Монтаж на индустриални подове
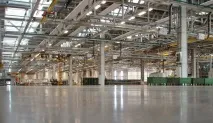
Процесът на създаване на индустриален бетонен под с втвърден горен слой се състои от следните основни стъпки:
- проектиране на подова конструкция;
- подготовка на основата за пода;
- изливане на бетон;
- изравняване на бетоновата смес;
- обработка с мистрия;
- нанасяне на втвърдяваща смес;
- фугиране на бетонна повърхност;
- нанасяне на импрегниране;
- рязане и запълване на дилатационни фуги.
дизайн на пода
На етапа на проектиране клиентът, проектантът и изпълнителят съвместно определят:
- конструктивни изисквания към пода, необходими технологии, материали, компоненти. Дебелината на основата се изчислява за бъдещото подово и бетонно покритие;
- характеристики на бетонната смес. Това са минималната марка бетон (за индустриални подове M300-350), вида на пълнителя и размера на неговата фракция, съотношението вода-цимент (съотношението W / C не трябва да надвишава 0,45), вида на добавките за пластификатор (използват се материали на базата на Na-нафталинсулфонати, Na-лигносулфонати, Ca-лигносулфонати), вида на армиращите материали;
- схема на устройството за деформация, изолационни шевове;
- вид и характеристики на материалите за запълване на фуги;
- вида и характеристиките на материалите, използвани за създаване на втвърдения горен слой;
- вид и характеристики на материалите за изпълнение на повърхността на бетонния под влаго- и химическа устойчивост;
- оптимални разходи и срокове.
Резултатът от погрешни (неправилни) изчисления на бетонната смес, както и подценяване на необходимото качество на бетона, може да бъде разрушаването на бетонната конструкция, появата на пукнатини, чипове и други дефекти.
Подготовка на основата
Бетонните подове в повечето промишлени предприятия се извършват на земята.
Подготовката на земната основа се състои от няколко етапа:
- Първо трябва да изравните повърхността на почвата. В зависимост от дебелината на пода и проектната кота, почвата може да бъде отрязана или насипана. Освен това почвата трябва да се уплътни с вибриращ валяк или виброплоча. Обикновено при монтаж на индустриален под дебелината на основата трябва да бъде най-малко 10 cm, а при полагане върху уплътнен пясък - 15-25 cm;
- Нивото на пода е отбелязано по стените на стаята. След това се полага хидроизолация от 2 слоя покривен материал и се извършва армировка. Армировката може да бъде под формата на мрежа от армировка или със стоманени фибри. Тези два метода на укрепване могат да се комбинират. Към бетона се добавят стоманени влакна, за да се намали напукването. При извършване на армировка с помощта на армировъчни мрежи е необходимо постоянно да се следи тяхното местоположение спрямо дадена маркировка на пода, тъй като от това зависи издръжливостта на пода и неговата устойчивост на напукване. Полагането и заваряването на армировъчната мрежа се извършва стриктно съгласно проекта, в който в зависимост от натоварванията на пода са посочени размерите на клетките на мрежата и дебелината на армировката. Монтажът на пода с недостатъчна армировка или без армировка води до напукване на покритието и чести ремонти.
- Върху фаровете се излива бетонна замазка. Като маяци могат да се използват метални профили, монтирани върху гипсови пити.
- По периметъра на помещението се полага амортисьорна лента. Това е необходимо, за да се предотврати напукване на пода в резултат на разширяването на бетонната смес по време на втвърдяване.
Ако се извърши подготовката на основатанеправилно могат да възникнат проблеми като прекомерно свиване на бетона, неравности на основната повърхност, лоша адхезия между армировката и бетона и др.
Изливане на бетон
След приключване на работата по подготовката на основата се пристъпва към приготвянето на бетоновия разтвор и неговото изливане. Спазването на всички изисквания на технологията на този етап избягва такива проблеми като хетерогенност на бетона, разделяне на сместа, повишена порьозност и др. Дебелината на бетонния слой зависи от очакваното натоварване на бъдещия под.
