MRP и MRP II стандарти
Един от най-важните компоненти на управленските дейности във всяко предприятие е ефективното планиране на дейностите. Необходимостта от планиране се дължи на факта, че основните забавяния в производството на продуктите са свързани предимно с нередовни доставки на поръчано оборудване и компоненти. В резултат на това ефективността на производството намалява (поради недостатъчно производство на продукти), а в складовете има изобилие от материали, получени по-рано от планираната дата, натрупват се готови и непланирани продукти. Освен това, поради дисбаланса в доставката на компоненти, възникват различни трудности при отчитането им в производствения процес и поддръжката на продукта.
MRP Методология за планиране на нуждите от материали на предприятието
Първото прилагане на възможностите за използване на компютърни технологии за планиране на дейността на предприятията (включително планирането на производствените процеси) възниква в началото на 60-те години на ХХ век (например по време на изпълнението на проекта Boeing 747, който изисква стотици хиляди листове документи и подробности). През 1965 г. се появява терминът BOMP (Bill Of Material Processing) за обозначаване на системи за обработка на състава (спецификация) на продукт с цел изчисляване на необходимостта от материали. Такива системи се основават на концепцията за спецификация на продукта (Bill of Material - BOM), която показва зависимостта на търсенето на суровини, полуготови продукти и т.н. от плана за производство на готови продукти (като се вземе предвид времето).
Алгоритъмът на работа на такава система беше следният: основният производствен план (MPS) и списъкът на продуктовата гама (IM) се задават на входа. След това се извършва операцията "експлозия (разкриване)" - изчисляване на разходите и / или необходимостта от материали. В резултат на изчислението се получава план за доставки.
Естественото развитие на такива системи е добавянето на отчитане на материалните запаси в складовете и отчитане на времето на операцията. Резултатът е: "план за покупки и план за производство + корекция на плановете", ако книгата за поръчки се промени.
Такива корпоративни системи се наричат планиране на материалните изисквания (MRP).
Основните цели на MRP системите са:
- задоволяване на необходимостта от материали, компоненти и продукти за планиране на производството и доставка до потребителите;
- поддържане на нива на запасите не по-високи от планираните;
- планиране на производствени операции, графици за доставка, операции по закупуване.
Методологията MRP е имплементация на два добре познати принципа – „Поръчка навреме“ (Order In Time) и „Навреме за производство“ (Kanban), обединени в методологията „Точно навреме“ (Just In Time – JIT). Всъщност тази методика представлява алгоритъм за оптимално управление на поръчките за готова продукция, производство и запаси от суровини и материали, реализиран с помощта на компютърна система.
MRP модулът изисква следните входни данни:
- данни за състоянието на инвентара („Файл със състоянието на инвентара“). Този документ отразява цялата налична номенклатура: запаси, незавършено производство, полуфабрикати, готови продукти. Освен това трябва да посочи планираните поръчки и поръчките, очакващи доставка;
- спецификация на състава на продукта (Bill of Material - BOM).
Резултатите от MRP модула са следните документи:
- график на поръчките за покупка / производство на материали и компоненти (Планиран график на поръчките) - документ, който описва колко суровини, материали,частите трябва да бъдат поръчани във всеки период от периода на планиране. Този документ определя вътрешния производствен план за използване на компоненти и плана за външни покупки;
- промени в графика на поръчките за покупка / производство на материали и компоненти (Промени в планираните поръчки) - документ, съдържащ корекции на предварително планирани поръчки за покупка / производство на материали и компоненти.
Първоначално с помощта на MRP системи планът за поръчки и потребление на компоненти за определен период просто се формира на базата на одобрена производствена програма. Това не задоволява напълно нарастващите нужди на предприятията.
За да се подобри ефективността на планирането в края на 70-те години на 20 век. в MRP системите е внедрена идеята на Oliver White и George Plosl за възпроизвеждане на затворен цикъл (Closed Loop Material Requirement Planning), което предполага изготвяне на последователна производствена програма и нейния контрол на ниво цех. Допълнителни функции са добавени към основните функции за планиране на капацитета и изискванията за материали, като например измерване на производителността. В общия случай това е следене на съответствието на количеството на произведените продукти с количеството на компонентите, използвани в процеса на сглобяване, изготвяне на регулярни отчети за забавяне на поръчките, за обема и динамиката на продажбите на продуктите, за доставчиците и др.
Отчетите, създадени по време на работата на модифицираната MRP система, бяха анализирани и взети предвид на по-нататъшни етапи на планиране, променяйки (ако е необходимо) производствената програма и плана за поръчки (като по този начин се осигурява гъвкавост на планирането във връзка с такива външни фактори като нивото на търсене, текущото състояние на нещата с доставчиците, наличносттааксесоари и др.).
