Технология на ремонт на топлообменници
В процеса на продължителна експлоатация настъпва ерозионно и корозивно износване на тръбите и стените на корпуса: топлообменните повърхности се замърсяват и ефективността на топлообмена намалява. Типичните дефекти са намаляване на дебелината на стената на тръбата, дъното, тялото, фистули в заваръчни шевове, увреждане на уплътнителните повърхности, пукнатини в частите на тялото и тръбите, вдлъбнатини, течове и празнини при валцоване на тръби в тръбни листове, увеличаване на диаметъра на отворите в тръбните листове, питинг, междукристална и други видове корозия, повреда на опори, резби на крепежни елементи, влага или повреда на топлоизолацията.
Структурата на цикъла на ремонт на оборудването е различна и зависи от характера на производството, вида на апарата и хладилния агрегат като цяло. Цялото топлообменно оборудване на хладилните инсталации се експлоатира с рутинна проверка на всеки три месеца, годишна поддръжка, среден ремонт (след 3 години) и основен ремонт след 12 години. В някои случаи те се ограничават до два вида ремонт - текущ и капитален.
По време на превантивните проверки те проверяват затягането на фланцовите връзки, отстраняват течовете, затягат или прекъсват уплътненията на клапаните, проверяват управляващите устройства, предпазните устройства, проверяват напрежението на задвижващите ремъци в устройства с бъркалки и вентилатори и почистват улуците в напоителните кондензатори.
По време на текущия ремонт се извършва допълнително количество работа: частичен демонтаж и демонтаж на спирателни вентили, прекъсване на всички уплътнения, подмяна на уплътнения, проверка на херметичността на клапаните, ремонт на предпазни и възвратни клапани, в кондензатори за напояване - демонтаж и почистване на щитове и тръби на калниците, почистване и настройкаводоразпределителни устройства
По време на основен ремонт, в допълнение към обема на средния ремонт, се извършват работи по подмяна на всички предварително запушени тръби (ако са запушени повече от 15% от тръбите), замяна на тръби и участъци, които имат течове, замяна на тръби с износване над 25% от дебелината на стената, ремонт и подмяна на спирателни кранове, преглед на съдове от инспектор на Госгортехнадзор на СССР.
Почистване на топлообменници.
Доброто почистване на топлообменната повърхност не само увеличава топлообмена, но и удължава експлоатационния живот на апарата. Почистването се извършва чрез химически, механични, хидравлични ултразвукови или смесени методи.
За почистване на тръбите на топлообменника се използват методи за механично почистване. Устройството за почистване се състои от въртящ се прът с режещ инструмент в края. Прътът заедно със задвижването (електрическа бормашина или пневматичен двигател) е прикрепен към количката, движеща се по монорелсата, докато прътът се движи по топлообменната тръба. Въртящият се прът е затворен в тръба, която предпазва ръцете на работниците и в същото време служи като тръбопровод за подаване на вода за промиване на отлаганията. Инструментът се движи хоризонтално на ръка. За почистване на U-образните тръби на топлообменниците и тръбите с малък диаметър се използват гъвкави валове, задвижвани от различни видове двигатели.
Инструментът, използван за механично почистване, е разнообразен: свредла, ръфове, фрези, свредла, фрези.
При пясъкоструене пясъкът се подава заедно с вода в машината за почистване (мокро пясъкоструене). Ако пясъкът се подава във водата със струя въздух, тогава в този случай почистването се извършва със смес от вода, въздух и пясък.
По време на хидропневматично почистване водата под налягане се подава в тръбата с помощта на водно-въздушен пистолет.0,5-0,6 МРа и въздух под налягане 0,7-0,8 МРа в съотношение 1:1. Сгъстеният въздух, разширявайки се, рязко увеличава скоростта на движение на водата, която започва да се движи в удари с интензивна турбулентност, което допринася за разрушаването на отлаганията.
Време за почистване
По време на хидромеханично почистване водата под налягане до 70 MPa се изпомпва през гъвкав маркуч с високо налягане в куха пръчка, в края на която е фиксирана дюза с отвори, разположена в повечето случаи под ъгъл 45 спрямо оста на пръта. Този метод изисква определени предпазни мерки, но позволява почистването да се извърши бързо и без ерозионно износване.
