Конструктивни характеристики на различни видове фрези
В допълнение към инструментите за преминаване на струговане, широко се използват инструменти за пробиване, пробиване и рязане.
Резците(фиг. 3, a, b) се изработват с огънати и прави държачи. Въпреки че огънатият държач усложнява производството на ножове, той осигурява следните предимства: 1) гъвкавост, тъй като през ножовете могат да работят при преминаване и подрязване; 2) възможността за обработка на по-малко достъпни места.
Пробивните фрези(фиг. 3, c, d) се използват за обработка на вътрешни проходни и глухи отвори, както и вътрешни канали. Поради дългия надвес на държача на инструмента, намалената площ на държача на инструмента и трудната евакуация на стружките, бормашините работят при по-трудни условия, отколкото през фрезите. Държачите на пробиващи ножове са направени кръгли, а в точката на закрепване имат удебеляване на квадратно сечение. Диаметърът на държача зависи от диаметъра на отвора, който се обработва и е равен на dd = (0,5. 0,8) do, където do е диаметърът на отвора, който се обработва.
Пробивните фрези имат ниска устойчивост на вибрации и твърдост. За да се изключи нарязването на задната повърхност на ножа в режещата повърхност, острието на ножа е поставено малко под оста на отвора, а задната повърхност е извита.
Фрези(фиг. 3, д) се използват за рязане на детайли от прът и завъртане на външни канали в детайли на стругове, револверни стругове, автоматични машини и др.
Поради трудните условия на работа (голям надвес на ножа, трудни условия за деформация на метала по време на прехода към чипове, ниска твърдост на режещата част и следователно ниска устойчивост на вибрации), фрезите най-често се изработват от бързорежеща стомана. Режещата част има основен режещ ръб с ъгъл φ = 90° и два спомагателни ръба с ъгли φ1 =1°30'. 3°. Ако трябва да обработите края на детайла, без да оставяте пръта (главата) в центъра му, тогава основният режещ ръб се заточва под ъгъл φ = 75,80 °.
Когато използвате запоени твърдосплавни режещи пластини, дължината на главния режещ ръб на режещия инструмент трябва да бъде най-малко 5 mm. За да се увеличи твърдостта във вертикалната равнина, режещата глава обикновено се прави по-дебела, а режещият ръб, за да се избегне откъсване на карбидната плоча, се поставя под оста на машинните центрове на разстояние 0,5. 1,0 мм.
Наклоненият ъгъл γ има голямо влияние върху устойчивостта на вибрации на режещите инструменти, която намалява с намаляването му. Затова се препоръчва заточване на ъгъл γ = 15,20° със закаляваща фаска с ширина f = 0,2. 0,3 mm и под ъгъл γf = 0,–5°, заден ъгъл α = 10,12°.
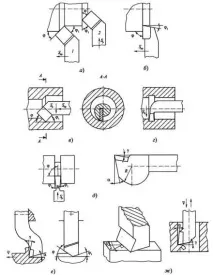
Фиг. 3. Видове фрези:
a - точкуване (чрез огънат надясно); b - нарязване (натискане направо през проход); c - пробиване за проходни отвори; g - скучен жлеб; e - рязане; д - рендосване; g - набраздяване
Фрезите за ренде и канали(фиг. 3, f, g) са инструменти, които работят с ударно натоварване по време на периодично повтарящо се рязане. Поради конзолния монтаж на такива фрези със сравнително дълъг надвес, техните държачи са подложени на еластични деформации и вибрации. Тези фрези работят при намалени скорости на рязане поради големи инерционни маси и сечения, които са 1,5-2 пъти по-големи, отколкото при струговане. Поради тези причини условията на рязане са неблагоприятни за използването на твърдосплавни пластини, така че най-често тези фрези се изработват от бързорежещи стомани.
За да се избегне проникването на задната повърхност на рендето в обработваната повърхност на детайла поради еластични деформации на държача, неговият връхтрябва да бъде разположен наравно с опорната повърхност и следователно държачът има извита форма.
На фиг. 3, д показва геометричните параметри на рендета с несвободно и свободно рязане (без спомагателни ръбове), а на фиг. 3g показва ъглите γ и α на шлицовите фрези. В примера за свободно рендосване може да се даде друга дефиниция на ъгъла на наклона на главния режещ ръб λ - това е ъгълът между вектора на скоростта на рязане и нормалата към проекцията на главния режещ ръб върху равнината на рязане, която в този пример съвпада с обработваната повърхност. Това определение на λ се прилага и за други видове инструменти, като свредла и фрези.
Стойностите на геометричните параметри на фрезите за рендосване и прорези обикновено се вземат близки до тези, приети за стругови фрези, с някои изключения. Така че, за да се предотврати раздробяване на върховете на ножовете при работа с удари, ъгълът λ се увеличава до 10,12 °. За несвободно рендосване се препоръчва главният водещ ъгъл φ = 20,45°. За довършителни операции (за изстъргване) е желателно ъгълът φ1 да се намали до 0.
Твърдосплавните фрезиса фрези, оборудвани с твърдосплавни пластини, които осигуряват висока производителност и са най-широко използвани в практиката.
Вложките се закрепват към държача чрез запояване или механично. Твърдосплавните фрези се произвеждат само в малки размери (използват се в инструментостроенето и часовникарската индустрия).
