7.5. Вибродъгово наваряване на детайли
Вибродъговото напластяване се различава от разгледаните по-рано методи за напластяване по това, че по време на възстановяването на детайла краят на електродната жица осцилира в равнина, перпендикулярна на нанасяната повърхност, а също и по това, че наслоеният метален слой се охлажда принудително.
Процесът се осъществява чрез нестабилна дъга (дъга с тлеещ разряд) в комбинация с периодично повтарящо се късо съединение на електрическата заваръчна верига. Това спомага за смекчаване на топлинния режим на настилка. Прехвърлянето на метал в режим на късо съединение улеснява образуването на отложени перли. Вибродъговата наварка се извършва върху инсталацията със стоманена тел (фиг. 7.14), която се подава през мундщука 9, докато влезе в контакт с повърхността на част 1. Към частта и телта се подава заваръчен ток с ниско напрежение. В момента на контакт на електрод10с т.1 по проводника протича ток на късо съединение. Това допринася за топенето на повърхността на детайла в точката на контакт и краят на електрода бързо се нагрява до температурата на топене. В резултат на такова взаимодействие се постига структурна връзка между детайла и отложения метал. Поради осцилаторното движение на мундщука9, краят на електрода 10 се отдалечава от повърхността на детайла 1 за кратко време и при прекъсване на заваръчната електрическа верига възниква искров разряд с преход към етапа на тлеещ разряд, който продължава до момента на следващия контакт на края на електрода с повърхността на детайла.
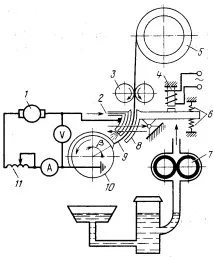
Фиг. 7.14.Схема на монтаж за вибродъгова наварка:
1 - източник на заваръчен ток;2—фитинг за подаване на охлаждаща течност;3—захранващо устройство за електродна тел;4—електрически вибратор; 5 - касета селектроден проводник;6- балансиращи пружини;7 -помпа за охлаждаща течност;8 -мундщук;9 -електрод;10 -заварена част; 11 - дросел
Полезността на електрода, изпълняващ този осцилационен цикъл, е, че когато заваръчната верига е късо, основното количество топлина практически се натрупва в изпъкналостта на електрода и малък микрообем от повърхностния слой на детайла. В този случай температурата на течната баня достига 1450 - 1500 ° C, т.е. не надвишава температурата на топене на метала. Това не само омекотява термичния режим на наваряване, но също така предотвратява възможността за изгаряне и изпаряване на химическите компоненти на метала. Етапът на тлеещ разряд, когато краят на електрода се отстранява от повърхността на детайла, се използва за предварително загряване на повърхността на детайла преди отлагането на следващата порция метал. За разлика от стабилната дъга, чиято температура е около 6000 ° C в средната част, дъгата на етапа на тлеещ разряд има температура под 4000 ° C, което също е фактор, смекчаващ термичния режим на наваряване. В допълнение, азотната молекула, съдържаща се във въздуха, не се дисоциира при тази температура и следователно азотът остава химически неутрален по отношение на желязото. Това допринася за факта, че процесът на автоматично вибродъгово наваряване на детайли може да осигури достатъчно добро качество на наваряване без използване на защитни средства (флюс, газ и др.).
В някои случаи охлаждаща течност (2,5 - 6% воден разтвор на калцинирана сода или 20% воден разтвор на глицерин) се подава към зоната на настилка. Получената водна пара допълнително предпазва разтопения метал от излагане на атмосферен азот, което допринася за производството на топчета с по-високи механични свойства.
Учени от Института по електрозаваряване. EO Paton от Академията на науките на Украйна разработи метод за вибродъгова наварка под слой от поток, който успешно се използва за наваряване на тънкостенни продукти с голям диаметър. Използването на флюс осигурява забавено охлаждане на метала и предотвратява образуването на пукнатини. Много ефективна защитна среда в процеса на автоматично вибродъгово наваряване е въглеродният диоксид.
Натрупването на топлина с последващо бързо охлаждане на малки части от повърхностния слой на метала осигурява възможност за наваряване на цилиндрични части с малък размер по метода на вибродъгата. В този случай няма опасност от изтичане на течен метал от повърхността на детайла. На практика диапазонът от размери на детайлите, подходящи за наваряване по този метод, варира от 3 до 200 mm.
Вибродъговата наварка позволява да се получат равномерни слоеве с дебелина от няколко стотни от милиметъра до 3 мм в едно минаване. Уникалното свойство на тази настилка е, че в определен диапазон от режими е възможно да се извърши процесът на въздух без използване на защитни средства. Вибродъгово наваряване възстановява стоманени и чугунени части. При напластяване с нисковъглеродна тел, например клас Sv-08, повърхността лесно се обработва с фреза. За получаване на устойчиви на износване повърхности се използват телове Np-50G, Np-65G, Np-ZOHGSA, Np-40X13 и др.
Наваряването се извършва на променлив и постоянен ток с обратна полярност. Режимите на вибродъгово напластяване са дадени в табл. 7.18.
Вибродъговата настилка има редица сериозни недостатъци. По този начин ограничените обеми на заваръчната вана не осигуряват добро смесване на основния и наплавения метал, което води до образуване на пори и микропукнатини в последния. В процес на възстановяване на части, охлажданетечността, подадена в зоната на заваряване, осигурява втвърдяване на отложената перла, а насложената следваща перла частично разтопява предишната и създава зона на отгряване, което води до възникване на напрегнато състояние и увеличаване на пукнатините в отложения метал. Увеличеният слой на сплавта има нееднородна структура и съответно физични и механични свойства. Следователно, за части, възстановени чрез вибродъгова наварка, якостта на умора намалява повече от 2 пъти. В допълнение, производителността на вибродъгово напластяване в сравнение с наваряване с подслой от поток е много по-ниска, а невъзвратимите загуби на електродната тел поради отпадъци и пръски се увеличават с 3-4 пъти.
Поради тези причини в момента рядко се използва вибродъгово напластяване за възстановяване на автомобилни части. Части, които са били възстановени по-рано по този метод, сега успешно се депозират с помощта на по-модерни методи, например електрическо контактно заваряване на метален слой.
Таблица 7.18. Приблизителни режими на вибродъгово автоматично наваряване в течна струя (4% воден разтвор на калцинирана сода)