Възстановяване на части под ремонтния размер
Ремонтните размери са разделени на стандартни, безплатни (монтажни) и регулирани.
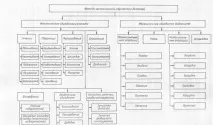
Ориз. 15. Методи и видове обработка на детайли
Безплатните ремонтни размери, получени чрез механична обработка на частта за получаване на правилната геометрична форма и необходимата грапавост на повърхността, не са строго регулирани по размер и техните размери са ограничени само от минималната стойност. Напасването на свързващата част (хлабина) се постига чрез извършване на регулиране. Например, гърбиците на разпределителния вал се възстановяват чрез шлайфане по протежение на копирна машина до свободен ремонтен размер. Компенсацията за увеличаването на пролуката между клапаните и пръстите на кобилиците се постига чрез намаляването й с регулиращ болт. Минималният размер на гърбицата е ограничен от изпъкналостта на гърба на гърбицата над повърхността на вала (0,05 mm). При безплатния ремонтен размер се възстановяват износените повърхности на фаските на плочите, седалките и краищата на клапаните, притискащите плочи на съединителя и други части.
Схемата за възстановяване на ремонтните размери на вала и цилиндровата обшивка на двигателя с вътрешно горене е показана на фиг. 16. Минималният размер на диаметъра на вала и максималният размер на диаметъра на отвора на цилиндъра се определят от здравината на стените на вала или цилиндъра и минималната дебелина на слоя за термична обработка на повърхностния слой на детайла. Възстановяването на частите до ремонтния размер се извършва в съответствие с разработените работни технологични процеси.
За възстановяване на основните части на двигателя с вътрешно горене - цилиндрови втулки и шийка на коляновия вал - чрез механична обработка до ремонтния размер, изчислението се извършва в следната последователност: - определяне на най-големия и най-малкия диаметър на цилиндровите втулки и шийките на коляновия вал; въз основа на спецификации за контрол, сортиране ивъзстановяване на части според най-големия размер на диаметъра на цилиндъра и най-малкия размер на диаметъра на шийките на коляновия вал определя най-близкия ремонтен размер; – след избор на ремонтния размер се определят режимите на обработка на пробиване, скорост на рязане, дълбочина на рязане, подаване, скорост на шпиндела, брой проходи и основно машинно време.
Скоростта на рязане ur се определя от таблични данни в зависимост от вида на обработвания материал и според графика в зависимост от необходимата грапавост на повърхността на детайла.
Режимите на шлифоване включват периферна скорост на въртене на шлифовъчното колело, напречно и надлъжно подаване. Кръстосаното подаване (дълбочината на смилане) се избира според справочниците и е в диапазона 0,05-0,08 mm, в зависимост от материала и размера на детайла. Надлъжното подаване (траекторията на движение на шлифовъчното колело за един оборот), скоростта на смилане и скоростта на въртене на шлифовъчното колело се определят подобно на въртенето.
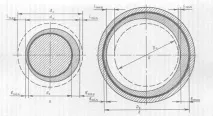
Ориз. 16. Възстановяване на части до ремонтния размер
Обещаващи насоки за подобряване на обработката и подобряване на качеството на възстановените части.
Усъвършенстването на механичната обработка се извършва в три направления: - усъвършенстване на технологичните процеси за възстановяване на детайли; - използването на модерно високопроизводително индустриално и специализирано оборудване в ремонтната индустрия; - прилагане на нови методи за обработка на детайли и нови видове инструменти.
Технологичните процеси се подобряват чрез подобряване на точността на обработващите части, при оборудване на оборудване с лагери, които не са подложени на износване (например лагери с въздушно смазване, хидравлично смазване), повишаване на производителността на технологичнитепроцеси (увеличаване на скоростите на рязане при обработка на части чрез рязане, намаляване на спомагателното време) въвеждане на плазмени машинни части.
Подобряването на механичната обработка при използване на нови видове инструменти се постига с фрези, шлифовъчни дискове, хонинговащи камъни, полиращи ленти, пасти от синтетични материали (кубичен борен нитрид-елбор-3), диаманти, подвижни твърдосплавни пластини от волфрам TN-20 и термит.
Ремонтни части с допълнителни ремонтни части
В ремонтната практика се използват няколко метода за възстановяване на части.
Ремонтни размери. Една от износените свързващи части, обикновено по-скъпи или сложни, се обработва до определения размер, а другата част се заменя с възстановена или нова, също изработена до ремонтния размер.
Метод на допълнителни ремонтни части. Използват се при използване на готови детайли, които се монтират върху специално подготвени повърхности на отвори или валове и по този начин заместват износената част на детайла (биелни лагери, бутала, бутални пръстени и др.).