Основната задача на MRP-системите е да осигурят наличността на необходимото количество необходими материали (компоненти) в складовите и производствените помещения по всяко време в рамките на плановия период. Софтуерните системи, внедрени на базата на методологията на MRP, позволяват оптимално регулиране на доставките, контрол на запасите и самата производствена технология. Използването на MRP системи позволи да се намали обемът на постоянните запаси чрез оптимизиране на процеса на доставка.
Безспорните предимства на MRP системите включват: организационна ефективност на планирането на инвентара, автоматизация на тяхното счетоводство, намаляване на грешките в планирането на инвентара и разходите за складиране на материални ресурси. Основните недостатъци на MRP системите:
- значително количество входни данни и тяхната предварителна обработка;
- увеличаване на логистичните разходи за обработка на поръчки и транспорт, тъй като компанията се стреми да намали допълнително запасите от материални ресурси или да премине към работа с малки поръчки с висока честота на тяхното изпълнение;
- нечувствителност към краткосрочни промени в търсенето;
- наличието на откази поради големия размер на системата и нейната сложност.
Въпреки това, през 60-те години на миналия век много големи производствени компании - автомобилни, корабостроителни, самолетостроителни - успешно използват MRP системи за повишаване на ефективността на производството.
MRP II стандарт
При изчисляване на необходимостта от материали в MRP системите не се вземат предвид производствените мощности, степента и неравномерността на тяхното натоварване, разходите за труд и др. През ХХ век методологията на MRP-системите със затворен цикъл се трансформира в система за планиране на производствените ресурсиза цялото предприятие (Manufactory Resource Planning), което беше наречено MRPII (римската цифра II беше добавена поради идентичността на съкращенията). До 1980 г. формулата беше MRPII = MRP + производствен капацитет.
Стандартът MRPII е разработен в САЩ и се поддържа от Американското общество за контрол на производството и инвентара (APICS). По едно време, с подкрепата на APICS, беше публикуван документът "MRPII Standard System" (Landvater Darryl V., Gray Christopher D.), който описва основните изисквания към системите за производство на информация.
В съответствие със "Стандартната система MRPII" в информационна система, реализирана на базата на стандарта MRPII, трябва да бъдат реализирани следните 16 групи функции:
- Планиране на продажби и производство (Sales and Operation Planning).
- Управление на търсенето.
- Съставяне на производствен план (Master Production Scheduling).
- Планиране на материалните изисквания.
- Спецификация на продукта (списък на материалите).
- Управление на склад (подсистема за транзакции на складови наличности).
- Подсистема за планирани постъпления.
- Управление на ниво производствен цех (Shop Flow Control).
- Планиране на капацитета (Capacity Requirement Planning).
- Контролен вход / изход (Input / Output Control).
- Логистика (закупуване).
- Планиране на ресурсите за разпределение.
- Планиране и контрол на производствените операции (Tooling g Planning and Control).
- Финансово планиране (Financial Planning).
- Симулация
- Оценка на резултатите от дейността (Performance Measurement).
IS, реализиран на базата на MRPII, е предназначен за ефективно планиране на всички ресурси на предприятието (включително финансови и човешки ресурси). Основната същност на концепцията MRPII е, че прогнозирането, планирането и контролът на производството се извършват през целия жизнен цикъл на продуктите, от закупуването на суровини до доставката на продуктите до потребителя.
Задачата на информационните системи от клас MRP II е оптималното формиране на потока от материали (суровини), полуготови продукти (компоненти) и готови продукти. Системата има за цел да интегрира основните процеси, изпълнявани от предприятието: планиране и наблюдение на изпълнението на плана, разходи, доставки, производство, продажби, управление на запасите, зареждане на дълготрайни активи и др.
В такава система са интегрирани голям брой модули, резултатите от които се анализират от системата MRPII като цяло, което осигурява нейната гъвкавост по отношение на различни външни фактори - например текущото търсене на продукти, ценови котировки и т.н. (Фигура 10.1).
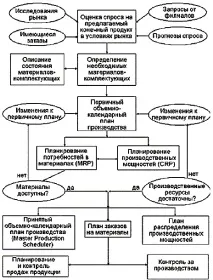
Ориз. 10.1. Общата схема на планиране на ресурсите за производствено предприятие
В резултат на прилагането на стандарта MRPII се реализират:
- своевременно получаване на информация за текущите резултати на предприятието, както общо, така и с пълна информация за отделни поръчки, видове ресурси, изпълнение на планове;
- дългосрочно, оперативно и детайлно планиране на предприятието с възможност за коригиране на планираните данни въз основа на оперативна информация;
- оптимизиране на производствените и материалните потоци със значително намаляване на непроизводствените разходи и реално намаляване на материалните ресурси в складовете;
- връщаненаправени инвестиции в информационни технологии;
- възможността за поетапно внедряване и развитие на системата, като се вземе предвид инвестиционната политика на конкретно предприятие;
- отразяване на финансовата дейност на предприятието като цяло.
В момента стандартът MRPII е основата за разработване на ядрото на стандартизирана ERP система.