Пещ за синтероване (машина за синтероване)
Пещ за синтероване - пещ, предназначена за производство на синтер. Агломератът е малки материали, синтеровани на парчета (фини руди, прахообразни руди и флюсове). Агломерацията в пещта за синтероване възниква главно в резултат на образуването на течни, нискотопими химични съединения, които при охлаждане свързват отделните зърна в парчета.
Има няколко метода за агломерация:
- с всмукване на въздух в слоя отгоре надолу;
- в ротационни пещи;
- в окачено състояние;
- с подаване на въздух отдолу.
Най-разпространен е първият метод на синтероване - върху решетка с засмукване на въздух през шихтовия слой. За справка: решетка е решетка, изработена от чугунени решетки с проходни отвори за подаване на въздух и предназначена да поддържа слой горящо гориво в пещта. С използването на решетка процесът на агломерация може да бъде периодичен (агломерация в купа) и непрекъснат (на транспортна лента на машина за синтероване).
В металургичните заводи агломерацията се извършва главно в машини за синтероване от лентов тип, които представляват непрекъсната верига от колички за синтероване с решетъчно дъно, изработено от решетки.
Принципът на действие на агломерационната машина е следният. На агломерационни колички през питатели се поставя „легло“ с височина 30-35 mm от част от подходящ агломерат с размер на частиците 10-25 mm и върху него се поставя заряд, състоящ се от фина руда, концентрат, кокс, варовик и вар. Височината на заряда е 250-350 мм. Под лентата на количките за синтероване се създава вакуум от около 7-10 kPa, в резултат на което външният въздух се засмуква през горната повърхност на слоя. Последователно движейки се, количките попадат под огнището, което служи за запалване на кокса в заряда. Клаксонът се нагрявагорелки. Като гориво обикновено се използва смес от газ от доменна пещ и коксова пещ с калоричност 5900-6300 kJ / m³. Консумацията на газ е приблизително 30 m³ / t агломериран газ. Температурата на заряда в огнището достига 1200-1300 °C.
След излизане на сместа от огнището, горенето се поддържа в резултат на засмукване на атмосферен въздух под действието на разреждане. В зоната на горене температурата достига 1500 °C. Продуктите от горенето отдават топлината си на долните слоеве и излизат с температура 60-150 °C.
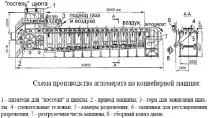
Когато зоната на горене достигне „леглото“, процесът на синтероване завършва. Продължава 10-20 минути. Полученият агломерат има средна температура около 500 °C.
Готовият кейк от агломерат се раздробява, след което връщането (5 мм) се отделя на сита. След това подходящият агломерат се охлажда в специален охладител чрез продухване или засмукване на въздух. Има флюс (с варовикови добавки) и нефлюсован агломерат (без варовик и вар). Използването на флюсов агломерат позволява спестяване на скъп кокс в доменните пещи.
Приблизителните материални и топлинни баланси на синтероването на шихтата в машината за синтероване са дадени в табл. 2.7 и 2.8. При съставянето на балансите са приети следните състави на материалите. Рудна смес: FeO - 7%; Fe2O3 - 59; MnO - 2; SiO2 - 9; Al2O3 - 3; CaO - 1; MgO - 3; CO2 - 6%. Агломерат: FeO + Fe2O3 + S + FeS + FeS2 + SO3 + P2O5 + MnO = 68%; SiO2 - 10; Al2O3 - 4; CaO - 15; MgO - 3%. Горивна смес: 80% кокс и 20% антрацит.
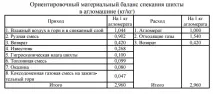
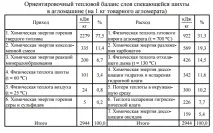
Ефективността на процеса на агломерация е 0,85-0,87. Специфичният разход на стандартно гориво (твърдо гориво + газово гориво) е около 80-100 kg еквивалент на гориво/t флюсов агломерат.
