Пълнене на форми и отливане на нокаут - Здравей ученик!
За да получите качествена отливка, трябва да излеете метала във форми при правилната температура.
Времето за изливане се определя от естеството и размера на запълващата се форма, като задължителното условие е разтопеният метал да се вкарва във формата възможно най-плавно, без удар.
Количеството разтопен метал в килограми, преминаващо през 1 cm 2 от напречното сечение на леяк за 1 секунда, се нарича специфична скорост на изливане.
Специфичната скорост на леене в мокра форма ще бъде значително по-малка, отколкото при сухо леене. Специфичната норма на наливане на мокро варира от 0,40 до 0,65, а на сухо - от 1,50 до 2,00 и повече.
Температурата на метала, когато се освобождава от пещта, не трябва да се бърка с температурата, която металът има, когато се излива във форми. Освободеният от пещта метал трябва да бъде възможно най-добре прегрят и да се излее във форми при възможно най-ниската температура. Така че, по-специално, силното прегряване на чугун в пещ е желателно: 1) за да може да се пренесе в кофи на възможно най-голямо разстояние от мястото на топене; 2) за подобряване на механичните свойства, тъй като прегряването допринася за образуването на по-фини зърна от графит. Изливането на чугун във форми при силно прегряване е нежелателно, тъй като колкото по-висока е температурата на метала, толкова по-голямо е свиването му и толкова повече газове ще се разтворят в него, което ще доведе до образуването на голям брой кухини на свиване и по-голямо кипене.
Формите с тънки стени се пълнят с по-прегрят метал, а с дебели - с по-студен.
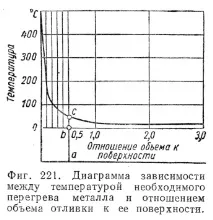
На фиг. 221 е диаграма, показваща връзката между температурата на прегряване на метала и съотношението на обема на отливката към нейната повърхност (колкото по-тънки са стените на формата, толкова по-малкоще има тази връзка). Абсцисата на диаграмата показва отношението на обема на формата към повърхността, а ординатата показва стойността на прегряване в градуси. Числените стойности на диаграмите са дадени за конкретен случай - за чугун. Точка a съответства на температурата на топене на чугун с определен състав; сегмент ab показва степента на охлаждане на метала по време на прехвърлянето на чугуна от купола до най-отдалечената форма; сегментът bс е стойността на необходимото прегряване в зависимост от отношението на обема на формата към повърхността. На практика температурата на чугуна по време на изливане във форми трябва да бъде в диапазона 1250-1400 °.
Разтопеният метал се подава към формата в кофи.
Леярските кофи се изработват от листово желязо; дебелината на листовете за страничните стени е 6-8 мм, за дъната - 10-12 мм. Кофите обикновено се изработват заварени, щамповани или занитени и покрити с огнеупорен материал отвътре. Дебелината на огнеупорния слой за малки кофи трябва да бъде най-малко 20 mm) Кофите, съдържащи повече от 5 тона метал, са облицовани с огнеупорни тухли отвътре.
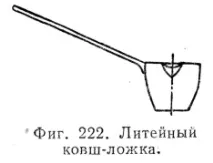
Огнеупорният слой трябва да бъде добре изсушен; не трябва да се допуска образуването на пукнатини в покритието на черпака, тъй като металът, прониквайки в пукнатината, може да разтопи металната част на стената или дъното на черпака.
Малките кофи, обслужвани от един работник, са с вместимост 15-20 кг; те се наричат лъжици или лъжички (фиг. 222).
Кофите с лостове се използват за изливане на голямо количество метал (фиг. 223, а). Капацитетът на такива кофи достига 150 кг; обслужват се от няколко работници.
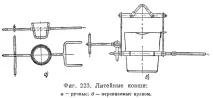
Кофите с голям капацитет се преместват с кранове. На фиг. 223, b показва устройството на такава кранова кофа.
За предпазване на метала от бързо охлаждане, отпадъци, както и за изолиране на блясъка на повърхността на разтопения метал ипламъци върху него, които имат вредно въздействие върху работниците, леярските кофи понякога получават формата на барабани. Такива барабани се поставят на колички или се окачват на кранове. Разположението на барабана за изливане е показано на фиг. 224.
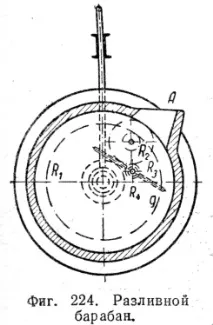
За да предпазите формата от навлизане в нея на различни отломки, плаващи по повърхността на метала, запълващ черпака, тези отломки понякога се забавят с дървен прът или шпатула. В големите черпаци за този делхи устройствата са подредени под формата на преграда, намазана с глина, поставена пред гърлото на черпака (фиг. 225).
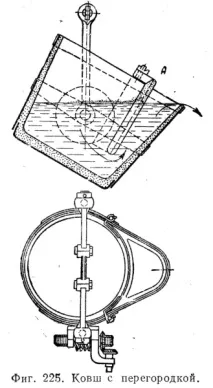
При запълване на формата с метал започва неговото втвърдяване, след което в твърдо състояние металът се охлажда.
Ако отливката е със значителни размери, е необходимо нейното охлаждане да протича равномерно във всички части; За да направите това, понякога охлаждането на по-масивните части на отливката се ускорява, освобождавайки ги от формовъчния материал, а охлаждането на тънките части се забавя, оставяйки ги неотворени.