При подаване на вода към куха пръчка, в случай че върхът е направен от карбидна резачка или свредло, е възможно да се почистят тръби със солидно запушване. Налягането на водата в този случай не надвишава 1,0 MPa.
Най-простият и надежден метод за предотвратяване на отлаганията по стените на тръбите е ултразвукът. Неговата същност се състои в това, че скоростите на разпространение на вълните в метала и в отлаганията се различават значително и когато се появи деформация в граничната зона, тънък слой от отлагания непрекъснато се разрушава.
По време на техническото преоборудване на промишлени инсталации, в случаите, когато в циркулационните цикли на водно охлаждане не са предвидени ефективни устройства за пречистване на вода от утайки, препоръчително е да се използват псевдокипящи кондензатори (самопочистващ се кондензатор). По време на работа, под въздействието на пясъчни частици, повърхността на тръбите се почиства от тиня и котлен камък. Недостатъкът на този ефективен кондензатор е корозионно-ерозионното износване на стените на кондензатора и необходимостта от производство на тръби поради тази причина само от легирана стомана.
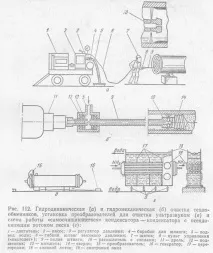
Редът на ремонтните операции след подготовкатана апарата, изключен от веригата и въвеждането му за ремонт, следното: демонтаж на арматура и тръбопроводи, демонтаж на резбови съединения, отстраняване на капаци, люкове, изкопаване на тръбни листове, ако конструкцията на апарата позволява, проверка на плътността и здравината на тръбите и тяхното закрепване в тръбни листове чрез пневматични или хидравлични тестове, заклинване и разширяване (заваряване) на тръби в тръба листове, отстраняване на тръби от корпуса при подмяната им, настройка на нови тръби с предварително почистване на отвори в решетките и зад почистване на краищата на тръбите, ремонт на частите на тялото, щанцоване и изрязване на уплътнения, подготовка на крепежни елементи, монтаж на апарата, изпитване на плътност и якост, пускане в експлоатация.
Ремонтът на топлообменниците започва с проверка на тяхната плътност. Течовете в топлообменниците се откриват, когато се тестват с водно налягане (изпитване под налягане). При изпитване на апарат с една част от корпус и тръба се подава вода към пръстеновидното пространство и чрез повишаване на налягането до изпитвателното налягане апаратът се проверява за липса на течове в тръбния лист и от кухината на тръбите. В случай на затруднено отстраняване на водата от апарата, течовете в хладилните топлообменници се определят чрез налягането на сух въздух или азот (пневматично изпитване под налягане) със сапунен тест или детектори за течове. Идентифицираните тръби с течове могат да бъдат запушени с временни тапи, за да продължи тестването.
При ремонт на топлообменници, както е посочено по-горе, е разрешено задръстването на не повече от 15% от тръбите. Редактирането на смачкани тръби се извършва върху винтови приспособления чрез плъзгане на щепсел-дорник върху прът. Тръбите са задръстени от двете страни с тапи на резбата или на спойката.
При смяна на валцованите тръби те се изрязват зад тръбната ламарина със специален нож или се разширяват, за да се намали дебелината на стената и последващото изкопаване.Всички тези операции се извършват така, че да не се повреди повърхността на дупките в решетката. Разширяването се извършва със стъпаловидно свредло с центриращ гладък край, равен на вътрешния диаметър на тръбата и режеща част, равна на 3 D от външния диаметър на тръбите. Намаляването на дебелината на тръбите рязко намалява напрежението в валцованото съединение и тръбата може лесно да се отстрани. За да не изпусне тръбата в пръстеновидното пространство, в нея се вкарва метален прът от друг тръбен лист или се използват устройства.
