Шлифовъчни материали - Студиопедия
Схемата за смилане на материалите на електродните покрития с довеждането им до необходимия гранулометричен състав се определя от специфичните условия на производството на даден електрод. Въпреки това, за всички електродни индустрии, които смилат бучките материали, основните и необходими операции са: • грубо раздробяване, средно раздробяване и фино смилане, последвано от класификация за отделяне на материала с необходимата гранулация.
Грубо и средно раздробяване на замърсен материал на бучки (мрамор, фелдшпат и др.) Трябва да се извърши веднага след измиване, тъй като навлажненият материал ще се "разпраши" много по-малко. В този случай материалът се изсушава преди фино смилане.
Грубо натрошаване. За грубо раздробяване се използват челюстни трошачки, които наред с високата производителност осигуряват и висока степен на раздробяване - в рамките на 5-6 (степента на раздробяване е съотношението на размера на парчето материал преди и след раздробяването). Процесът на раздробяване се свежда до раздробяване на парчета материал между бузите (оребрени плочи), едната от които извършва люлеещи се движения, осигурявайки периодично сближаване и разминаване на бузите, а втората е неподвижна (фиг. 3.15).
![]() |
Фигура 3.15 Схема на челюстна трошачка:
Размерът на парчетата материал, заредени в трошачката, зависи от нейната мощност и твърдостта на материала. Например при трошене на мрамор трошачката може да се захранва с парчета с максимално допустим размер. При раздробяване на феросплави с висока твърдост размерът на парчетата не трябва да надвишава 140-160 mm. Феросплави с висок вискозитет, като нисковъглероден ферохром или фероволфрам, трябва да бъдат натрошени след закаляване (нагряване до 850–900 °C, задържане за 30 минути, охлаждане на студеновода).
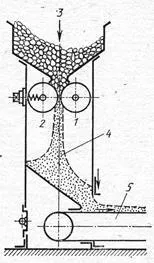
Фигура 3.16 Ролкова трошачка с гладки ролки:
Ролковите трошачки са прости по дизайн, надеждни при работа и имат висока производителност, осигурявайки коефициент на редукция 3-5. Процесът на раздробяване се свежда до раздробяване на парчета материал между гладки ролки, въртящи се един към друг.
Сушене на материали. За да се осигури необходимото съдържание на влага на компонентите, в някои случаи е необходимо те да бъдат изсушени. При смилане на мокър материал той може да се сгъсти, да залепне по облицовката на мелниците и да се натрупа в транспортните системи. Влажните материали ще запушат екраните по време на проверката и класификацията. Кримпваемостта на електродите при използване на навлажнени материали значително се влошава.
Компонентите на бучки се сушат в пещи с талига, а по-малките - в механизирани линии за сушене.
Фино смилане. В зависимост от вида на смилащата среда, използвана в оборудването за фино смилане, се разграничават топкови и прътови мелници.
В първия стоманените топки служат като смилащи тела, във втория - метални пръти. Най-разпространени са топковите мелници. При смилане на материали в прътови мелници крайният продукт съдържа по-малко фини фракции, отколкото при смилане в топкови мелници.
Обикновено топковата мелница е цилиндрична обвивка, от вътрешната страна на която през гумено уплътнение са завинтени бронирани плочи (облицовка), изработени от манганова или хромирана стомана. Понякога черупките се сглобяват и заваряват от отделни плочи, чиято работна повърхност е покрита с устойчива на износване сплав. Заза подобряване на ефективността на мелниците, облицовъчните плочи се отливат с удебелени ребра. При сглобяването на облицовката тези удебеления образуват прагове, които забавят приплъзването на топките и прътите по време на въртенето на мелниците. В момента специални гумени пръти понякога се използват като подплата. Използването на гумена облицовка не води до загуба на производителност, но намалява консумацията на топки и значително подобрява условията на работа поради намаляване на шума.
