Намаляване на емисиите на вредни вещества във въздуха от отработените газове при изгаряне на гориво
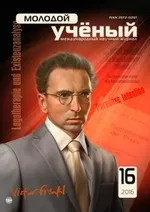
Библиографско описание:
Изгарянето на гориво е не само основният източник на енергия, но и най-важният източник на замърсители за околната среда. Най-„отговорни“ за засилващия се парников ефект и киселинните валежи са ТЕЦ-овете. Те, заедно с транспорта, доставят на атмосферата основния дял техногенен въглерод (главно под формата на CO2), около 50% серен диоксид, 35% азотни оксиди и около 35% прах.
В индустриализираните страни използването на висококачествени въглища - сортирани, с ниско съдържание на пепел, с ниско съдържание на сяра, и в малки пластови пещи на котелни - екологични бездимни и нискодимни въглища с ограничено отделяне на летливи вещества се счита за най-евтиният начин за намаляване на емисиите в атмосферата.
Действащите в България стандарти за въглища за послойно горене предлагат много широка гама от марки и класове въглища: от антрацити до дългопламъчни, от сортирани концентрати до обикновени, чиято технологична и екологична ефективност на изгаряне може да варира значително.
При изгаряне на "бездимно" гориво котелните помещения, оборудвани със стратифицирани пещи с фиксирани решетки и ръчно впръскване на гориво, могат да бъдат екологични дори при липса на оборудване за почистване на газ. В същото време се наблюдава значително намаляване на емисиите на продукта от непълно изгаряне: специфичните емисии на CO намаляват с 80–95% [1].
В момента, като част от изпълнението на екологичната програма, повечето топлоелектрически централи (ТЕЦ) реконструират съветски, морално и технически остарелиелектростатични филтри в котелни агрегати, което позволява да се намалят емисиите на вредни вещества в атмосферата с 8-10 хиляди тона годишно и да се постигнат европейски стандарти: ефективността се увеличава от 98,5 на 99,9%.
За оптимална високоскоростна работа на котелния агрегат BKZ-420-140, който се използва в повечето случаи в когенерационните централи, е необходимо да се реконструират горелките на котела.
В този случай могат да се препоръчат следните методи за реконструкция:
1) Монтаж в реконструираната горелка на нова разделителна обвивка с вихрови лопатки, два новоформирани канала за вторичен въздух - коаксиален междинен канал за вторичен въздух, съседен на каналите за въздушна смес и ограждащ го, и преграда във входящата тръба за въздух.
2) Монтиране на въртящи се клапи в каналите на входящата тръба за осигуряване на изчислените скорости на вторичния въздух във всеки от каналите на вторичния въздух.
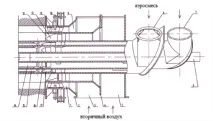
Ориз. 1. Реконструирана горелка: 1 - тяло на горелката; 2 - входяща тръба за вторичен въздух; 3 - входен канал на външния поток от вторичен въздух; 4 - разделителна стена на входната тръба на горелката; 5 - входен канал на вътрешния поток от вторичен въздух; 6 - входна тръба на външния поток на въздушната смес; 7 - входна тръба на вътрешния поток на въздушната смес; 8 - централна тръба; 9 - външен канал за вторичен въздух; 10 - устройство за регулиране на въртенето на лопатките на външния вторичен въздушен канал; 11 - въртящи се лопатки на канала за вторичен въздух; 12 - вътрешен канал за вторичен въздух; 13 — лопатки на вътрешния канал за вторичен въздух; 14 - вътрешен канал на въздушната смес; 15 - външен канал на въздушната смес; 16 - лопатки на вътрешния канал на въздушната смес; 17 - остриета на външния канал на въздушната смес
Посочените фитинги за настройка и управление са монтирани в отделен разклонителен тръбопровод,в непосредствена близост до фланеца на тръбата за подаване на въздух на тялото на горелката.
3) Монтаж на две колони за групово дистанционно управление на ротационни шибъри с общо задвижване към всяка група горелки от едната страна на горивната камера.
4) В допълнение към този обхват на работа се планира да се монтира отклоняващ конус на изхода на външния вторичен въздушен поток.
5) Рециркулация на продуктите от горенето в пещта на котела
Методът се състои в връщане на част от продуктите на горенето от газовия път на котелния агрегат към горивната камера (фиг. 2).
Причини за намалено образуване на азотни оксиди:
- намаляване на максималната температура на горене в резултат на разреждане с охладени продукти на горене;
- баластиране на зоната на образуване на NО с продукти на горене, т.е. намаляване на концентрацията на реагиращи вещества;
- разширяване на зоната на горене, т.е. намаляване на температурата на пламъка в резултат на по-голям пренос на топлина от повърхността му.
