Котли с циркулационен кипящ слой
При разглеждане на перспективите за използване на твърдо гориво, по-специално за енергийни блокове от ново поколение, един от основните въпроси е неговото ефективно изгаряне. Последното се отнася преди всичко до изпълнението на две изисквания: изгарянето трябва да е пълно, т.е. икономичен и не трябва да води до големи емисии на вредни вещества (предимно серни и азотни оксиди).
Дълго време за горене се използва и продължава да се използва така наречениятфакелен метод, при който смес от фино смлени въглища и горещ въздух непрекъснато се подава към зоната на горене, поддържайки горящ факел, който е източник на лъчиста и топлинна енергия за загряване на работния флуид. За изпълнение на горните изисквания са разработени и въведени в практиката редица режимни и конструктивни мерки, които обаче не могат да решат изцяло проблема. Ето защо през последните 15 години се търсят екологични технологии за изгаряне на широк спектър от твърди горива, особено нискокачествени енергийни твърди горива. Сред тези технологии е технологията за изгаряне на твърди горива вциркулиращ кипящ слой(CFB) при атмосферно налягане.
Теоретичната основа за функционирането на котли с PCS е концепцията закипящ слой. Ако в някаква камера е монтирана решетка (фиг. 11.9,a), върху която е поставен слой въглища и към решетката се подава малко количество въздух, тогава след предварителното нагряване на слоя, горивото ще започне да гори от повърхността с отделяне на газообразни продукти от горенето. При попълване на горящото гориво върху решетката ще се поддържа горящ фиксиран слой. Ще се извършва така нареченотослойно изгарянена твърдо гориво. Ако увеличите подаването на въздух под решетката, тогава счастици гориво върху решетката, ще има скоростно налягане, което ще противодейства на силата на гравитацията, действаща върху всяка частица гориво. При определена скорост на въздуха частиците гориво ще бъдат в суспензия в издигащия се въздушен поток и дебелината на горящия слой ще се увеличи (фиг. 11.9,b).
С по-нататъшно увеличаване на скоростта в слоя се появяват отделни въздушни мехурчета (фиг. 11.9,c), а дебелината на слоя се увеличава още повече. Това е така нареченият балон кипящ слой. Той се държи като кипяща течност, откъдето идва и името на метода - изгаряне в кипящ слой.
При още по-голям въздушен поток повдигащата сила, действаща върху горивните частици, се оказва толкова голяма, че те нямат време да изгорят и да излязат от кипящия слой. При по-нататъшно увеличаване на въздушния поток видимият слой изчезва и се получава изгаряне на натрупвания от горивни частици в целия обем на камерата с интензивно смесване (фиг. 11.9,d). По-голям брой горивни частици нямат време да изгорят и се изнасят извън камерата. Тук по пътя им е монтиран циклон - цилиндричен съд, в който продуктите от горенето се отделят от неизгорелите частици. Продуктите от горенето се насочват към втората част на котела - конвекционната шахта - за загряване на работния флуид (вода и пара), а неизгорелите частици се движат във вихров поток, изхвърлят се към стените, падат надолу и отново се изпращат в горивната камера. Това ециркулиращият кипящ слой. Основната му характеристика е, че циркулиращият материал е стотици пъти по-голям от количеството въздух, подаван за горене.
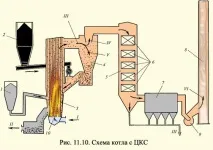
Една от основните идеи, реализирани в CFB котлите, е, че температурата на кипящия слой се оказва ниска, на ниво 820–900 ° C. При такива температуриобразуването на азотни оксиди е много бавно. Имайте предвид, че в пещите с въглищен прах с горелка температурата на горене достига 2000 °C. От своя страна ниската температура на горене се осигурява от големия размер на въглищните частици (от 2 до 25 mm) и тяхното отделяне в кипящия слой, за разлика от изгарянето на въглищен прах, когато размерът на праховите частици е на ниво от 200 микрона.
Друга важна идея е многократната циркулация на гореща смес от пепел, варовик и сравнително малко количество прясно гориво. Това осигурява не само добро десулфуриране на продуктите от горенето, но и значително интензифицира процеса на горене.
Котлите с CFB, в допълнение към предимствата, отбелязани по-горе, имат редица други.
- 2. Един и същи котел може да гори горива с различно и различно качество.
- 3. Преди да се подаде в CFB пещта, горивото не изисква фино смилане (достатъчно е раздробяване), което премахва необходимостта от въглищни мелници и подобрява екологичната ситуация в ТЕЦ.
- 4. Липсата на отделно пречистване на сяра и азот (в CFB котлите те са органично интегрирани в горивния процес) осигурява компактността на тези котли, което ги прави привлекателни за реконструкция на работещи топлоелектрически централи.
В същото време, в сравнение с котлите, работещи с въглища, CFB котлите са по-сложни, работят при по-трудни условия (ерозия на повърхността на нагряване от прахов поток) и имат повишена консумация на енергия за задвижване на вентилатори с високо налягане за подаване на въздух към зоната на горене и създаване на кипящ слой.
Проучванията за осъществимост показват, че CFB котлите в енергийни блокове от 150-200 MW осигуряват разходите за електроенергия, капиталови разходи, гориво, поддръжка и ремонтни разходи, които не надвишават подобни разходи за котли на въглищен прах с десулфуризация. При коетоподчертава се, че резултатите от сравнението зависят от голям брой фактори и се определят от конкретни условия.
Обхватът на CFB котлите е изгаряне на нискокачествени твърди горива с паропроизводителност до 250 t/h, както за нови ТЕЦ, така и за модернизирани. Понастоящем в световен мащаб работят повече от 200 CFB котли, включително енергиен блок с мощност 250 MW. В България се разработват CFB котли с паропроизводителност 160, 500 и 1000 t/h за изгаряне на каменни и кафяви въглища от различни находища.