TOPP_ch1 - Страница 6
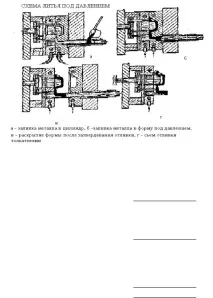
Най-точният метод за леене, който осигурява отливки, които в много случаи не изискват допълнителна обработка,
леене под налягане.
се шприцова във формата и се втвърдява под налягане от
20 до 1000 ати какво
осигурява ниска порьозност
метал (фиг. 4.6). Въпреки това, стените
формите са изключително
топлинни натоварвания, т.н
стоманените форми се използват за отливане на сплави на базата на алуминий, цинк и мед по този метод. Леенето на стомана по този метод е възможно само във форми, изработени от топлоустойчиви сплави на базата на молибден. Трудностите при направата на матрицата, високата й цена я правят рационална за използване
в сериен - маса
производство, обикновено
метални части на домакински уреди (ключалки,
дръжки за врати и прозорци, детайли
превозни средства, шасита на електронно оборудване и др.).
Сравнителна характеристика на различни методи за леене
Форма и размери
, от маса до
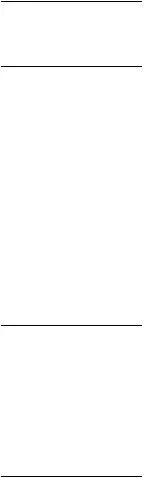
размер и форма
Тегло до 250 кг,
тегло до 10 кг, в
Въпроси за самопроверка:
1. Какъв метод на леене осигурява най-висока точност на получената отливка?
2. Кои методи за отливане не изискват изработка на модел?
3. Какви са предимствата на леенето в сравнение с други методи за получаване на заготовки за машинни части?
4. Какви продукти се произвеждат чрез центробежно леене?
5. Какви са предимствата на леенето под налягане?
6. От какви сплави се изработват шприцформите?
7. С какъв метод на отливане може да се получи отливка на легло на машина с дължина 10m и маса 10 тона?
8. Какъв метод на леене е препоръчително за отливане на кутии за брави от алуминиева сплав?
9. Какво физическофактори определят течливостта на сплавта, когато тя запълва формата?
10. От какви материали е изработена шприцформата?
Примерна карта за контрол на теста:
1. По какъв метод на леене е препоръчително да се получи отливка от силумин с маса
10 kg с точност на размерите според клас 12: a). Отливане в калъп b). леене под налягане c). Инвестиционно леене
2. Какъв метод се използва за направата на художествено отливане от бронз:
А). Леене под налягане b). леене под налягане
V). Инвестиционно леене
3. Кои методи за леене не използват пръчки: а). при леене под налягане b). При леене по модели в). При леене под налягане
4. Какъв метод на леене е невъзможно да се произведе маса за леене на стомана
200 кг а). Леене под налягане
б). Леене в черупкови форми c). Леене в калъп
5. Какъв метод на леене осигурява производството на отливки с най-сложна форма а). Шприцоване
б). леене под налягане c). Инвестиционно леене
5. Методи за формоване на метали
Поради пластичността на металите, която се проявява по време на деформация в студено или горещо състояние, е възможно да се промени формата на оригиналния детайл, получен естествено по друг метод.
Възможността за обработка на метали чрез налягане до голяма степен определя тяхното широко приложение. Това технологично свойство е толкова важно, че дори е в основата на определението за метал (Металът е леко тяло, което може да се кове).
По време на пластичната деформация на метала атомните слоеве се изместват един спрямо друг вътре в кристалите и кристалите се изместват един спрямо друг. Важна характеристика на този вид деформация е липсата на разрушаване. Разбира се различни метали и технитесплавите имат различна способност да се деформират без счупване. Пластичността на металите се оценява по стойността на относителното удължение на стандартната проба при скъсване. Тази стойност за пластичните метали варира от 10 до 50%. Понастоящем са разработени суперпластични сплави, чието относително удължение при скъсване може да достигне стотици проценти.
Сплавите с висока пластичност, които могат да се обработват чрез методи под налягане, включват: нисковъглеродни стомани, сплави от алуминий, мед (месинг), много легирани стомани.
Пластичността на металите се увеличава значително, когато се нагряват, поради което обработката под налягане се извършва главно в "горещо" състояние. При нагряване якостта на металите също значително намалява, така че силите за тяхната деформация са много по-ниски, което позволява използването на по-просто оборудване и инструменти.
