Теглителни характеристики на гъсенични булдозери
Тази публикация продължава поредица от статии за булдозерно оборудване на гъсенични вериги.
В предишна статия (виж "ОС" № 6, 2010 г.) беше разгледан въпросът за развитието на булдозерните трансмисии. Накратко можем да кажем, че основните дизайнерски решения на етапи бяха:
- механична трансмисия (MT), използвана, тъй като терминът „булдозер“ е назначен в началото на миналия век за гъсенични трактори „с лопата“ и не се е променил до ден днешен (заема пазарен дял главно благодарение на булдозерите ChTZ - B130, B170, B10);
- хидромеханичен (GMT), използващ преобразувател на въртящия момент (GTR), заема огромен пазарен дял;
- хидростатичен (HST) на базата на чифт хидравлична помпа-хидромотор, който става все по-популярен; Германският индустриален гигант Liebherr е технологичният пионер и лидер на пазара за булдозери HTS. Ползите и перспективите на GTS вече бяха обсъдени в предишна статия.
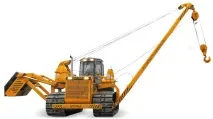
Следващата най-важна група аспекти на работата на булдозера са характеристиките на прилагането на теглителната сила, предавана от двигателя през трансмисията и гъсеницата към острието / рипера поради свойствата на свързване на булдозера с опорната повърхност.
Схематично маршрутът на енергийния поток е показан на фиг. 1.
Жълтото подчертава етапа, на който е необходима „опорна точка“ за преобразуване на енергията в работа, което в нашия случай е повърхността. Действието на различни видове сили на триене на гъсеницата върху повърхността определя качеството на сцеплението и в крайна сметка нивото на преобразуване на енергията в работа на булдозер. Схемата на взаимодействие на тези сили е показана на фиг. 2.
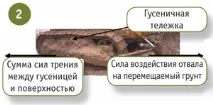
Обхватът на статията позволява само разширено разглеждане на въпроса за взаимодействието на всички сили имоменти от процеса на булдозериране и определяне на решаващите фактори. Като цяло тези две сили са равни и качеството на булдозерирането зависи от сцеплението на пистите с повърхността - това е основният извод от диаграмата на фиг. 2. Качеството на сцеплението се определя от вида на верижния камион и схемата на закрепването му към рамката на булдозера с равни характеристики на земната повърхност. Тук стигаме до основния въпрос на статията - етапите на развитие на ходовата част на верижните булдозери и техните особености.
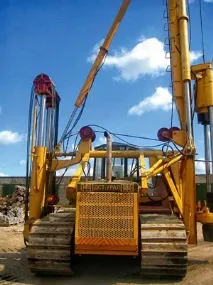
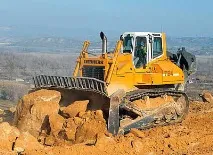
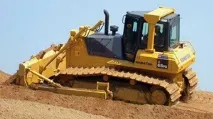
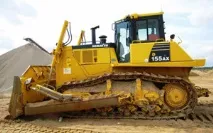
Етап 1 - твърдо окачване: талиги, твърдо фиксирани върху рамката с ролки, твърдо фиксирани на свой ред върху нея. Това е твърда конструкция, базирана на двете коловози, чиито обувки винаги са в една и съща равнина по време на работа. На фиг. 3 показва основния недостатък на такава схема за булдозер - по време на работа на неравна повърхност, устройството се опира върху него само с две точки, което води до преждевременна повреда на пътните колела.
Също така, когато се движи, такъв булдозер изпитва постоянни вибрационни натоварвания, което води до ускорено разрушаване на всички структурни елементи.
Независимо от това, в някои видове специално оборудване се използва точно такава схема - тръбоукладчици, ротационни каналокопатели и др., При които скоростите на движение са минимални и в същото време се изисква максимална твърдост на основната рама на трактора.
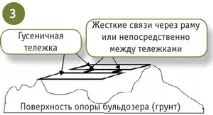
Етап 2 - полутвърдо окачване: триточкова опора на рамката (първоначално с пружина) върху осцилиращи талиги и ролки, здраво закрепени към талигите. И окончателното решение под формата на въртяща се ос на талигата, отделена от крайните предавки и балансираща греда вместо пружина.
Схеми на твърдо (а), полутвърдо окачване (б) и отдалечена ос на люлеене на талигите (в): 1 - талига, 2 - ос на нейното люлеене,3 - рама на трактора, 4 - еластична връзка на количката с рамата на трактора; 5 - задвижващо колело; 6 - оста на задвижващото колело
Използва се предимно на булдозери до клас 15 включително. Схематично този тип ходова част е показана на фиг. 4. На същото място, за сравнение, е показана диаграма на твърда ходова част.
Този тип окачване в окончателната му форма (виж фиг. 4, c) е най-често срещаният днес, тъй като има следните характеристики:
- относителна евтиност и лекота на производство на колички;
- намаляване до приемливо ниво на динамичните натоварвания върху рамата на трактора;
- когато оста на въртене на талигата е изместена, бордовата скоростна кутия се "освобождава" от прякото въздействие на ударните сили от острието и неравната земя;
- точността на планирането отговаря на съвременните изисквания;
- при работа върху твърди и неравни, скалисти почви, схемата на ролките, фиксирани в една и съща равнина върху рамката на талигата, не осигурява плавно движение. Само две ролки се поддържат на такива повърхности за всяка от количките, следователно, ако само една ролка е износена, е необходимо да смените цялата „страна“, в противен случай, когато сменяте само една, тя постоянно ще се проваля.
