7.4. Почистване на продуктаизгаряне от пепел и прах
Ефективността на устройствата за събиране на пепел зависи от физичните и химичните свойства на пепелта и димните газове, които я транспортират. Основните параметри на пепелта са плътност, дисперсен състав, електросъпротивление, лепкавост.
За почистване на газове от пепел и прах се използват апарати, които се различават по дизайн и принцип на отлагане на частици (фиг. 7.1). Разделят се на четири групи: "сухи" механични, "мокри" механични, филтри и електрофилтри.
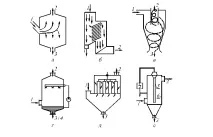
Ориз. 7.1. Пепело- и прахоуловители на ТЕЦ и котелни:
а– утаителна камера;b– жалузиен пепелно-прахоуловител;v– циклон;g- "мокър" прахоуловител;д– ръкавен филтър;e– електрофилтър;
1 –замърсени газове;2– пречистени газове;3– твърди частици;4– вода;5– корониращи електроди;6– събирателни електроди
Колекторите за пепел и прах се характеризират с ефективност на улавяне, което е съотношението на масата на уловения прах към общото количество прах, постъпващо в апарата.
«сухи»механични устройствавключват: утаителни камери, циклони, инерционни, жалузни, вихрови и динамични прахоуловители.
Те са лесни за производство и експлоатация. Ефективността на прахоулавяне в тях обаче не винаги е достатъчна, така че те се използват главно за предварително пречистване на газове.
Утаителните камериса кухи или с хоризонтални камерни рафтове (фиг. 7.1.а). Те използват гравитационно утаяване на частици при преминаване на газ през обема на апарата със скорост 0,2–0,8 m/s.
Жемлезни колектори за пепел и прах(Фиг. 7.1.b) са прости по дизайн и иматмалко хидравлично съпротивление. Състоят се от решетка с жалузи и прахоуловител (циклон). Целта на жалузийната решетка е да раздели газовия поток на две части: едната е по-малко прашна, съставляваща 80–90% от общия газов поток, а другата се засмуква в циклона, съставлявайки 10–20% от общия поток и съдържаща по-голямата част от праха, който е уловен в циклона. Освен това пречистеният в циклона газ се смесва с основния поток.
Скоростта на газа в жалузийния прахоуловител е 12–15 m/s; хидравлично съпротивление на решетката - 100–500 Pa. Използва се за улавяне на частици с размер над 20 микрона.
Циклонитеса най-разпространените устройства за почистване на газове от пепел и прах. Те са лесни за производство, работят надеждно при високи температури и газови налягания, имат почти постоянно хидравлично съпротивление и не променят фракционната ефективност с увеличаване на запрашеността на газа.
Подаването на газ към циклона може да бъде спирално, тангенциално, тангенциално-спирално. Циклоните могат да бъдат цилиндрични или конични. Цилиндричните циклони са устройства с висока производителност, докато коничните циклони са високоефективни.
Принципът на действие на циклона е следният (фиг. 7.1.c). Газовият поток, подаван тангенциално или спирално, се извива и се движи надолу по спиралата. Твърдите примеси, съдържащи се в газове, под действието на центробежни сили се притискат към стените на тялото на циклона и навлизат в бункера, а потокът от пречистени газове се изхвърля от горната част на циклона. Степента на пречистване на такива устройства е до 90%.
За повишаване на степента на пречистване се използват циклони с малък диаметър (0,23–0,5 m), комбинирани в батерии, така нареченитебатерийни циклони. Разпространени са три типа акумулаторни циклонни елементи: с аксиаленнаправляваща лопатка (BTsR-254), полуобемен газ (BTsU-M) и четирипосочен газ (BTs-512). Батерийните циклони от типа BTsU-M и BTs-512 имат по-висока степен на улавяне.
Батерийните циклони се използват за улавяне на пепел (прах) зад котли с паропроизводителност 500 t/h. Препоръчва се използването на циклони с тангенциално полуобемно подаване на газ тип BTSU-M с вътрешен диаметър 231 mm. Степента на пречистване за такива циклони е 88–92% при загуба на налягане от 500–700 Pa.
