Повърхностни дефекти на големи стоманени блокове
Повърхностни дефекти
Качеството на голям стоманен блок се определя от чистотата на стоманата, нейната физическа и химическа хетерогенност, както и наличието на повърхностни и вътрешни дефекти. В големи слитъци линейните размери на дефектите могат да варират от няколко метра (сегрегационни дефекти и пукнатини) до няколко десетки микрометра (натрупвания на неметални включвания). Редица дефекти са доста трудни за идентифициране директно в слитъка (чрез методи за безразрушителен контрол). Това всъщност води до факта, че проявата на тези дефекти се случва или в коването, или в готовия продукт. На практика, за да се получат висококачествени блокове, те се стремят да оптимизират системата от параметри за топене, обработка на кофа и леене на стомана, като се вземат предвид специфичните изисквания към продукта.
Повърхността на слитъка до голяма степен характеризира неговото качество, тъй като дефектите, образувани върху него, остават по време на последващата обработка на заготовката. Повърхностните дефекти на слитъците проникват дълбоко в тялото с няколко милиметра (5-20 mm) и се появяват по време на последващото им коване и механична обработка под формата на счупвания на повърхността на получените заготовки и продукти. Отстраняването на тези дефекти (чрез рязане, пожар или студено почистване) е една от най-отнемащите време операции при обработката на детайлите (фиг. 6.1). Въпреки това не винаги е възможно напълно да се премахнат установените дефекти.
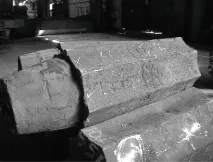
Фигура 6.1. - Общ изглед на ковашки слитъци с повърхностни дефекти
Образуването на повърхностни дефекти възниква по време на пълненето на формата и по време на втвърдяването на външните слоеве на блока. Основните повърхностни дефекти се считат за: плен, горещи пукнатини, колани, субкортикални мехури, отпечатъци от мрежатакалъпи и др.
Дебелината е един от най-често срещаните и доста трудни за отстраняване типове дефекти на повърхността на слитъка. Те представляват участъци от повърхността на слитъка, върху които ясно се вижда кората, образувана в резултат на изливането (фиг. 6.2). Основната причина за възникването на този тип дефекти е интензивното образуване на пръски по време на запълването на формата с метал. Металните пръски, които удрят стените му, бързо се втвърдяват и окисляват. В процеса на изливане отгоре процесът на образуване на пръски протича особено интензивно в момента на удара на струята течна стомана върху съда или дъното на формата. Значително намаляване на разпръскването на струята може да се постигне чрез избор на рационална форма на дъното на слитъка.
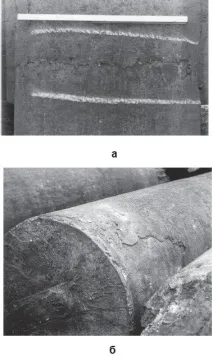
Фигура 6.2- Филми върху повърхността на многостенни (a) и кръгли (b) слитъци
Образуването на плен се улеснява от небрежното сглобяване на канавката: изместването на оста на резервоара спрямо оста на матрицата, наклонената инсталация на дюзата за изливане и др.
Смята се, че увеличаването на скоростта на леене води до намаляване на броя на филмите, тъй като в този случай стоманената кора на повърхността на формата е заварена към тялото на слитъка без образуване на дефект. Склонността на филмите към варене зависи от интензивността на два едновременно протичащи процеса - скоростта на втвърдяване и скоростта на окисление на филма. Захващането се заварява със слитъка, ако нивото на течния метал се е повишило и влиза в контакт с него, докато захващането се втвърди напълно.
Радикално решение на проблема с подобряването на чистотата на повърхността на слитъка се осигурява от прехода към сифонно леене на стомана. Въпреки това, в процеса на сифонно леене, могат да се образуват петна, когато металът тече във формата с висока скорост. Задържане в плен възниква и когатокогато има разпръскване на метал към стените на матрицата на изхода на крайната сифонна тухла. На практика като технологични мерки за борба с филмите по време на леене на сифон се използват повишаване на температурата на леене на стомана, увеличаване на изходния отвор на крайната сифонна тухла, както и леене под топлоизолационни смеси. Леенето на блокове под вакуум до голяма степен елиминира образуването на плен, т.к. струята, протичаща във вакуум, се разбива на множество малки капки и струйки и пръскането от удара в тигана спира. Отсъствието на окислителна атмосфера също влияе благоприятно върху качеството на повърхността на блока. Но при изливане във вакуумна камера е необходимо да се следи подравняването на струята по оста на формата и да се вземат мерки за предотвратяване на прекомерното й отваряне.