Икономията на гориво на агломерационните машини е възможна в следните области:
- използване на топлината на горещ агломерат за предварително загряване на въздуха;
- използването на газова агломерация, т.е. засмукване през зарядния слой на смес от доменен газ с въздух, който се запалва в зоната на горене. Това може значително да намали потреблението на кокс;
- въздушно отопление в отделна горивна камера. Целта е същата – намаляване потреблението на кокс;
- увеличаване на слоя заряд с едновременно увеличаване на разреждането под количките за синтероване. Всяко 20 mm увеличение на височината на слоя заряд осигурява от 0,6 до 1,5% икономия на гориво. Отрицателни последици: известна загуба на производителност на агломерационната машина;
- въвеждането на малки запалителни пещи с нисък разход на гориво за запалване поради бързото нагряване на повърхностния слой на заряда. Възможно е да се намали консумацията на газ 2-3 пъти.
Машините за синтероване са лентови и кръгли. Най-често срещаната е лентовата машина за синтероване. Машината е безконечна лента, състояща се от голям брой колички, движещи се по рамката, затварящи се една с друга. Количките се задвижват от две предавки, разположени в челото на машината. Тези колела подхващат отделни колички със зъбите си, повдигат ги от долните релси към горните и ги избутват към опашката на пещта. По този начин се образува непрекъснат непрекъснато движещ се влак от отделни талиги, които, достигайки края на машината, се търкалят върху долните водачи и под въздействието на тежестта достигат до задвижващите колела по тях.
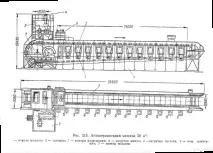
Количките са изработени от сферографитен чугун или стомана и представляват участъци от корито, чието дъно се състои от решетка. Под решетките има газови камери, свързани с аспиратор, който създава вакуум в тях. първоначално зареждане,за изпичане и синтероване, се зарежда от бункера в главата на машината върху решетката на колички със слой с дебелина 100-400 mm. Веднага след зареждането зареждащият слой се нагрява с помощта на малка пещ, разположена над машината и загрята от въглеродно гориво. Газовете на тази пещ се насочват директно към слоя заряд, в резултат на което температурата му се повишава и в слоя се развиват процеси на окисляване и синтероване. Въздухът за окислителни процеси се засмуква през слоя от синтерован материал поради значително разреждане под решетката, създадено от изпускателя в газовите камери. Агломерираният материал под формата на пай се движи върху колички със скорост 1–4 m/min, а в опашката на машината, в резултат на отделянето на количките от влака и удрянето на други колички, агломератът се изхвърля от решетката в приемен бункер. Машините за синтероване имат работна ширина на решетката от 1–4 м, с ефективна дължина на машината от 6,6–75 м. Работната площ на машините е съответно 6,6–300 м 2.
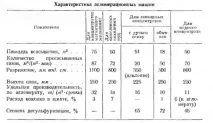
Пускане и експлоатация на агломерационни машини
Пускането в експлоатация на агломерационни машини обикновено съвпада с пускането в експлоатация на нови агломерационни инсталации или с пускането в експлоатация на следващия етап от строителството на вече работеща инсталация. И в двата случая пускането на машините е възможно само след приключване на строително-монтажните работи във всички части на завода, като се осигури доставката на пусковата машина със заряд. Освен това трябва да бъде завършена, тествана и пусната в експлоатация приточна и смукателна вентилация в основната сграда на завода. В други помещения на завода може да се пусне вентилация паралелно с доставката на технологичните звена на завода.
Пускането в експлоатация на фабриката трябва да започне с калибриране на захранващите устройства на партидния отдел.
Работата по калибриране се извършва няколко дни преди товапредстоящото пускане на завода успоредно с практическия инструктаж на работниците от отдела за зареждане. За калибриране на захранващите устройства в отделението за зареждане е монтирана десетична скала, която остава там постоянно дори след пускане в експлоатация на цялата фабрика, за да може систематично да се проверява калибровъчната скала. Освен кантар е необходимо и леко метално корито, което при поставяне на конвейера трябва да минава свободно под бункерните хранилки.
