Режими на Chrome
При възстановяване чрез хромиране на големи части, които не се побират във ваната, се използват различни конструкции на специални вани, които позволяват хромиране без баня (локално). Същността на този метод е, че върху частите на правилното място с помощта на устройство се създава локална баня и се извършва разширение.
Локалното хромиране намери широко приложение за възстановяване на монтажни отвори в частите на тялото (фиг. 1). Хромираната секция на вала е поставена в преносима вана, чиито странични стени са изработени от текстолитни плочи под формата на плъзгащи се сменяеми касети с отвори, равни по диаметър на хромирания вал. Вътре в преносимата вана е поставен анод под формата на два половин пръстена. Електролитът, загрят в основната вана, постоянно се подава в преносимата вана с помощта на помпа и след това се оттича в основната вана.
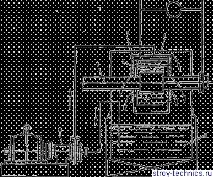
Ориз. 1. Схема на хромиране без баня 1 - вал; 2 - преносима вана; 3 - касета; 4 - анод; 5 - основна баня; 6 - помпа
Защитно и декоративно хромиране се извършва върху предварително нанесен слой от мед и никел във вани с електролит със следния състав: хромен анхидрид - 350 g / l, сярна киселина - 3,5 g / l. Режим на работа на ваната: температура на електролита 35…45°С, плътност на тока на катода 10…60 A/dm2. Подложка от мед с дебелина 0,03 ... 0,04 mm, никел - 0,015 ... 0,02 mm също е необходима за хромиране на части, които работят за износване в корозивни среди.
Хромирането е сложен и скъп процес. Получаването на отлагания със значителна дебелина изисква много време и е свързано с висока консумация на енергия, тъй като ефективността на ваната е изключително ниска и възлиза само на 13 ... 18% при средни скорости на отлагане на хром от 0,02 ... 0,25 mm / h.
Технологията за възстановяване на част чрез хромиране обикновено се изпълнява в такивапоследователности: 1) износените части се шлифоват, за да се получи правилната геометрична форма и необходимото покритие на повърхността. На повърхността на частта, подготвена за хромиране, не трябва да има неметални включвания, черупки, пукнатини, дълбоки драскотини; 2) за отстраняване на грес, частите се измиват с керосин или бензин, последвано от продухване със сгъстен въздух; 3) изолирайте нехромираните части на частта и окачването с помощта на целулоиден лист, цепонов лак (разтвор на целулоид в ацетон), оловно или алуминиево фолио, гума, PVC тръби, винилова пластмаса, текстолит и др.; 4) частите са монтирани на приспособления, които осигуряват тяхното надеждно и удобно закрепване по време на хромиране, добър електрически контакт и равни разстояния между анодите и всички части на хромираните повърхности. Последното е необходимо за равномерно отлагане на хром по цялата повърхност; 5) за отстраняване на мазни отлагания и други замърсители се извършва химическо и електролитно обезмасляване. Химичното обезмасляване се извършва при температура 80 ° C във вани с алкален разтвор със следния състав: сода каустик - 70 g / l, натриев карбонат - 30 g / l. По-ефективно е електролитното обезмасляване, което се извършва в алкална баня от 100 g/l натриев хидроксид и 2...3 g/l течно стъкло, загрята до 65...70°C. За обезмасляване детайлът се суспендира като катод във ваната и се държи 5...6 min при плътност на тока 5...7 A/dm2. Като аноди се използват железни плочи; 6) измити в гореща вода за отстраняване на следи от алкали; 7), за да се отстранят оксидите, които предотвратяват силната адхезия на хрома към повърхностите на частите, се извършва химическо или анодно декапиране. По-често се използва анодно декапиране, при което частите се окачват в хромирана вана като анод.и след загряване те се излагат на ток с плътност 30 A / dm2 за 40 ... 45 s; 8) нанесете хромово покритие при определен режим, избран в съответствие с работните условия на частта. Продължителността на хромирането зависи от дебелината на нанесеното покритие, режима на процеса и състава на електролита. 9) измива се в дестилирана вода за събиране на останалия хромен анхидрид и след това в течаща студена вода; 10) демонтирайте частите от приспособленията, отстранете изолацията и изсушете частите; 11) части, работещи при динамични натоварвания след хромиране, се препоръчва да бъдат подложени на топлинна обработка за 1 ... 2 часа при температура 150 ... 200 ° C; 12) се регулират до необходимите размери чрез шлайфане с абразивни колела CM1-C2 със зърненост 36 ... 46 или CM1-C1 с зърнистост 60 ... 80.