Най-разпространените технологични методи за формоване на метали са: валцуване, пресоване, изтегляне, коване, щамповане.
Повече от 80% от произведената стомана и около 50% от цветните метали се обработват чрез валцуване. По този начин (фиг. 5.1) се получават дълги заготовки с определен профил - асортимент. Тези продукти служат като заготовки за производство на различни машинни детайли или имат собствено приложение - тръби, шини, профили за строителни конструкции.
Чрез валцуване се получава листов материал, който след допълнителна обработка се използва за производство на корпуси на кораби, машини, самолети и др.
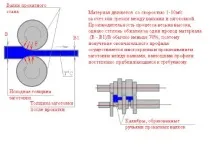
Оборудване - валцови мелници.
Мелниците за производство на заготовки за последващо производство на асортимент се наричат цъфтящи, а за производство на заготовки за последващо валцуване на листове - плочи. Като заготовки на тези мелнициизползват се слитъци. Естествено, за да се намали консумацията на енергия, е рационално слитъците да се валцуват в горещо състояние, след като металът е излят и втвърден. Следователно, такива мелници обикновено се инсталират в металургични заводи, които произвеждат (варят) сплав (стомана).
Технологични възможности на валцуване
1. Възможно е да се валцуват само пластични метали в горещо или студено състояние (фолиото е продукт от студено валцуване на чист алуминий).
2. Форма. Формата (Фигура 5.2) може да бъде доста сложна, но има значителни ограничения, свързани с условията за преминаване на метала през валцоващите ролки. Трудно е да се получат повърхности, перпендикулярни на осите на ролките, така че е необходимо да се предвиди специален наклон на такива стени. Трудно е или понякога невъзможно да се получат асортиментни профили със затворени, затворени повърхности.
3. Размери. Диапазонът от размери (дебелини) на валцувания метал е доста широк. От плоча (>200 mm) до фолио до
4. Точност. Ако при горещо валцуване точността е десети от мм, което отговаря на квалификациите за точност, то при валцоване без нагряване точността може да бъде значително по-висока и при валцоване фолиото достига хилядни от милиметъра.
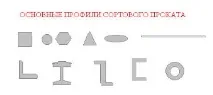
5. Грубост. Зависи и от наличието на нагряване, като при горещо валцуване грапавостта е значително по-висока (до Rz 320), докато при студено валцуване (фолио) може да се получи много ниска грапавост (по-малко от Ra0,63).
Пресоването е процесът на екструдиране на метал от затворена кухина (контейнер) през профилния отвор на матрицата (фиг. 5.3).
Оборудване. Хоризонтални и вертикални хидравлични преси с усилие тонове.
Матрици, поансони за пресованеса изработени от изключително здрави стомани и сплави, тъй като налягането при пресоване е много високо. Следователно, този метод произвежда предимно продукти от алуминиеви и медни сплави.
Формата на получения профил може да бъде много сложна, този метод осигурява най-сложните профили, като оребрени тръби за топлообменници, строителни профили (рамкови профили от леки сплави).
Точността и качеството на повърхността на получените профили също са много високи, тъй като те практически се определят от качеството на матрицата, чиято точност и грапавост на повърхностите могат да бъдат постигнати в производствения процес. Разбира се, по време на работа матрицата се износва, което влошава горните параметри на продукта.
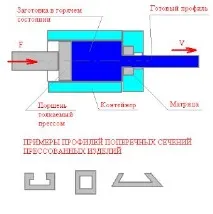
Процесът на компресиране на метала на детайла, докато го издърпвате през матрицата, е инструмент с отвор, чието напречно сечение е по-малко от първоначалното сечение на детайла (фиг. 5.4).
В резултат на процеса напречното сечение на детайла намалява и дължината
тя се увеличава. Изтеглянето се използва без нагряване на детайла, за да се получи тънък проводник (от 0,002 mm до 4 mm).
За един цикъл на компресия в матрицата е невъзможно значително да се намали напречното сечение на детайла, тъй като силата може да се приложи само към края на детайла, излизащ от матрицата, и при прекомерна сила жицата може просто да се счупи.
Чертежът може да се използва и за калибриране (с цел подобряване на точността) на пръти с различни профили, тънкостенни тръби и др.
Оборудването е специални мелници за изтегляне, на които телта може да получи няколко редукции в един цикъл.