Групата«мокри»механични прахоуловителивключва: кухи, набити, пластинчати, ударно-инерционно действие, центробежни, високоскоростни (скрубери на Вентури) скрубери. Отстраняването на пепел (прах) в тях става чрез директен контакт на течността с прашен газ. Принципът на тяхното действие се основава на отделянето на частиците пепел (прах) от потока чрез инерционни сили и тяхното прилепване към водния филм, измиващ стените или повърхността на опаковката, което изключва връщането на частици в газовия поток. В пепелоуловителите от този тип, освен улавянето на пепелта, протичат химични процеси на абсорбция на въглеродни и серни оксиди от димните газове.
Колекторите за мокра пепел се отличават с висока ефективност (степента на пречистване достига 95-97%), относително ниска цена, умерени размери, лесна поддръжка и относително ниски експлоатационни разходи.
Кухите скрубери(фиг. 7.1.d) са кръгли или правоъгълни колони, в които се осъществява контакт между газ и водни капки, разпръснати от дюзи. Дюзите са монтирани в колоната в една или повече секции. Най-разпространени са противоточните скрубери. Скоростта на газа в тях варира от 0,6 до 1,2 m/s. Ако се работи прискорости на газа до 5–8 m/s, след което се монтират капкоуловители.
Хидравличното съпротивление на скрубера без капкоуловител е 250 Pa. Осигурява се висока ефективност на скрубера при размер на частиците над 10 µm.
Впрахоуловителите с подвижна дюзакато дюзи се използват пръстени, седла и топки от полимерни материали или пореста гума. Плътността на опаковката не трябва да надвишава плътността на течността. Оптималният режим на събиране на прах в такива устройства е зададен при пълна флуидизация.
Процесът на почистване се препоръчва да се извършва при следните условия: скорост на газа - 5–6 m/s; специфичен разход на течност за напояване - 0,5–0,7 l / m 3 газ; свободно сечение на решеткатаS0= 0,4 m 2 /m 2 с ширина на прореза 4–6 mm. Оптималният диаметър на топките е 20–40 мм. Обемна плътност - 200–300 kg / m 3. Минималната статична височина на уплътнителния слой е 5–8 диаметъра на топките в уплътнението, а максималната не трябва да надвишава диаметъра на скрубера.
Втарелковите колонипепелта (прахът) се задържа от слой газ-течност (пяна), образуван върху контактните плочи по време на взаимодействието на газ и течност. Най-често срещаните апарати за пяна със ситови плочи или с неуспешни плочи - перфорирани, решетъчни, тръбни и решетъчни.
Работата напорести филтриот всички видове се основава на процеса на филтриране на газове през порести прегради. При филтриране върху преградата се задържат твърди и течни частици, а газът преминава изцяло през нея. Филтриращите прегради са много разнообразни, но се състоят главно от влакнести или гранулирани елементи.
В зависимост от предназначението си порестите филтри условно се делят на фини филтри, въздушни филтри и индустриални филтри.
Фини филтрипречиствателитеса проектирани да улавят главно субмикронни частици от газове с ниска първоначална концентрация ( 3 ). Те се използват за улавяне на особено токсични частици с висока ефективност. За пречистване на газове с 99% от частици с размер 0,05–0,5 µm се използват материали под формата на тънки листове или насипни слоеве от тънки или ултратънки влакна (с диаметър по-малък от 2 µm).
Хидравличното съпротивление на чистите филтри е 200–300 Pa, а на запушените с прах 700–1500 Pa.
Фините филтри са проектирани за период от 0,5–3 години. Те не се регенерират, а се заменят с нови.
Въздушните филтрисе използват във вентилационни и климатични системи.
Индустриалните филтривключват платнени, гранулирани и груби влакнести филтри, използвани за пречистване на промишлени газове с концентрация на пепел (прах) до 60 g/m 3 . Най-често срещаните са тъканите филтри, които съдържат гъвкава филтрираща преграда под формата на цилиндрични ръкави (торбени филтри) (фиг. 7.1.e). Ефективността на такива филтри е повече от 99,5%, а загубата на глава е 1–1,5 kPa при скорост на филтриране 0,5–2 m/s.
