LiAZ - Ликински автобусен завод (69 снимки)
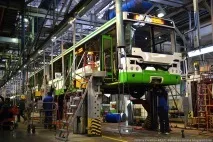
1. Нашата обиколка на завода започва с цеха за преса и заготовки.

2. Тук се извършва надлъжно и напречно рязане на валцована стомана, както и всички необходими заготовки за студено щамповане на части за бъдещи автобуси.
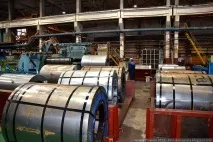
3. Линия "Халброн".
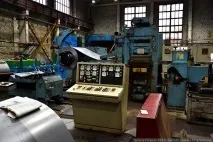
4. В производството на студено щамповане се изработват облицовъчни панели на тялото, както и части и възли от елементи на рамката на тялото.
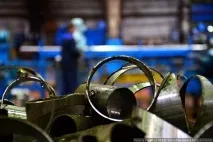
5. Участък за лазерно рязане с комплекс "Trumpf TL - 3030".
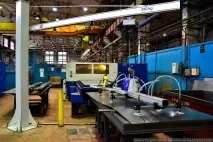
6. С помощта на хитър кран операторът подава металния лист в работната зона на машината.
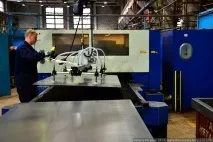
7. Успяхме да погледнем зад защитния екран и да видим как лазерният лъч изгаря правилния профил на бъдещия детайл с висока скорост.
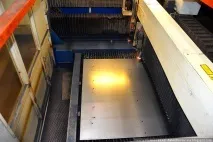
8. След известно време машината разтоварва готовите части.
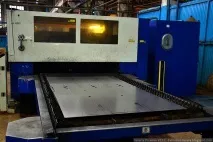
9. Но това е само началото на един дълъг процес.
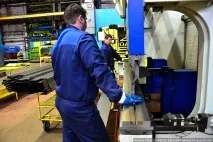
10. Малко по-късно, на пресата, ще им бъде дадена желаната форма.
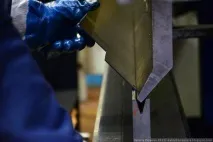
11. Готовите части чакат да бъдат изпратени към следващите етапи на производство.
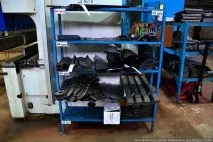
12. Работен процес.
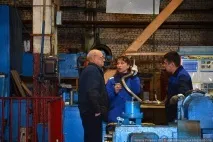
13. Производство, бобина - изпарител, въздушна система. По-късно ще видим как изглежда частта върху готовия автобус.
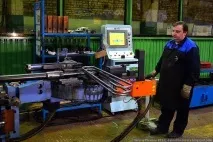
14. Сега нека да продължим към работилницата за заваряване и каросерия. Снимката показва линията за сглобяване и заваряване на покрива SCHLATTER. Преди това работниците събират елементи от бъдещия покрив на хелинга.
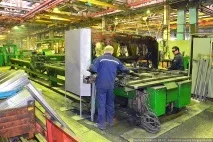
15. ШЛАТЕР на работа.
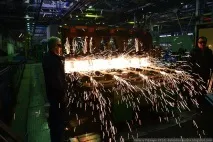
16. Следваме нишката на конвейера. Стъпка по стъпка елементите на автобуса придобиват все повече и повече нови детайли.
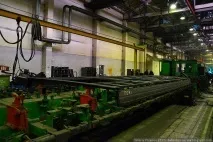
17. Сглобява се предният панел на автобуса. Заварчик на работа.
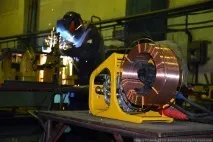
18. Най-накрая идва времетокогато всички елементи на рамата на автобуса се сглобяват в едно цяло на конвейера. Предницата е на снимката.
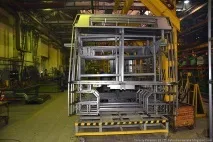
19. Така наречената рама е долната, носеща част на каросерията на автобуса.
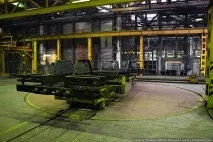
20. На хелинга, спазвайки строгата геометрия на тялото, всички части се сглобяват в едно цяло.
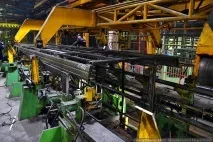
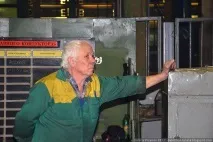
22. Заваряване на корпуса на хелинга. Сега, ако желаете, можете да разгледате силуета на бъдещия автобус.
