Опции за намаляване на шума за редуктори и скоростни кутии
ВЪЗМОЖНОСТИ ЗА НАМАЛЯВАНЕ НА ШУМА НА ЗАБЕЛЕЖКИ И СКОРОСТНИ КУТИИ
Терехова О.А., Марголит Р.Б.(RI (f) MGOU, Рязан, РФ)
Отчита се намаляването на нивото на шума при отворена верига и при работно натоварване. Предполагаме да намалим натоварванията вътре в редуктора, да използваме безконтактно лабиринтно уплътнение и поддържащо регулиране на лагера, за да избегнем няколко предавки, работещи на една и съща честота на предаване.
За многостепенни зъбни редуктори, работещи в променливи режими, които включват скоростни кутии на металорежещи машини, скоростни кутии на асансьори, транспортни и много други машини и механизми, представлява интерес нивото на шума при празен ход и при работно натоварване.
Дизайнерите и производителите на тези механизми не винаги обръщат необходимото внимание на начините за намаляване на шума. Ние ще предложим някои от тях.
1. Намаляване на натоварванията вътре в самата скоростна кутия.
1.1. Ускоряващите предавки за въртене изискват повишен въртящ момент, като по този начин създават натоварване не само в тази предавка, но и във всички предишни. При проектирането трябва да се избягват предавките с повишена скорост.
1.2. Натоварването на крайната връзка възниква в скоростните кутии на металорежещите машини, когато се използват контактни уплътнения, които предпазват лагерите на шпиндела от изтичане на смазка от главата и от замърсяване и навлизане на охлаждаща течност. Предлага се изоставяне на гумените контактни уплътнения в полза на безконтактни лабиринтни уплътнения. Смяна на контактното уплътнение в задната опора на шпиндела на универсален струг винтово нарязване мод.
1.3 Натоварването в лагерите често зависи от качеството на изработката. Практиката на сглобяване на възли показва, че качествен монтаж сизползването на регулирането на лагерните опори води до намаляване на шума до 5 dB.
2. Не е необходимо да се допуска работа на няколко предавки в конструкцията при една и съща честота на предавките. Честотата на зацепванеfв Hz отразява въздействията при всяко захващане на зъб и може да се изчисли по формулата:
f=,
къдетоn– скорост в об/мин;
z е броят на зъбите на въртящото се колело.
С висока степен на сигурност може да се приеме и практиката потвърждава, че честотата на звуковото налягане от работеща предавка е равна на честотата на нейното зацепване. Не е желателно дизайнът на възлите да има зъбни колела, които работят:
- с равни честоти на ангажиране;
- с високи честоти на ангажиране.
Съвпадението на честотите в един възел не винаги се обръща внимание при проектирането, въпреки че дизайнерът винаги има резерв за промяна на честотата на предавката. Използването на междинни, така наречените паразитни колела в дизайна трябва да се избягва. Такива колела винаги имат две предавки, работещи при една и съща честота на предавките. Ето един пример (фиг. 1) за даване на паразитна предавка вместо твърдо паразитно колело 1 [1] (опцияa) на две различни джанти 2 и 3. Проверката на решението (опцияb) при проектирането на веригата за обратно въртене на шпиндела на струга доведе до намаляване на нивото на шума с 4 dB.
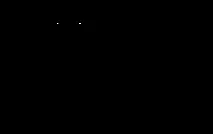
Снимка 1 - Промяна на дизайна на междинното колело
За да определите общата звукова мощност, излъчвана от няколко източникаLpна машинните възли, трябва да използвате формулата за енергийно сумиране на шума:
Lp= ,
къдетоLi(i= 1, 2,…n) е нивото на звукова мощност, излъчвано от отделен източник;nе броят на източниците, в този случай връзките със същата честота.
Следователно, когато стойностите на няколко честоти на предавката съвпадат, задачата за постигане на нисък шум става много по-сложна и понякога става трудна за решаване на практика. За да се отървете от съвпадението на равенството на честотите на предавките, е необходимо да промените стойностите на модулитеmи броя на зъбитеzза някои от колелата. Чрез избор на нов брой зъби може да се запази предишното предавателно отношение. Ако продуктътmzсе запази непроменен, няма да е необходимо да се променят централните разстояния в телата на кутията. По-добре е да следвате пътя на намаляване на броя на зъбите с увеличаване на модулите. В този случай няма да има проблеми с прехвърлянето на максимални натоварвания, а честотата на предавките също ще намалее, което допълнително ще има положителен ефект върху характеристиката на шума.
