РАЗРАБОТВАНЕ НА МЕТОД ЗА ИЗРАВНЯВАНЕ НА МАКСИМАЛНИ ДЕФОРМАЦИИ В НАПРЕЧНИ СЕЧЕНИЯ НА ТРАНСПОРТНИ ЛЕНТИ -
Понастоящем рамките на транспортните ленти по дължина се състоят от надлъжни нишки - основи или стоманени кабели, разположени успоредно по цялата ширина на лентата с еднаква стъпка между тях и възприемат цялото общо натоварване от съпротивлението на движение на натоварената лента, значителна част (0,25-0,7) от която се дължи на компресия и разширяване на товара от лентата върху междуролковите пространства по цялата дължина на конвейера. или В същото време, ако стоманените кабели са разположени в лентата в един слой, тогава надлъжните нишки на гумено-тъканните ленти са подредени многослойно под формата на отделни платнени дистанционери, но всички те са закрепени заедно с гумен пълнител, който придава определена твърдост и здравина на лентите. За да се предотврати разпиляване на малки части от товара, правилата за безопасност предвиждат свободни граници от двете страни на лентата, а товарът се концентрира в средната част на напречното сечение на лентата, т.е. нейните надлъжни силови елементи изпитват най-голяма деформация. В допълнение, страничните свободни полета, поради малката деформация на техните силови елементи, се превръщат в допълнително натоварване за средната част на секцията на лентата. В тази връзка, когато участъкът на лентата излезе от разтоварващия барабан, поради липсата на натрупване на движещи се маси върху барабана, всички надлъжни носещи елементи на лентата трябва да бъдат подложени на същата максимална деформация. Ако за средната част на лентата тази деформация се постига постепенно, като статична, то за свободните странични полета се постига като моментна динамична с динамичен коефициент>2, което е съпроводено с разкъсване на гумени пълнители в тези места. В резултат на това в гумено-тъканните ленти се получава отделяне на уплътненията, а в гумените ремъци се придружава от освобождаване на кабелите от ремъците. И в двата случая лентите са подложени на интензивно унищожаване и преждевременно излизане отсграда. Следователно е необходимо разработването на проактивни начини за защита на транспортните ленти от максимални деформации.
Известен е метод за защита на гумено-тъканни ленти от максималните им деформации чрез увеличаване на коефициента на безопасност и едновременно намаляване на допустимото натоварване на единица ширина (cm) на едно уплътнение [1]. Например, за свръхздрав колан (OPB) с брой на уплътненията от 2 до 4, коефициентът на безопасност n = 10, а допустимото натоварване на 1 cm от ширината на уплътнението е 11,5 kg; с броя на дистанционните елементи от 5 до 8, n = 11, допустимото натоварване е 10,4 kg на 1 см. С броя на дистанционните елементи 9-12, n = 12, а допустимото натоварване е 9,1 kg на 1 cm.
Най-прогресивният метод за защита е предложен в [2], където се предлага защита на гумено-кабелни ленти само с един постоянен параметър n = 9, независимо от броя на кабелите в лентата, техния диаметър и ширина на лентата, което значително опростява изчисляването и избора на транспортни ленти. Недостатъците на този метод са: значителна маса на лентата, сложността на поддръжката на лентата и конвейера, високата специфична консумация на материал и консумацията на енергия на конвейера, значителната цена на лентата, значителни загуби на производителност при смяна на ленти.
Очевидно е, че минимизирането на загубите може да се постигне само ако формата и параметрите на участъка на лентата с товара се запазят непроменени във всеки характерен участък на конвейера, т.е. ако участъкът на лентата е представен като лъч с еднаква устойчивост на огъване. Както е известно, когато греди с постоянно сечение са огънати, всичкисекциите, в допълнение към опасната, имат прекомерна граница на безопасност, което показва нерационалното използване на материала. Най-рационална би била такава форма на гредата, при която напреженията във всички напречни сечения ще бъдат еднакви (равни на допустимите), такива греди се наричат греди с еднаква устойчивост на огъване.