Във връзка с този недостатък, който всъщност е пречка за критични режими на работа на тежки булдозери с клас на тяга над 15 тона и работно тегло над 30 тона, се използва по-модерен тип ходова част, която днес отваря последния етап от тяхното развитие.
Етап 3 - балансиращи еластични окачвания: еластично фиксирани люлеещи се колички на гъсеничен камион, здраво закрепен към рамката. На балансьорите на люлеещите се колички са фиксирани две ролки. Схемата и типичните примери за изпълнение на това шаси от различни производители са показани на фиг. 5.
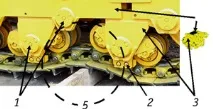
Устройството на еластичното балансиращо окачване на булдозера и работата на ходовата част при преодоляване на твърдо препятствие: 1 – люлеещи се оси на каретката и балансира с ролки; 2 - водач на гъсеница; 3 - карета; 4 - еластичен амортисьор и мястото му на работа на количката
Този тип ходова част започва да се използва при Caterpillar D8 и по-старите булдозери през 1975 г. Именно тази компания традиционно действа като предшественик на най-обещаващите решения в дизайна на промишлени булдозери. Същата схема е приложена за първи път в световната практика на по-леки булдозери ТМ10 (23 тона) на завода DST-Ural през 2006 г. (виж фиг. 5), приложена е и на булдозери Liebherr PR 764, но само през последните две години. Масовото прилагане (на собствена схема на каретата, по очевидни причини, различна от Caterpillar) на D155 и по-стари булдозери, лидер на световния пазар на булдозери Komatsu, започна през 90-те години. (фиг. 6).
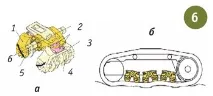
Принципът на работа на ходовата част на булдозера Komatsu D155: a - каретно устройство; b - диаграма на "работата" на количката и вагоните върху неравна повърхност: 1 - външна количка; 2 - гумена възглавница; 3 - вътрешна карета; 4 - направляваща ролка; 5 - ос, твърдо закрепена към гъсеничния камион; 6 - централна линия
Характеристики на този тип шаси:
- максимално сцепление със земята сред всички видове окачвания за булдозери с клас на тяга от 10 тона и повече (фиг. 7);
- най-малкото динамично въздействие върху рамката на булдозера при работа в трудни условия (фиг. 8);
- най-малко износване на скъпи елементи на ходовата част - гъсеници, ролки, крайни предавки. В същото време, ако Caterpillar е решил проблема с „разединяването“ на крайните задвижвания от талигата чрез фундаментално различен дизайн - поради горното разположение на крайните задвижвания, тогава задруги производители, този тип ходова част коригира "проблема с разстоянието А" (виж Фиг. 4, c), когато твърде голямото аксиално колебание на талигата създава "претоварване" на гъсеницата в полутвърда ходова част. И друго решение за "разединяване" на бордовите скоростни кутии от камиона на гъсеницата все още не е намерено.
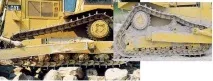
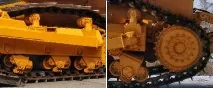
Недостатъците на този тип окачване включват само относително високата производствена цена. Въпреки това, колкото и да е странно, при преминаването към масово производство на този тип окачване цените на булдозерите не се промениха, което показва незначителна крайна разлика в цената на масовото производство.
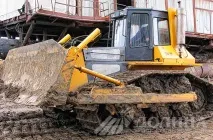
Всеки специалист от експлоатационни организации ще направи заключение от тази статия, разчитайки единствено на своя опит, за целия набор от специфични условия на работа на булдозерно оборудване. Но бих искал да отбележа: състоянието на „почивка“ в развитието на дизайна на машините днес означава за инженерните предприятия действителното изоставане от пазара и следователно неговата загуба. Ако прекрачите сегашното технологично ниво и работите пред кривата, местният производител ще получи някакъв шанс да излезе от виртуална задънена улица. Натискът от всички страни на старите (западни) и новите (източни) лидери в българската система "монополни цени - недостиг на кадри - компресиран пазар - критично високи данъци - висока цена на кредитите" изключва еволюционното развитие. Всъщност кризата постави твърда бариера за много предприятия в Руската федерация.
Заводът DST-Ural, следвайки лидерите на пазара CHETRA и ChTZ, се опитва да избегне някои от грешките на тези компании. Наред с продължаващата модернизация на производството винаги стои въпросът за целесъобразността на собственото производство на отделни компоненти и възли. И така, внедряване на нов дизайн на булдозер, базиран нахидростатична трансмисия, DST-Ural първоначално отказа да използва вътрешни и среднокачествени вносни компоненти. Доверяването на световните лидери в технологията на Bosch Rexroth с максимално ограничаване на режийните разходи, които „висят“ над себестойността на продукцията, дава възможност на купувачите на булдозерна техника в България да бъдат предоставени модерни машини, изградени по най-новите технологии, както в техническо, така и в качествено отношение, и същевременно достъпни.