Използването на запоени стандартни твърдосплавни пластини с различни форми позволява компактни конструкции на фрези. Последните, след заточване, имат оптимални стойности на геометричните параметри и се характеризират с ефективно използване на твърда сплав поради многократно повторно шлифоване. Въпреки това запояванеима такъв значителен недостатък като появата на вътрешни термични напрежения в съединението и в самите плочи поради голямата разлика (около 2 пъти) в коефициентите на линейно разширение на твърдата сплав и стоманения държач. По време на охлаждане след запояване, получените напрежения водят до образуване на микропукнатини в плочите, които се отварят по време на заточване или по време на процеса на рязане. Микропукнатините водят до отчупване и дори до счупване на плочите. Често използваните технологични методи за облекчаване на напрежението: релаксация чрез забавяне на скоростта на охлаждане, използване на разширителни подложки и други, не решават напълно този проблем. Възможно е да се отървете от напрежението само чрез използване на сменяеми полиедрични вложки (SMP), които са механично прикрепени към тялото на инструмента. Тъй като пластините се затъпяват чрез завъртане, режещите ръбове се актуализират, което осигурява бързата им смяна и не изисква повторно шлифоване.
Инструментите, оборудвани с SMP, в сравнение със запоените, имат следните предимства:
Недостатъци на инструментите, оборудвани с SMP:
В зависимост от броя на режещите ръбове и форми, пластините имат различни дизайни, фиксирани в международни и национални стандарти. Някои от тях са показани на фиг. 4, а.
Геометричните параметри на инструментите, оборудвани с SMP, се определят в статика по време на производството на вложки и се коригират, когато са фиксирани в тялото (държача) на инструмента, като се вземат предвид кинематиката на машинния инструмент и условията на рязане.
Според геометричните параметри SMP се разделят на: а) отрицателни (γ = 0°, α = 0°); b) положителен (γ = 0°, α> 0°); в) отрицателно-положителен (γ> 0°, α = 0°) (фиг. 4b).
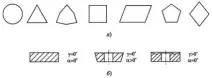
Фиг. 4. Карбидни сменяеми многофасетни вложки (SMP):
а - форми на плочи; b – геометрични параметри на плочи (отрицателни, положителни, отрицателни-положителни)
Ъгълът на хлабина при монтиране на отрицателни и отрицателно-положителни вложки се създава чрез завъртането им, когато са монтирани в държача на ножа. В този случай предните ъгли на отрицателните пластини стават отрицателни, т.е. (–γ) = α, за отрицателно-положителни плочи ъгълът γ намалява със стойността на ъгъла α. За положителните плочи ъгълът γ е равен на ъгъла на въртене на плочата по посока на часовниковата стрелка, а ъгълът α намалява със същото количество.
Има много дизайни на резци, които се различават по метода на закрепване на SMP, някои от които са направени с отвори за по-лесно закрепване. Анализът на многобройни дизайнерски решения за закрепване на плочите позволи да се сведат до следните схеми на закрепване (съгласно ISO):
Някои примери за дизайна на тези схеми на фрези са показани на фиг. 5.
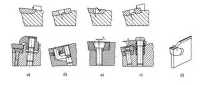
Фиг. 5. Схеми на механично закрепване на твърдосплавен SMP:
а - халс отгоре; b - лост през отвора; в - винт с конична глава; d - с щифт през отвора и със скоба отгоре; e - поради еластична деформация на стената на жлеба
Отрицателните и отрицателно-положителните плочи най-често се закрепват чрез затягане отгоре (схема а) или съгласно схема г. Последното осигурява по-надеждно закрепване. Винтовото закрепване (диаграма c) се използва за леко натоварени вложки и е просто и компактно.
При резците най-често срещаните са пластини с дупка. Това осигурява свободно движение на стружките по предната повърхност и значително по-малки размери на крепежните елементи, поставени в тялото на държача.
Възможни са нестандартни схеми за монтаж на нестандартни твърдосплавни пластини. Пример за това са режещите инструменти (фиг. 5, д), разработени от Sandvik Coromant (Швеция). Тук вложката е закрепена от силите на еластична деформация на стената на жлеба на държача.
Режещата керамика се доставя под формата на неподлежащи на смилане многостранни плочи (GOST 25003-81) с кръгла, квадратна, триъгълна и ромбична форма с различни размери. Отрицателните керамични вложки се монтират главно в същите държачи като твърдосплавните вложки - чрез затягане отгоре (фиг. 6, а).
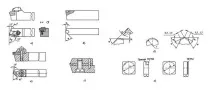
Фиг. 6. Сглобяеми инструменти за струговане:
а - с механично закрепване на керамична плоча; b - със запоен диамантен кристал; в - с междиненвложка; d - с механично закрепване на диамантения кристал; e - формата на режещите ръбове на диамантените инструменти (праволинейна, радиус, фасет); е - SMP със запояване от PSTM
Групата на свръхтвърдите материали включва диаманти (естествени и синтетични) и композити на базата на поликристали от кубичен борен нитрид (елбор).
Тъй като диамантите са много малки, те се фиксират чрез запояване, залепване или механично. Диамантът се закрепва чрез запояване директно в държача (фиг. 6b) или с помощта на междинни вложки (фиг. 6c). В последната версия вложката се пресова и синтерова заедно с диамант чрез прахова металургия. Механичното закрепване на диаманта е показано на фиг. 6, гр
Геометрични параметри на заточване на диамантени фрези: γ = 0.–5°, α = 8.12°, φ = 15.45°. Горната част на фрезата в плана е направена със закръгляване r = 0,2. 0,8 мм или с няколко фаски (фасети) (фиг. 6, д). В участъка, нормален към режещия ръб, радиусът на заобляне на режещия клин достига стойност r
Оптимално зададената скорост на рязане позволява рационално използване на всички ресурси, използвани в производствения процес. С увеличаване на скоростта на рязане се намалява времето за машинна обработка и като цяло трудоемкостта на производството на продукт.
Изследванията, проведени от съветски и чуждестранни учени, показват, че най-важните фактори, влияещи върху условията на триене и износване на режещите инструменти, са: физико-механичните свойства на обработвания материал и режещия инструмент.