Изчисляване на камерата за пропарване на ямата
Конструкцията и принципът на работа на камерата за пара на ямата. Избор на режим на термична обработка на стенни блокове в камерата. Материален баланс, основни размери, продължителност на работния цикъл, аеродинамичен и хидравличен разчет на камерата за пропарване на ямата.
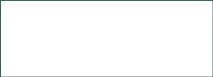
Изпратете добрата си работа в базата знания е лесно. Използвайте формата по-долу
Студенти, докторанти, млади учени, които използват базата от знания в обучението и работата си, ще ви бъдат много благодарни.
Хоствано на http://www.allbest.ru
Хоствано на http://www.allbest.ru
1. Описание на конструкцията и принципа на работа на камерата за пропарване
2. Технологично изчисление
2.1 Характеристики на продуктите, подложени на топлинна обработка
2.2 Избор на режим на готвене
2.3 Физични и химични процеси, протичащи по време на термичната обработка на стенни блокове в камерата за пропарване
2.4 Основни размери на камерата за пропарване
2.5 Време на цикъла на уреда за пара
2.6 Производителност и необходимия брой термични инсталации
2.7 Материален баланс на парната камера на шахтата
3. Топлинно изчисление
3.1 Отоплителен период
3.2 Изотермичен период на задържане
3.3 Период на изчакване
4. Аеродинамично изчисление
5. Хидравлично изчисление
5.1 Хидравлично изчисление на общия паропровод
5.2 Хидравлично изчисляване на перфорирана тръба
5.3 Хидравлично изчисление на кондензната система
5.4 Технико-икономически показатели на топлинна обработка
6. Здраве и безопасност при работа с ямна пропарна камера
Списък на използваната литература
Втвърдяване на бетон и стоманобетонни изделия (бетонови изделия) в заводи нанормалната температура е нерационална, тъй като е твърде дълга, намалява оборота на формулярите, забавя освобождаването на готовите продукти. Термичната обработка се използва за ускоряване на втвърдяването на бетона.
Известно е значението на топлинната и влагообработка на бетона в технологичната верига за производство на бетонови и стоманобетонни изделия. Топлинната и влага обработка е най-ефективният от съществуващите методи за ускоряване на втвърдяването на бетона. Това е най-важната технологична операция при производството на стоманобетонни изделия.
Всички дейности в заводите за стоманобетон са насочени към намаляване на потреблението на топлинна енергия и гориво, без да съкращават производствения цикъл за производство на продукти, използвани в различни условия.
През последните години основното внимание в заводите за сглобяем бетон се обръща на повишаване на ефективността на работата на оборудването, използващо топлина, прилагане на набор от мерки, налични за всяко предприятие за нормализиране на потреблението на технологична топлина, въвеждане на нови ефективни топлинни инсталации с повишена термична защита на ограждащи конструкции и енергоспестяващи технологии, използващи пара, електричество, продукти от изгарянето на природен газ и различни видове възобновяеми енергийни източници [1].
При производството на сглобяеми стоманобетонни изделия термичната обработка е един от най-енергоемките етапи, като отнема около 60% от общата консумация на енергия. Теоретично само 10-15% са необходими за нагряване на бетонни и метални форми, тоест почти една десета от консумираната в момента топлинна енергия, а планираните и непланирани загуби достигат 50% от общата консумация на енергия [2].
Енергийната ефективност трябва да се превърне в един от основните критерии за производствена технология, заедно с такива показатели катосебестойност, трудоемкост, материалоемкост, както и специфични капиталовложения. Следователно проблемът за намаляване на потреблението на енергия по време на топлинна обработка на сглобяеми бетонни и стоманобетонни конструкции е много актуален [3].
Изборът на метод за термична обработка се определя от вида на конструкцията. условията на неговата работа по време на работа, вида на армировката, класа на бетона и други фактори.
За да се спести енергия по време на топлинна обработка, трябва да се премине от ямкови камери към по-ефективни слотови и вертикални камери, използване на предварително загряти бетонови смеси, отопление в касетъчни инсталации или термоформирани пакети [3].
Инсталациите за термична обработка на бетон могат да бъдат периодични и непрекъснати. Инсталациите за партидно производство включват пещи от ямков тип, тунелни пещи, формовъчни касетъчни машини, настолни инсталации и автоклави. Непрекъснатите инсталации са тунелни камери, камери с прорези, вертикални камери и термоформи за подреждане. В този случай като топлоносител (източник на топлинна енергия) могат да се използват водна пара, паровъздушна смес, горещ въздух, електрически ток, слънчева енергия, продукти от изгаряне на природен газ [4].
Най-често срещаният вид топлинна обработка на бетон в стоманобетонните заводи е нагряването на продуктите с наситена пара в парни камери [2]. Използват се периодични и непрекъснати камери, най-често камери с периодична яма.