Появата на високи честоти на предавките също не винаги се обръща внимание при проектирането. Санитарните стандарти за шум определят по-строги изисквания за шум при високи честоти. Най-доброто решение е да се избегнат прекалено високите честоти на предавката в дизайна, което ще предотврати появата на шум при високи честоти.
3. Изисквания за точността на зъбните колела.
Тези изисквания трябва да се задават в съответствие с изискваните шумови характеристики на възлите и скоростите на въртене на предавките. От трите компонента на точността на колелата съгласно GOST 1643-81 (кинематична точност, гладкост, контакт на зъбите) за колелата на скоростни кутии на металорежещи машини и транспортни средства, най-важните показатели са нормите на гладкост, на второ място е контактът на зъбите. Поради икономически причини е препоръчително да се задават комбинирани изисквания: например при скорости до 8 m / s 8-6-6, при по-високи скорости 7-5-6.
Препоръчително е да се отделят изискванията запрофил а) към формата на повърхността, б) към местоположението. Грешката на позицията е отклонението от определения ъгъл на зацепване. За да се осигури нисък шум, важно е да се гарантира, че ъглите на зацепване на двете трансмисионни колела са еднакви. Нека наречем това основно правило за нисък шум. Големината на самото отклонение е напълно маловажна, тъй като няма значение дали ъгълът е 20º или малко по-голям или по-малък. Грешки във формата също могат да бъдат въведени умишлено, за да се подобри гладкостта: хълбок в горната част и малко подрязване в областта на корена на зъба.
4. Повишаване на плавността на натоварените предавки.
Зъбите при натоварване се деформират, а задвижващото колело се деформира повече от задвижваното. Основното правило за нисък шум е нарушено До известна степен е възможно да се компенсира разликата в размера на деформацията, като се даде на задвижваното колело леко отрицателно отклонение в профила в сравнение с задвижващото [2]. Не е възможно напълно да се компенсира разликата в деформациите, тъй като при цилиндричните зъбни колела винаги има преход от една двойка към двучифтна предавка в съответствие със стойността на коефициента на припокриване. Колкото по-голям е коефициентът на припокриване, толкова по-голям е периодът на зацепване на две двойки, толкова по-малка е деформацията на зъбите.
Най-радикално това се проявява при прехода към спирално зацепване. Коефициентът на припокриване става повече от две. За да се увеличи носещата способност и да се премахнат аксиалните натоварвания върху лагерите, те се преместват от спирални зъбни колела към шевронни зъбни колела.
Увеличаването на гладкостта и носещата способност на еволвентните зъбни колела се осигурява от прехода от цилиндрични зъбни колела към спирални, шевронни и аркови зъбни колела. Продуктивната технология за рязане на зъбни колела на високопрецизни аркови колела с еволвентен профил [3] е разработена от екип от служители на Рязанския институт (клон) на Московската държавна образователна институция.
1. Необходимо е да се намалят натоварванията вътре във възела и да се избегне съвпадението на честотите на предавките.
2. Плавността и ниският шум на предавките се осигуряват от съвпадението на ъглите на предавките.
3. Намаляването на шума чрез намаляване на големината на деформацията на зъба под натоварване възниква по време на прехода от цилиндрични към спирални, шевронни и аркови зъбни колела.
1. Марголит Р.Б., Терехова О.А. Конструктивни предпоставки за производство на нискошумни металорежещи машини // Монтаж в машиностроенето, инструментостроене - 2005. - № 8.- С.3 -12.
2. Сертификат за полезен модел № 11117 Цилиндрично еволвентно цилиндрично зъбно колело // Изд. измислям. Р.Б. Марголит, Ю.С. Маркин, E.N. Моос, М.М. Слугин, В.И. Бойко. - действа на територията на България от 09.03.99г., регистриран на 16.09. 99.