студено пресоване
Обект на процес
Процесите на обвиване, обвиване, оразмеряване, обемно формоване и студено пресоване се характеризират с триосно компресиране на детайла по време на неговото оформяне. Оформянето на частта се извършва поради преразпределението и предварително определеното движение на метала в работната кухина на щампата под действието на налягане, няколко пъти по-високо от границата на провлачване на деформирания материал. Получените части се характеризират с повишена точност и повърхностна обработка. Материалът на частите в резултат на студена деформация е значително подсилен.
Чернова
Обвиването на метала е операция по формоване на метал, в резултат на което височината намалява и в същото време се увеличават напречните размери на детайлите. Използва се утайка:
1) За увеличаване на диаметъра или площта на напречното сечение на оригиналния детайл (при липса на детайл с желаното сечение) с кръгла, правоъгълна или профилна форма;
2) За увеличаване на диаметъра или площта на напречното сечение на крайната или средната част на детайла, например при производството на част като болт с оформена глава;
3) Да подготви детайла за последващо пробиване на отвори в него;
4) Да се получат изковки с необходимата микроструктура и с определена посока на влакната;
5) Да се елиминира анизотропията на механичните свойства и да се получи еднаква метална структура в целия обем на детайла.
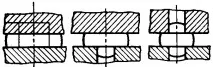
Ориз. 1 - Утаяване между плоски цокли, с отлив в една и две кухини
Заготовките, които трябва да се разрушават преди обработка, трябва да се нагреят до максималната температура, допустима за обработвания метал. Това значително намалява сложността на производството на коване, намалява броя на нагряванията и времето за обработка. Поради триенето, страничната повърхност на разстроения детайлпридобива бъчвообразна форма, което характеризира неравномерната деформация. Повтаряйки разфасоването няколко пъти от различни страни, е възможно детайлът да се приведе в първоначалната му форма или близо до нея, като същевременно се получи по-високо качество на метала и неговите идентични свойства във всички посоки.
Има два вида чернова - пълна и непълна. Извършва се пълна тяга, за да се увеличи сечението на детайла по цялата му дължина. Последните от своя страна включват крайна и средна чернова. За извършване на тегленето се използват наковалня, чукове, клещи, ръчни спирачки, гвоздеи; изправянето и довършването на изкривената изковка се извършва с помощта на мистрия, гофрове и др.
Заминаване
Облягането е ковашка операция, която се състои в деформация на детайла чрез частично облягане, за да се създадат локални удебеления чрез намаляване на дължината на детайла. Слизането се извършва в загрято или студено състояние.
Горещото заглавие се извършва на хоризонтални ковашки машини. Чрез горещо заглавие се изработват изковки на зъбни колела, клапани, пружини, пръстени, ролки и др.
Студената обработка е основната операция за получаване на части като болтове, винтове, нитове. За производството на такива части се използват машини за студено зареждане, на които освен заглавието се извършват и други операции (отрязване, пробиване, навиване на резба и др.), Което позволява да се получат части, които не изискват рязане, с производителност до няколкостотин в минута. В автомобилната и тракторната промишленост почти всички крепежни елементи се изработват чрез студено зареждане. Този метод се използва и за производство на по-сложни части (например сферични и стъпаловидни щифтове, лагерни ролки и топки и др.).
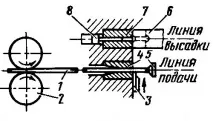
Ориз. 2 - Кацане на главата на нита на машина с един удар.
1- Тел или прът
2- Сървъриролки
4- Режеща матрица
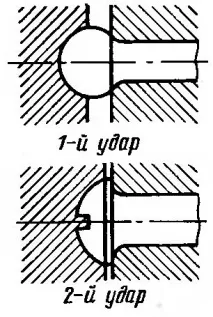
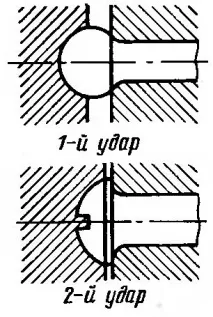
Ориз. 3 - Дебаркиране на винтове с шлици на двушокова машина.
Студената глава се подлага на калибрирани стоманени пръти с диаметър от 0,6 до 38 mm, както и пръти от цветни сплави (алуминий, мед и др.), Кръгли шестоъгълни и други форми на напречно сечение. Стоманените пръти трябва да бъдат предварително закалени.
В сравнение с други процеси на щамповане, обтягането се характеризира с висока производителност и прецизни изковки (без флаш). Кацането с локално контактно нагряване на заготовки в матрица на електрическа машина за обвиване набира популярност, което прави възможно получаването на удебеления с голям обем с едно преминаване.
