Обработка на външни и вътрешни конични повърхности - Струговане
Обработка на дърво и метал
Ако завъртим правоъгълен триъгълник ABV около катет AB, то полученото тяло се нарича пълен конус, катет AB се нарича височина на конуса. Правата AB се нарича образуваща на конуса, а точката A е негов връх. При въртене на крака BV около оста AB се образува повърхност, наречена основа на конуса. Ъгълът между образуващата AG и оста AB е ъгълът a на наклона на конуса. Ъгълът VAG между образуващите AB и AG на конуса се нарича ъгъл на конуса; то е равно на 2а. Ако отрежем горната му част от пълен конус с равнина, успоредна на основата, тогава полученото тяло ще бъде пресечен конус (фиг. 206.6), който има две основи - горна и долна. Разстоянието 001 между основите е височината на пресечения конус. На чертежа обикновено се посочват три основни размера на конуса (фиг. 206, c): по-големият диаметър D, по-малкият диаметър d и височината на конуса.
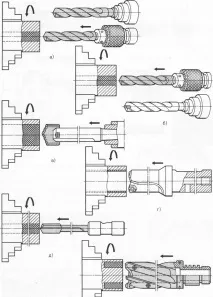
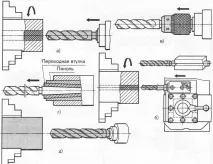
Използвайки формулата tga \u003d \u003d (D - d) / (2l), можете да определите ъгъла a на наклона на конуса, който е зададен на струга чрез завъртане на горната опора или преместване на задната част. Понякога конусът се задава, както следва: K \u003d (D - d) / l, т.е. конусът е съотношението на разликата в диаметрите към дължината. На фиг. 206, d показва конус, в който K = (100 -90) / 100 = 1/10, т.е. на дължина от 10 mm диаметърът на конуса намалява с 1 mm. Конусността и диаметърът на конуса са свързани с уравнението d = D - Kl, откъдето D = d + Kl.
Ако вземем съотношението на полуразликата на диаметрите на конуса към неговата дължина, тогава получаваме стойност, наречена наклон на конуса M \u003d (D - d) / (2l) (фиг. 206, д). Наклонът на конуса и конусността обикновено се изразяват в съотношения 1:10, 1:50 или 0,1:0,05 и т.н. На практика се използва формулата
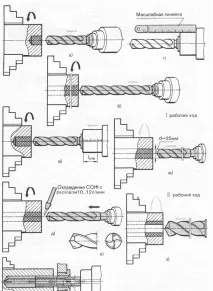
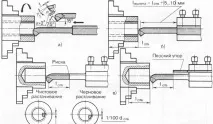
В машиностроенето морзовите и метричните конуси са често срещани. Конусът на Морз (фиг. 207) има седем числа: 0,1, 2, 3, 4, 5 и 6. Всяко число отговаря на определен ъгъл на наклон: най-малкото е 0, най-голямото е 6. Ъглите на всички конуси са различни. Метричните конуси имат конус от 4; 6; 80; 100; 120; 160 и 200; имат еднакъв ъгъл на наклон (фиг. 208).
Обработката на конусовидни повърхности се различава от обработката на цилиндрични само по ъгъла на подаване на фреза (фиг. 209), което се постига чрез настройка на машината. Когато детайлът се върти, върхът на ножа се движи под ъгъл a (ъгълът на конуса). На струг конусите се обработват по няколко начина. Обработката на конус с широк фреза е показана на фиг. 210 а. В този случай височината на конуса трябва да бъде не повече от 20 mm. В допълнение, режещият ръб на фрезата е поставен под ъгъл a спрямо оста на въртене на частта точно по височината на центровете (фиг. 210.6).
