Отстраняване на леярски дефекти с DIMET
За елиминиране надефекти в отливкитехнологията DIMET се използва широко в предприятия, произвеждащи сложно оборудване, използващоотливкиот леки сплави, предимно при елиминиране надефекти в алуминиеви отливки.
Предимствата на газодинамиката при ремонт на отливки
Първо, той ви позволява да елиминирате основнитедефекти на отливките в отливките,като кухини, фистули, порьозности, локални течове и други, включително веднага след откриването надефектиотливкии по този начин да намалите процента на първичните бракувани (намаляване с 25-40%).
Впо-долу3 снимки, етапите на добавяне на металкъм формата.
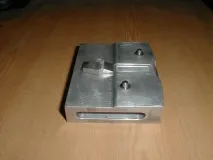
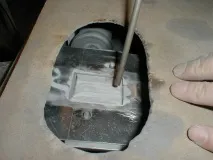
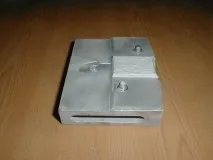
Второ, и което е по-важно, това ви позволява да елиминирате скрититедефекти на леярството, които се откриват по време на машинната обработка на отливките. В този случай цената на частта се увеличава значително и съответно корекциятана дефектната отливкае много важна. Възможността за запазване на отлятата част, и което е важно - без влошаване на техническите характеристики и промяна на оригиналната форма, осигурява значителна икономическа изгода. Трябва също да се отбележи, че е възможно да се елиминиратдефекти в отливките, които възникват по време на обработката поради грешки на персонала: подценяване на размерите, неправилно пробиване на отвори и др.
Трето, технологията на CGN(студено газодинамично пръскане)ви позволява да коригиратедефекти в отливките, да повредите или промените геометрията на моделите, използвани при производството на части според инвестиционните модели.
Успешното приложение на технологията DIMET прикоригиране на дефекти в отливки и шприцформисе състои в образуването на метални покрития на базата на фиксиране на твърди истудени метални частици върху повърхността на детайла по време на свръхзвуков удар. Основното предимство на тази технология е, че по време на нанасянето на метални покрития няма значителен топлинен ефект нито върху напръсканите метални частици, нито върху детайла: температурата на детайла в зоната на покритие не надвишава 60-70, рядко 100-150 0 C. В резултат на това по време на такава обработка:
- няма процеси на окисляване на покритията и отливките;
- няма структурни промени в материала на отливката;
- няма деформации и изкривяване на детайла;
- няма вътрешни напрежения в покритата част;
- нанасянето (натрупването) на метални покрития се извършва на място за пръскане с площ от 0,5-1 cm 2, без да се засягат други части от повърхността на детайла. За да намалите площта на приложение, можете да използвате шаблон;
- дебелината на покритието може да бъде всяка.
Отделна тема е ремонт на форми, дорници и др. при производството на детайли от пластмаса, гума, стъкло.
Особено икономически оправдано е използването на технологията DIMET при отстраняване налеярски дефектина тънкостенниотливкисъс сложна геометрия. Практиката на използване на технологията и оборудването DIMET показва, че тя е най-подходяща за решаване на подобни проблеми в сравнение с всички традиционни технологии.
Възможно е да се отстранят някоилеярски дефектив детайли от стомана и чугун, но в този случай могат да се използват само алуминиеви и медни покрития. В резултат на това могат да бъдат елиминирани само дефекти на леене, при които покритието няма да изпита значителни механични въздействия, т.е., на първо място, премахване на течове и възстановяване на търговски вид.
Ограничения за използването на DIMET при коригиране на дефекти при леене:
- покритията имат много ниско относително удължение и не могат да се използват, когато се прилагат сили на опън и огъване; но само за компресия и срязване. Това означава, че напуканите отливки не могат да бъдат съединени чрез пръскане. Един подход е да се използва точково заваряване, за да се коригира пукнатината.
- могат да се поправят само дефекти, които могат да бъдат достигнати от пръскащата дюза.
- технологията не позволява нанасяне на метални покрития от твърди метали.
Като примери са представени типични образци на части,леярски дефективърху които са елиминирани с помощта на оборудване DIMET.
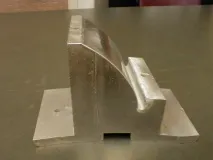
Обратна връзка от НПО "Сатурн" за ремонт на дефектни отливки с DIMET: