Технология на производство на полимерни тръби и фитинги
Производството на всички термопластични тръби, включително металопластични, полипропиленови и армирани полипропиленови, се извършва на тръбопроводи. Основният изглед и отделните съставни елементи на такава линия са показани на фигура 1.
Фиг. 1. Принципна схема на технологична линия за производство на полимерни тръби чрез екструдиране:1 - смесител на компоненти, 2 - зареждащо устройство, 3 - екструдер, 4 - екструзионна глава, 5 - калибриращо устройство, 6 - охлаждаща баня, 7 - теглещо устройство, 8 - маркиращо устройство, 9 - навиващо устройство - барабан; използвани за производство на тръби на рулони; 10 - режещо устройство; Прилага се при освобождаване на тръби по сегменти.
Термопластичните тръби се произвеждат на специални машини - екструдери, чрез екструдиране - чрез непрекъснато екструдиране на вискозен полимер през неговата работна, изходна част - глава с пръстеновиден прорез, който директно образува тръба.
Пълната технологична схема за производство на металополимерни тръби и последователността на операциите изглеждат така:
- 1 - приемане на суровини - полиетиленови гранули, алуминиева лента, лепилен състав и др., съхранение на суровини,
- 2 - дозиране и смесване на компонентите,
- 3 - екструдиране на полиетиленовия вътрешен слой на тръбата (5-ти слой на фиг. 2),
- 4а - екструдиране на адхезивния състав (4-ти слой) върху външната повърхност на произведената полиетиленова тръба,
- 5 - формоване на плоска алуминиева лента в цилиндрична обвивка (3-ти слой), плътно покриваща предишните 2 слоя без припокриване (други производители формоват обвивката сприпокриване - припокриване - лента),
- 6 - надлъжно (по протежение на генератора) челно заваряване на ръбовете на алуминиевата обвивка,
- 7 - контрол на качеството на заваръчния шев,
- 8 - индукционно нагряване на получения продукт,
- 4b - екструдиране на адхезивния състав (2-ри слой) върху външната повърхност на алуминиевата обвивка,
- 9 - екструдиране на полиетиленовия външен (1-ви) слой на тръбата,
- 10 - охлаждане на готовия продукт и маркиране на тръбата,
- 11 - рязане на тръбата на измерени сегменти, или - 12,
- 12 - навиване на тръбата в рулони,
- 13 - контрол на херметичността,
- 14 - тръбна опаковка,
- 15 - складиране на готовата продукция.
Работното тяло на екструдера, фиг. 3, е въртящ се червяк (шнек), обикновено с постепенно намаляващ диаметър на шнековия канал към изхода. Суровината под формата на гранули се улавя от шнека и се движи в междината между вътрешната стена на корпуса на екструдера и шнековия канал, тя се компресира (налягането достига 15–50 MPa), нагрява се, пластифицира се и се хомогенизира. Топлината, необходима за нагряване и пластифициране, се доставя от електрически нагреватели, монтирани на тялото на екструдера, а също така се освобождава поради интензивната деформация на полимера и неговото триене по стените на тялото и шнека.
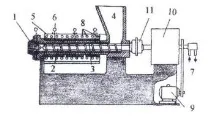
Фиг. 3. Схема на шнеков екструдер:1 - екструдираща глава, 2 - шнеков вал, шнек, 3 - винтова втулка, 4 - бункер, 5 - електрически нагреватели, 6 - термодвойки за контрол на температурата, 7 - подаване и изпускане на циркулираща охлаждаща вода, 8 - канали за водно охлаждане, 9 - електродвигател, 10 - редуктор, 11 - еластичен съединител.
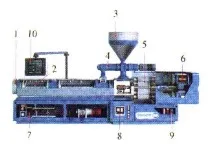
Фиг. 4. Външният вид на модерен екструдер:1 - екструзионна глава, 2 - двоен винтов вал, 3 - бункер, 4 -дозатор, 5 - система за превключване на предавките, 6 - асинхронен електродвигател, 7 - резервоар за водно охлаждане, 8 - термичен блок за управление на зоните за нагряване на стопилката по дължината на червячния вал, 9 - помпа на системата за смазване, 10 - контролен панел.
Екструзионните глави са конструктивно проектирани в многобройни варианти на приемане на влезлите в тях компоненти и излизане от стопилката на полимерната композитна маса, в която може да се изработи тръба от хомогенен материал, също и тръба от два (три) материала, отличаващи се например по цвят или свойства, технологичният процес, при който два или повече компонента на полимерната маса се екструдират едновременно, се нарича коекструзия (коекструзия) и един от възможните схеми на такъв процес са показани на фиг. 4.