Най-лесният начин за получаване на конусовидни повърхности е изместването на централната линия. Този метод се използва само при обработка на повърхности в центровете чрез изместване на тялото на опашката. Когато тялото на задната част се премести към работника (към държача на инструмента), се образува конична повърхност, в която по-голямата основа на частта е насочена към главата (фиг. 211, а). Когато тялото на опашката е изместено от работника, по-голямата основа е разположена към опашката (фиг. 211.6). Странично изместване на корпуса на опашката H = L - sina. С леко изместване на ъгъла на наклона на конуса a, можем да приемем, че sinaa; tga, тогава H = L(D - d)/(2l). Преместването на тялото на задната стойка се измерва с линийка (фиг. 211, c), подравняването на центровете също може да се провери с линийка (фиг. 211, d). Въпреки това, когато премествате тялото на задната част, трябва да се има предвид, че преместването е разрешено не повече от 1/50 от дължината на частта (фиг. 211, д). При по-голямо изместване се образува непълно прилягане на централните отвори на частта и центровете, което намаляваповърхностна точност.
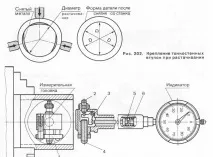
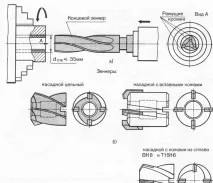
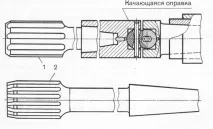
Целесъобразно е да се обработват конуси с голям ъгъл a и малка височина чрез завъртане на горната опора. Този метод се използва при обработка на външния (фиг. 212, а) и вътрешния (фиг. 212.6) конус. В този случай ръчното подаване се извършва чрез завъртане на дръжката на горната опора. За завъртане на горния шублер до необходимия ъгъл с механично подаване се използват деления, отпечатани върху фланеца на въртящата се част на шублера. Ако ъгълът a не е посочен на чертежа, той се изчислява по формулата tga = (D - d) / (2l). Фрезата е поставена строго в центъра. Отклонение от праволинейността на генератора на обработения конус възниква, когато фрезата е монтирана над (фиг. 213.6) или под (фиг. 213, c) централната линия.
За да се получат конични повърхности с ^ 10 ... 12 °, се използва линийка за копиране (фиг. 214). Върху плочата 1 е монтирана линийка 2, която се завърта под необходимия ъгъл a около щифта 3 и се фиксира с винт 6. Плъзгачът 4 е здраво свързан към напречната част на опората 8 с помощта на прът 7 и скоба 5. Копирната линийка трябва да бъде монтирана успоредно на образуващата на конуса, който трябва да се получи. Ъгълът на завъртане на копирната линийка се определя от израза tga = (Z) - d) / (2l). Ако деленията на плочата са посочени в милиметри, тогава броят на деленията е C - H (D - d) / (2l), където R е разстоянието от оста на въртене на линийката до нейния край.
Конус, в който дължината на генератора е по-голяма от дължината на хода на горния шублер, се завърта чрез прилагане на надлъжно и напречно захранване (фиг. 215). В този случай горната шейна трябва да се завърти под ъгъл p спрямо централната линия: sinp \u003d tga (Snp / Sn + 1), където OPR и Sn са надлъжното и напречното захранване. За да се получи конус с необходимата форма, фрезата е поставена строго в центъра.
Коничният отвор се обработва в следната последователност. Пробива се отвор с малко по-малък диаметър от диаметъра на по-малката основа на конуса (фиг. 216), след което отворът се пробива със свредло. След това стъпаловидният отвор се пробива с фреза. Друг начин за получаване на коничен отвор е пробиване на отвор (фиг. 217, а), грубо разстъргване (фиг. 217.6), полуобработка (фиг. 217, в), довършителни работи (фиг. 217, г).
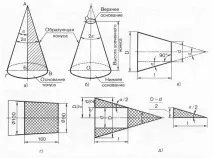
Коничните повърхности се контролират от гониометри (фиг. 218, a), измервателни уреди (фиг. 218, b, c) и шаблони (фиг. 218, d). Конусните отвори се проверяват за издатини и рискове, маркирани върху измервателните уреди (фиг. 219). Ако краят на коничния отвор на частта съвпада с левия край на перваза, а външният диаметър съвпада с една от маркировките или е между тях, тогава размерите на конуса съответстват на посочените.