Измерване на геометрията на тръбопровода
Предприятията на автомобилната и космическата промишленост използват различни методи за проверка на тръбопроводи. При това методът, използващ оптична измервателна система, създадена на базата на технологията фотограметрия, притежава редица предимства, което повишава перспективите за неговото развитие.
Развитие и предимства Оптичното измерване като отделна технология датира от 19 век с появата на самата фотография. Дълго време фотограметрията се използваше изключително за картография с помощта на технологии за въздушна фотография, въздушна геодезия и др. и с разработването на специализирано оборудване, способно да ориентира снимките една спрямо друга (Фиг. 1 ).
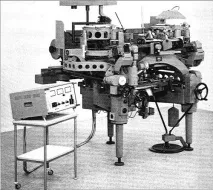
Ориз. 1. Фотограметрични устройства Автограф А7 и А8
В съвременния свят значението и ефективността на оптичните измервания е изключително голямо. Развитието на фотографските технологии и компютърните технологии повишават точността на самите измервания. Методът за фиксиране на обект стана предпоставка за появата на машинното зрение, което сега е повсеместно в автоматизираното производство.
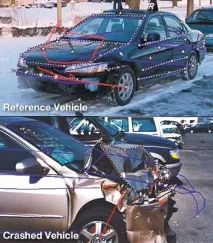
Ориз. 2. Анализ на катастрофиралия автомобил
Такова широко приложение на фотограметрията се дължи на следните предимства:
- Висока точност, тъй като изображенията на обекти се получават от прецизни камери, а обработката на изображенията се извършва по строги методи, използващи одобрени алгоритми.
- Висока производителност, постигната поради факта, че се измерват не самите обекти, а техните изображения. Това ви позволява да автоматизирате процесите на измерване на изображения и последваща обработка на компютър.
- Обективност и достоверност на информацията.
- Възможност за повторение на измерванията презв случай на съмнителни резултати.
- Възможност за бързо получаване на информация за състоянието както на целия обект, така и на отделни негови части.
- Безопасност на работа, тъй като измерванията се извършват по безконтактен метод. Това е от особено значение, когато обектът е недостъпен или престоят в района му е опасен за човешкото здраве.
- Способността да се изучават стационарни, както и бавно и бързо движещи се обекти, преходни и бавни процеси.
Традиционна технология за измерване на тръбопроводи Поради сложността на измерването на геометрията на тръбопровода, като правило предприятията за производство на автомобили и самолети използват самостоятелно направени калибриращи стендове (Фиг. 3 ).
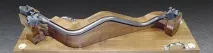
Ориз. 3. Пример за стенд за калибриране
Основната причина за използването им е липсата на 3D модели и оборудване за работа с модели, ръчният метод на изработка и възможността за бързо огъване в случай на несъответствие. Най-критичните участъци са фиксирани в хлъзгача, а при проверка тръбопроводът трябва да бъде твърдо фиксиран в хлъзгача с точността, предоставена от производителя. Всъщност самият хелинг имитира местоположението на критичните системи и позицията на тръбопровода спрямо тях. Измерването на тръбопровода в оборудването на хелинга се използва широко в момента. От предимствата може да се отбележи, че това е най-точната и най-бърза технология за измерване на тръбопроводи, но става доста сложно, ако е необходимо да се използват плъзгачи за големи тръбопроводи, широка гама от продукти (тъй като всеки тръбопровод изисква собствен хлъзгач) и сложност на производството. Също така, точността и обективността на измерването може да падне значително, ако се използва несолиден дизайн.хелинг и оборудване за набиране, което трябва да бъде фиксирано според условното положение на тръбопровода. Системата за подреждане не дава обратна връзка, т.е. операторът, въз основа единствено на собствения си опит, може да определи зоната за повторно огъване, ако размерите на продукта не съвпадат. Освен това хелингът се нуждае от периодична проверка, а такава процедура е доста сложна при наличието на широка гама от продукти. В случай на промяна на който и да е елемент от структурата на тръбопровода, хелингът изисква ревизия и не може да се използва.
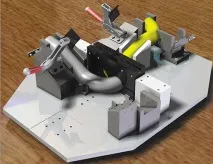
Ориз. 4. CAD-моделиране на стенд за калибриране на тръбопровод с колена
В съвременното производство прикладите се създават на базата на триизмерен модел (фиг. 4 ), където дизайнерът поставя фиксиращите елементи директно върху основата на детайла. Също така, създаването на запаси е необходимо за тези продукти, които са сложни геометрични форми, тръбопроводи с няколко клона, преход на диаметри и размери и т.н., тъй като не съществува модерно оборудване за бързи измервания на такива продукти. Най-оправданото използване на оборудване за хелинг в производството на автомобилни продукти поради високата производителност в комбинация с нисък диапазон. Съвременните компании, произвеждащи оборудване за огъване на тръби, предлагат на своите клиенти и измервателни рамена за проверка на тръбопроводи (фиг. 5 ). Оборудването представлява шарнирен манипулатор с контактен сензор или лазерен сензор в края - операторът го довежда до зоната за измерване и след това го премества в следващата зона за измерване. В резултат на това операторът получава несъответствия между измерването и 3D модела на референтния елемент. В комбинация с машината за огъване на тръби, софтуерът на измервателното рамо можеизпрати офсетните данни за машинната програма и производството на друг детайл.