По време на охлаждането в отливката възникват вътрешни напрежения, които ще бъдат толкова по-малки, колкото по-бавно става охлаждането, и колкото по-големи, колкото по-сложна е формата и колкото по-големи са размерите на отлятия обект. Следователно големите отливки не трябва да се изваждат бързо от формата.
Големите артикули обикновено се охлаждат на мястото за отливане, докато по-малките артикули във вградените леярни се подават в секцията за избиване.
В последния случай отливките се охлаждат частично по време на транспортиране и частично в секцията за избиване. Процесът на освобождаване на отливката от формата се нарича нокаут.
Когато започвате да избивате чугунени и стоманени отливки, трябва да се помни, че отливката не трябва да се излага, ако температурата му не е паднала под 700 °, тъй като само след тази температура спират структурните промени в сплавите желязо-въглерод.
За да се избият големи отливки, първо горната колба се повдига с кран, след това долната колба и формовъчният материал и отливката се избиват от колбата с удари с чук. Понякога се използват пневматични вибратори за избиване на плесени. Вибраторът хваща колбата с челюстите си и след като се задвижи, започва бързо да я разклаща. С помощта на вибратор значително се намалява процесът на избиване на големи форми. Малки колби се поставят върху решетки за разклащане, задвижвани от пневматичен цилиндър или електрически мотор.
Отливката, извадена от матрицата, обикновено има много придатъци (издатини, издутини, неравности, филми от метал, захванати между частите на матрицата, шпилки); в допълнение, отливката често е замърсена с формовъчен материал, изгорен до повърхността му; следователно следващите операции след избиване са отчупване и почистване на отливката.
Почистването на отливката започва с избиване на сърцевините, които могат да се избиват на ръка или при големи сърца със специално направени за целта пневматични чукове. Тази работа се извършва върху решетки, поставени в пода, или върху работни маси с решетки; под решетките се поставят прахосмукачки.
Отстраняването на лея, лея, щрангове и филми се извършва с длета (ръчни или механични), триони на различни устройства или газово рязане. Отливката се почиства от полепнал по повърхността й формовъчен материал с метални четки. За ръчна работа се използват четки, които представляват сноп краища на тел, напълнени с олово от едната страна и свободни от другата страна. За механично почистване четките са изработени под формата на диск и се задвижват от електродвигател.
За почистване на повърхности, където формовъчният материал е особено изгорен, се използват абразивни колела.
Замалките отливки се почистват с помощта на въртящи се барабани, в които продуктите за почистване се поставят заедно с едър пясък; бели чугунени зъбни колела, специално направени за тази цел, понякога се добавят към пясъка. Когато барабанът се върти, продуктите се сблъскват помежду си, както и с пясък и чугунени или стоманени зъбни колела и по този начин се извършва почистването.
Недостатъците на този метод включват понякога възникващото счупване на ръбовете на почистваните продукти.
Устройството на почистващия барабан е показано на фиг. 226. При механизирано товарене целият процес на почистване с товарене и разтоварване продължава от 1 до 2 1/2 часа. (в зависимост от степента на замърсяване на продуктите).
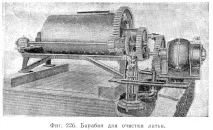
За да се предотврати счупване на ръбовете на почистваните продукти, се подреждат барабани с много бавно въртене (около един оборот в минута). Понякога в барабаните се впръсква струя пясък, която всъщност почиства продуктите, а чрез въртене на барабана се постига само обръщане на заредените предмети.
В барабаните за пясъкоструене могат да се почистват относително малки предмети. Пясъкоструйните машини се използват за почистване на големи предмети, давайки силна струя пясък. Пясъкоструйните машини могат да се използват и за избиване на пръти.
Тъй като по време на почистването на отливки с пясъкоструйни устройства се оказва: голямо количество прах, работата обикновено се извършва в специални камери. Понякога отливките се монтират на въртяща се маса вътре в камерата, като работник остава извън камерата и оттам насочва дюзата на пясъкоструйката през прозореца.
В момента вместо пясък в устройства, работещи на принципа на пясъкоструене, се използват стоманени и чугунени изстрели с различни диаметри. Тази замяна на пясъка има следните предимства: шот, в сравнение с пясъка, сервирапо-дълго (приблизително 60 пъти), действа по-силно върху повърхността на почиствания продукт и произвежда по-малко прах.
В резултат на това използването на метални сачми дава освен редица удобства и спестяване на разходи.
Напоследък се използва хидравличен метод за почистване на отливки. При почистване по този метод струя вода се насочва към почистваната повърхност под силно налягане, което в някои инсталации достига до 100 атм. Продуктите се поставят в камерата, а работникът е извън нея.
Голямото количество прах и наличието на метални фрагменти, отскачащи от детайлите, налагат специални мерки за защита на работниците, заети в отделите за подрязване и почистване на леярните.
работилници; на работни маси се използват специални предпазни устройства от телена мрежа; избиващите решетки са оборудвани с устройства за прахоотвеждане; работата се извършва в защитни очила; особено вредни за здравето на работещите, въпреки взетите мерки за защита, са пясъкоструйните машини, поради което са забранени в редица леярни.
Изтегляне на резюме: Вие нямате достъп за изтегляне на файлове от нашия сървър. КАК ДА ИЗТЕГЛЯТЕ ТУК