Отстраняване на дефекти чрез натиск. Въз основа на използването на пластичните свойства на материала на частите. Използват се за възстановяване на размерите на износени повърхности на лагери (набраздяване на повърхности), якост и твърдост на умора (обработка на пружини с профилна ролка) и деформирани части (втулки и др.).
Отстраняване на дефекти чрез галванично и химическо натрупване на метал (хромиране, остатък, медно покритие, поцинковане). Липсата на нагряване на детайла и структурни промени в метала, което отличава този метод от другите (заваряване, наваряване и др.).
Електроискрови и плазмени методи. За легиране и изграждане на износени повърхности на детайли, които са по-скъпи и трудоемки за производство.
Запояване. Елиминирайте пукнатини и използвайте при отслабване на якостта на кръстовището в блоковете на електрическото оборудване.
Заваряването и наваряването е най-разпространеният начин за възстановяване на части. Това се дължи на възможността за възстановяване на части, изработени от различни метали и имащи голямо разнообразие от дефекти. )
Дефекти в части от алуминиеви сплави (пукнатини, дупки, счупвания, износени повърхности на отвори) могат да бъдат отстранени чрез електродъгово заваряване с електроди от марката OZA-2. Електродите се съхраняват в сухо проветриво помещение; електродите, които не са използвани в рамките на един месец от датата на тяхното производство, трябва да бъдат калцинирани при температура 22O преди употреба. 23O°C за 1 ч. За заваряване на пукнатини се изрязва плитка бразда по цялата дължина на пукнатината. Шлаките, покриващи шева, се измиват с вода след заваряване и едновременно с това се почистват с метална четка. Преди заваряване частта трябва да бъде предварително загрята до 15O. 25°C.
При възстановяване на мотоциклетни части от алуминиеви сплави се използват електроди с диаметър 3,5 mm. Силата на тока трябва
бъде 125,160 A, дължината на дъгата е равна на диаметъра на електрода, скоростта на заваряване е 0,4. 0,6 м/мин.
Възстановяване на части с епоксидни състави и лепило.
Методите, използвани за ремонт на части, по-специално електрическо и газово заваряване, наваряване, хромиране, покритие, изискват специално оборудване и производствена база и следователно често са неприемливи за водача. Епоксидните смоли и различни състави и лепила на тяхна основа могат да се използват за ремонти на място и в някои случаи без демонтаж на възли и възли. Помислете за тезиметоди по-подробно.
Следните части могат да бъдат възстановени с епоксидни състави: картер на двигателя и неговите капаци, цилиндрова глава и нейния капак, маслен съд, корпус на скоростна кутия и нейните капаци, корпус на карбуратора, резервоар за гориво, кални щитове и тяло на талигата (дупки и пукнатини). Също така е възможно да се поправят износени повърхности в интерфейсите между лагери на валове, лагери и лагери и да се коригират разхлабени шпилки и щифтове.
Ремонтираната част трябва да бъде предварително почистена от ръжда и мръсотия с механични или химически средства. Механичното почистване се извършва със скрепер, пила, шкурка, шлифовъчен диск или обработка на металорежещи машини. Химически почистени (обезмаслени) с ацетон, бензин Б-70 или разтворители № 646 или № 648 и РДВ. При обезмасляване използвайте само четки за коса или четки.
Във всички случаи, за да се подобри механичната адхезия на епоксидния състав към ремонтираните повърхности, последните се третират с повишена грапавост.
Понякога върху повърхността на ремонтираната част се нанасят плитки нарези с длето по протежение на пукнатина или около дупка. Дупките или жлебовете се покриват с кълчища или азбестово въже. След такава подготовка те се обезмасляват, след което частта се държи при температура 18,23 ° C в продължение на 5 минути, докато разтворителят изсъхне напълно. Готовността на повърхността се определя с помощта на капка вода: ако водата се разпространи и намокри повърхността, тогава нейната адхезия към епоксидния състав ще бъде добра.
При вграждане на пукнатина върху детайлите повърхността около нея се почиства с 10,15 mm и ръбовете се затъпяват, върху почистените и обезмаслени ръбове на пукнатината се нанася епоксиден състав, след което се нанася пластир от фибростъкло (или друга плътна памучна тъкан).0,3 дебелина. 0,4 mm и се навива с валяк, както е показано на фигура 1. Втори слой от състава се нанася върху пластира и повърхността на частта, след което се прилага втори пластир и т.н. Общо 3-8 слоя плат се нанасят върху отвора, последният слой се покрива със състава. След пълно втвърдяване неравностите се обработват с шмиргел.