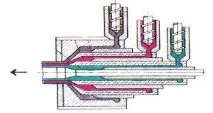
Фиг. Фиг. 4. Схематична диаграма на процеса на коекструзия при производството на трицветна тръба (подаване на стопилката към пръстеновидния процеп на главата чрез три винта)
Стоилката може да се подава от матрицата за екструдиране в надлъжна или напречна посока спрямо оста на произвежданата тръба. В първия случай материалът се оформя директно в тръбата чрез излизане от полимерната маса през пръстеновидния процеп. Във втория случай материалът се екструдира и нанася върху друго, вече готово изделие, преминавайки през главата на екструдера. Ролята на вътрешната стена на произведената тръба в този случай се изпълнява от външната стена на предварително изработената тръба.
Устройството за калибриранедейства като първоначално охлаждане на оформената тръба. Калибрирането - осигуряване на точните размери на продукта в рамките на толеранс - се извършва според вътрешния или външния диаметър на тръбата, в зависимост от изискванията към продукта.
Тъй като температурата на получения продукт на изхода на екструдераглавата е доста висока, близка до температурата на стопилка: за полиетилен с висока плътност при 170-280 ° C, а за пропилен при 204-218 ° C, след което след екструдера се монтира охлаждащо устройство. Той е предназначен да охлажда готовата тръба и да й придава твърдост и е направен под формата на удължена отворена или затворена течаща вода вана, разделена на няколко независими отделения. Тръбата във ваната е под нивото на водата, така че уплътняването на отделенията, когато тръбата влиза и излиза от ваната, се постига чрез монтиране на гумени маншети, кръглият отвор в които е малко по-малък от диаметъра на полимерната тръба.
Издърпването на тръбата от екструдера и по-нататъшното й движение по производствената линия се извършва от издърпващо устройство тип гъсеница.
Маркиращо устройство, извършва прилагането на необходимите данни върху външната повърхност на тръбата. Ако по-рано маркирането на тръбите се извършваше механично - чрез горещо щамповане с маркировъчен печат, вдлъбнат в тялото на тръбата с 0,1-0,2 mm, сега на съвременния етап на техническия прогрес тази операция се извършва от компютър, който изпраща команди към устройство за пръскане на боя (например под формата на мастилено-струен принтер), който прилага циклично повтаряща се информационна информация върху външната повърхност на тръбата.
Режещото устройство, настроено на конкретна, предварително определена дължина на рязане, се задейства автоматично от краен превключвател. Тъй като тръбата е в постоянно транслационно движение по време на нейното формиране, режещото устройство също се движи със скоростта на тръбата по време на рязане.
Уплътняването на бобината по време на производствения процес се постига чрез механично прищипване (сплескване) на напречното сечение на тръбата. Според тази скоба тръбата се нарязва с ножица. единия крайна изрязания херметичен участък е краят на необходимата дължина на намотката (определена от маркировката на ходовите метри), навит върху барабана, а другият край на изрязания участък, също запечатан, служи като начало на нова намотка, навита на втория - свободен барабан на линията.
Процесът на получаване на полипропиленова тръба чрез екструзия се извършва на един етап, за разлика от екструдирането на металопластична тръба, няма операции за нанасяне на адхезивни слоеве и създаване на алуминиева обвивка.
Предимството на екструзионния метод на производство е, че осигурява непрекъснатост и стабилност на процеса, точност на размерите и високо качество на продукта, висока производителност, лекота на управление и автоматизация на процеса.
Благодарение на еластичността на полимера и малката дебелина на стените, произведените тръби са гъвкави и това дава възможност, освобождавайки ги в неограничена дължина, да се навиват на рулони, а не да се нарязват на парчета от 4-6 m.
Процесът на получаване на подсилени полипропиленови тръби чрез екструзия се допълва от включването на допълнително технологично оборудване в тръбопровода.
Технологичният режим на екструдиране на тръбите и съответно качеството на тръбата зависи от много фактори: химичния състав на суровината с набор от добавки, техническото съвършенство на съставните елементи на технологичното оборудване, най-новите постижения в технологията за обработка на пластмаси на ниво ноу-хау ("ноу-хау", буквално преведено от английски - "знам как").
Като се има предвид технологията за производство на термопластични тръби, е необходимо да се спрем на самия материал на тръбата. Това е състав, който в допълнение към основния материал: полиетилен или полипропилен включва различни добавки: пълнители, пластификатори,стабилизатори, омекотители (лубриканти), пигменти и багрила, агенти против стареене, втвърдяващи добавки. Всеки от тези компоненти придава определени свойства на полимерната маса и заедно се получава съставен технологичен клас, продуктите от който имат определени технически характеристики. При наличие на пазарна конкуренция марката, получена от разработчика-технолог за набор от компоненти, не се разкрива, това е ноу-хау на компанията.
