Шпинделно задвижване
Задвижването на главното движение предава на шпинделите от двигателя определената мощност на рязане P, kW. Той е пропорционален на произведението на силата F, H и скоростта на рязане v, m/min или въртящия момент Mcr, Nm и скоростта на шпиндела n, min -1.
Силата на рязане в първото приближение може да се определи от специфичната сила на рязане q, N/mm 2 и режими на рязане: скорост v, m/min; захранване s, mm; дълбочина на рязане t, mm. Продуктът f \u003d st, mm 2 е равен на площта на напречното сечение на изрязания слой и определя силата на рязане F \u003d qst. Като вземем предвид зависимостта, намираме силата на рязане:
Специфичната сила на рязане е широко представена в материалите SANDVIKCoromant (нелегирана стомана - q ≈ 2000 N/mm 2 , високоякостен легиран сив чугун - q = 1500 N/mm 2 ).
За извършване на процеса на рязане е достатъчно да се прехвърли само въртящият момент и скоростта на въртене към шпиндела.
Като двигател в металорежещите машини по правило се използва електрически двигател и много рядко - хидравличен или пневматичен. Предаването на движение от електродвигателя към шпиндела най-често се осъществява чрез зъбни колела и ремъчни предавки.
Скоростите са прости по дизайн, компактни, осигуряват постоянно предавателно отношение. Използват се при обиколни скорости до 20-30 m/s с цилиндрични зъбни колела и до 30-50 m/s с винтови зъбни колела. Ограничението на скоростта е причинено от повишени вибрации и шум, причинени от грешка на стъпката, профил на зъбите, променлива твърдост на мрежата и лагери на шпиндела. На фиг. 1, b въртенето от електродвигателя 1 през ремъка 2 и предавката 4 се предава на шпиндела 3.
Ремъчните задвижвания са структурно по-сложни, имат по-големи размери, силите на опън на колана създават значителни радиални натоварвания. Но те се отличават с гладко въртене, намаляват динамичните натоварвания по време на прекъсванияпроцес на рязане, не изискват смазване, позволяват ви да предавате въртене на големи централни разстояния.
Тесните клиновидни ремъци се използват при скорости до 40 m/s. Широко разпространени са клиновидни ремъци с надлъжни V-ребра по вътрешната повърхност.
Задвижванията със зъбни ремъци се използват при скорости до 50 m/s и създават по-ниски радиални сили.
На фиг. 1, а от електродвигателя 2 чрез ремъчната предавка 3, скоростната кутия 4 и ремъчната предавка 1 въртенето се предава на шпиндела 5.
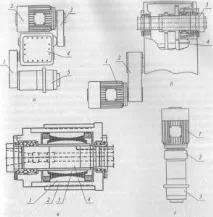
В съвременните машинни инструменти все по-често се среща директно въртене на шпиндела от електродвигател без междинни предавки, което се улеснява от безстепенното регулиране на скоростта на шпиндела с помощта на честотен преобразувател. Популярни са шпинделите с вграден електродвигател (електрошпиндели или моторшпиндели) - фиг. 1, c. Статор 1 е монтиран неподвижно върху корпус 2, ротор 3 върху шпиндел 4. Задвижването не натоварва шпиндела с радиална сила или огъващ момент. Като цяло дизайнът е опростен. Всички недостатъци, характерни за зъбни и ремъчни предавки, са изключени. Диапазонът на управление се определя от възможността за преобразуване на честотата на напрежението, захранващо двигателя, f, Hz:
където p е броят на полюсите на двигателя, s е приплъзването.
За регулируемо задвижване на главното движение се използват честотни преобразуватели и асинхронни променливотокови двигатели с диапазон на регулиране D = (3-5) (при постоянна мощност). На фиг. 2 показва характеристиките на регулатор с постоянна мощност P = 5,5 kW и максимален въртящ момент M = 35,8 Nm. Скорост n = 1500min -1, от която започва постоянната мощност на електродвигателя, се нарича номинална. Възможно е да се работи при скорости на въртене n = (60-1500) min -1, но в този случай инсталираната мощност на електродвигателя ще бъде недостатъчно използвана, което освен намаляване на производителността води и до допълнителни загуби на енергия - намаляване на cosφ.
Разновидност на директното въртене на шпиндела е коаксиално задвижване (коаксиален метод за предаване на въртене), фиг. 1, d, при който въртенето от електродвигателя 1 се предава на шпиндела 3 чрез съединителя 2 без предавки. Запазват се предимствата на шпиндела с вграден двигател. Специфичен недостатък е голямата обща дължина на двигателя и шпинделния възел, което не винаги е удобно по конструктивни причини. Коаксиалният метод за предаване на въртене към шпиндела се намира в електромеханичните задвижвания, за да се елиминират деформациите на огъване на шпиндела.
Инерционно задвижване, когато детайлът се върти свободно. Рядко се изисква малка грапавост Ra. c - силфонна втулка; g - конични пръстени.
Ключовите връзки са доста прости, но водят до периодична промяна в твърдостта по време на въртене, натоварвайки шпиндела с радиална задвижваща сила. Задвижваната връзка 1 (предавка, шайба) се натоварва с периферна задвижваща сила F0 (виж фиг. 3, а). Действието му върху шпиндела може да се замени със силата Fr=F0, преминаваща през оста на въртене и въртящия момент Мcr = F0R. Силата F. огъва шпиндела, намалява точността на обработка.
За да се спаси шпинделът от силата Fr, която го деформира и предава само въртящ момент, понякога се поставят два ключа (фиг. 3, b). Но поради производствена грешка моментът може да се предава само през една повърхностконтакт a, оставяйки втората повърхност a' напълно (както е показано на фиг. 3, b) или частично разтоварена. Силата на огъване на шпиндела Fr също се запазва.
Използването на вградени електрошпиндели и коаксиално задвижване също позволява да се предава само въртящ момент към шпиндела. Същите условия се поддържат при използване на коаксиално интегрирани зъбни колела и фрикционни съединители. Останалите типове от изброените връзки на задвижваната връзка с шпиндела запазват радиалните сили на задвижването, ако не е предвидена ненатоварена конструкция.
Връзката със силфонна втулка 1 (фиг. 3, c) предава въртящ момент поради силите на триене, осигурява точно центриране на задвижваната връзка 2. Силите на триене се създават поради деформацията на втулката (виж пунктираните линии), когато се компресира от винт 3. Използват се втулки с диаметър d = (14–100) mm и дължина L = (20–60) mm.
Връзките с конични пръстени 7 (фиг. 3, d) не осигуряват точно центриране, необходимо е кацане върху повърхност с диаметър d. Пръстените не се спират сами. Използват се с размери d = (10-300) mm. Надеждна работа при ударни натоварвания. По-долу са ориентировъчните стойности за въртящия момент Mkr. предавани от конструкцията съгласно фиг. 3, г-н
Последните две връзки изискват допълнително пространство в радиалната посока на задвижваната връзка за поставяне на втулката или пръстените.
Стъпаловидни втулки, интегрирани с макарата, са обичаен начин за предаване на въртящ момент. Те не изискват допълнително пространство, но налагат по-строги изисквания за точност на изработка и др.