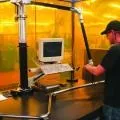
Ориз. 5. Измервателно рамо за измерване на тръбопроводи
Измервателните рамена са най-разпространените индустриални системи за измерване на тръбопроводни секции. Един от основните недостатъци на такива системи е влиянието на оператора върху процеса на измерване - всеки път той измерва различни области и по този начин внася допълнителна грешка в измервателната технология. Всъщност ръката измерва позицията на един прав участък спрямо друг, като по този начин изгражда напречни линии в софтуера за приблизителното местоположение на чупката. Обаче участъците кривина в чупка или много малки прави секции са изключително трудни за измерване. В допълнение, тръбопроводът изисква инструмент за фиксирането му пред измервателното рамо. Обратното инженерство, тоест изграждането на модел въз основа на продукт, има ограничени приложения. Предимствата на измервателното рамо в сравнение с приспособлението за калибриране са очевидни: оборудването работи с триизмерен модел, има връзка с машини за огъване на тръби за коригиране на програмите за огъване, проста работа и сравнително бърза работа в сравнение с традиционните системи за измерване на координати.
Измерване на тръбопроводи, базирано на оптична система AICON TubeInspect В началото на 1990 г. AICON 3D SYSTEMS (Германия) разработи своята система AICON TubeInspect, базирана на оптично измерване с помощта на цифрови камери. Системата се състои от стоманен корпус с монтирани CCD камери, които снимат работната зона от няколко позиции и по този начин определят контура на тръбопровода за по-нататъшна обработка. Софтуерът симулира 3D моделтръбопровод, който може да се използва за сравнение с референтен модел или като еталон за последващи измервания. Системата също така взаимодейства с най-разпространените марки машини за огъване на тръби. В съответствие с технологията за цифрова фотограметрия, хардуерът и софтуерът използват обработка на изображението пиксел по пиксел, като подчертават контурите на обект на контрастен фон и по този начин определят геометричните параметри на продукта (фиг. 6, 7 ).
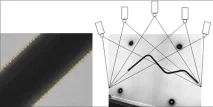
Ориз. 6. Заснемане на тръбопроводи и подчертаване на контура на обекта
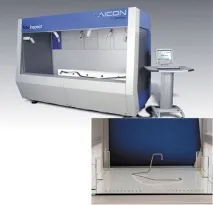
Ориз. 7. Общ изглед на системата AICON TubeInspect и местоположението на тръбата за измерване
Възможностите на инсталираните съвременни цифрови фотоапарати, съчетани със софтуерни алгоритми, осигуряват грешка до 0,1 мм за отклонение на корпуса. Оптичната система за измерване на тръби е третият и най-напреднал метод. Основните предимства са работа върху триизмерен модел на продукта, възможност за извършване на обратно инженерство и безусловна скорост на измерване, която е скоростта на получаване на моментна снимка на продукта. В същото време възможностите на фотограметрията при измерване на тръбопроводи се основават на възможностите на софтуерните алгоритми и в някои случаи, както беше споменато по-горе, стандартното стеково оборудване остава необходимо за използване при проверка. Едно от допълнителните предимства на системата и метода за фотограметрия е възможността за заснемане на обекта „както е“, т.е. не са необходими фиксиращи устройства или преинсталации. Недостатъците включват икономически разходи, които могат да бъдат несравними с малка гама и простота на продуктите, ниска производствена програма на самото предприятие и много другивисоки изисквания към операторите на оборудване в сравнение с използването на стандартно оборудване за подреждане. Системите с възможност за обратно инженерство са от основен интерес за космическата индустрия, която произвежда и тества тръбопроводи, използвайки метода на плазмения шаблон. В предприятието има продуктови стандарти, въз основа на които се излага или произвежда оборудване за хелинг за последваща проверка. В момента има сложен процес на въвеждане на цифрови технологии за обработка и производство на продукти според триизмерни модели. В такива случаи система с прогресивни възможности за обратно инженерство - преобразуване на шаблони и стандарти в цифрови модели с обективни измервателни данни - изглежда търсена и необходима. Ролята на фотограметричната технология при измерването на тръбопроводи само ще нараства. Понастоящем се проучва възможността за измерване на геометричните размери на краищата на тръбите, работа с гъвкави маркучи, пълнофункционално измерване на тръби с участъци завой в завой, преходни диаметри и оценка на овалността на тръбопровода след процеса на огъване.