Газозаваряване - Студопедия
По време нагазнаваряване (GN) газов пламък се използва като източник на топлина за получаване на отложен метален слой. Газовият пламък на специалните горелки може да се използва за наваряване, пръскане на покрития, както и тяхното изплакване. Газов пламък се получава чрез изгаряне на газообразни продукти в кислород. Като горим газ най-често се използва ацетилен, чиято максимална температура на пламъка е 3150 ° C. За тези цели се използва и пропан-бутан.
При наваряване, за разлика от заваряването, е желателна малка дълбочина на проникване на основния метал, следователно наваряването се извършва чрез високоскоростно заваряване (метод на Линда). При заваряване (наваряване) по този начин се използва горелка с дюза с голям диаметър, нагряваща основния метал с карбюризиращ пламък. При заваряване с горима смес, обогатена с ацетилен, върху металната повърхност се отлагат частици редуциран въглерод, образувайки тънък карбуризиран слой с дебелина
0,02 мм. Поради намаляването на точката на топене на метала на карбуризирания слой, топенето се случва само в тънък повърхностен слой. Появата на това явление, наречено "замъгляване", показва готовността на основния метал за газово заваряване. "Замъгляването" на основния метал в комбинация с използването на пълнежен материал създава особено благоприятни условия за газова наварка с леко проникване на основния метал. Появата на "замъгляване" също така позволява да се определи моментът на нагряване до температурата на наслагването и по-точно да се избере времето за подаване на наслагващ материал. В същото време повърхностната карбуризация по време на наваряване по този метод води до увеличаване на съдържанието на въглерод в отложения метал, което се отразява неблагоприятно върху неговите механични свойства и устойчивост на корозия.издръжливост. В тази връзка понастоящем разглежданият метод се използва само при напластяване на сплав с високо съдържание на хром на базата на желязо и други високовъглеродни повърхностни материали, докато при нанасяне на покрития от устойчива на корозия стомана, за които карбуризацията е нежелателна, се използват методи за дъгова наварка с консумативи и волфрамови електроди в среда от инертен газ.
Методите за напластяване с пламък, използващи материали за настилка под формата на пръти, пръти и телове, са традиционни до известна степен. Те се използват в промишлеността от дълго време и по отношение на техниката на изпълнение се различават малко от методите с електрическа дъга. Заедно с тези методи значително развитие получи методът на газово-прахово наваряване.
Газо-праховатанаварка позволява да се втвърдяват части със сложна конфигурация със слой с минимална дебелина (0,1 - 0,3 mm) без разреждане с основния метал, тъй като преходната зона в този случай е само 100 - 120 микрона. За наваряване се използват специални горелки (фиг. 8.7).
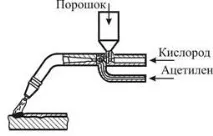

Ориз. 8.8. Горелка за газопрахова наварка Фиг. 8.8. Схема на плазмено наваряване с две
Наплавъчният материал под формата на прахова сплав се подава от бункера под действието на гравитацията и инжекционното действие на кислородна струя през кислородно-газов пламък към мястото на наваряване. В резултат на нагряване с пламък прахообразните частици достигат повърхността на детайла в силно пластично или разтопено състояние и след втвърдяване образуват отложен метален слой, използван за възстановяване и втвърдяване на машинни части.
Наваряването се извършва с гранулиран самофлюсиращ прах от системата хром - бор - никел. Консумацията на прах е до 2,7 kg/h. Препоръчителните размери на частиците на праха са 40 - 100 микрона.
Използва се газово-прахово наваряванеглавно при ремонтни дейности за възстановяване и закаляване на автотракторни детайли, матрици и матрици, релсови глави в жп транспорта и други части.
Основните предимства на метода:ниско проникване на основния метал; универсалност и гъвкавост на технологията; възможността за наслагване на слоеве с малка дебелина.
Основните недостатъци на метода: ниска производителност на процеса; нисък коефициент на използване на повърхностните материали (60 - 80%); нестабилност на качеството на отложения слой.
Не намерихте това, което търсихте? Използвайте търсачката:
Деактивирайте adBlock! и опреснете страницата (F5)наистина е необходимо