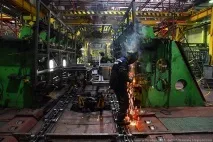
23. Освен това на конвейера готовата рамка се обшива с метални листове.
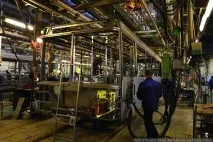
24. За да бъдат страните на автобуса абсолютно равни, ЛиАЗ използва уникална технология. Преди заваряване металният лист се нагрява до температура от 90 градуса по Целзий. Увеличава размерите си и едва тогава се изтегля върху рамката.
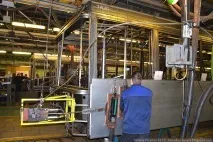
25. Последни щрихи на каросерията.
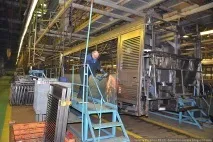
26. Обърнете внимание, една по една две части от съчленения автобус се изпращат за катафореза на тялото.
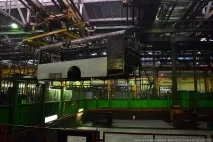
27. Няма аналози на този процес за тела с такива размери в България, други страни от ОНД и съседни страни.
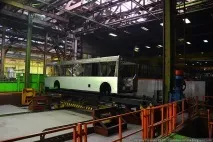
28. Крехко момиче командва операцията.
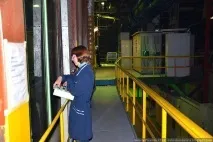
29. Телата се потапят последователно в няколко огромни вани.
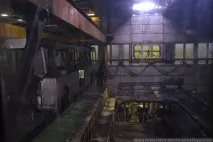
30. Навремето заводът става първото предприятие в България, което прилага цялостна антикорозионна обработка на каросерии по метода на катафорезата. Същността на този метод на електролитно оцветяване е, че продуктът, поставен във вана за катафореза, се излага на електрическо поле. В резултат на това върху целия продукт се нанася специална боя на водна основа, като не се пропускат дори труднодостъпните ъгли. Адхезията на епоксидния слой към метала е изключително силна, а полученото покритие е устойчиво на най-агресивни климатични условия.
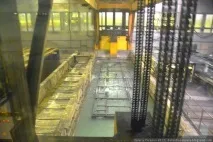
31. В момента този метод за нанасяне на електролитен грунд, в допълнение към LiAZ, се използва само в отделни предприятия в Западна Европа.
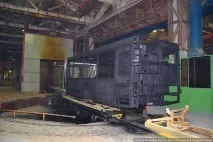
32. За мен беше откровение, че покривът на автобуса е сто процента покрит с найлон.
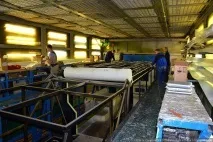
33. LiAZ твърди, че тази технология е с порядък по-практична и издръжлива.
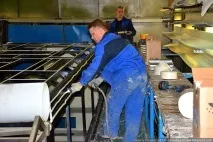
34. В компанията постоянно работят около хиляда и половина работници със средна заплата от 35 хиляди рубли.
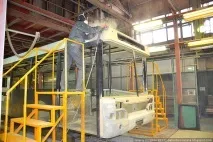
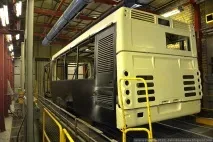
36. Но най-големият обем поръчки в LiAZ пада в края на годината, т.к основните клиенти на предприятието са бюджетни организации. В такива моменти производството на автобуси от поточната линия се увеличава драстично. Компанията набира временни работници и вдига заплатите.
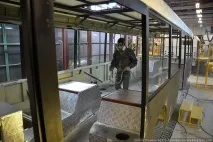
37. Телата са въпрос на законна гордост на завода.
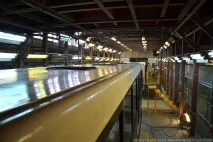
38. LiAZ гарантира, че каросерията на неговите автобуси ще издържат поне 12 години преди корозия.
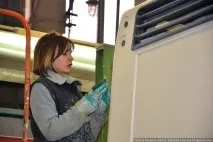
39. Споделете усмивката си!
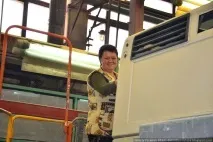
40. Последният етап преди изпращане на картината на тялото.