ИЗПОЛЗВАНЕ, Рециклиране на прах от производството на стомана
Съставът на заряда оказва значително влияние върху състава на отстранения прах; този ефект е особено забележим, когато стоманата се топи в дъгови пещи за топене на стомана. При производството на високолегирани стомани в състава на отпадъците се забелязва делът на ценни легиращи елементи (Cr, Ni и др.). При претопяването на обикновена, неподбрана шихта (основно закупен метален скрап с голям дял битов и амортизационен скрап) прахът съдържа висок дял цветни метали, предимно Zn, Pb, а понякога и Cd.
Обработката на такъв прах изисква специално внимание, тъй като, първо, е невъзможно просто да ги използвате като добавка в заряда (това ще влоши качеството на стоманата); второ, не подлежи на погребване в земята, тъй като е възможно отравяне на почвата (погребването в земята е забранено в редица страни); трето, от такъв прах е целесъобразно да се извлекат съдържащите се в него ценни (с изключение на желязото) компоненти.
Съвременната индустрия използва редица технологии, които осигуряват обработката на праха от производството на стомана. Една от опциите е показана на фиг. 25.10.
Преработка на прах от топене, съдържащ цинк и олово. Скрапът е основният източник на такива примеси като Zn и Pb (поцинковано желязо, влизащо в заряда, месингови и бронзови части, обвивки на електрически кабели и др.), влизащи в стоманодобивните съоръжения. Цинк - точка на топене 419,5°С и точка на кипене 906°С, олово - точка на топене 327,4°С и точка на кипене 1725"С.
Попадайки в зоната на високотемпературни металургични реакции, оловото и особено цинкът се изпаряват, окисляват и се отстраняват заедно с отработените газове. Основната част от цинка и оловото, попаднали в агрегата със заряда, се улавят от прахоуловители. И цинк, и оловоса скъпи материали, поради което непрекъснато се разработват нови технологии за обезвреждане на прах, съдържащ Zn и Pb.
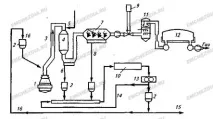
Около половината от произведения цинк се изразходва за защита на стоманата от корозия (процес на поцинковане), т.е. навлизането на съдържащи цинк компоненти заедно с металния заряд в стоманодобивните агрегати е неизбежно.
В тази връзка специално отбелязваме значението на така наречения автоскрап. По този начин автомобилният парк на западноевропейските страни има повече от 140 милиона автомобила; около 10 милиона броя излизат от строя всяка година. След раздробяване на автомобилни части стоманата лесно се отделя чрез магнитна сепарация, полученият метален скрап обикновено се използва като заряд в дъгови пещи. При претопяването на такъв заряд се улавят 10–25 kg/t дисперсен прах, съдържащ 10–35% Zn, както и Pb и Cd. Според прогнозите в началото на XXI век. повече от 700 000 тона такъв прах ще бъдат събрани в електродъгови пещи в Западна Европа.
Обемът на амортизационния скрап в света през 1994 г. достигна 272 милиона тона и непрекъснато нараства (в момента амортизационният скрап е единственият вид скрап, чието количество нараства) . Същите процеси и тенденции са характерни и за нашата страна.
В индустриализираните страни делът на листовете с покритие е повече от 40% от производството и ще нарасне до 60-80% в бъдеще. Проблемът е как да се организира изхвърлянето на отпадъци (топен прах), съдържащи Zn. От гледна точка на потребителя (и преработвателя) на тези отпадъци, колкото по-висока е концентрацията на Zn и Pb в тях, толкова по-изгодно е тяхното обезвреждане.
Някои фабрики в Западна Европа използват технология, чиято същност е следната. Процесните газове преминават през газоочистване с ръкавни филтри; Събраният прах се събира в спецбункер и се използва отново: малко след разтопяването на скрап, той се вдухва в границата метал-шлака. За подобряване на процеса на пневматичен транспорт се използва смес от прах и въглища (фиг. 25.11).
Инжектирането продължава около 10 минути. Като се има предвид, че на 1 тон стомана се генерират 15-20 кг прах, за 140-тонна пещ трябва да се вдухат около 2,5 тона отпадъци през това време. Почти целият цинк, съдържащ се в издуханите отпадъци, се изпарява и преминава в новообразувания прах. Чрез този метод е възможно да се увеличи концентрацията на цинк в отпадъците около 1,5 пъти.
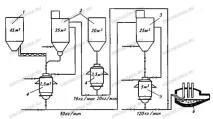
Редица предприятия използват методите на двустепенна или едноетапна вализация; в резултат на това се получава междинен продукт („мръсен“ цинков оксид), от който чрез многократна обработка може да се получи чист цинк.
Процесът Waelz гарантира, че цинкът и другите метали, предназначени за продажба, се оползотворяват от отпадъците. Желязният остатък се връща в пещта. В системите за обработка с пламъчен реактор цинковият оксид се възстановява и желязото остава като оксиди в шлаката.
Обработка на прах, съдържащ хром и никел
При производството на високолегирани стомани (например неръждаема стомана) в електрически пещи, уловените отпадъци, в допълнение към цинк, олово, кадмий и др., Съдържат ценни компоненти като хром, никел и др. Разработват се специални технологии за обезвреждане на такъв прах.