Наличието на манган намалява вредните ефекти на сярата поради факта, че феромангановите сулфиди са по-огнеупорни и присъстват в стоманата в твърда форма при по-високи температури от железните сулфиди. Склонността на стоманата да образува горещи пукнатини намалява с увеличаване на съотношението Mn/S. Според много изследователи, за да се предотврати образуването на горещи пукнатини, е необходимо да има съотношение Mn/S > или = 20-30.
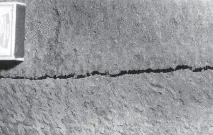
Фигура 6.3– Общ изглед на надлъжна пукнатина върху повърхността на листов слитък с тегло 30 тона
Причините за прекъсването на втвърдяващия се метал под формата на повърхностни пукнатини са следните. Когато течната стомана влезе във формата, тя бързо се охлажда до температурата на ликвидус поради интензивно отстраняване на топлината от студени стени, след което започва процесът на бързо нарастване на твърда кора. В резултат на рязко понижаване на температурата, повърхностните слоеве на слитъка се компресират, но това се предотвратява от по-горещовътрешни слоеве с по-малко свиване, както и сили на триене между повърхността на блока и стените на формата. Това води до високо ниво на термични напрежения и напрежения при свиване в неговата здрава рамка. Тъй като между стените на формата и слитъка се образува празнина, в нейната кора се появяват напрежения, причинени от феростатично налягане. Тези напрежения достигат максималната си стойност в момента на пълното изтегляне на кората от вътрешната повърхност на формата.
С образуването на газова междина между слитъка и формата, преносът на топлина към формата рязко намалява и охлаждането на външните слоеве на слитъка значително се забавя. По-дълбоките слоеве с температура по-висока от тази на външните слоеве им дават топлината на прегряване и латентната топлина на кристализация, като същевременно се охлаждат с по-високи скорости от външните.
По този начин основната причина за образуването на горещи надлъжни пукнатини трябва да се счита за високо ниво на напрежения на свиване, които възникват, когато свиването на блоковете във формата е забавено и по време на неравномерно свиване по височината и периметъра на блока. Образуването на такива пукнатини е свързано с температурата на изливане и нейното повишаване увеличава вероятността от образуване на пукнатини. Горещи пукнатини също често се появяват, когато има различни дефекти по вътрешната повърхност на формите, които увеличават триенето между стените му и блока и възпрепятстват свиването.
Значително влияние върху появата на пукнатини оказва дизайнът на вътрешната кухина на матрицата - формата на напречното сечение, радиусите на ъглите, конусността. Установено е, че пукнатини се образуват, като правило, на места с трудно отвеждане на топлината от слитъка. Трябва да се има предвид, че доброто отвеждане на топлината се възпрепятства от получената газова междина между блока и формата. Образува се първо в горната част на слитъка, къдетоферостатичното налягане върху кората е малко и след това последователно се придвижва към средата на слитъка и най-накрая до дъното.
Много изследователи отбелязват, че концентрацията на напрежение възниква в определени области на повърхностния слой на слитъка. Такива области в близост до слитъка са ъглите, където газовата междина се образува по-рано поради интензивно двуизмерно отстраняване на топлина, отколкото по ръбовете. Известно е, че колкото по-голям е радиусът на кривина на ъглите на слитъка, толкова по-малко издръжлива е твърдата кора и толкова повече надлъжни и ъглови пукнатини се получават по време на свиването на слитъка.
До известна степен величината на напреженията, възникващи в кората, може да се контролира чрез промяна на вътрешния профил на стените на формата. Склонността към пукнатини може да бъде намалена чрез увеличаване на периметъра на сечението на формата при постоянна площ. По този начин придаването на лицето на слитъка на определена изпъкналост спомага за намаляване на напреженията на опън, възникващи под действието на феростатично натоварване. От металургичната практика е известно също, че блоковете с вдлъбнати фасети също са по-малко склонни към образуване на надлъжни пукнатини.
Бързото охлаждане на слитъци до температури под 500-600°C води до образуването нанадлъжни студени пукнатини поради неравномерно компресиране на различни метални слоеве.
Напречни пукнатини възникват в случай на така нареченото "окачване" на блокове по време на образуването на заливи (фиг. 6.4), изгоряла облицовка на удължението на щранга към главата на блока, както и при наличие на издатини, вдлъбнатини и грапавост в матрицата, предотвратявайки естественото свиване на блока. Поради препятствието за свободно свиване, в този случай възникват значителни напрежения на опън, якостта на кората става недостатъчна и на повърхността на блока се образуват напречни пукнатини (фиг. 6.5).