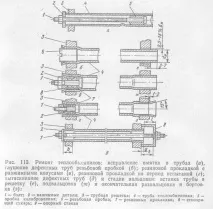
Тръбите, фиксирани в тръбния лист чрез заваряване, се отстраняват от апарата чрез ръчно пробиване на пръстеновидния шев или отрязване на края на тръбата и валковия шев с нож, задвижван от гъвкав вал. Преди да смените избитите дефектни тръби с нови, отворите в тръбните листове се почистват, продухват и избърсват. Надлъжните рискове по повърхностите на дупките се почистват със скрепер. Грапавостта на повърхността в отворите за валцуване не трябва да бъде по-ниска от R„ 0,80 µm.
Краищата на тръбите се почистват, избърсват, тръбите се вкарват в тръбния лист, пролуките се продухват с въздух. Стойността на хлабината не трябва да бъде по-малка от 0,5 и повече от 1,5% от диаметъра на тръбата. При малки междини е трудно да се вкарат тръби в тръбната плоча, а при големи има опасност от загуба на здравина на тръбата и херметичност на съединението. Развалването започва с навиване - разпределяне на края на тръбата, за да се фиксира в отвора. Валцуването се извършва чрез валцуване с дължина на ролките 10-12 mm над дебелината на тръбния лист. След prn-валцоване на всички тръби се извършва окончателно развалцоване със скорост 15-20% от дебелината на стената на тръбата, която се валцува, а краищата на тръбите се нагъват под ъгъл от 15 ° спрямо оста на тръбата. Валцоването се извършва чрез закрепващо валцоване, окончателно валцоване и фланцоване - чрез странично валцуване (със странични ролки).
Първоразгънете всички тръби в една мрежа, а след това в друга. При голям брой тръби, които трябва да бъдат сменени, процедурата за валцуване е следната. Първо четири тръби се навиват напречно, а след това всички тръби около периметъра, след което всички останали.
Качеството на работа се проверява чрез проверка за липса на пукнатини и счупвания, рязане на тръба по ръба на гнездото и също така се уверете, че няма ясно изразен преход между валцуваната и невалцуваната част.
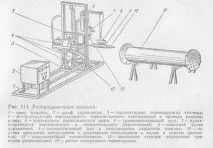
При ремонт на топлообменници могат да се използват устройства, работещи в полуавтоматичен режим. Пример е машина за развалцоване (фиг. 114), която може да се използва с подходяща смяна на инструмента за развалцоване, подрязване и отстраняване на тръби от топлообменник, както и за рязане на пръстеновидни жлебове в отворите на тръбни листове на топлообменници с тръби с диаметър от 14 до 57 mm. Автомобилът работи в ръчен, автоматичен и полуавтоматичен режим. На рамата на машината има количка 3, която се придвижва в хоризонтална посока с помощта на верижно задвижване. Върху него е монтирана вертикална рамка, по която се движи хоризонтално разположена рамка със задвижване за разваляне. Рамката със задвижването се движи вертикално също с помощта на верижно задвижване, а в напречна посока - с помощта на лост.
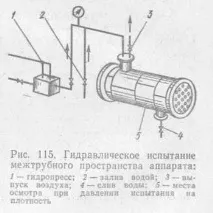
Задвижванията на вертикални и хоризонтални движения се управляват от координационния панел, а управлението и изборът на режим на работа на развалцовото задвижване се извършва от дистанционно управление, разположено върху защитния корпус на телескопичния вал. Разширяването на тръбите в отворите на тръбните листове се извършва с инструмент, фиксиран в главата, свързана с вала. При подрязване, подрязване и изрязване на канали в решетката, управление на мотор-редуктора от бутонастанции.
Фистули и пукнатини в частите на тялото и черупките са заварени. След всички работи по заваряване на части на корпуса, съдовете, които са под контрола на Госгортехнадзор на СССР, се подлагат на тест за хидравлична якост. Кримпването на кожухотръбни апарати с твърда конструкция се извършва с отстранени капаци и с проверка на качеството на валцуване в решетките. По време на пълненето на апарата с вода преди тестването е необходимо да се осигури, за всеки дизайн, освобождаването на въздух от тестовата кухина.