Процеси за получаване на метали Суровини за топене в доменни пещи, подготовка на железни руди - Производство
Процеси за получаване на метали: суровини за топене в доменни пещи, подготовка на железни руди - Производство на пелети от желязна руда
Процеси за получаване на метали: суровини за топене в доменни пещи, подготовка на железни руди |
Етапи на високотемпературно коксуване на каменни въглища |
Изграждане на коксови пещи и цехове |
Качество на кокс |
Желязни руди |
Оценка на качеството на железните руди |
Извличаемост на рудата |
Най-важните находища на желязна руда |
Най-големите чуждестранни находища на желязна руда |
Съвременна схема за подготовка на руди за топене в доменна пещ |
Обогатяване на руда |
Агломерация на железни руди и концентрати |
Конвейерни машини за синтероване |
Реакции между твърди фази |
Топене на шихтата, кристализация на стопилката |
Отстраняване на вредни примеси от шихтата по време на агломерирането на руди и концентрати |
Качество на агломерата |
Производство на пелети от желязна руда |
Високотемпературно втвърдяване на пелети |
Получаване на пелети без печене |
Металургични свойства на пелетите |
Сравнение на металургичните свойства на агломерата и пелетите |
Всички страници |
PПроизводство на пелети от желязна руда
По време на агломерацията на фино раздробени концентрати от желязна руда, скоростта на процеса значително намалява (поради рязко намаляване на газопропускливостта на заряда). МеждуВъпреки това, поради постоянното увеличаване на дела на рудата, подложена на обогатяване, все повече и повече суровини от желязна руда, съдържащи 80–90% или повече фракции, участват в металургичния процес.
Успешно решение на проблема с агломерацията на фини концентрати от желязна руда е производството на пелети от желязна руда, предложено за първи път през 1912 г. от Anderson (Швеция) и през 1913 г. от Brakkelsberg (Германия). Производството на пелети от желязна руда напоследък се разви бързо в много страни по света и сега надхвърли 200 милиона тона годишно.
Схемите за пелетиране са комбинация от два етапа: образуване на пелети чрез пелетизиране на мокра шихта в специални апарати - пелетизатори (производство на сурови пелети) и втвърдяване на гранулите (чрез методи на печене или без изпичане), за да се придаде на пелетите необходимата якост за съхранение, транспортиране до доменни пещи и тяхното топене в пещи.
Зелените пелети се образуват чрез пелетизиране на фино диспергиран материал от желязна руда, който е навлажнен до известна степен. Фино смляната желязна руда на прах принадлежи към хидрофилни дисперсни системи, характеризиращи се с интензивно взаимодействие с водата. В такава система желанието за намаляване на енергията се реализира чрез намаляване на повърхностното напрежение на фазовата граница (по време на взаимодействие с вода) и огрубяване на частиците (в резултат на тяхното сцепление). Може да се приеме, че като цяло дисперсната система желязоруден материал-вода има определена термодинамична склонност към пелетизиране.
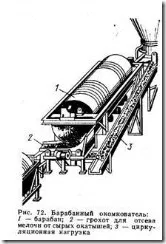
Суровите пелети трябва да имат достатъчна здравина, за да се избегне деформация и разрушаване, когато бъдат доставени до съоръжението за печене, както и добра термична стабилност, т.е. способността да не се срутват по време на печене. За подобряване на тези свойства,в пелетния заряд се въвеждат свързващи добавки (главно бентонит, както и сместа му с вода, вар, калциев хлорид, железен сулфат, хуминови вещества).