В случай на пластмаси, използвани за битови и хранителни цели, суровините не трябва да имат вредно въздействие върху живия организъм и затова се тестват за съответствие с техните хигиенни изисквания.
Суровината на полимера се произвежда и доставя под формата на гранули - сферични, цилиндрични, лещовидни или други закръглени "зърна" с малък размер, с максимален диаметър около 3 mm, или под формата на суспензионни прахове.
Отделно ще покажем предназначението на добавките.
Пълнителитеса полимерно неутрални вещества от органичен или неутрален произход, добавени за запазване на самия полимер и в същото време му придават ценни експлоатационни свойства: механична якост, устойчивост на топлина и др. Като пълнители се използват памучни и азбестови тъкани, фибростъкло, синтетични влакна и стъклени влакна; под формата на прахове: титанов диоксид, железни и силициеви оксиди, калциев карбонат, азбест, графит, сажди, талк, слюда, каолин, дървесно брашно и др. Пълнежът може да достигне 60%, а количеството на оригиналния полимер е 40%. С въвеждането на разпенващи агенти в състава на полимерния състав се получават напълнени с газ пенопластмаси - пенопластмаси.
Пластификатори- вещества, които намаляват температурата на преход на полимера в течностпластично състояние и при нагряване намаляват вискозитета на полимера, като по този начин увеличават подвижността на макромолекулите и улесняват преработката на полимера в продукти. Увеличаването на количеството пластификатор намалява якостта на опън и натиск на полимера, но в същото време якостта на удар и якостта на опън се увеличават драстично. Като пластификатори се използват течни маслени вещества: фталати, алкил- и арилфосфати и др. Когато се въведе голямо количество пластификатор, до 30-50%, полимерът се нарича пластифициран.
Стабилизатори- вещества, които забавят стареенето на полимерите, правят ги по-малко чувствителни към слънчева светлина (светлинни стабилизатори), кислород, топлина и позволяват да се удължи експлоатационният живот.
Омекотители(лубриканти) са предназначени да намалят триенето както между полимерния състав и металните формовани повърхности на обработващото оборудване, така и да намалят вътрешното триене в самата полимерна маса. Въвежда се в състава, за да се улесни изтласкването на полимерната стопилка през формовъчната дюза. Примери за лубриканти: парафин, восък, мастни киселини, алкохол, стеарин, соли на стеаринова киселина.
Багрилата и пигментитепридават на полимера желания цвят на продукта, който, докосвайки се до тръбите, отличава продуктите от различни производители, които имат само един присъщ, регистриран корпоративен цвят на продуктите, и в същото време дава възможност да се оцени предназначението на тръбата - захранване със студена, топла вода, отопление и наличието на визуален контрол за правилното използване на тръбата за дадена санитарна система. Примери за багрила: титанов диоксид, железни оксиди, алуминиев прах (придава на продукта перлен метален блясък), пигменти - алено, оранжево, синьо, зелено, кафяво идруги
Антиоксиданти (агенти против стареене)- удължават живота на лулата. Втвърдяващите агенти насърчават прехода на полимера към незатопимо, втвърдено състояние. Същността на втвърдяването се крие в омрежването на молекулните вериги. Полиамините се използват като втвърдители.
Нейните отговорности включват следните периодични изпитвания на опитни образци директно от технологичния процес, извършвани в сроковете, определени от Методиката или Инструкцията за изпитване:
гравиметричен:
- претегляне на електронни везни на стандартна проба от тръба за определяне на нейната маса и съответствие с нейния стандарт
- определяне на дебелината на стената на тръбата с микрометър
- разкъсване на проба от пръстеновидна тръба, за да се определи качеството на заварения шев на алуминиевата обвивка
- определяне на налягането на разрушаване на проба от тръба
- тестване на серия проби от тръби за издръжливост чрез симулиране на ускорена работа на проби, поставени в гореща баня и под работно хидростатично налягане
Изходен материал за производството на фитингите са: месинг за MP тръби и полипропилен за PP и PP армирани тръби.
Месинговите свързващи части се произвеждат на високопроизводителни машини за горещ печат с последваща механична обработка.
Полипропиленовите свързващи части, включително и тези, комбинирани с вградени месингови вложки, се произвеждат на машини за леене под налягане чрез леене под налягане.