Монтаж на зъбни колела въз основа на силата на триене - Монтажни и монтажни работи
Обработка на дърво и метал
Механичните трансмисии, чиято работа се основава на силата на триене, могат да бъдат разделени на две групи: ремъчни - използват се, ако взаимодействащите валове са на известно разстояние един от друг, и триещи - ако валовете са разположени в непосредствена близост.
При ремъчните задвижвания движението се предава с помощта на гъвкав, затворен пръстен, ремък, носен на две макари. Коланите могат да бъдат плоски, клиновидни и кръгли.
Плоските колани са изработени от кожа, гумирани или памучни тъкани, вълна или коприна. Преди монтажа такива колани се разтягат за три до пет дни, след което краищата на коланите се свързват чрез залепване, зашиване или използване на метални скоби. Най-добрият метод на свързване е залепването (кожа - с наклонен шев, гумирана - със стъпаловиден шев). За залепване на кожени колани се използва mezdrovy, желатин, целулоза, рибено лепило, за гумирани - каучукови тиуратни лепила от 1-ви и 2-ри клас в равни пропорции. Преди залепване краищата на кожените колани се почистват старателно, нанасят се два слоя лепило на интервали от 5-6 минути и се застъпват. След това залепеният шев се захваща между две дъски, които се затягат с болтове и се задържат 5-8 часа. Краищата на гумираните ленти се почистват с нож, след това се правят стъпаловидни первази с пила и се обезмасляват с бензин, нанасят се три или четири слоя лепило (преди нанасянето на следващия слой, предишният се изсушава), след нанасянето на последния слой (без proT ^ chpka), краищата се свързват, затягат се със скоби между две дъски и се държат при температура 16-20 градуса C за 24 часа (или при температура 100 градуса С - 3-4 часа). Плоските ремъци се използват в предавки със скорост на въртене до 30 m/s.
клиновидни ремъциможе да бъде от плат или шнур-корд, с гладък и назъбен профил, ъгълът на трапецовидната форма е 40 градуса.
С достатъчна гъвкавост и по-голяма здравина в сравнение с плоските ремъци, клиновите ремъци се използват за предаване на мощност от 0,3 до 75 kW (в зависимост от профила и дължината на ремъка). Ремъчните шайби на джантата имат клиновидни канали с профилен ъгъл 34-40 градуса.
Коланите с кръгъл профил са кожени, памучни, найлонови или гумирани, с диаметър от 2 до 20 мм. Обхватът е същият като при плоските колани. Профилът на канала на задвижващата шайба с кръгъл ремък е полукръгъл с радиус, равен на радиуса на ремъка.
Технологичният процес на сглобяване на ремъчна предавка се състои от следните стъпки: - балансиране на шайбите, т.е. премахване на техния дисбаланс. Постига се или чрез пробиване на част от метала от макарата, или чрез натоварване със специални тежести; - монтаж на шайби на валовете. Те се притискат и фиксират с ключ или слот (трябва да се отбележи, че ударните инструменти не могат да се използват за натискане на ролката върху вала, поради което се извършва с помощта на специални устройства); - регулирането на трансмисията се състои в създаването на определена сила на опъване на колана. Опънът се проверява с динамометър или тежести, окачени на скобата (при въздействие на определена сила от 50 до 100 N или с определено тегло на тежестите трябва да има еднаква деформация на колана, която е определена от техническите условия за всеки конкретен механизъм). Ако напрежението на ремъка е ниско, той се плъзга по време на работа на механизма или „бие“ (изскача), нагрява се, което води до бързо износване, прекомерното напрежение на ремъка създава прекомерно натоварване на лагерите, а също така води до бързо износване на шийките на вала имакари. Напрежението се регулира чрез преместване на опъващата ролка.
Работоспособността на механичното ремъчно предаване се характеризира с големината на ъглите на обвиване (ъгълът, образуван от лъчите, излизащи от центъра на шайбата и преминаващи през крайните точки на интерфейса шайба-ремък). Решаващ фактор е ъгълът на навиване на по-малката шайба, той трябва да бъде поне 120 градуса. Това условие е изпълнено, ако съотношението на диаметъра на задвижващата шайба към диаметъра на задвижваната шайба е в диапазона от y до 3, а центровото разстояние е не по-малко от два пъти сумата от диаметрите на двете шайби.
Фрикционните предавки предават въртеливи движения между валовете с помощта на сила на триене. Най-често срещаните механизми, които използват фрикционни предавки, са фрикционни съединители и спирачки.
Фрикционните съединители, в зависимост от предназначението, могат да бъдат съединителни (в постоянно зацепване, но, ако е необходимо, изключени), например съединител в автомобил или безопасност, те предпазват задвижването от повреда по време на претоварване.
Името на спирачката говори само за себе си - това е устройство за намаляване на скоростта до пълно спиране на автомобила. Спирачката на всеки механизъм се характеризира с два показателя: времето за спиране и скоростта, с която започва спирането. Времето за спиране зависи от контакта на спирачната накладка или лента с въртящите се елементи на спирачката, следователно е важно фрикционният материал да прилепва плътно към накладката или лентата (без бръчки, издутини и издатини на глави на нитове), а площта на контакта му със спирачната повърхност трябва да бъде най-малко 80%.
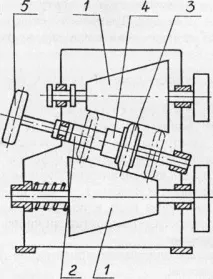
По време на работа на механизма, т.е. когато спирачката е неактивна, фрикционният материал не трябва да влиза в контакт с въртящи се части, за коитоопределена празнина.
Но ако тази празнина е много малка, това неизбежно ще доведе до нагряване на повърхностите на триещите се двойки и до бързото им износване.
Основната част на фрикционната предавка е фрикционното колело, което предава въртеливи движения от един вал на друг (може да бъде текстолит, влакна, кожа, дърво или гума). Размерът на предавания въртящ момент зависи от коефициента на триене на триещите се двойки, както и от силата на притискане един към друг на отделните звена на триещото предаване. Технологичният процес на сглобяване на фрикционни предавки е подобен на сглобяването на зъбни колела.