Характеристики на технологията за производство на дебелостенни съдове под налягане
При производството на дебелостенни съдове широко се използва електрошлаково заваряване, което осигурява надеждно проникване на цялото напречно сечение в едно преминаване. Надлъжните шевове на дебелостенни черупки, като правило, се извършват чрез електрошлаково заваряване. В зависимост от размера на съда листовата заготовка се огъва в нагрято състояние по дългия или късия ръб на листа. В първия случай черупката е дълга и броят на периферните шевове в съда е по-малък. Въпреки това, за съдове с голям диаметър, дължината на късия ръб на листа може да е недостатъчна, тогава черупката се състои от две корита с два надлъжни шева. Във втория случай черупката е по-къса, но с един надлъжен шев. Втората техника изглежда по-малко подходяща, тъй като периферните шевове са по-трудоемки в сравнение с надлъжните. Черупка с един надлъжен шев може да се получи чрез валцуване. След разрязването листът се нагрява до 1000,1050 °C и се валцува до затваряне на фугата, оставяйки участъци с ширина 100,150 mm недовалцовани (фиг. 13). След като обвивката се охлади, съединението се фиксира чрез заваряване на скоби 1 и празнина 2 се изрязва чрез термично рязане за електрошлаково заваряване.
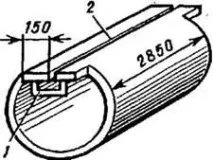
Ориз. 13. Навита черупка с един надлъжен шев
Трудно е да се получат черупки с дължина над 3500 mm и дебелина на стената над 100 mm, като се използва методът на валцуване. Огъването на мощна преса няма такива ограничения, особено ако черупката е оформена от две корита. Сглобяването на корпуса за електрошлаково заваряване в този случай (фиг. 14) се извършва с помощта на скоби, а постоянството на празнината в съединението се постига чрез поставяне на дистанционни елементи, които се отстраняват преди заваряване. След заваряване на изходните пръти и джоб за индуциране на шлаков басейн, сглобената за заваряване обвивка се монтира вертикално. Ако черупката има два надлъжни шева, препоръчително е да ги изпълните едновременнодвама заварчици.
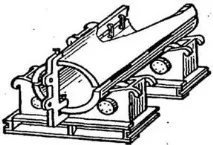
Ориз. 14. Сглобяване на корпуса с две надлъжни връзки
При заваряване на корита, огънати под налягане, се получава черупката
сравнително правилна цилиндрична форма и последващо калибриране
по желание. Черупките, получени чрез валцуване, изискват изправяне.
Калибрирането се извършва при температура 1000. 1050 ° C и при охлаждане
черупки във въздуха, той едновременно претърпява процес на нормализиране.
Периферните заварки се извършват чрез многослойно заваряване под флюс или
електрошлаково заваряване с едно преминаване. Пълно проникване при
многослойното заваряване се осигурява чрез полагане в жлеба отвън
няколко заваръчни слоя 1 (фиг. 15), като се почиства коренът на шева с помощта на
пневматично длето или фреза и налагане на вътрешен заваръчен шев 2. След това се извършва многослойно запълване на външното рязане 3.
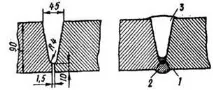
Ориз. 15. Формата на рязане на пръстеновидното съединение под многослойния слой
Сглобяването на периферния заваръчен шев за електрошлаково заваряване трябва да бъде достатъчно точно, тъй като локалната депланация на извити ръбове над 3 mm може да доведе до повреда на уплътнението и изтичане на резервоара от шлака. Следователно, преди сглобяването, външната и вътрешната повърхност на всяка от черупките се обработват до ширина 70,100 mm от края (фиг. 16). Подготвя се и сглобката на кората с дъното. Съединението се сглобява с помощта на ленти, които се монтират "на ръба" през пръстеновидния шев и се заваряват към повърхността на черупките. Ако като вътрешно оформящо устройство се използват медни охлаждащи подложки, огънати по радиуса на заварения продукт, вътре в корпуса допълнително се монтират временни закрепващи скоби. Облицовките 1 (фиг. 17) се вкарват в отворите на скобите 2 и се фиксиратклинове 3 или винтови скоби.