Препоръки за изливане на бетон:
- за изливане е най-добре да използвате висококачествен цимент с маркова якост най-малко M-300;
- за изливане използвайте бетонна смес с подвижност най-малко P2;
- дори ако изливането се извършва върху стоманобетонна основа, е необходима армировка. За подове, изпитващи нормални натоварвания, се използват армировъчни пръти с диаметър 8 mm. В случай, че се оборудва под с повишена якост, армировъчната мрежа е направена от прът с диаметър 16 mm. Клетките на армиращата мрежа могат да имат размери 100x100 или 150x150 mm;
- подът се излива върху монолитни карти. За да направите това, площта на пода е разделена на секции, поставяйки кофража по бъдещите разширителни фуги;
- така че бъдещият под да е издръжлив и да не изисква чести ремонти, трябва да се направят разширителни фуги, които ще предпазят горния слой бетон от напукване по време на свиване;
- изливането на бетон не може да се извършва при температура на въздуха под +5 градуса.
Изравняване
За изравняване и уплътняване на бетонната смес се използва преносим дълбок вибратор. След това с помощта на виброзамазка се извършва първичното изравняване на бетона. За проверка на бетон при нивелиранес помощта на лазерно ниво. След това се извършва вторичното изравняване на бетона с нивелираща релса със странични скоби. За уплътняване на бетон се използват вибрационни замазки с подходящо тегло, честота и амплитуда на движенията. Минималното време на вибрация трябва да бъде 25 секунди. Времето на вибрация е много важен момент: ако вибрацията приключи преждевременно, съответните параметри на бетонната смес намаляват. Ако вибрацията приключи по-късно, това ще доведе до загуба на влага в бетона и преразпределение на сместа.
Обработка с мистрия
Известно време след изливането (това може да бъде от 2 до 6 часа, в зависимост от втвърдяването на бетонната смес), обработката се извършва с мистрия, която популярно се нарича "хеликоптер". Това се прави с цел диспергиране и уплътняване на циментовото мляко. В този случай е много важно правилно да се определи моментът на началото на тази операция. Ненавременното фугиране не само няма да укрепи, но дори ще отслаби повърхностния слой на бетона, което в бъдеще ще доведе до неговото разрушаване и влошаване на декоративните свойства на повърхността.
Нанасяне на втвърдяваща смес
Втвърдяването на бетонния под започва, когато дълбочината на отпечатъците върху него е не повече от 3-4 mm. Сухите втвърдяващи смеси (топинг) се нанасят върху повърхността на прясно излят бетон, за да се повиши неговата устойчивост на износване, устойчивост на удар, устойчивост на динамични и статични натоварвания.
Сухата смес се нанася върху пресен бетон с дозираща количка в разход 4-8 кг/кв. метър. Дебелината на слоя от нанесената смес трябва да бъде 2-3 mm. Най-популярният състав за топинг марка Turbofloor. Цената му зависи от вида на сместа. В зависимост от пълнителя тези смеси могат да бъдат кварцови, корундови илиметализиран. За промишлени помещения, по пода на които се движи различно работно оборудване, се препоръчва използването на метализиран покрив.
Предимства на бетонни подове с покритие:
- дългосрочна експлоатация (най-малко 25 години без основен ремонт);
- устойчивост на удар, незапрашеност, устойчивост на агресивни химически среди;
- простотата на устройството. Технологичният процес не отнема твърде много време;
- лекота на работа и лекота на поддръжка;
- оптимално съотношение на качество и цена на материалите;
- горният слой е едно цяло с бетонната основа, което напълно елиминира разслояването му;
- пода с топинг може да бъде изработен в различни цветове (сиво, синьо, зелено, бордо и др.).
Вторична обработка с маламашка
След нанасяне на сухата смес подът се третира повторно с мистрия, но остриетата на мистрия се заменят с абразивни шлифовъчни дискове. На този етап бетонната повърхност се довежда до огледална гладкост. След смилането подът трябва да бъде добре почистен от прах със строителна прахосмукачка.