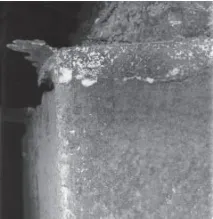
Фигура 6.4- Наводнение, образувано върху голям листов слитък в резултат на метал, протичащ под изгодно разширение
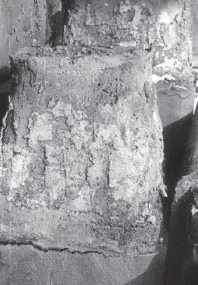
Фигура 6.5- Общ изглед на напречната пукнатина, образувана, когато слитъкът виси във формата
В случай на временно спиране на изтичането на стомана в процеса на запълване на матрицата, върху слитъка по периметъра се образува така нареченият "колан " (фиг.6.6). При изливане на студен метал при ниска скорост могат да се натрупат мехурчета и неметални включвания близо до повърхността на слитъка, което също причинява колани. За да се предотврати образуването на този дефект, скоростта на леене трябва стриктно да съответства на температурата на отливаната стомана.
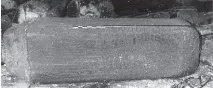
Фигура 6.6- "Колани" на повърхността на долната част на цъфтящия слитък
Подкоровите мехури (Фиг.6.7) са разположени между равноосните фини дендритни кристали на повърхностната зона и зоната на колонните кристали на дълбочина до 15 mm. Газовите мехурчета в подкоровата зона на слитъка, като правило, причиняват появата на дефекти, когато заготовките са разстроени под пресата.
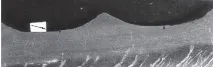
Фигура 6.7- Подкоркови мехури близо до повърхността на листов слитък с тегло 27 тона (напречно сечение на слитъка)
Появата на газови мехурчета в кристализирал метал обикновено се свързва с отделянето на въглероден окис в началния период на втвърдяване на блока. Големите удължени мехурчета са придружени от голям брой неметални включвания като сулфиди и стъкловидни силикати. Установено е, че процесът на образуване на подкоркови мехурчета в слитъци от спокойна стомана е особено интензивен при недостатъчно дезоксидиране и повишено съдържание на водород в него, както и при неправилно боядисване или проникване на влага в порите на вътрешната повърхност.плесени.
По време на сифонно леене на стомана с помощта на шлакообразуващи смеси, повърхността на слитъка е засегната от шлакови включвания или остатъци от неразтопена смес. Наличието на такива включвания също е една от причините за появата на субкортикални мехури.
Основните начини за предотвратяване на подкоркови мехурчета са правилното дезоксидиране на стоманата и нейното обезгазяване преди леене чрез вакуумиране, както и почистването на формите, използването на оптимални състави на покрития върху вътрешната повърхност на матрицата (те трябва да осигурят добро намокряне на стените на формите с течен метал), добре установено наблюдение на състоянието на формите и тяхното навременно отхвърляне в случай на откриване на значителни дефекти.
Ако подкоровите мехурчета, разположени в дълбоките слоеве на метала, нямат връзка с повърхността на слитъка, не са замърсени с сегрегати и неметални включвания, тогава те обикновено се заваряват по време на коване или валцуване.
Степента на увреждане на повърхността на слитъка от дефект тип "газови мехурчета" се увеличава, когато се излива студен метал. Въпреки това, както беше отбелязано по-рано, високата температура на отлятата стомана води до горещи пукнатини по повърхността на блока.
Намаляването на температурата на леене на стоманата под оптималната, както и намаляването на скоростта на леене води до появата на дефект "обръщане на кората". Проникването на окислената кора в слитъка води до образуване на мехурчета и замърсяване на стоманата с неметални включвания. По време на коване и валцуване обръщанията на кората допринасят за образуването на пукнатини.
Особено груби обръщания се получават при запълване на формата с метал с прекъсвания на струята.
Отпечатъкът от решетката на огъня (фиг. 6.8) е следствие от частичното разрушаване на вътрешната повърхност на калъпа. Такова разрушаване на плесента води до промяна в нейнатавътрешна конфигурация в напречното сечение и съответно води до нарушения на геометричната форма на слитъка. Възможните последици от това са технологични затруднения при изваждането на слитъка от формата, както и неговото "увисване" по време на процеса на охлаждане. На практика при установяване на такъв дефект вътрешната повърхност на формата се ремонтира или формата се заменя с нова.
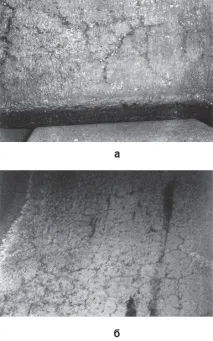
Фигура 6.8– Огнена решетка върху вътрешната повърхност на формата (a) и причинените от нея дефекти на повърхността на блока (b)