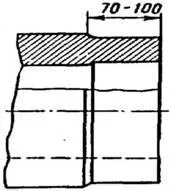
Ориз. 16. Обработка на краищата на черупката
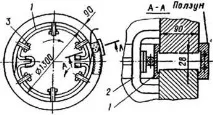
Ориз. 17. Пръстеново съединение сглобено за електрошлакова
Електрошлаковото заваряване на пръстеновидния шев започва върху спомагателна плоча, заварена в междината на съединението (фиг. 18, а). След заваряване на около половината от обиколката на съединението (фиг. 18, b), заварчикът отстранява началото на шева от процепа с нож, докато липсата на топене се елиминира напълно и дава на края на шева наклонен разрез, което улеснява затварянето на шева (заключване) (фиг. 18, c). Свиващата се обвивка или се поставя в специален отлив във външния плъзгач или в медна форма, или се разтопява и вари на ръка.
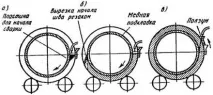
Ориз. 18. Схема на електрошлаково заваряване на периферни шевове
Обещаващо е еднопроходното заваряване на дебелостенни съдове с електронен лъч във вакуум. Експериментално е доказано, че при използване на заваряване с хоризонтална греда е възможно да се направят надлъжни и периферни заварки на метал с дебелина 250 mm или повече при скорост на заваряване
2.5.. .5 m/h. Производственото приложение на този обещаващ метод обаче все още изисква разработването на редица технологични въпроси, както и създаването на големи вакуумни камери.
След приключване на заваряването на тялото на съда, изрязване на отвори за
фитингите се произвеждат механично или чрез термично рязане.
Особено голямо количество такава работа се извършва в производството
котелни барабани и колектори. За да намалите работата по монтажа
монтаж при сглобяване на колектори и барабани с екранни тръбни блокове, до
точността на монтажа на фитингите налага строги изисквания. Заваряването на голям брой фитинги трябва да бъде автоматизирано. Използваните за тази цел специализирани машини и полуавтоматични машини обикновено се центрират отгоречасти от заварения фитинг.
Възможностите за проектиране на фитинги с черупки с голяма дебелина са разнообразни. Най-подходящи са тези, които ви позволяват да получите надеждно проникване на цялата стена на дюзата, изключвайки възможността за образуване и нарастване на пукнатини от липса на проникване. За тази цел можете да използвате формираща облицовка, която се отстранява след заваряване (фиг. 19, а, б) Друг вариант на свързване е показан на фиг. 20, а, б. В корпуса 2 в центъра на монтажа на тръбния адаптер се пробива центриращ отвор d, в който се вкарва заготовката 1 на адаптера с режещи ръбове за заваряване. След заваряването се пробива отвор с диаметър D (фиг. 20, а). Крайната връзка е както е показано на фиг. 20б. Той има концентрация на напрежение върху външната повърхност, но отсъства върху вътрешната кухина. парогенераторите включват газонепроницаеми тръбни панели. При използване на обикновени тръби заваряването на ленти - джъмпери се извършва чрез сдвоени глави за заваряване под флюс, първо от едната страна (фиг. 21), а след накланяне - от другата. Използването на оребрени тръби намалява броя на шевовете. Първото преминаване се извършва върху охладен меден плъзгач; вторият - от другата страна по протежение на предварително завършения първи (фиг. 22, а, б).
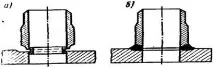
Ориз. 19. Дизайнът на съединителната връзка: а - преди заваряване; b - след заваряване
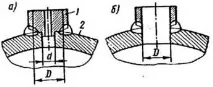
Ориз. 20. Свързване на фитинги с корпуса, последвано от отстраняване на корена на заварката чрез пробиване
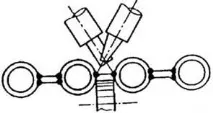
Ориз. 21. Схема за заваряване на лента между гладки тръби (заваръчни шевове)
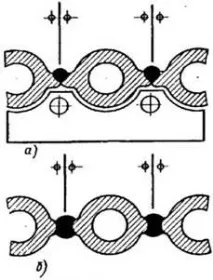
Ориз. 22. Заваряване на газонепроницаеми оребрени тръбни панели
Особено критични съдове, като например съдове на ядрени реактори с дебелина на стената до 200 mm и повече, са направени от твърди ковани корпуси, получени чрезсвободно коване на преса с последваща механична обработка. Разделянето на тялото на отделни
Фигура 23. Заготовка на корпуса на реактора
заготовките се произвеждат въз основа на възможностите на технологичното оборудване (фиг. 23). За да се подобри устойчивостта на корозия, вътрешната повърхност се подлага на автоматично дъгово наваряване с аустенитен лентов електрод. Черупките са свързани чрез периферни шевове чрез многослойна заварка под флюс.