Заготовките за изтегляне са продукти от валцоване (тел "валцована тел" с диаметър 6 mm).
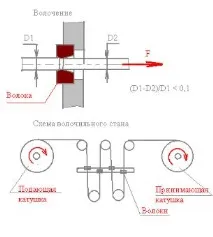
По чертеж, всички проводници за електроника и електроникапромишленост, стоманена тел за машиностроенето, строителството и др.
Точността на профила достига 6 степени, а грапавостта на повърхността може да бъде постигната под 0,32 µm.
Щанцовете, работещи в изключително натоварен режим и подложени на интензивна абразия, са изработени от свръхтвърди металокерамични сплави и кристали (диамант).
Коването е процес на гореща обработка на метали чрез натиск, при който заготовката се удря с чук, глава на чук, чрез натискане на пресова глава или друг универсален инструмент.
Първоначалният детайл по време на коване е слитък или валцуван детайл.
Понастоящем ръчното коване се използва при ремонтни дейности и художествена обработка на метали.
Машинното коване се извършва на машини:
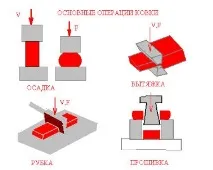
ковашки чукове с маса на падащи части от 0,5 до 16 тона, ковашки преси със сила от 500 до 100 000 тона.
Материал на детайла. Основното производство са стоманени изковки, които се коват при температура.Въпреки че цветните изковки се произвеждат в ограничена степен. Свойствата на материала по време на коване са значително подобрени, тъй като металните кристали се смачкват, изравняват
може да се създаде
Поради това в някои случаи се използва коване
в производството на заготовки
критични части на машини (валове, ротори на турбини, оръдейни цеви.). Формата на продуктите, получени в промишлеността, обикновено е много проста, въпреки че при художественото коване формата е ограничена само от въображението на художника.
Размерите на заготовките могат да бъдат много големи. Например коване на витлов вал на кораб, ротор на голяма турбина. Масата на изковките може да бъде десетки тонове. Разбира се, би било невъзможно да се деформира пластично такъв огромен детайл изцяло при липса на подходящооборудване, но по време на коване е възможна локална пластична деформация на детайла и, естествено, големите изковки се коват последователно в секции.
Точността на изковките съответства на степен 14 и по-груба, а грапавостта на повърхността обикновено е много висока (> 300 μm), така че изковките се обработват чрез рязане и други методи за получаване на машинни части от тях.
Използването на универсален инструмент за коване значително намалява разходите за предварително производство, така че коването се използва в индивидуално и дребно производство.
5.5 Горещо коване
По време на тази обработка металът на детайла се деформира изцяло и неговият поток е ограничен от кухината на щампата. В същото време формата
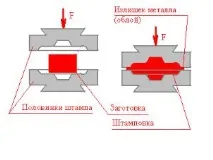
полученият продукт съответства на формата на щампата. Естествено, в сравнение със свободното коване, процесът е много по-продуктивен, но изисква производството на специални инструменти за матрици (фиг. 5.6).
Поради това се използва главно в серийно и масово производство.
Деформирането на целия обем на детайла изисква, въпреки нагряването му, значителни сили, действащи върху матрицата, така че размерите (масата) на детайлите обикновено са ограничени (по-малко от 250 kg).
Материалът при високи степени на пластична деформация, както и при коване, се уплътнява, зърното се раздробява, което води до подобряване на механичните свойства на продукта. Следователно процесът се използва при производството на заготовки за много важни продукти: валове, зъбни колела, турбинни лопатки и др.
Точността на получените заготовки също е много по-висока, отколкото при коването и достига 12 качество.
Грапавостта на повърхността, наличието на мащаб върху повърхността на нагрятия детайл е висока (100 - 500 микрона).
Обемното щамповане понякога се извършва на студеносъстояние и в този случай точността и грапавостта могат да бъдат значително подобрени. Въпреки това е трудно да се осигури голяма степен на пластична деформация на детайла и инструментът (матрицата) се износва бързо.
5.6 Щамповане на ламарина
Щамповането на листа е процес на деформация на заготовка на лист върху преса с помощта на щампа.
При щанцоване на поансон (фиг. 5.7) се получава разрез на материала между ръбовете на сложен контурен поансон и матрица, равноотдалечена от него по контура. Щанцото и матрицата са изработени от материали значително