Върху гладкия под се нанася обезпрашаващ и втвърдяващ полимерен уплътнител. Обработката с тези състави предотвратява риска от напукване по време на втвърдяването на бетона. Уплътнителят се нанася върху все още пресен бетон с пръскачка, валяк или четка. Специалната формула на разтвора насърчава дълбокото проникване на неорганичния реагент в порите на бетона и му осигурява оптимален процес на втвърдяване. Първо, химическа реакция регулира неравномерното или рязко изсушаване на заливката и след това насърчава образуването на кристали, които в крайна сметка запушват порите и запечатват основата. Този процесобикновено продължава една година след изливането. След завършването му се проявяват всички експлоатационни качества на покритието.
Рязане и фугиране
След завършване на обработката на бетонния под с покривна смес и уплътнител, трябва да се внимава да се предпази покритието от възможни деформационни процеси. Бетонните настилки се свиват при ниски температури на околната среда и, разбира се, се разширяват при високи температури на околната среда. Следователно монолитната мрежа трябва да може да променя параметрите си в зависимост от влиянието на външни фактори. За това са предвидени компенсаторни фуги, които поемат пълзящи отклонения и по този начин предотвратяват напукване на бетонната замазка.
Разграничават се следните видове шевове:
- изолиращ. Те се изпълняват с цел осигуряване на независимост на подовете от съседните стени. Изолационните фуги предотвратяват прехвърлянето на деформационните процеси от стените към подовото покритие. Те се създават чрез полагане на амортисьорна лента по протежение на стените около периметъра на помещението преди изливане на бетонната смес. Ширината на шевовете трябва да бъде приблизително 10 mm;
- свиваемите фуги се изпълняват, за да се елиминира напрежението вътре в замазката, което възниква поради факта, че горният слой се втвърдява по-бързо от долния. Изпълнете тези шевове с помощта на направляващи релси, докато бетонът изсъхне;
- структурните шевове са разположени успоредно на другите шевове на разстояние 1,5 m от тях.
Разрязването на компенсационни фуги се извършва съгласно следните правила:
- рязането се извършва не по-късно от 6-8 часа след вторичното фугиране на втвърдения слой;
- шевовете се нарязват на дълбочина до 1/3 от дебелината на замазката;
- посоката на рязане трябва да съответства на посоките на технологичните фуги и фугите на подовите карти. Припри планиране на посоките на рязане е необходимо да се избягва появата на Т-образни пресичания и образуването на остри ъгли в ставите на шевовете;
- за да се определи интервалът на рязане, дебелината на замазката се умножава по коефициент 24-36. Например, при дебелина на замазката 16 см, шевовете трябва да се режат на разстояние 16 х (24-36) = 384 - 576 см.
Шевовете след рязане трябва да бъдат запечатани с мастика или с помощта на специални уплътнителни елементи: водни спирачки, деформационни профили, уплътнителни корди. За уплътняване на фуги на закрито и на открито експертите препоръчват използването на деформационни профили Deflex. Тези профили не изискват точни размери на фугите, тъй като се адаптират към промени в ширината на фугите, отклонения встрани, наличие на стружки по ръбовете.
Правилно монтираните профили Deflex повишават топлоизолацията на пода и го предпазват надеждно от изтичане на ГСМ и вода. Те са в състояние да издържат на повишени натоварвания на шевовете, както и на сезонни промени в тяхната ширина. Продуктите на такива фирми като Dewmark и Lankmeta също се доказаха добре. Вътрешните аналози на Miguya, Aquabarrier практически не са по-ниски от вносните проби.
Ако се спазват всички технологии по време на монтажа на пода, бетонната замазка е правилно оформена, поддържат се определени ъгли на наклон, тогава такъв под ще може да издържи всички натоварвания, присъстващи в производственото помещение. Дългият експлоатационен живот и постоянно привлекателният външен вид са основните предимства на индустриалните бетонни подове.
За повече информация относно основните точки на монтажа на бетонни подове за предприятия, вижте статията Полирани бетонни подове в промишлени предприятия.