Калибриране
Калибриране - студено изтегляне, последвано от малки редукции на горещовалцована профилна стомана, за да се получи по-високо качество на повърхността, по-точни размери и в някои случаи подобряване на някои механични свойства.
Калибрирането се използва в работи, свързани с машиностроенето, автомобилостроенето, корабостроенето, уредостроенето, както и някои други индустриални области, които изискват използването на точни и икономични профили, както и висококачествена стомана.
Чрез използването на оразмеряване е възможно да се получи изковка (междинен продукт, получен чрез коване или коване) с най-точен размер и тегло, който ще има най-висококачествена повърхност. Калибрирането може значително да ускори обработката, използвайки само шлайфане, за да я завършите.
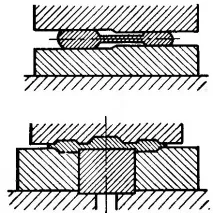
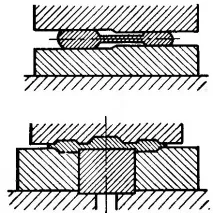
Ориз. 4 - Планарно и обемно калибриране
Калибрирането се извършва както на студено, така и на горещо.
Чрез използването на студено калибриране става възможно да се постигненай-точни размери и високо качество на повърхността. На свой ред горещото калибриране е станало по-често при работа с изковки с по-големи размери, тъй като не позволява постигане на същата точност като студеното калибриране.
Равнинното калибриране е необходимо за получаване на по-точни вертикални размери, които са разположени между отделните равнини на изковаване успоредни една на друга, както и за да им се придаде високо качество. В този случай има увеличение на размерите на изковката, които са в перпендикулярна посока спрямо действието на пресовата сила.
При комбинирано калибриране първо се извършва обемно калибриране, последвано от калибриране в равнина. Увеличаването на точността се увеличава.
3D формоване
Обемното формоване е вид обвиване, но се различава от него по това, че заготовката се оформя в кухината на матрицата, която е напълно или частично затворена. В съответствие с това се прави разграничение между отворено формоване с освобождаване на излишния метал в брус и затворено формоване, при което целият обем на метала на детайла се използва за оформяне на детайла. Формата и размерите на детайла трябва да бъдат такива, че деформацията във всяка секция да е най-малка, условията за потока на метала в матрицата да са оптимални и всички елементи на частта да са ясно дефинирани. Този процес изисква високо налягане и висококачествено производство на матрици. Предимствата на затвореното формоване включват по-големи възможности за формоване и повишена точност на частите.
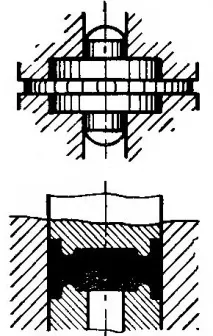
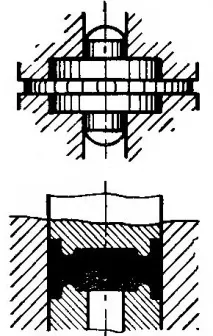
Ориз. 5 - Отворена и затворена обемна корниза
Тази технология се използва за производство на пространствени части с малки размери, но с по-сложна форма и висока точност. Материал на заготовки, използвани в процеса на студено формованетрябва да има висока пластичност, следователно заготовките (заготовки, пръти или пръти) се използват главно от цветни метали, нисковъглеродна стомана, по-рядко средно въглеродна стомана. Методът на студено формоване на метали произвежда готови детайли, които не изискват механична обработка или детайли, близки до тях, чието последващо рязане е минимално. С помощта на тази технология е възможно да се постигне степен на използване на метала от 90-95% (при рязко формоване тази цифра варира от 30-40%). Това се постига, наред с други неща, от факта, че няма нужда от предварителна обработка. По правило операциите по предварителна обработка са свързани с голяма загуба на изходния материал. В допълнение, обемното формоване не нарушава целостта на метала на детайла. Отбелязва се по-високо качество на продуктите, произведени по тази технология: якостта на частите се увеличава 3-10 пъти (в зависимост от степента на деформация), което позволява да се заменят скъпите високолегирани сплави и да се получат продукти с превъзходни механични характеристики.
Студено пресоване
Студеното пресоване (ударно или студено екструдиране) е процес на оформяне на куха част чрез изместване на метала на детайла с щанца в отворените кухини на матрицата. Студеното пресоване се разделя на директно, обратно и комбинирано, в зависимост от това дали посоката на изтичане на метала съвпада с движението на щанцата, противоположно на него, или се извършва едновременно в различни посоки. Възможно е и радиално пресоване, при което посоката на изтичане на метала е перпендикулярна на посоката на деформиращата сила P.