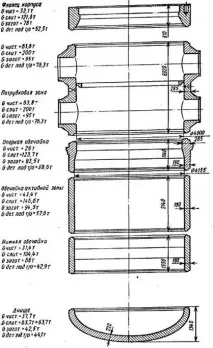
Така, при производството на корпуса на реактора ВВЕР-1000 от стомана 15Kh2NMFA и корпуса на парогенератора от стомана 10GN2MFA, обвивките с дебелина 80,285 mm бяха монтирани на скоби и заварени чрез многопроходно заваряване под флюс с нагряване (120,250 ° C), като зададената температура по време на заваряване се поддържа с помощта на индуктори или газови горелки. След полагането на кореновите ролки (фиг. 24, а) се запълва ^ 3 част от сечението на външния жлеб (фиг. 24, b); отрязвам
Фигура 24. Последователност на запълване на ръба при заваряване на пръстеновидния шев на корпуса на реактора
монтажни скоби и почистете корена на шева отвътре (фиг. 24, b). След това жлебът се запълва отвън до пълното сечение (фиг. 24, d); кореновите ролки бяха положени отвътре (фиг. 24, д) и цялата секция на рязане беше запълнена (фиг. 24, е). Облицовката на зоната на топлинно въздействие и заваръчния шев отвътре се извършва чрез наваряване с аустенитна тел (фиг. 24, g). Електрошлаковото заваряване е използвано само при изработката на заготовка за дъното на корпуса на реактора, като се използва нагряване за щамповане за едновременна термична обработка - нормализиране, за осигуряване на необходимите свойства, на заваръчното съединение.
Електрошлаковият процес се използва и за формиране на издадени части със сложна форма. Например на фиг. 25, а показва диаграма на процеса на топене на разклонителна тръба.Предварително в корпуса 3 се пробива отвор, в който отвътре се вкарва запушалка 4, а от външната повърхност на корпуса се монтира медна форма 2. Преди започване на процеса във формата се излива течна шлака; чрез подаване на електрод, 1 отвор и кухината на матрицата се запълват с течен метал. В резултат на такова електрошлаково топене в тялото се образува издатина (фиг. 25, b), чиято механична обработка гарантира получаването на разклонителна тръба с необходимата конфигурация.
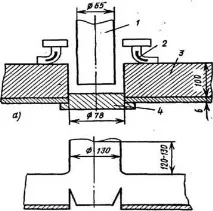
Ориз. 25. Електрошлаково топене на разклонителна тръба: а - диаграма на процеса; b - форма на напречното сечение на тръбопровода за консуматив
При производството на барабани за котли, съдове под налягане и
реактори, термичната обработка е от голямо значение. Напълно заварени
съдът обикновено се подлага на силно темпериране, но понякога се налага
нормализиране за подобряване на структурата на зоната на шева. В този случай има опасност при нагряване до високи температури (900. 1000 ° C) да възникнат деформации от собственото си тегло, които да изкривят формата на съда. Тези деформации могат да бъдат предотвратени чрез предварително запечатване на готовия съд и създаване в него на излишно вътрешно налягане на въглероден диоксид от 0,2. 0,3 N/mm (MPa). Това не само запазва формата на съда, но и предотвратява образуването на котлен камък по вътрешната му повърхност. За термична обработка обикновено се използват големи пещи. Ако съдът не може да бъде подложен на термична обработка като цяло поради липсата на пещ с необходимия размер, както и поради необходимостта от монтажни съединения, тогава се използва локална или обща термична обработка с помощта на индукционни или други нагреватели.