Така в един от италианските заводи за преработка на отпадъци, генерирани по време на топенето на неръждаема стомана, е инсталирана плазмена пещ за претопяване с постоянен ток, която годишно обработва около 20 хиляди тона отпадъци.
Получава се сплав (в зависимост от състава на отпадъците), съдържаща, %: Cr 8-16; Ni 2-8; MP 2-4; От 3-5. Съставът на шлаката при претопяване, %: CaO 40-45; SiO2 25-30; Cr2O3 около 2. Уловен в процесапрахът от топене при претопяване съдържа повече от 50% ZnO и около 6% PbO.
Обработка на прах при нагряване във вакуум
Япония е разработила процес, наречен VHR процес.
Около 450 000 тона прах се генерират годишно само в японските дъгови пещи. Прахът от електрическите пещи, чийто основен компонент е метален скрап, съдържа средно 32% Fe и 23% Zn. Освен това прахът от пещта съдържа значителни количества опасни за околната среда компоненти, включително олово (2,2%), хром (0,36%), кадмий (0,024%), хлор (3,14%). Процесът на VHR се извършва на няколко етапа:
- 1) сухият прах се държи при температура 500-900 ° C за 3 минути във вакуум при налягане 133 Pa (1 mmHg); на този етап от отпадъците се отстраняват натрий, калий, олово и неговите съединения (PbO, PbCl2, PbF2);
- 2) ръководят възстановяването на цинка; Fe и FeO действат като редуциращ агент;
- 3) изпареният редуциран цинк се кондензира в кондензатор при температура, надвишаваща точката на кипене на цинка (при същото ниско налягане);
- 4) железният продукт, оставащ след отстраняването на цинка от праха, се брикетира и използва като част от металния заряд при производството на стомана.
Степента на отстраняване на цинка от отпадъците с тази технология е близо до 100%.
Третиране на прах в ELI процеси
Има няколко варианта за организиране на процеса на течнофазова редукция на желязо от материали от желязна руда. Някои от тях предвиждат възможност за използване на разтопен прах в заряда.
Японската фирма Kawasaki Steel Corp. е разработен процес на редукция в течна фаза, специално проектиран за обработка на прах и утайки от конверторното производство (фиг. 25.12). Пещта съдържа два реда фурми: долната е за прегряваща течноствани с температура над 1500 ° C, като горната е за издухване на прах. Между ланцетите има зона на интензивна редукция на трудно възстановими оксиди.
При обработката на хром- и никел-съдържащи прах и утайки е постигната степен на извличане на хром 98% и никел 100%.
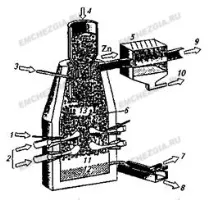
Използване на хидрометалургични методи
Извличането на цинк, олово и други примеси от цветни метали от стоманодобивните отпадъци може да се извърши и чрез хидрометалургични методи. Според един от вариантите технологията включва излугване на цинк, олово, мед, кадмий и калций с разтвор на оцетна киселина за образуване на съответните разтворими метални комплекси и последващо сулфидно утаяване на тежки метали със сероводород H2S. Обработката на цинксъдържащ прах по хидрометалургични методи се прилага в някои заводи в Италия и САЩ.
Прахът се подлага на излугване в разтвор на амониев хлорид. За цинка реакцията има формата
- ZnO + 2NH4Cl = Zn(NH3)2Cl2 + H2O.
Други метали (олово, кадмий, мед) реагират по подобен начин с амониев хлорид. Степента на извличане на цинка е 60-80%. Твърдият остатък (състоящ се главно от железни оксиди и цинкови ферити) се суши, пелетизира се с въглища и се въвежда в заряда на дъгова пещ, по време на топенето, при което цинковите ферити се дисоциират, цинкът се изпарява и се отстранява заедно с технологичните газове в системата за пречистване на газ (където отново се улавя съдържащият цинк прах).
Разтворът за излугване на свой ред влиза в електролизните вани, където цинкът се отлага върху титанови катоди:
Редица процеси за екстракция на цинк използват съкращението ZINCEX в имената си.
Според много експерти най-икономичният процес за обезвреждане на цинка от отпадъци трябва да включва предварителенизбор на поцинковани продукти, обработката им в разтвор на гореща основа и последваща електрохимична обработка.
Производство на стъкло
Изхвърлянето на праха от производството на стомана може да се организира по съвсем различен начин. И така, през 1991 г. в САЩ е организирана компания за производство на стъкло и стъклени изделия. Процесът, използван в това производство, се състои в това, че отпадъците от цеховете за производство на стомана (прах, шлака, огнеупорни отпадъци) се раздробяват, смесват и след това се стопяват в пламъчни пещи, в които се получават стопилки, които се използват за производството на продукти от цветно стъкло, използвани за декоративни цели, както и цветни тухли, стъклени филтри и др.
В зависимост от състава на шихтата полученият материал съдържа различни количества примеси като мед, кобалт, хром, никел, антимон, цинк, ванадий и др.