Градуирането се извършва на различни височини на пълнене на бункерите с материали, тъй като в зависимост от височината на материалната колона в бункера, при една и съща височина на портата на захранващото устройство, количеството на разпределения материал ще бъде различно. Обикновено е достатъчно да се калибрира, когато бункерът е пълен, наполовина пълен и една трета пълен, което може да се направи след пускане на завода.
Градуирането се извършва по следния начин: върху движещ се транспорт се поставя корито, в което постъпва материал от захранващото устройство по време на преминаването му под бункера. Времето на преминаване на коритото под бункера се записва с хронометър. След това коритото се изважда от конвейера и се претегля, за да се определи теглото на заредения в него материал. При същото повдигане на вратата се правят две или три измервания и се взема средноаритметичната им стойност. Познавайки теглото на материала и времето, за което е влязъл в конвейера, производителността на захранващото устройство се изчислява при определено повдигане на вратата, което е изобразено под формата на графика, поставена на всяко захранващо устройство за ежедневна употреба.
Преди подаване на шихтата към агломерационните машини се проверяват и изпитват газопроводите и въздуховодите към огнището, входовете и изходите на водата за огнището и хидравличните уплътнения, пусковото оборудване, блокировката и сигнализацията.
Машината е стартиранав следната последователност:
- Пуснете вода в охладената система на запалителната ковачница и в маркучите на хидравличното уплътнение на ковачницата.
- Пускането на аспиратора се извършва при затворени капаци на вакуумните камери и шибъра на аспиратора.
- Запалете клаксона. Първото запалване на огнището, за да се избегне разрушаването на зидарията, се извършва с постепенно повишаване на температурата за 4-6 часа. до работна температура 1100-1200°.
Стартирането на газ в горелката е разрешено само при добре горящ огън под планински огън. Продуктите от горенето се отвеждат през първата и втората вакуумни камери, като за целта на тези камери се отварят шибъри и изпускателен шибър за осигуряване на вакуум в първите две камери от порядъка на 200-300 mm.
Прехвърлянето на огнището към газ се извършва в следния ред:
- отворете вентила, пуснете въздух в горелката;
- пуснете газ при налягане не по-ниско от 30 mm воден стълб. Изкуство.;
- настройте на автоматичните регулатори определеното съотношение въздух - газ.
Разпалването на огнището и прехвърлянето му на газ може да се извърши и с колички, предварително заредени със заряд. Непрекъснатото натоварване на талигите със заряд се извършва след запалване на огнището и вагоните се подават под агломерата или агломерата се приема по друг начин, предвиден в завода.
С пускането на шихтата на машината, с придвижването на количките за синтероване, последователно се отварят вратите на вакуумните камери и се проверява с гореща горелка работата на уплътнителната система от двете страни на машината и в крайните части. Освен това той проверява:
- температурата на изходящата вода от охладителната система на огнището и уплътнителните маркучи, която за огнището не трябва да надвишава 80 °, а за уплътнението 20-30 °;
- показания на електроизмервателната апаратура при зададен режим на работа на агломерационната машина;
- равномерно доставяне и пълнене на количките с постеля и заряд до зададената височина на слоя;
- непрекъснато подаване на смазка към уплътнителните плочи;
- липса на стъпала във веригата от талиги, движещи се по горния път;
- равномерно запалване на повърхността на заряда по цялата равнина на огледалото за запалване;
- по време на стартиране на машината е необходимо да се следи смазването на лагерите, зъбните колела и ролковите зъби на задвижващите зъбни колела.
За да се избегне значително нагряване на страните и телата на палетите, е забранено спирането на машината за повече от 3-5 минути. под работеща планина.
Всички забелязани недостатъци в работата на машината и спомагателното оборудване незабавно се отстраняват, а при постигане на нормална работа на всички механизми пробният пуск приключва и машината или целият завод се пуска на постоянна работа.
В периода на подготовка за пуска се разработват подробни инструкции за основните работни места, набира се персонал на завода, с който се изучава необходимия технически минимум по специална програма и се допускат до работа тези, които са усвоили необходимия минимум знания и са преминали подробен инструктаж по охрана на труда и безопасност.
По време на пробния пуск предварителните инструкции се уточняват, допълват и след одобрение от ръководството на предприятието се поставят на видни места за ежедневно ползване.