Според принципа на работа се разграничават топкови или прътови мелници:
с периодично натоварване (мелници с периодично действие);
с непрекъснато натоварване:
а) работа за преминаване;
б) с периферно разтоварване (с непрекъснато пресяване).
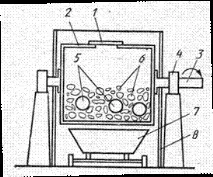
Фигура 3.17 Диаграма на партидна мелница:
Пакетните мелници не са много продуктивни. Въпреки това, те са незаменими за смилане на редица компоненти, въведени в малки количества в специални електродни покрития: ферониобий, метален хром, феромолибден и др. Тези мелници позволяват получаване на желания гранулометричен състав на натрошените компоненти, което също е от голямо значение при производството на електроди от много марки.
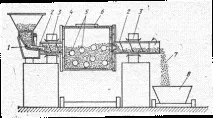
Фигура 3.18 Схема на мелница, работеща на проход:
При непрекъснато подаване на материал за повторно смилане с по-голяма пълнота се осигурява постоянството на гранулометричния състав на крайния продукт.
В конвенционална топкова или прътова мелница материалът се раздробява поради удар и абразия от смилащата среда, във вибрираща мелница - само поради абразия. Следователно, ако една топкова или прътова мелница може да бъде заредена с материал с размер на парчета до 20-30 mm, тогава вибрационната мелница може да бъде заредена само с материал не по-голям от 3-5 mm.
Мелни тела. Топки или пръти обикновено се използват като мелница. Топките могат да бъдат ковани, щамповани или валцовани от манган, хром или въглеродна стомана; прътите са стоманени. Стоманените смилащи топки за топкови мелници се доставят съгласно GOST 7524-83. Твърдостта на повърхността на топките в термично обработено състояние трябва да бъде 400-450 HB за топки с обикновена твърдост, 451-550 HB за повишена твърдост. Диаметър на топката от 50 до 100 мм, диампръти 50-120 мм.
При запълване на достатъчно голям обем с топки с еднакъв диаметър, степента на запълване ще бъде около 62%, а делът на кухините между топките ще бъде около 38%. При различни диаметри на топките степента на пълнене ще варира донякъде. Топките с голям диаметър работят предимно върху удар, малките топки - върху абразия. Оптималният набор от топки в диаметър зависи от размера на изходния материал, неговата твърдост и необходимата степен на смилане. За вибрационните мелници диаметърът на топките обикновено е 16-20 mm. На практика те се придържат към степента на пълнене на мелницата с топки на 40-45% от обема на светлина. Правилният избор на смилаща среда има решаващо влияние върху работата на мелницата.
Скоростта на въртене на мелницата зависи от нейния диаметър. Колкото по-малък е диаметърът на мелницата, толкова по-голяма трябва да бъде скоростта на нейното въртене.
Смилането на материала в топкова или прътова мелница протича по следния начин. В първия момент на въртене мелещата среда и материала за смилане се изхвърлят под действието на центробежна сила и се притискат към стените на мелницата. В следващия момент мелещите тела и материал, издигнали се на определена височина, се откъсват от стената на мелницата и падат по параболична крива. В момента на падане част от мелещите тела разбиват парчетата материал, а част, плъзгайки се по стените на мелницата, ги ожулват. В зависимост от скоростта на въртене на мелницата се променя естеството на работата на смилащата среда. При малък брой обороти мелещите тела и материалът се издигат по стената на мелницата до височина, определена от ъгъла на покой, след което започват да се търкалят; мелещите тела само изтриват материала. Ако броят на оборотите на мелницата е твърде висок, мелещите тела и материалът се притискат към стената на мелницата поради центробежна сила - няма да се получи смилане.
Особено негативно върху производителността се отразява наличието в мелницата на вече натрошен материал, който, намирайки се по протежение на стените й по време на въртенето на мелницата, създава слой, който намалява силата на удара на топките.
Не намерихте това, което търсихте? Използвайте търсачката: