Заваряване в защитни газове
Същността на метода
Заваряването в защитни газове може да се извърши с неконсумативен, обикновено волфрамов, или консумативен електрод. В първия случай заваръчният шев се получава чрез разтопяване на ръбовете на продукта и, ако е необходимо, телта за пълнене, подадена в зоната на дъгата. Консумираният електрод се топи по време на процеса на заваряване и участва в образуването на заваръчния метал. За защита се използват три групи газове: инертни (аргон, хелий); активни (въглероден диоксид, азот, водород и др.); смеси от газове от инертни, активни или първа и втора група. Изборът на защитен газ се определя от химичния състав на заварения метал, изискванията за свойствата на завареното съединение; икономическа ефективност на процеса и други фактори.
Препоръчва се и смес от инертни газове с активни за повишаване на стабилността на дъгата, увеличаване на дълбочината на проникване и промяна на формата на шева, металургична обработка на разтопен метал и повишаване на производителността на заваряване. При заваряване в смес от газове преходът на електродния метал в шева се увеличава.
Смес от аргон с 1-5% кислород се използва за заваряване с консумативен електрод на нисковъглеродна и легирана стомана. Добавянето на кислород към аргона намалява критичния ток, предотвратява образуването на пори и подобрява формата на заваръчния шев.
Смес от аргон с 10-25% въглероден диоксид се използва при заваряване с консумативен електрод. Добавянето на въглероден диоксид при заваряване на въглеродни стомани позволява да се избегне образуването на пори, до известна степен повишава стабилността на дъгата и надеждността на защитата на зоната на заваряване при наличие на течения и подобрява образуването на шев при заваряване на тънък метален лист.
Смес от аргон с въглероден диоксид (до 20%) и с не повече от 5% кислород се използва при заваряване с течен електрод на въглеродни и легирани стомани. Добавките от активни газове подобряват стабилносттаарки, образуване на шевове и предотвратяване на порьозност.
Смес от въглероден диоксид и кислород (до 20%) се използва при заваряване на въглеродна стомана с консумативен електрод. Тази смес има висока окислителна способност, осигурява дълбоко проникване и добра форма, предпазва шева от порьозност.
Смес от въглероден диоксид и кислород (до 20%) се използва при заваряване на въглеродна стомана с консумативен електрод. Тази смес има висока окислителна способност, осигурява дълбоко проникване и добра форма, предпазва шева от порьозност.
Защитният газ може да се подава централно към зоната на заваряване (виж фиг. XI.2 и XI.3, a, c), а при повишени скорости на заваряване с консумативен електрод - отстрани (виж фиг. XI.3, b). За да се спести потреблението на оскъдни и скъпи инертни газове, се използва защита с два отделни газови потока (виж фиг. XI.3, c); външният поток обикновено е въглероден диоксид. При заваряване на активни материали, за да се предотврати контакт на въздуха не само с разтопен, но и с нагрят твърд метал, се използват удължени дюзи (движещи се камери, виж фиг. XI.3, d). Най-надеждна защита се постига, когато продуктът се постави в стационарни камери, пълни със защитен газ. За заваряване на големи продукти се използват преносими камери, изработени от мека пластмаса, обикновено прозрачни материали, монтирани локално над заваръчното съединение. Топлофизичните свойства на защитните газове оказват голямо влияние върху технологичните свойства на дъгата, а оттам и върху формата и размерите на заваръчния шев. При равни условия дъгата в хелий, в сравнение с дъгата в аргон, е по-мека, има по-високо напрежение, а получената заварка е с по-малка дълбочина на проникване и по-голяма ширина. Въглеродният диоксид заема междинна позиция по отношение на ефекта си върху формата на шева.
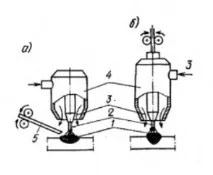
XI.2.Схеми на заваряване в защитни газове a, b - неконсумативен, консумативен електрод; 1 - заваръчна дъга; 2 - електрод; 3 - защитен газ; 4 - газова дюза (горелка); 5 - тел за пълнене
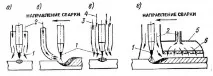
XI.3. Схеми за подаване на защитен газ към зоната на заваряване а - централно; b - страничен; c - два концентрични потока; g - в подвижната камера (дюза); 1 - електрод; 2 - защитен газ; 3, 4 - външни и вътрешни потоци на защитни газове; 5 - дюза; 6 - разпределителна решетка
Предимства и недостатъци на метода
Широката гама от използвани защитни газове прави този метод широко използван както по отношение на заваряваните метали, така и по отношение на техните дебелини (от 0,1 mm до десетки милиметри). Основнитепредимства на разглеждания метод на заваряване са следните:
- високо качество на заварени съединения на различни метали и техните сплави с различна дебелина, особено при заваряване в инертни газове поради малкия отпадък на легиращи елементи;
- възможност за заваряване в различни пространствени позиции;
- липса на операции по насипване и почистване на флюса и отстраняване на шлака;
- възможността за наблюдение на образуването на шев, което е особено важно за механизирано заваряване;
- висока производителност и лекота на механизация и автоматизация на процеса;
- ниска цена при използване на активни защитни газове.