При монтаж върху отвор на метална обшивка с дебелина 0,5. По контура на отвора с диаметър 1,5 се пробиват отвори 0,8 мм. 2,0 mm (фиг. 2) и почистете облицовката и повърхността на частта около отвора. След това ръбът на отвора, почистената повърхност на отвора и металното покритие се обезмасляват.
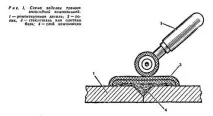
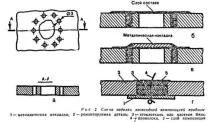
ku, за което тези повърхности се избърсват старателно с ацетон или бензин B-70 и се изсушават за 5 минути. След това всички отвори се запълват със състава, приготвен на базата на съединението K-P5, тънкият му слой се нанася върху почистената повърхност около отвора (фиг. 2, b) и върху металната плоча, а последната се нанася върху отвора (фиг. 2, c).
Понякога върху металния слой се поставят още няколко наслагвания от фибростъкло с ролково валцоване (фиг. 2d).
За запечатване на дупки и пукнатини в картера и други части е препоръчително да използвате епоксидна смес K-P5
(STU 30-14148-63) с пълнители. Съставът на състава (в тегловни части): съединение K-P5-12, пълнител (един от следните номера): 1) стоманен прах - 10 и графит - 2; 2) графит - 7; 3) смляна слюда - 6; 4) алуминиев прах - 4,5. Втвърдител - AF-2 (TU 264-70).
Съставът се приготвя непосредствено преди употреба, тъй като когато в него се въведе втвърдител, той може да се нагрее и бързо да се втвърди. Съставът за предпочитане се приготвя в плоски метални, картонени или пластмасови тави в количествонеобходими за еднократна употреба (150.200 g), тъй като срокът на годност е не повече от 35.40 минути. При производството на състав от епоксидна смола, последният се нагрява във водна баня до температура 5O. 60 ° C и изсипете в тава за печене, така че дебелината на слоя да е не повече от 10,15 mm. След това в него се въвежда пластификатор, дибутил фталат, при старателно разбъркване в продължение на 5 минути. Пълнителят се добавя към получената смес, разбърква се още 5 минути и се охлажда до температура 18,23 ° C, след което втвърдителят се въвежда в сместа на части и се разбърква старателно в продължение на 4,5 минути.
Съставът трябва да се нанася върху частта, която ще се ремонтира, и наслагването само с дървена, метална или гумена шпатула. Съставът се втвърдява в зависимост от температурата на околната среда. При температура 18,23°С експозицията е 24,36 часа, при 60°С - 2,3 часа и при 100°С -0,5 часа. Един час
За ремонт на износени повърхности на части, работещи в лагери на валове, съединители на лагери и лагери, и за фиксиране на разхлабени шпилки и щифтове се препоръчват епоксидни пасти, които не изтичат от вертикална стена при температура 18,23 ° C. За да се приготви пастата, един от пълнителите се въвежда в епоксидната смола в количеството, посочено в таблица 2.
Таблица 2. | Състави на епоксидни пасти, % от теглото на смолата | |
Пълнител | Смола ED-16 | Смола ED-20 |
Желязо на прах Графит Алуминиев прах Бронз на прах Кварцово брашно Портланд цимент | 200 80 25 130 230 200 | 160 40 20 80 150 120 |
Също така е възможно да се използват други пълнители и техните смеси. За да се предотврати изтичането на пастата (с недостатъчен вискозитет и значителна дебелина на слоя), върху нанесения слой се нанася хартия. Тези пасти са особеноефективен при възстановяването на части с малко износване (не повече от 0,3 мм), т.е. износване на седалката на лагера.
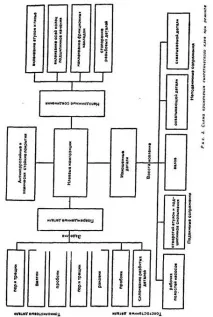
За възстановяване на дупки в картера на двигателя, скоростната кутия, задната предавка, в главините на колелата и на други места се препоръчва и съставът на следния състав: епоксидна смола 100 части; алифатна смола (DEG-1) - 10; полиетилен-полиамин - 13,5; графит - 30; стоманен прах - 100 и аеросил - 3. 4 части.
Възстановяването на интерфейса лагер-гнездо с лепило е възможно само ако разстоянието между тях не надвишава 0,1. 0,2 мм. При възстановяване на седалките за лагери лепилото се нанася в тънък слой върху предварително обезмаслената повърхност на седалката и лагера, след което лагерът се монтира в седалката и се държи 24 часа при температура 18,23 ° C или 3 часа при температура 60 ° C.
За тези проводници се препоръчват лепила: VS-YuT, VS-350 и VK-32-200. Областта на приложение на лепила по време на ремонт е показана на фигура 3.