Прост хром. Електролитните хромни покрития имат висока микротвърдост. Въпреки това, хромът има слаба способност за омокряне по отношение на маслото и може да възникне задръстване, ако смазването е недостатъчно. В тези случаи се използва поресто хромиране, което включва същите операции като гладкото хромиране. Върху повърхността на частта се нанася гладко, лъскаво отлагане на хром. По време на отлагането на лъскави утайки се образуват микропукнатини в слоевете на покритието. След това тази повърхност се подлага на анодно ецване, т.е. плюсът е свързан към детайла, а минусът към оловните плочи. В този случай хромът се отделя от покритието неравномерно и главно от ръбовете на микропукнатините, задълбочавайки последните и образувайки мрежа от канали или точки. Времето за обработка на анода за получаване на порьозност варира в рамките на 6…14 min, температура на електролита 58…60°С, плътност на тока 45…S5 A/dm2.
След анодна обработка частите се измиват, изсушават и се подлагат на смилане с меки колела с размер на зърното 200 ... 240 с обилно охлаждане.обработена повърхност с керосин.
Оставането, за разлика от хромирането, прави възможно отлагането на метални слоеве с много по-голяма дебелина (2…3 mm или повече), имащи финозърнеста структура и механични свойства, наподобяващи средно въглеродни стомани.
Скоростта на охлаждане е 10…30 пъти по-висока, а нуждата от електроенергия е 5…6 пъти по-малка в сравнение с хромирането. В допълнение, почивката е по-евтин начин за възстановяване на части от хромирането.
Устойчивостта на износване и здравината на покритията, получени чрез втвърдяване, могат да бъдат подобрени чрез последващо карбуризиране или хромиране.
Ограниченото използване на хромиране и стомана при ремонта на строителни машини се обяснява с относителната сложност, продължителност и висока цена на процесите на възстановяване.
Утаяването има редица предимства пред другите процеси на метално покритие, тъй като се използват евтини и обичайни материали. Оставянето се използва за изграждане на външни и вътрешни повърхности на детайли за фиксирани прилягания с лека намеса, както и за получаване на подслой за тънко хромирано покритие.
Електролитните стоманени покрития могат да бъдат подложени на термична обработка (въглеродяване, втвърдяване, цианиране), което прави възможно широкото използване на втвърдяване при ремонт на строителни машини.
Отлагането на желязо чрез галваничен метод може да се извърши в горещи и студени електролити. Най-често срещаните са горещи хлоридни електролити, които се приготвят чрез ецване на меки стоманени стърготини в солна киселина. Електролит № 1 се използва за детайли с фиксирани прилягания и детайли, циментирани след втвърдяване; електролит № 2 - за получаване на покрития с повишена твърдост с дебелина 2 ... 3 mm; електролит номер 3 -за закалени стоманени детайли с дебелина на покритието до 1 mm, работещи на плъзгане.
Високата температура на електролита и свързаното с това изпарение на вредни примеси, както и високата химическа активност по отношение на стените на ваната и нейното замърсяване с продукти на окисляването, налагат използването на специално оборудване за почивка.
оставащи. извършва се в метални вани, облицовани с гума, азбовинил, емайл или в неметални вани от керамика и фиолит. Електролитът се нагрява до 80...85°C с помощта на масло, излято в корпуса около ваната. Необходимата температура на електролита по време на електролиза се поддържа от електрически нагреватели или парни намотки, спуснати във ваната.
Баните са оборудвани с вентилационно устройство и циркулационен блок, който смесва електролита и го пречиства с помощта на специални филтри.
Подготовката на частите преди напускане е подобна на подготовката на частите, извършена по време на хромиране.
След като останат, детайлите се измиват в гореща вода и разтвор на сода, след което се подлагат на термична обработка (стареене) при 200...250°C и задържане при тази температура за 1,5...2 часа.Тази обработка намалява крехкостта на слоя, премахва вътрешните напрежения и повишава твърдостта на покритието с 15...20%.
Обработката след закаляване се извършва на стругове или шлифовъчни машини, в зависимост от допуска на обработка, необходимата точност и повърхностна обработка на детайла. Дебелината на отложения железен слой след окончателната обработка трябва да бъде най-малко 0,2…0,3 mm.
По този начин върху повърхността на детайла се получават покрития с ниска твърдост (150 ... 20 HB). Повишаването на твърдостта на покритията се постига чрез използване на технологията на твърдо охлаждане, което се произвежда в електролитследния състав: железен хлорид FeCl2 - 200 ... 220 g / l, натриев хлорид NaCl - 200 ... 250 g / l, манганов хлорид MpC12 - 10 g / l, солна киселина HC1 - 0,5.D8 g / l.
Режим на твърдо охлаждане: плътност на тока 5…40 A/dm2, температура 80…85 °С.
Покритията, получени по този начин, имат твърдост над 400 HB и са сходни с белия чугун по отношение на обработваемостта. Те имат устойчивост на износване, равна на устойчивостта на износване на термично обработена стомана, с якост на адхезия на покритието към метала на частта Yu0…150 MPa.