Отстраняване на неизправности и контрол при ремонт на машини, Агро Корзина
Селскостопански материали
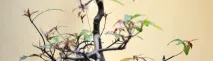
Главно меню
Навигация на публикации
Отстраняване на повреди и контрол при ремонт на машини
Статията разглежда процедурата за отстраняване на неизправности на възли, възли и части на селскостопанска техника по време на нейния ремонт, както и контрол - крайната операция по време на производството на нови части или актуализиране на износени.
Най-важните процеси при ремонта на селскостопански машини са отстраняването на неизправностите и контролът върху годността на частите. Отстраняването на неизправности се извършва след разглобяване на възли, възли на части, за да се идентифицират дефекти и да се оцени годността на частите за по-нататъшната им употреба. Частите са сортирани в групи: подходящи за по-нататъшна употреба, такива, които подлежат на ремонт, и негодни. Проверката е крайната операция по време на производството на нови части или подновяването на използвани и се извършва за оценка на: размерите, твърдостта, отклоненията на формата и взаимното разположение на работните повърхности. Качеството на ремонтираните продукти зависи от качеството на контрола.
Отстраняването и контролът се извършват по три метода: органолиптичен, инструментален и специален.
Органолептичният метод е откриването на дефекти чрез инспекция и слушане.
Чрез инструменталния метод се определя състоянието на работните повърхности, като се измерват с помощта на универсален и специален инструмент. Използването на специални инструменти за измерване: скоби, измервателни уреди, шаблони и позволява незабавно да се направи заключение за годността или негодността на частта.
Същността на специалния метод е използването на специални устройства, стендове, методи за идентифициране на определени характеристики. Например хидравлично изпитване на цилиндрови блокове за проверка на целостта на кожухаохлаждане.
Рационалната последователност на дефектиране ви позволява да спестите работно време. Маршрутът трябва да бъде изграден според правилото: от просто към сложно, от сложно към най-трудно.
Най-голямата част в детайлите са цилиндрични повърхности. Те се обработват основно по шести – девети ценз. Работата на тези повърхности е разрешена до 0,020-0,030 mm. А състоянието на нишката се контролира чрез външна проверка и габарити. Болтове, шпилки, гайки и тапи, които имат повече от две оголени резби, се отхвърлят. Не използвайте болтове, тапи и гайки със смачкани ръбове.
Състоянието на повърхностите на зъбите на зъбните колела се определя първо чрез проверка. При счупване и откъртване не се допуска използването на зъбни колела. Ако няма признаци на дефект, оценката за годността на зъбните колела се определя въз основа на измерването на зъбите, предлагани от производителя.
Отстраняването на неизправностите на правите гнезда се извършва с дебеломер или шаблон. Работата на шлиците е разрешена в рамките на 0,4-0,8 mm.
Пригодността на радиалните търкалящи лагери се оценява чрез резултатите от външна проверка, проверка на гладкостта на изтичането и измерване на радиалната хлабина. Радиалната хлабина се определя на специални устройства с различни конструкции. Допустимата стойност на радиалната хлабина на търкалящите лагери е толкова по-малка, колкото по-отговорно е мястото на нейното монтиране, т.е. лагер, който не е подходящ за работа на едно място, може да се използва на друго, по-малко критично.
За конусните лагери се определя монтажната височина, която е разстоянието между противоположните краища на вътрешния и външния пръстен.
Ако има пукнатини, прорези, дълбока корозия по повърхността на пружината, тя подлежи на отхвърляне. Измерване на генерираната силапружината се извършва на специални устройства (например MIP-100), чиито основни елементи трябва да бъдат владетел и инструмент за измерване на силата.
Втулково-ролковите вериги, които се използват широко в зърнокомбайни, се проверяват за липса на стружки и пукнатини по ролки, ролки, втулки, плочи. Връзките на веригата трябва да се въртят свободно в пантите, не се допуска заклинване. Разтягането на веригите се контролира чрез измерване на десет брънки, опънати със сила 300-400 N. Измерванията се извършват с шублер на три секции, разположени равномерно по цялата дължина на веригата.
При верижните зъбни колела работата на зъбите се контролира чрез измерване на тяхната дебелина, както и диаметрите на монтажните отвори на главините и работата на шпонковите и шлицовите канали.
В случай на масов (специализиран) ремонт на определени продукти, работилницата оборудва работното място на дефектьора, което е оборудвано по съответния начин. Във фермите отстраняването на неизправностите се извършва главно на мястото на разглобяване на продукта.
Предметите трябва първо да бъдат почистени. Температурата на частите и измервателния инструмент трябва да бъде еднаква.
Задължителен елемент от процеса на отстраняване на неизправности е техническата документация, без която е невъзможно да се знаят нормалните (фабрични) и допустимите размери на повърхностите.
Контролът върху годността на частите трябва да се извършва чрез позоваване на фабрични или ремонтни чертежи, които в момента не са налични за повечето машини или са налични, но на значителна цена.