Най-широко използван в производството е бентонитът, който в количество от 0,5–1,5% се въвежда в шихтата преди пелетизиране. Бентонитът е глина, характеризираща се с фина дисперсия, йонообменна способност, висока степен на набъбване при навлажняване, кохерентност и способност за постепенно освобождаване на вода при нагряване. Бентонитът се състои главно от монтморилонит (Al, Mg)2_3(OH)2-(Si4O10)-/iH2O и близки до него минерали по състав. Част от катионите на кристалната решетка могат да бъдат заменени с Ca 2+ и Na 1+ йони. Когато се навлажни, бентонитът интензивно абсорбира вода, увеличавайки обема си 15-20 пъти. Изборът на бентонит се дължи на способността му при навлажняване да образува гелове с изключително развита специфична повърхност (600–900 m 2 /g), която е приблизително 7 пъти по-голяма от повърхността на частици от други видове глина. Бентонитът увеличава порьозността на зелените пелети, което влияе благоприятно върху скоростта на отстраняване на влагата по време на сушенето на пелетите, без да намалява тяхната здравина.
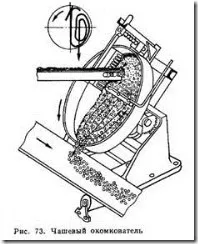
В съвременните инсталации за пелетиране суровите пелети се произвеждат в пелетизатори тип барабан и диск (или купа). Барабанният пелетизатор (фиг. 72) е цилиндричен барабан с гладка вътрешна повърхност, който е разположен под ъгъл спрямо хоризонта (до 8-9 °) и се върти на ролки (скорост на въртене 7-11 минути "1). Ядрата на пелетите, когато се движат в барабана, под действието на гравитацията и центробежната сила, се притискат към повърхността на барабана. В същото време, върху тях се валцува слой концентрат от фина фракция.Размерите на индустриалните барабани са доста големи: диаметър 3 m и повече, дължина до 14 m.на такива агрегати за сурови пелети е над 90-100 т/ч. Барабанният пелетизатор не дава възможност за производство на пелети от фин клас, поради което зад барабана е монтиран механичен сито, който пресява пелети от фина фракция (обикновено
Пелетизаторите с форма на купа или чиния (фиг. 73) представляват наклонено монтиран (под ъгъл 45-60 °) диск със страна. Първоначалният заряд, зареден във въртящата се купа, се заклинява между страната и дъното и се издига на определена височина. Спускайки се по наклоненото дъно, ядрата се търкалят върху себе си слой от тънък концентрат, превръщайки се в сферични частици. Като се има предвид, че частици с големи размери и маса могат да се издигнат на голяма височина по дъската, когато плочата се върти, височината на дъската регулира крайния размер на зелените пелети.
Диаметърът на плочата на съвременните индустриални гранулатори е 5–7 м. Специфичната им производителност зависи от свойствата на шихтата и достига 90 т/ч. Дисковите гранулатори, отстъпващи на барабанните гранулатори по производителност и стабилност, осигуряват по-равномерен размер на пелетите, позволяват възможност за регулиране и оперативно преструктуриране на режима на работа. За дисковите пелетизатори, както и за барабанните, е важно да се поддържа висококачествен слой на черепа, правилният избор на ъгъла на наклон и скоростта на въртене на купата и съдържанието на влага в материала.
Механичната якост на суровите пелети трябва да е достатъчна, за да предотврати разрушаването им по време на транспортиране до съоръженията за печене. Към днешна дата няма разумна методология за определяне на големината на кохезионните сили в зелените пелети. Обикновено статичните и динамичните натоварвания се моделират съответно чрез тестове за смачкване и падане.
Тестът за смачкване се провежда чрез компресиране на пелетата, за да сеопределяне на силата, при която пелетите се деформират или счупват. Минималната якост на смачкване на една пелета трябва да бъде 45-55 N за пелети с диаметър 25 mm и 9 N за пелети с диаметър 9,5 mm.
При тестване на падане е важно да изберете правилната височина. В съответствие с действителните нива на височина на конвейерите по време на презареждане, височината на падане трябва да бъде най-малко 300 mm. В България суровите пелети трябва да издържат поне 15 изпускания от височина 300 мм без да се счупят. В САЩ стандартната височина на теста за падане (5 пъти) е 457 mm.