Курсовата работа по дисциплината "Процеси и апарати 2" е насочена към определяне на конструктивните характеристики, основните размери на камерата за пропарване и топлинните характеристики на нейната работа.
Основните цели на курсовата работа:
- базиранзадълбочено проучване на техническа информация за описание на дизайна и принципа на работа на термична инсталация; да характеризира основните процеси, протичащи при обработката на материала в инсталацията;
- да обоснове избора на режим на термична обработка на продуктите;
- извършване на технологичен разчет на инсталацията и определяне на нейните размери;
- извършва топлинно изчисление на инсталацията, съставя топлинен баланс и анализира основните разходи за топлина;
- извършване на аеродинамични изчисления на инсталацията;
- извършване на хидравлични изчисления на инсталацията за топлоснабдяване;
- да се определят основните технико-икономически показатели за термична обработка на продуктите в инсталацията.
Курсовата работа предвижда анализ на режима на работа и технико-икономическите показатели. В тази работа производителността на инсталацията е 35 000 m3 / година, обект на топлинна и влагообработка е стенен блок.
Курсовата работа е представена под формата на сетълмент - обяснителна бележка с обем от страници и лист формат А1 на графичната част, изобразяваща шахтна камера и диаграми, характеризиращи нейната работа.
1. Описание на конструкцията и принципа на работа на камерата за пропарване
Камерите за парно отопление (Фигура 1) се използват на стендови, полуконвейерни и поточни монтажни линии за производство на бетонни и стоманобетонни изделия. В курсовата работа се възприема агрегатно-поточен производствен метод, който се отличава с ограничен брой технологични постове, няколко операции се комбинират на всеки от постовете. Формите се транспортират с кранове. Едно от основните предимства на този метод е възможността да се използва за производство на продукти без значително пренастройване на производствените линии [3].
Камерата е инсталация, вкопана в земята, където се формовапродуктите се подлагат на топлинна обработка.
1 - етаж; 2 - стълба; 3 - изтичане на кондензат; 4 - система за оттичане на кондензат; 5 - стена; 6 - отвор за въвеждане на пара; 7 - тръбопровод; 8 - тръби; 9 - отвор за вентилация; 10 - канал; 11 - уплътнителен конус; 12 - червячен винт; 13 - порта за захранване; 14 - капак; 15 - канал; 16 - ъгъл; 17 - топлоизолация.
Фигура 1 - Камера за парна яма
Основните елементи на шахтната камера са стени, бетонен под с дренаж за кондензат, подвижен капак с хидравлично уплътнение, паропровод и системи за дренаж на кондензат.
Стените на камерата са с дебелина 400 мм. За да се намалят топлинните загуби в околната среда, стените на камерата са снабдени с топлоизолация 17. Стените на камерата 5 имат отвор 6 за вкарване на пара, която се подава надолу по камерата през тръбопровода 7 от мрежата. Тръбопроводът завършва с тръби 8, положени по периметъра на камерата с отвори - перфорации, през които парата влиза в камерата. Ямните камери и касети имат голяма топлинна инерция. Следователно е възможно да се регулира максималното отваряне на вентила за подаване на пара по такъв начин, че повишаването на температурата да отнеме време, приемливо за технологията [4].
В допълнение към отвора за вкарване на пара, в стената на камерата е направен отвор 9 за вентилация по време на периода на охлаждане. Чрез канал 10 е свързан с вентилатор, който отвежда паровъздушната смес от камерата [5].
Дъното на камерата е от бетон с топлоизолационен слой и хидроизолация. Дъното е с наклон 0,005-0,01 за изтичане на кондензат в дренажа и е оборудвано с воден затвор. В ямата на стълбата 2, където тече кондензатът, има устройство за оттичане на кондензат 3, което най-често е водоотделящ контур. Устройството премахва кондензата, но не пропуска пара.
Капак на ямаКамерата се състои главно от два компонента (има и други видове капаци). Капакът на камерата 14 е твърда метална рамка, пълна с топлоизолационен материал за намаляване на загубите в околната среда. Парата кондензира върху вътрешната повърхност на капака. Ако капакът не е топлоизолиран, тогава количеството на конденза е голямо, големите му капки разрушават повърхността на задушените продукти. За изолиране на камерата по време на нагряване и изотермично излагане от вентилационната система е монтиран уплътняващ конус 11, който може да се повдига и спуска с помощта на червячен винт 12, оборудван с маховик. Когато конусът е повдигнат, възниква вентилация, когато се спусне, камерата е надеждно изолирана от тази система. В допълнение към уплътнителния конус, за същата цел може да се използва хидравличен (воден) затвор чрез монтиране на канал 15 (дълбочина 100-150 mm). Капакът около периметъра е ограден с ъгъл 16, който е включен в канала. Кухината на канала е пълна с вода, което предотвратява избиването на пара от камерата. Вътрешната повърхност на капака има наклони отстрани, което гарантира оттичането на конденза към стените. В този случай парата не пада върху продукта и се извършва автоматично попълване на хидравличното уплътнение. Монтажът и демонтажът на капака се извършва с помощта на хидравлично задвижване или мостов кран [4].
