Завод на VW в Калуга - Локализация на производството - Магазин за авточасти Autopilot Tula
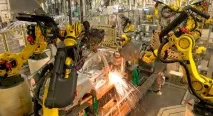
Когато преди пет години започна производството на седана Polo в завода на Volkswagen край Калуга, степента на локализация на производството му беше около 30 процента, а сред доставчиците имаше 29 български предприятия. Сега вече има 60 такива компании, но германците не посочват текущата степен на локализация на Polo - само общата за завода: 45%. Това е предвид факта, че Volkswagen Touareg и Multivan, Audi A6 и A8 се сглобяват в Гръбцево по SKD метода „отвертка“. Според пълния цикъл, със заваряване и боядисване на каросерията, в допълнение към Polo, тук се произвеждат само лифтове Skoda Rapid и кросоувъри Volkswagen Tiguan. Освен това, ако германците, в рамките на споразумението за промишлено сглобяване, до 2017 г. не доведат нивото на локализация до шестдесет процента, те могат да загубят митнически привилегии за внос на вносни автокомпоненти.
![]() | ![]() | ![]() | ![]() |
Първо, електро-поцинкованият покривен лист се залепва към каросерията с лепило и след това колата се изпраща в затворена кутия за лазерно запояване | Това е референтен образец на новата бежова вътрешна пластмаса | Както външните части, така и вътрешните елементи се проверяват в климатични камери: най-ниската температура е минус 40 ° C, а максималната разлика е повече от 100 ° C | Тестват се облицовки на предните калници (доставени от Индия) с надпис "Polo". Реагентите "разкриват" хромовото покритие - и можете да изучавате структурата му. Първо върху пластмасовата основа се нанася слой мед, след това никел и едва след това - хром |
За да запази качеството на местните компоненти на вътрешнокорпоративно ниво, Volkswagen основа преди пет години собствена лаборатория в завода в Гръбцево.От последното ни посещение в него са инвестирани около два милиона евро - тук все още работят девет души, а в завода на ГАЗ в Нижни Новгород, където се сглобява Jetta, има отделен филиал с четирима служители. Много работа: за да се качи на конвейера, материалът или частта трябва да отговарят на всички стандарти. Например, за производството на едно Polo са необходими 68 кг различни пластмаси, но засега само 13 кг са с български произход - и се използват само за производството на скрити части. И всички интериорни пластмаси се произвеждат от вносни гранули - например пластмасовите интериорни елементи за Polo се доставят от френската компания Reydel, която е в съседство с завода. Броните също са отляти от вносна пластмаса досега - това се прави от клона на Magna в Калуга.
Най-обширната локализация беше постигната в каросерията: ако в зората на живота на конвейера Polo почти изцяло се състоеше от вносна стомана (например концерна ArcelorMittal), сега се използва само местна стомана. Валцуваният метал се доставя от три най-големи металургични завода: Magnitogorsk, Novolipetsk и Cherepovets Severstal. Частите се щамповат тук, в съвместното испано-българско дружество Гестамп-Северсталь-Калуга.
Точно преди актуализацията, Polo локализира най-важните галванизирани стоманени части, които са свързани чрез лазерно запояване: покрив, странични стени и капак на багажника. Факт е, че обикновените стоманени елементи, поцинковани чрез потапяне в горещ разтвор, не могат да бъдат съединени с помощта на лазер: неравен слой цинк кипи и нарушава процеса. А при електропоцинковане защитният слой е по-равномерен и с по-високо качество, което позволява използването на лазерно запояване. Но за нанасяне на цинково покритие чрез електролиза в промишленосттамащаб в България може да го направи само едно предприятие - Лъсвенският металургичен комбинат, разположен в Пермския край.
Отне повече от година лабораторни проверки и одобрения, преди електро-поцинкованата стомана Lysva да стигне до конвейера. Интересен факт: в техническите изисквания Volkswagen предписва минималната допустима дебелина на цинковия слой (5-7,5 микрона). И ако опитни европейски доставчици приспособяват своите продукти точно към това изискване (няма нужда да губите скъп цинк), тогава заводът в Лисва често произвежда слой цинк с марж - за да сте сигурни. Но до началото на серийното производство електропоцинкованите части на българския завод се оказаха не по-лоши от европейските си колеги.
Въпреки това Tiguan и Jetta все още се произвеждат предимно от вносна стомана. Между другото, друга лаборатория на Volkswagen скоро ще започне да работи в Калуга, при производството на двигатели EA211, инвестициите в нея ще възлизат на около 1,7 милиона евро.
![]() | ![]() |
За да се изследва структурата на частите, те се изливат със специална смола и след втвърдяване "шайбата" се смила до желания размер, приближавайки се до даденото сечение - така е тествана електропоцинкованата стомана Lysva |