Недостатъците на метода включват: необходимостта от прилагане на защитни мерки срещу светлината и топлинното излъчване на дъгата; възможността за нарушаване на газовата защита, когато газовата струя се издуха от движението на въздуха или когато дюзата се пръска; пръскане на метала, при което пръските са здраво свързани с повърхностите на шева и продукта; наличието на газово оборудване и в някои случаи необходимосттагорелки с водно охлаждане.
Подготовка на ръба и монтаж за заваряване
Методите за подготовка на ръбовете за заваряване (механични, газови и др.) са същите като при другите методи на заваряване. Видът на режещите ръбове и неговите геометрични размери трябва да отговарят на GOST 14771-76 или технически спецификации за производство на продукта. При механизирано заваряване с консумативен електрод е възможно да се получи пълно проникване без режещи ръбове и без празнина между тях с дебелина на метала до 8 mm. При разрязване или рязане на ръбове се постига пълно проникване с дебелина на метала до 11 mm. При автоматично заваряване на челни съединения производителността на процеса се увеличава значително, когато се използва жлеб без скосени ръбове (жлеб на шлица, виж фиг. X.11). При дебелина на метала до 40 мм, разстоянието между ръбовете в долната част на фугата е до 10 мм. За да се осигури постоянството на празнината в зоната на заваряване поради напречно свиване по време на заваряване на всеки проход, частите са шарнирно закрепени с ъгъл на отваряне на ръба в зависимост от дебелината на заварения метал.
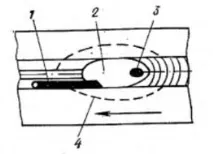
XI.11. Разположението на телта за пълнене спрямо заваръчната вана 1 - тел за пълнене; 2 - заваръчен басейн; 3 - електрод; 4 - граници на струята на защитния газ. Стрелката показва посоката на заваряване
При заваряване с въглероден диоксид на многослойни заварки на стомани, преди нанасяне на следващия слой, повърхността на предишния слой трябва да бъде добре почистена от пръски и образуваща се шлака. За да се намали пръскането върху повърхността на част от въглеродна стомана, тя е покрита със специални аерозолни препарати като "Arc". Заваряването може да се извърши с мокра подготовка. Частите се сглобяват с помощта на скоби, клинове, скоби или скоби. Захващанията се правят най-добре в защитни газове по същия начин, по който ще се извършва заваряването.Прихватите се проверяват преди заваряване и се усвояват по време на заваряване.
Общи препоръки за техниката на заваряване
Ръчното и механизираното заваряване обикновено се извършва по тегло. Автоматичното заваряване може да се извърши по същия начин като заваряването под флюс, върху оставащи или подвижни подложки и подложки с флюс. В много случаи обаче най-благоприятните резултати се постигат с газови възглавници (Фигура XI.4). Те подобряват образуването на корена на заваръчния шев, а при заваряване на активни метали също допринасят за защитата на нагретия твърд метал от излагане на въздух. Газовете, подавани към подложката, могат да бъдат подобни по състав на тези, използвани за защита на зоната на заваряване.
XI.4. Схеми на газови възглавници a, b - едностранно и двустранно заваряване; 1 - защитен газ; 2 - медна облицовка
Качеството на шева до голяма степен се определя от надеждността на изтласкване на въздуха от зоната на заваряване. Необходимият разход на защитен газ се задава в зависимост от състава и дебелината на заварявания метал, конструкцията на заваръчното съединение, скоростта на заваряване и състава на защитния газ.
Влиянието на скоростта на заваряване върху надеждността на защитата на заваръчната зона може да се види от фиг. XI.5. Вятърът и теченията също намаляват ефективността на газовата защита. В тези случаи се препоръчва да се увеличи потокът на защитен газ с 20-30%, да се увеличи диаметърът на изхода на дюзата или да се приближи горелката до повърхността на детайла. При заваряване при високи скорости също е полезно да наклоните горелката под ъгъл напред, а за автоматично заваряване използвайте странично подаване на газ (виж фиг. XI.3, b). За защита от вятър зоната на заваряване е покрита с щитове. За достатъчна защита на връзките, посочени на фиг. XI.6, c, d, изисква се повишена консумация на газ. При заваряването им се препоръчва да се монтират екрани отстрани и успоредно на шева, които забавят изтичането на защитен газ. ПриПри равни условия консумацията на хелий, поради по-ниската му плътност, трябва да се увеличи в сравнение с аргон или въглероден диоксид.
XI.5. Влияние на скоростта на заваряване върху ефективността на газовата защита a-c - заваряване, съответно, при малки, средни и много
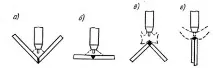
XI.6. Схеми (a-d) на местоположението на границата на струята на защитен газ по време на заваряване на различни видове съединения