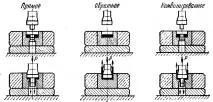
Ориз. 6 - Видове студено пресоване
Студеното пресоване се използва за части с различни форми.Обичайната (икономически осъществима) точност на производството на части е в рамките на 9 ... 11 квалификации, а грапавостта на повърхността е Ra 2,5 ... Ra 0,63. Степента на деформация (в проценти по време на студено пресоване се характеризира с израза:
където са площите на детайла и напречното сечение на детайла. Допустимата степен на деформация в една операция е 75 ... 95%, което позволява да се получат части с най-малка дебелина на стената от 0,3 ... 0,7 mm и височина до 6d (d е вътрешният диаметър на детайла) чрез обратно и до 40d чрез директно пресоване. С увеличаването налягането на натискане също нараства, достигайки (5 ... 10) . Това ограничава възможностите за оформяне на частите и техните общи размери, тъй като при такова високо налягане здравината и издръжливостта на работните части на щампата е недостатъчна за нормална работа. Като изходни заготовки могат да се използват заготовки, изработени от листове, пръти или профилирани. С помощта на екструзия се изработват голямо разнообразие от части, например: чаши, ръкави, кутии, тръби, ролки, болтове, гайки, маховици, фланци и др. Материалът за този процес може да бъде както цветни метали и техните сплави, така и стомана. Сравнително нов проблем е производството на стоманени части чрез този процес. В сравнение с цветните метали стоманата е много по-трудна за екструдиране.
За получаване на стоманени продукти по този метод е необходимо стриктно спазване на редица условия по отношение на избора на материала на матриците и щанците, термичната му обработка, качеството и свойствата на подложената на екструдиране стомана, скоростта на процеса, размерите и формата на продукта, методите на смазване и др. Величината на специфичното налягане по време на студено екструдиране на стомана и преди всичко работата на инструмента за щамповане се влияе особено от механичните свойства на кованата стомана, степента на деформация,дебелина на стената на чашата, ъгъл на конус на матрицата, ъгъл на конус на Поасон, лубриканти.
При екструдиране на твърди части специфичното налягане е много по-ниско, отколкото при производството на кухи части. Например, при екструдиране на пръти от мека стомана (механичните свойства са посочени по-горе), при степен на деформация от 40%, специфичното налягане ще бъде около 25 kg/mm2 (250 MN/m2), а при степен на деформация от 70%, около 100 kg/mm2 (1000 Mn/m2). Студената екструзия на стоманени продукти е препоръчително да се използва в масовото производство, тъй като цената на матриците е висока. Голямото предимство на този процес е високата им точност - 0.1 - 0.2 mm. Качеството на повърхността на частите, получени чрез студена екструзия, надвишава качеството на повърхността на изковките, направени чрез горещо коване с последователно студено калибриране. Загубата на метал при прилагане на студено екструдиране в сравнение с горещо коване може да бъде намалена с 60-70%.
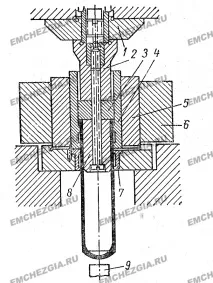
рисуване. 6.6. Схема на щампа за директно екструдиране на кухи части: 1 - горна плоча, 2 - стебло на поансон; 3 - поансон, 4 - матрица, 5 - първа скоба, 6 - втора скоба; 7 - направляващ пръстен; 8 - ударна глава; 9 - ежектор
Частите могат да бъдат произведени чрез студено пресоване както на хидравлични, така и на по-производителни механични преси. В този случай пресовото легло трябва да има максимална твърдост и да осигурява праволинейно движение на плъзгача по цялата дължина на хода му без луфт.
Заключение
Процесите на формоване на детайли, които изследвахме, се използват широко в самолетостроенето и машиностроенето като цяло. С помощта на тези технологии е възможно да се постигне висока степен на използване на метала. Получените части са много точни иповърхностна чистота. Материалът на частите в резултат на студена деформация е значително подсилен. Технологията на процеса се подобрява.
1. А.Л. Абибов, Н.М. Бирюков, глава от книгата "Технология на самолетостроенето" 1982 г.
2. Метален интернет портал http://ags-metalgroup.ru
3. Интернет портал "Ковашки операции" http://www.mtomd.info
4. В.Р. Каргин, Б.В. Каргин глава от книгата "Основи на технологичните процеси на OMD: пресова секция"
следваща лекция ==> | ||
Интерференция на поляризирана светлина | Ролята на енергията в развитието на човешкото общество |