Тъканните филтри са изработени от материал, който трябва да издържа на високата температура на димните газове. Филтърният материал трябва да е устойчив на висока влажност и химически съединения. Вълна, вълнен филц или лавсан се използват като филтърен материал при температура на газа до 130 °C. За температури около 260 °C се използват стъклени влакна и стъклени влакна с графит. Трайността на плата е 1-3 години. Тъканните филтри обикновено се правят многокамерни. Броят на ръкавите в една камера може да бъде 100 или повече.
Димните газове влизат отдолу в ръкавите, отлагането на прахови частицивъзниква върху вътрешната повърхност на стената на ръкава. По време на регенерацията подаването на димни газове към една от камерите се спира и слоевете прах, полепнали по тъканта, се отстраняват чрез разклащане или вибриране на ръкавите. Отделянето на праха се улеснява и от струя сгъстен въздух, насочена срещу движението, извършвано по време на процеса на филтриране. Отделеният прах попада в прахоуловителя, разположен под ръкавите и се отстранява с помощта на шнекове.
Остатъчната концентрация на пепел (прах) след тъканните филтри може да бъде 15–50 mg/m 3 , което отговаря на най-строгите стандарти.
Промишленитеелектрически филтри(фиг. 7.1.е) се използват за пречистване на големи обеми газ (до 1 милион m 3 /h) с концентрация на частици до 50 g/m 2 . Те улавят частици от всякакъв размер с ефективност над 99%. Електрофилтрите могат да работят при температури на газа до 400–450 °C както под вакуум, така и под налягане. Тяхното хидравлично съпротивление е 100–150 Pa. Разходите за енергия са 0,1–0,5 kWh на 1000 m 3 газ, който се пречиства.
Електрофилтрите имат следните недостатъци: големи размери, повишена металоемкост, висока цена и изискват квалифициран персонал за тяхната поддръжка.
Електрофилтрите се подразделят: по конструкция - на еднозонови и двузонови; по посока на газовия поток - на хоризонтални и вертикални; според конструкцията на събирателните електроди - на пластинчати и тръбни; според метода за отстраняване на прах от електродите - на "сухи" и "мокри"; в зависимост от броя на последователно разположените електрически полета - на еднополеви и многополеви; в зависимост от броя на паралелните електрофилтри - на единични и многосекционни.
Основните конструктивни елементи на електрофилтърите са: корпус, в който са разположени електродите; възлидоставка, разпределение и отвеждане на пречистени газове; устройство за отстраняване на уловения прах от електродите; устройство за отстраняване на прах от електрофилтъра; входни възли в електрофилтъра на ток високо напрежение - изолационни кутии.
Пречистването на димните газове в електрофилтъра възниква в резултат на създаването на неравномерно електрическо поле с високо напрежение (около 50 kV) и образуването на коронен разряд между електродите. Йоните и електроните, образувани в зоната на коронния разряд, предизвикват ток от корониращите електроди към събирателните електроди - коронен ток. Частиците пепел, намиращи се между електродите, се зареждат под действието на силите на електрическото поле, придвижват се до събирателните електроди и се отлагат върху тях. При време на престой на газовете в активната зона на филтъра най-малко 8 s и скорост на газа 1,2–1,5 m/s, степента на улавяне е 99–99,8%.
Ефективността на улавянето зависи основно от електрическите свойства на газовия поток, главно от електрическото съпротивление на частиците пепел. С увеличаване на електрическото съпротивление на частиците скоростта на отлагане намалява. В допълнение, ефективността на електрофилтърите зависи от начина на разклащане на електродите, за което най-често се използват ударно-чукови механизми. Интервалите между разклащанията трябва да бъдат оптимизирани за всяко поле, тъй като количеството на депонираната пепел намалява във всяко следващо поле.
Ефективността на почистване на димните газове от пепел и прах се увеличава значително при използване на комбинация от филтри, например колектор за мокра пепел и електростатичен филтър. Увеличаването на влажността и понижаването на температурата на газовете в колектора за мокра пепел осигурява ефективно улавяне на пепелта в електростатичния филтър. Общата степен на улавяне на пепелта в този случай достига 99–99,5%.