Ямната камера работи по следния начин. Капакът се отстранява от камерата с кран и в него се монтират форми с продукти, така че да се обливат с пара от всички страни. За монтиране на форми в камери за пропарване на яма се използват стелажи с въртящи се скоби. Капакът се затваря и в съответствие с приетия режим на топлинна обработка температурата в камерата се повишава чрез подаване на пара през пароразпределителен колектор с дюзи. Цикълът на пара се състои от предварително излаганепродукти в топла камера до подаване на пара, температурата в камерата се повишава до максимум, изотермично задържане на продуктите при максимална температура и охлаждане на продуктите чрез продухване на въздух и е. Продължителността на топлинната и влагообработка зависи главно от дебелината на продуктите, активността и разхода на 1 m3 бетон на използвания портландцимент и предназначението на конструкцията.
Парата може да се подава към камерата на шахтата по два различни начина. Съгласно една от схемите колекторът за подаване на пара е разположен на ниво 0,6-0,7 от височината на камерата. Циркулацията се осигурява от енергията на парните струи, излизащи от едроразмерните точкови дюзи, чиито оси са насочени надолу. Друга схема предвижда потока на пара през хоризонтален паропровод, разположен по долния периметър на камерата, откъдето се насочва към вертикални перфорирани щрангове. В курсовата работа подаването на жива пара се осигурява чрез перфорирана тръба с примка (Фигура 2), разположена в долната част на камерата по периметъра. Парата, изтичаща от тръбата, се издига, смесва се с въздуха, образувайки паровъздушна смес.
1 - главен паропровод; 2 - диафрагма на дросела; 3 - общ паропровод; 4 - кран; 5 - паропровод на камерата на ямата; 6 - перфорирана тръба с примка
Фигура 2 - Схема на захранване с пара на камерата на ямата
Топлината се предава на материала по конвективно-проводим метод. Формата има директен контакт с охлаждащата течност. Предаването на топлинна форма се осъществява поради хаотичното движение на микрочастиците (конвекция). Преносът на топлина от формата към продукта се осъществява в резултат на топлопроводимост поради температурната разлика (проводимост).
За да се увеличи ефективността на отоплението в шахтните камери, се използват два фундаментално различни метода за организиране на топлинен процес:в паровъздушна среда с принудителна циркулация и в среда на чиста наситена пара. Паровъздушната смес се състои от сух въздух и водна пара. Нагряването на продуктите в среда на чиста наситена пара е препоръчително, ако е необходимо да се повиши температурата до 100oC за втвърдяване на бетон върху шлакови цименти. Тъй като портланд циментът се използва като свързващо вещество в курсовата работа, термичната обработка трябва да се извършва в среда пара-въздух. Това осигурява равномерно измиване на повърхностите на продуктите и също така намалява цикъла на загряване поради увеличаване на коефициента на топлопреминаване на нагряващата среда.
Колекторът за подаване на пара е разположен на ниво 0,6 от височината на камерата. Циркулацията се осигурява от енергията на парните струи, излизащи от едроразмерни точкови дюзи, чиито оси са насочени надолу. Високоскоростните потоци на нагряващата среда проникват поради разликата в налягането до всички повърхности на продуктите и изравняват температурата на средата по височината на камерата. Използването на принудителна циркулация на нагревателната среда намалява специфичния разход на пара до 150–200 kg/m3 [4].
Намаляването на дебита на охлаждащата течност по време на термичната обработка на бетона е спешно изискване на производството. За тази цел се използват следните мерки: надеждна топлоизолация на тръбопроводи, доставящи охлаждаща течност; поддържане в изправност на капаците на шахтните камери или завесите на други термични агрегати; увеличаване на коефициента на запълване на камерите с продукти; автоматизация на режимите на топлинна обработка на продуктите.
2. Технологично изчисление
2.1 Характеристики на продуктите, подложени на топлинна обработка
Сглобяемите стоманобетонни части и конструкции, произведени в заводи и доставени на строителни площадки в завършен вид, се използват широко в строителството.
Сглобяемите бетонни части са различнивисоко качество и издръжливост, не изискват специални грижи по време на работа, използването им намалява времето за строителство, намалява интензивността на труда, намалява потреблението на дърво и метал и опростява работата през зимния период [1].
В тази курсова работа се използва една от най-често срещаните части, изработени от сглобяем бетон - стенен блок, а именно вертикален блок на вътрешната стена.
Характеристиките на стенния блок са представени в таблица 1.