Защита на метала чрез закаляване - Детска енциклопедия (първо издание)
Можете да защитите повърхността на метала по друг начин - втвърдете тънкия външен слой, оставяйки сърцевината по-мека. Тогава детайлът ще понася добре натоварвания - няма да е крехък, а твърд закален слой ще го предпази от износване. Но за да се втвърди от повърхността, е необходимо да се предотврати проникването на топлина дълбоко в дебелината на метала.
Повърхността често се нагрява с пламък. Частта се върти около горелката, която се движи по протежение на частта; в същото време металът няма време да се загрее. След това се охлажда с вода. Слой от няколко милиметра след нагряване и охлаждане става твърд.
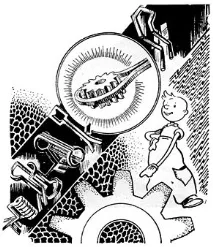
Закаляване на детайли с високочестотни токове
Широко се използва и друг метод за закаляване - с помощта на високочестотни токове. Ако поставите метална част в променливо магнитно поле, тогава в нея ще се появи ток, който ще се разпространи само върху повърхността и ще я нагрее. След няколко секунди повърхностният слой ще се нагрее и ще се втвърди след охлаждане.
Устройството за закаляване има индуктор - едно или повече навивки от медна тръба. През него преминава високочестотен ток, който възбужда променливо магнитно поле. Вътре в индуктора и поставете детайла. Чрез промяна на честотата на тока е възможно да се промени дебелината на втвърдения слой от части от милиметър до сантиметър. Индукторите с различни форми ви позволяват да втвърдявате голямо разнообразие от продукти - плоски, цилиндрични и др.
Високочестотните токове закаляват много части - от шевни игли, малки свредла и винтове до големи колянови валове и оси. Възможно е да се закалява не цялата част, а само отделните й части - зъби на зъбни колела, шийки на валове, краища на релси. Закаляването на релсите увеличава експлоатационния им живот, което спестява милиони тонове метал. Повърхностното закаляване на коляновите валове на трактора увеличава тяхнатапочти удвоена устойчивост на износване.
Има автоматични машини за закаляване например за закаляване на шийките на коляновия вал на автомобилни двигатели. Машината може да темперира 350 000 шевни игли на ден. Иглата по време на падането вътре в индуктора има време да се нагрее и веднага влиза в охлаждащото масло. Целият процес отнема 0,03 сек.
Високочестотните токове, освен за повърхностно закаляване, се използват и за закаляване на детайлите по друг начин. По време на работа на машината в нейните части възникват напрежения. Те са разпределени неравномерно: докато отделните слоеве метал са претоварени, други, напротив, не изпитват почти никакви усилия. Следователно частта се поврежда по-бързо, претоварените зони се износват повече. Чрез нагряване на частта на някои места е възможно изкуствено да се предизвикат напрежения в нея, противоположни на тези, които възникват в работните части на метала. Като се сумират, двете напрежения водят до намаляване на общата сила, действаща върху детайла.
Електричеството помага за втвърдяването на метала и по друг начин - чрез електроискрова обработка. Частта е включена във веригата и служи като електрод. Между него и друг електрод, когато се доближат, възниква електрически разряд. В този случай най-малките частици метал се прехвърлят от електродния инструмент към електродната част и повърхността на частта постепенно се покрива с най-тънкия слой метал. По този начин е възможно повърхностният слой да се насити с въглерод, ако електродът е направен от графит. Електрическа искра може да се използва и за нанасяне на покрития от твърди сплави.
КОЛКО ЖИВЕЕ ЖЕЛЯЗОТО?
Странен въпрос: все пак желязото е неодушевено, как можем да говорим за продължителността на живота му? Оказва се, че можете! Самото желязо не "умира". Но железните части на машините, стоманените инструменти, стоманените строителни конструкции, релсите рано или късно излизат от строя. Те трябва дазамени с нови. Оказа се, че в момента средният живот на изделията от желязо е 35 години. И това се счита за огромно постижение на металурзите, тъй като през миналите векове желязото е „умряло“ много по-бързо. През последните години машинните части се изработват от титан. Проучванията показват, че титанът е много по-издръжлив от желязото: той "живее" сто или повече години.
Износоустойчивостта на триещите се повърхности след електроискрово закаляване се увеличава десетократно. Това е така, защото металът от повърхността е наситен с частици от твърди съединения, а високата температура на изпускане (до 10 000 °) осигурява бързо втвърдяване. Твърдостта на закаления слой е три пъти по-голяма от тази на най-добрата стомана.
Износените части се заваряват с метал, който образува солиден защитен слой върху него. За да направите това, използвайте електрическа дъга, която възниква между частта и жичния електрод. Частиците от разтопена тел се заваряват към детайла, покривайки го със слой метал.
Не само металът може да служи като защитно покритие. Частите, които трябва да издържат на високи температури, са покрити с керамика, съдържаща оксиди на алуминий, титан, магнезий, хром, цирконий и други метали. Това предпазва частите на реактивния двигател, турбинните лопатки, нагревателите на електрическите пещи и тръбопроводите от изгаряне. Керамиката се нанася предимно чрез шприцване. Получава се много твърд тънък слой, устойчив на всякакви химически влияния, който е здраво свързан с метала.
Металът често трябва да бъде защитен от корозия и ръжда, особено когато работи във влажен въздух, във вода и влиза в контакт с вредни газове и течности. Ръждата, поради която металът умира, причинява големи щети. Смята се, че всяка годинаотнася една трета от всички разтопени метали и сплави. Следователно металът се търси да бъде защитен от директен контакт с влага и въздух. Всеки знае за никелирани, калайдисани, емайлирани съдове, покриви от поцинкована ламарина, лакове и бои, които покриват метални изделия.
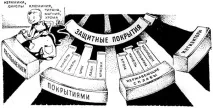
Методи за защита на метала от корозия
Често върху метала се нанася защитен оксиден филм. Тогава тънък слой от вече окислен метал предпазва от по-нататъшно разрушаване. Случва се металът да е защитен от друг метал - калай, цинк, никел, хром, алуминий. Що се отнася до алуминия, той се защитава сам: на повърхността му във въздуха се образува тънък, издръжлив слой от оксиди.
Сплавите се правят неръждаеми, като към тях се добавят различни елементи, които са добре устойчиви на ръжда. Например, ако добавите малко хром, никел, волфрам, молибден към стоманата, тогава тя става не само издръжлива, но и не ръждясва.
Сега те използват друго средство за защита - в случаите, когато е необходимо, например, да съхранявате части за дълго време в склад. Химиците са открили съединения, които предпазват метала от ръжда - инхибитори. В хартия, импрегнирана с такъв състав, продуктите могат да се съхраняват без страх от повреда.
Сега е трудно да си представим какво би се случило, ако не можем да укрепим метала, да го защитим от външни влияния. Ще бъдат загубени милиони тонове метал. Би било невъзможно да се създадат редица съвременни машини - от реактивен самолет до комбайн за въглища, от ракета, която носи спътник на Земята в орбита или лети до Луната, до автомобил. Металът трябва не само да бъде получен, обработен, но и направен издръжлив, за да се удължи животът на машините.