с ръкавици.
Тайван е основният производител на въглеродни влакна днес. Фибростъклото (стъклената подложка) е по-евтино и се използва за производството на фибростъкло или слоеве от въглеродни влакна са притиснати с него. Ако се опитат да ви убедят, че въглеродните влакна могат да бъдат направени от фибростъкло, не им вярвайте. Това просто ще бъде различен материал за цената на въглерода.
Така че, когато избирате съединение за въглерод, следните са важни параметри:
- Съотношение смола: втвърдител,
- Вискозитетът на сместа според Brookfield при 22 ° C,
- Живот на годност при 22 °C,
- време на желиране,
- Пълно време за втвърдяване
- Издръжливост на опън,
- Статична якост на огъване,
- Топлоустойчивост.
- Оптималното време за втвърдяване е 24 часа при 22-24°C.
Ако има малък опит, може да се направи пробен тест на сместа, за да се определи началното време на желиране за действителната температура и влажност в помещението.