През 2014 г. в катедрата по индустриален транспорт на Държавния технически университет в Караганда (Караганда) беше извършена работа за разработване на метод за изравняване на максималните деформации в напречните сечения на транспортните ленти. Разработеният метод е илюстриран на фигурата и се състои от следните стъпки:
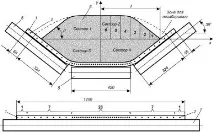

Начин за изравняване на максималните деформации в напречните сечения на транспортните ленти: гумено-кабелна лента 1; кабел 2; гумено-тъканна лента 3; уплътнения 4; средна ролка 5; странична ролка 6; долна ролка 7; товар 8
1. По време на работа на лентовия транспортьор, участъкът от товара върху лентата на тавата при ъгли на наклон на страничните ролки от 38 ° (равен на ъгъла на наклона на материала в движение) се оформя под формата на правилна елипса, която, за да се оптимизират и опростят изчисленията на параметрите на масата на товара върху лентата, трябва да бъде разделена по площ на четири равни сектора.
2. Площите на всеки сектор са разделени според модела на квантово-екстремалното разпределение на шест характерни секции Δ = l/6 по оста x, а по оста y - според големината на квантите на вероятността за поява на стойности на случайна променлива.
3. Определянето на площите на характерните сечения и натоварванията, действащи в тях, се извършва с помощта на теоремата на D.I. Журавски. Изчисленията показват, че основната част от натоварването пада върху лентата над средната ролка - повече от 75%.
4. Въз основа на резултатите от определянето на натоварването, действащо от товара върху колана, се определя броят на силовите елементи(платени подложки или кабели) в лентата. Това се осъществява с дискретна промяна на броя на силовите елементи, което превежда напречното сечение на транспортните ленти в режим на работа на греда с еднаква устойчивост на огъване, на гумено-кабелните ленти се постига чрез промяна на стъпката между кабелите, а в гумено-тъканните ленти - чрез промяна на ширината и броя на дистанционните елементи над страничните ролки.
Броят на силовите елементи над страничните ролки в натоварените секции на лентата трябва да съответства на 1/3, а в ненатоварените секции на лентата - 1/6. Примери:
1) при гумено-кабелна лента с широчина 1200 mm кабелите се подреждат на разстояние 15 mm; в натоварената лента над средната ролка броят на кабелите е 28 (420/15 = 28), а след това се извършва дискретна промяна в броя на кабелите над страничните ролки в натоварените секции на лентата със 7 (324/15 = 21,6; 21,6/3 = 7,2 - 7) кабела и отстрани на ненатоварените секции на лентата с 1 (66 /15 = 4,4; 4,4/6 = 0,73-1 ) кабел;
2) ако според условията на якост преминава шестслойна гумено-тъканна лента, тогава трябва да има 6 подложки с ширина b1 над средната ролка в лентата, 2 (6/3 = 2) подложки с ширина b2 всяка над страничните ролки в натоварените секции на лентата и 1 (6/6 = 1) подложка с ширина b3 отстрани на ненатоварените участъци на лентата.
В резултат на подобряване на метода за изравняване на максималните деформации в напречните сечения на транспортните ленти е получен иновативен патент на Република Казахстан [3]. За по-висока точност при определяне на рационални проектни параметри са необходими подробни проучвания с разработването на цифров модел в софтуерната среда на Sol >
Така разработеният метод дава възможност за ефективно изравняване на максималните деформации в напречните сечениятранспортни ленти. Изчисленията, проверени на примера на ленти с ширина 1200 mm, показаха, че при използване на разработения метод за ленти с гумени кабели броят на кабелите намалява от 80 на 44, за шест подложки от гумена тъкан, броят на подложките над страничните ролки се намалява до три, т.е. два пъти. Съответно, масата и цената на транспортните ленти намаляват, енергийната интензивност на лентовия транспортьор се намалява средно 1,5 пъти. Движението на товара под въздействието на деформация на лентите изчезва, съпротивлението на движение намалява с 1,4 - 1,7 пъти, в резултат на което отделянето на прах по трасето на конвейера ще намалее средно 1,25 пъти. Гумено-тъканната лента превъзхожда предишния си режим на работа 2 пъти по техническо ниво, а гумено-кордната - 1,83 пъти. Взети заедно, тези мерки осигуряват намаляване на инсталираната задвижваща мощност при дадена производителност на конвейера средно 1,5 пъти.