При използване на метода на рециркулация в енергийни котли са изследвани няколко начина за въвеждане на газове в горивната камера [1, 2]: през прорезите под горелките, през пръстеновидния канал около горелките и смесване на газове с взривния въздух пред горелките.
Най-ефективен се оказа последният метод, при който температурата в сърцевината на пламъка се понижава в най-голяма степен, а степента на намаляване на образуването на NО е (50–70)%.
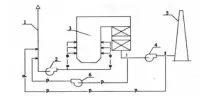
Ориз. 2. Рециркулация на продуктите от горенето в енергийни котли: 1 - вал за всмукване на въздух; 2 - вентилатор; 3 - горивна камера; 4 - димоотвод; 5 - комин; 6 – рециркулационен димоотвод; p - линия за рециркулация на продуктите от горенето
Оптималното количество рециркулирани газове в енергийните котли е 20% от консумацията на продукти от горенето. Принципно възможно2 схеми за вземане на проби от рециркулирани газове (фиг. 2):
- точка I - от газохода под вакуум, т.е. от смукателния тръбопровод на димоотвода; в този случай е необходим специално инсталиран рециркулационен димоотвод;
- точка II - от газопровода под налягане, т.е. от частта под налягане на димоотвода.
Предимството на първата схема е, че изборът на газове за рециркулация с помощта на специален рециркулационен димоотвод ви позволява да контролирате потока на избраните газове. Недостатъкът е цената на инсталирането и експлоатацията на димоотвод.
Предимството на втората схема е, че няма нужда от инсталиране на специален димоотвод (газовете навлизат в горивната камера поради остатъчното налягане на главния изпускателен вентилатор). Недостатъкът на тази схема е, че резервът в налягането на главния димоотвод обикновено не е достатъчен, за да се избере оптималният газов поток. В този случай степента на редукция на азотните оксиди намалява до (40–30)% или по-малко.
В промишлените котли се използва главно втората схема, т.е. изборът на газове за рециркулация се извършва от частта под налягане на газовия път. В този случай димоотводът и вентилаторът са монтирани в непосредствена близост един до друг, за да се намали аеродинамичното съпротивление на рециркулационния димоотвод.
Това дава възможност да се избере оптималната скорост на потока на продуктите от горенето, върнати в пещта, и спомага за намаляване на нивото на образуване на азотен оксид в промишлените котли с до 50%, при условие че са инсталирани специални камери за допълнително изгаряне.
Реконструкцията на стандартните горелки на разглежданата когенерация, всяка от които се състои от две автономни горелки в един корпус (с два канала за въздушна смес и два концентрични канала за вторичен въздух), беше сведена до организиране на трети вторичен въздушен канал и създаване на контролни клапи в захранващия въздухканали за регулиране на съотношението на скоростта на отделните потоци вторичен въздух. Всяка от тези две дейности създава специфичен независим ефект върху потискането на азотните оксиди. Когато във вторичния въздушен канал е монтирана допълнителна разделителна цилиндрична преграда с образуването на три изолирани (по цялата дължина на горелката) вторични въздушни канала с аксиални въртящи се лопатки във всеки от тези канали, характерът и интензивността на образуване на смес в пламъка значително се променят. Това се дължи главно на промяна в аеродинамичната структура на потока на изхода на горелката.
При почти еднакви стойности на параметъра на усукване за съседни потоци от аеро-смес и вторичен въздух, на изхода на горелката се образува плътен вихров поток, образуван от тези пръстеновидни потоци. На границата между тези слоеве се образува интензивен дребномащабен турбулентен масопренос, който допринася за завършване на образуването на смес в облака. Монолитният вихров поток от вторичен въздух и въздушна смес също създава мащабна турбулентност от вихровия пренос на част от продуктите на горенето към корена на пламъка (зона на обратен ток), което ускорява нагряването на частиците на горивото, тяхното запалване и изгаряне. Интензификацията на горенето с такава структура на пламъка допринася за по-бързото образуване на активна горивна зона, нейното изместване в областта на най-интензивното образуване на азотни оксиди.
По този начин, благодарение на разделянето на каналите за вторичен въздух, е възможно да се намалят емисиите на азотни оксиди. Сравнението на данните от изпитването на реконструиран котел (660 mg/m 3 ) и измерванията на съществуващи фабрични котли (800 mg/m 3 ) в типичен режим на работа (работят три прахови системи, натоварване 370 t/h) показва разлика в концентрацията на азотни оксиди(при еднакви стойности на излишния въздух на двата котела), който е около 150 mg/m 3 .